偏差调查(Deviation Investigation)是任何 GMP组织中最重要的质量活动之一。在FDA和其他监管机构的观察、警告信中,它们也常年位居最常被引用问题列表的显眼位置。[1]例如“未能彻底审查无法解释的差异,以及批次不符合规格的原因”,“在出现偏差时QA 对根本原因分析的责任“等相关事项。
显然,许多组织在管理偏差调查方面还有改进的余地。本文部分列出了许多公司在进行偏差管理时常犯的错误。
1.不利用历史数据进行持续改进
Lean Six Sigma管理理念的核心DMAIC (Define, Measure, Analyse, Improve, Control) 循环中很重要的环节之一就是Control (控制)。操作流程需要持续的反馈(feedback)和监控 (monitoring)。DMAIC是个闭环控制系统或“预警系统”,它会在流程开始向错误的方向转变时发出警报,以便在产生缺陷之前进行调整。
生产机构随着时间的推移,会通过不断增长的生产批次收集到大量数据,可用于持续改进、提高生产力和减少调查的重复发生。但实际上,很多组织对于这些数据并没有进行认真的分析研判,每年仅以一种有些敷衍的方式审查这些数据。不对生产数据进行统计过程控制(SPC, statistical process control), 就很难发现工艺在不断的生产过程中出现的可能偏差的趋势。同时对Cpk (process capability, 过程能力指数) 这样关键的工艺表现参数也忽略而过。良好的工艺趋势分析是监控和主动发现工艺中潜在问题的重要因素。
我们知道,一个生产工艺的Sigma级别会随着生产的不断进行逐渐趋向于减小,所以也就产生了所谓的1.5 Sigma规则,即工艺的长期Sigma级别通常会比它的短期Sigma级别低1.5。换句话说,工艺的标准偏差很有可能随着时间的延长逐渐增大,因此更需要不断收集生产数据,进行SPC分析,以便发现潜在的影响工艺稳定性的因素。所谓温故而知新,对于工艺来说也是成立的,通过不断地回顾分析历史数据,你就可能对工艺未来的表现做出更准确的判断。
2.淡化偏差严重性
有些CDMO,为了节约调查成本,减少工作量,或者减轻监管方面的责任,在向制药公司呈递的偏差报告中,会有意地淡化偏差的严重程度,将关键偏差(critical deviation)降格为重大偏差 (major deviation)甚至轻微偏差(minor deviation)。本身在划分偏差类型时就有很多主观因素,因此为偏差定性制造了可操作空间。降格偏差类型,不仅可能使产品质量受到影响,而且不利于对偏差的认真调查,可能致使该偏差在未来仍然不断发生。
3.忽略偏差与扩大生产之间的潜在关联
某些工艺参数,比如投料时间,反应温度,升(降)温速率控制等,可能受到批次反应规模的影响,因此在工艺开发的过程中,应该将这些潜在的与反应规模有关的工艺参数考虑进去,设定能够被大规模批次生产所遵从的参数范围。如果不将这些因素考虑进去的话,很可能在扩大生产规模的批次中造成某些参数的偏差。同时,仪器设备的变化,也有可能导致偏差的产生。从某种程度上讲,这些“可预见”的偏差应该通过合理的工艺设计消除,而不应该出现在生产的过程之中。
4.强行结论
对于只看见问题,找不到原因的情况,在GMP生产的偏差管理中实在是非常常见的现象。尽管机构的人员动用了很多精力和时间,收集大量的事实与信息,但仍然无法确定偏差的根本原因。这除了偏差本身的复杂性之外,也与从业者能力有限不无关系。
