车轮螺栓是车辆的重要零部件,是轮毂连接车轮的高强度紧固件。某公司车轮螺栓为A厂家产品,对应的车轮螺母为A,B两个厂家产品。在螺栓装配过程中,A厂家的螺栓和螺母同时使用时未发生失效,但在A厂家螺栓和B厂家螺母配合使用时,约5%的螺栓出现拉长、断裂情况。为查明螺栓拉长和断裂的原因,来自郑州精益达汽车零部件有限公司的武坤、杨帆等研究人员进行了一系列理化检验,并提出了相应改进措施,以避免该类问题再次发生。
1、理化检验
1.1 宏观观察
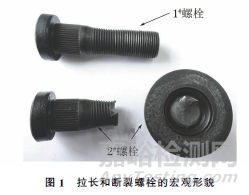
螺栓规格为20mm×1.5mm(外径×壁厚),性能等级为10.9级,表面处理方式为磷化处理。拉长和断裂螺栓的宏观形貌如图1所示,可见拉长螺栓(1#螺栓)螺纹处产生明显的颈缩塑性变形,断裂螺栓(2#螺栓)螺纹处发生断裂,断裂螺纹处同样产生了明显的颈缩塑性变形。
1.2 化学成分分析
螺栓材料为35CrMo合金钢,分别在1#,2#螺栓上取尺寸为18mm×12mm(直径×长度)的圆柱形试样,用磨床磨平,然后用直读光谱仪进行化学成分分析,由结果可见1#,2#螺栓的各元素含量均符合GB/T 3077—2015《合金结构钢》的要求。
1.3 力学性能及硬度测试
在1#,2#螺栓的同批次螺栓上取样,依据GB/T 228.1—2021 《拉伸试验 第1部分:室温试验方法》,用微机控制电子万能试验机对试样进行力学性能测试。在螺栓上截取厚度为16mm的圆柱形试样,用磨床磨平,然后用洛氏硬度计对试样进行硬度测试。螺栓的力学性能及硬度测试结果如表1所示,可见试样的力学性能和硬度均符合技术要求。
表1 螺栓的力学性能及硬度测试结果
1.4 金相检验
分别从1#,2#螺栓螺纹处截取纵向剖面试样,用体积分数为4%的硝酸乙醇溶液腐蚀,并用光学显微镜对试样进行金相检验,结果如图2,3所示。由图2可知:1#螺栓螺纹无明显脱碳,螺纹根部牙底过渡圆滑,无毛刺等缺陷,显微组织为回火索氏体2级,符合GB/T 3098.1—2010 《紧固件机械性能螺栓、螺钉和螺柱》的要求。由图3可知,2#螺栓的金相检验结果与1#螺栓基本一致。
1.5 扫描电镜(SEM)及能谱分析
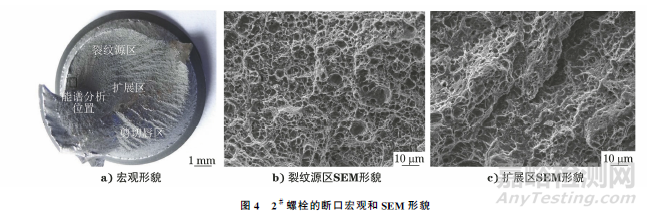
将2#螺栓断口用线切割取样,经超声清洗后,对试样进行宏观观察和SEM分析,结果如图4所示。由图4可知:2#螺栓的断口断面整体粗糙,凹凸不平,放射条纹方向明显,断面可分为裂纹源区、扩展区和明显的剪切唇区[见图4a)];裂纹源区有较多的圆形韧窝,有轻微的剪切痕迹,说明裂纹源处有力的长时间集聚,该处受力超过了螺栓的屈服强度;扩展区为准解理形貌,说明该区域裂纹扩展速率较快;螺栓最终在剪切唇区发生一次性剪切断裂。
对试样进行能谱分析,分析位置如图4a)所示,分析结果如图5所示,可见Fe元素的衍射峰比较明显,除有少量O 元素外,试样中无其他异常元素,可排除夹杂物引起的断裂。
2、摩擦性能测试
分别选取A厂家螺栓+A厂家螺母和A厂家螺栓+B厂家螺母各10组,按照GB/T 16823.3—2010 《紧固件 扭矩-夹紧力试验》,用力学试验机对试样进行摩擦性能测试。首先拧紧螺母至550N·m(装配力矩),记录扭矩系数等数据,再拧紧至螺栓产生屈服,记录屈服扭矩、屈服夹紧力等数据。A厂家螺栓+A厂家螺母摩擦性能的测试结果如表3所示。由表2可知,扭矩系数大部分为0.17~0.19,平均扭矩系数为0.18,标准差为0.009,均符合扭矩系数的相应要求,且一致性较好。
表2 A厂家螺栓+A厂家螺母摩擦性能的测试结果
表3为A厂家螺栓+B厂家螺母摩擦性能的测试结果,可见扭矩系数为0.10~0.16,平均扭矩系数为0.13,标准差为0.02,一致性较差。
表3 A厂家螺栓+B厂家螺母摩擦性能的测试结果
3、综合分析
螺栓是用夹紧力将多个零部件结合在一起,从而达到紧固的目的。夹紧力测量困难,但夹紧力与扭矩有一定的线性关系,且扭矩容易测量,因此,可用控制扭矩的方法得到合适的夹紧力。扭矩系数、夹紧力和扭矩之间的关系如式(1)所示。
从式(1)可知,扭矩系数与夹紧力成反比,即当扭矩系数减小时,夹紧力增大。在螺栓装配中,扭矩系数减小会使夹紧力超过螺栓的屈服强度,导致螺栓拉长变形,当夹紧力大到一定程度时,会导致螺栓断裂。
车轮螺栓实际装配扭矩约为(550±50)N·m,表3中所测最小屈服扭矩明显低于最大装配扭矩。根据技术要求,屈服强度最小为900MPa,计算可知螺栓屈服应力最小约为255kN,实际测试螺栓屈服夹紧力均大于该值,因此,可排除材料性能问题。
将最大装配扭矩T=600N·m和螺栓最小屈服夹紧力F=255kN代入式(1),可得最小扭矩系数K约为0.12,即扭矩系数不小于0.12可保证力学性能合格的螺栓不发生屈服拉伸甚至断裂情况。从摩擦性能测试结果可知:A厂家螺栓+A厂家螺母的实测扭矩系数为0.17~0.19,屈服扭矩均大于800N·m,说明螺栓发生屈服现象的可能性小;A厂家螺栓+B厂家螺母有3组实测扭矩系数小于0.12,其中有两组实测屈服扭矩小于600N·m,即装配中有两组螺栓可能发生塑性变形。同时根据螺栓受力结构分析,螺栓所需最小夹紧力为105kN,即当装配扭矩最小时,最大扭矩系数K约为0.23,说明理论计算扭矩系数保持在0.12~0.23可保证螺栓夹紧力符合要求,为增大容错率,将扭矩系数控制在0.15~0.20更为合适。
螺栓的扭矩系数K宏观上直接反映螺栓拧紧过程中,扭矩与夹紧力之间的系数,K值不仅取决于摩擦面的摩擦系数,还取决于螺纹连接副的几何状况。对理想的螺纹连接副而言,当摩擦系数确定后,扭矩系数也就确定了。通常情况下,在螺栓拧紧过程中100%的扭矩有90%需要用于克服摩擦力(50%用于克服螺栓螺母头的摩擦力,40%用于克服螺纹副中的摩擦力),10%用于转化为夹紧力(见图6),理论上只要有足够的夹紧力,就可以保证被夹零件在振动、高温及低温等恶劣环境下安全工作。
经以上分析可知,螺栓在装配过程中出现拉长和断裂的主要原因为:B厂家螺母摩擦系数控制较差,与A厂家螺栓配合连接副的扭矩系数一致性差,且扭矩系数较小,导致螺栓所受的夹紧力增大,多个螺栓屈服扭矩明显低于装配扭矩,造成螺栓在装配过程中出现拉长、断裂情况。因此,B厂家需要对螺母的摩擦系数进行改进。
4、结论
(1) 螺栓的显微组织、硬度、力学性能、屈服夹紧力等均符合相应技术要求;断口处有明显的塑性变形,属于一次性的拉伸过载断裂,裂纹源处无夹杂物。
(2) 造成螺栓失效的主要原因为:连接副扭矩系数较低,螺栓夹紧力增大,个别螺栓屈服扭矩明显低于实际装配可能达到的最大扭矩,导致装配过程中出现螺栓拉长,甚至断裂的情况。B厂家需对螺母摩擦系数进行改进提升,保证一致性。
(3) 经过B厂家对螺母摩擦系数的工艺过程进行改进提升,再次进行螺栓螺母扭矩系数试验,扭矩系数均在0.15~0.20,使用至今的两年内未再次发生该问题。