调查无果,无法得出确定性的根本原因是一个常见的局面,但有些机构却在无法准确认定原因的情况下,为悬而未决的偏差强行指派一个“根本原因”,这可能是出于监管标准要求而做出的行为。其实这种“强行结案”的方法不仅没有发现真正的偏差原因,而且也阻碍了机构对于偏差产生的深入调查。对事实的错误解释或不切实际的确定,可能会阻止调查最可能的根本原因。并没有监管标准要求所有调查结论都是必须是确定的。基于彻底调查,并由可用数据和信息支持并证明“最可能的根本原因”就足够了。但如果强行地赋予其“最终判决”的身份,这对于机构继续调查并确定根本原因是不利的。
5.错过真正的根本原因
错过真正根本原因,和上一点提到的“强行编排根本原因“还有所不同,后者属于一种知其不可而为之的明知故犯的错误,而前者却是“误入藕花深处“的一种不自觉。
找到真正的根本原因至关重要。在许多情况下,组织未能识别并纠正偏差的真正根本原因。而那个未被发现的根本原因原本是很容易解决的,只要你正确发现了它。而错误识别的“根本原因”有可能会造成非常惨重的经济损失。
真正的根本原因是导致偏差事件发生的最深层次的原因。了解真正的根本原因需要收集所有相关事实与数据,并且掌握正确的方法论。有时根本原因直接明了,但有时,发现根本原因需要长达数月的深入技术评估。
6.将人为错误作为根本原因
偏差管理中一个非常常见的错误,就是简单地将偏差产生的原因归咎为“人为错误“。诚然,所有的偏差都是由人的操作来产生的,但这并不代表简单地将”人为错误“认定为事故的根本原因。这是一种投机取巧的做法,可以通过不进行深入的调查研究就简单结案的终南捷径。
监管机构会在他们的观察(例如483表)中标注这一点,即反复地声明人为错误为根本原因的行为,表明该组织没有兴趣或资源来寻找真正的根本原因,并以此纠正重复发生的潜在问题。甚至存在一些质量体系,不允许将人为错误用作根本原因,以防止组织停止识别和解决人为错误背后的真正根本原因。
人为错误的确代表一种根本原因类别,但它本身很少是真正的、可执行的根本原因。真正的根本原因通常在其他方面,例如工艺中有太多模棱两可的描述、没有进行认真系统的生产培训等原因,而最终以人为错误的形式表现出来,但后者并不是真正的根本原因。重要的是找到真正的根本原因并赋以可执行的描述,以防止其再次发生,并减少未来与人为错误相关的事故数量。防止人为错误再次发生不仅可以为组织节省资金,还可以降低出现法规问题(包括监管调查结果)的可能性。
7.敷衍了事或者晦涩不清的调查报告
许多偏差报告撰写者并没有认真地按照标准准备偏差报告,而是敷衍了事地撰写一份语焉不详或者难以理解的报告。但他们有可能忽略一个事实,监管机构的检察员会在检查过程中认真地阅读他们写的偏差报告,而偏差报告的问题,也的确是包括FDA在内的监管机构反复强调的事项,并且有可能最终转化为一纸警告信。
调查报告应该易于理解,并提供所有必要的支持事实和理由,以便在事件发生多年后仍能追踪。要做到这一点,最困难的挑战是写作要合乎逻辑、清晰、简洁,不要呈现和重复冗余信息。因此,培训是撰写有效调查的重要因素。
8.不适当的 CAPA (Corrective Actions and Preventive Actions)
作为偏差管理的核心内容,最终都要落实到通过怎样的手段来消弭偏差的影响,保证产品的质量,以及通过预防的手段避免同样偏差的再次发生,因此CAPA肩负着偏差管理最终是否可以结案的关键角色。可想而知,正确有效的CAPA必须建立在合理的根本原因之上,也就是皮之不存,毛将焉附的道理。如果根本原因找错了,很难相信对应的CAPA能够起到它们应有的作用。但也存在正确发现病因,却没有开出合理药方的情况。需要指出的是,在终极的CAPA因为某种原因在短时期内无法实施的情况下,机构也可以提出“临时方案“,以保证生产可以顺利进行,但这种情况需要进行可靠的风险评估。
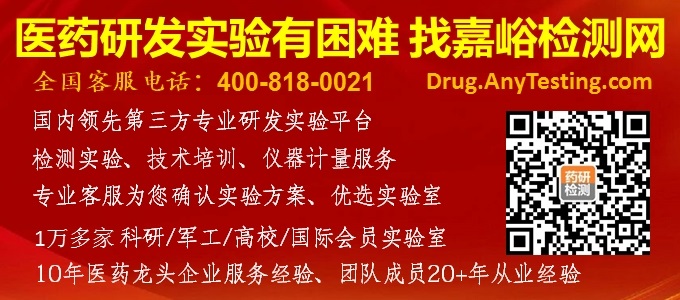