以Ni60A合金粉末和MoS2粉末为熔覆材料,采用激光熔覆技术在35CrMnSi钢基体表面制备MoS2/Ni60A固体自润滑涂层,研究了MoS2添加量(质量分数1%,3%,5%,7%,9%)对涂层物相组成、显微组织、显微硬度和摩擦磨损性能的影响。结果表明:不同MoS2添加量的涂层表面成形良好,均与基体达到冶金结合,涂层主要物相组成为MoS2、γ-Ni、NiS、Cr2B,其中,上部显微组织主要由短棒状、鱼骨状和放射状的树枝晶组成,底部与熔合线处的组织由平面晶和粒状晶组成。随着MoS2添加量的增加,涂层的显微硬度降低,磨损质量损失增多,摩擦因数先降低后增大。当MoS2添加量为3%时,涂层的摩擦因数最小,为0.43,磨损表面形成完整的固体自润滑膜,产生的犁沟较少,主要磨损机理为轻微的磨粒磨损。
1 、试样制备与试验方法
基体选用尺寸为100mm×50mm×10mm的35CrMnSi钢板,熔覆前用砂轮机对基体表面进行打磨,并用酒精清洗,烘干待用。熔覆材料为Ni60A自熔性合金粉末和MoS2粉末,平均粒径均为74μm,其中Ni60A合金粉末的化学成分(质量分数/%)为16Cr,3.5B,4.5Si,≤15.0Fe,0.8C,余Ni。按照MoS2粉末的质量分数分别为1%,3%,5%,7%,9%进行配料,采用全方位行星式球磨机进行干法球磨,磨球材料为不锈钢,球料质量比为2∶1,球磨时间为0.5h。将球磨后的粉末均匀铺在基体表面,铺粉厚度为1mm,使用光纤激光器系统进行激光熔覆试验,制备了长度100mm、厚度1mm的单道单层涂层试样。
采用X射线衍射仪(XRD)对涂层物相进行分析。采用扫描电子显微镜(SEM)观察涂层不同位置的截面微观形貌,采用附带的能谱仪(EDS)进行微区成分分析。采用显微硬度计测试截面显微硬度,从涂层表面向基体每隔0.25mm取点测试,距涂层表面相同距离处测3点取平均值。采用微机控制万能摩擦磨损试验机进行室温干滑动摩擦磨损测试,试验装置如图1所示,试样与对磨环为面接触,试样为圆柱状,对磨环材料为淬火45钢,采用分析电子天平称取磨损前后试样的质量,计算磨损质量损失。采用光学显微镜观察磨损形貌。
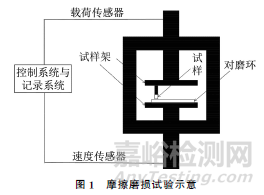
2 、试验结果与讨论
2.1 对宏观形貌的影响
由图2可以看出:不同MoS2添加量的MoS2/Ni60A 涂层成形良好,没有产生明显的宏观裂纹或气孔。但是随着MoS2添加量的增加,涂层表面逐渐粗糙,特别是含质量分数7%,9%MoS2的涂层。这是由于过多的MoS2粉末容易发生团聚,导致激光熔覆过程中熔池的流动性降低造成的。
2.2 对物相组成的影响
由图3可见,不同MoS2添加量的MoS2/Ni60A涂层均存在γ-Ni固溶体、MoS2、Cr2B和NiS相。NiS相是由于激光熔覆过程中熔池温度高达3000K,造成部分MoS2分解为钼元素和硫元素,在熔池液体流动过程中硫元素与镍元素反应而生成。当MoS2添加量(质量分数,下同)为1%时,MoS2衍射峰不明显,可能是MoS2分解后含量太低,未检测到。
2.3 对显微组织的影响
由图4可见,基体与涂层之间形成了一条光亮且完整无缺陷的熔合线,说明涂层与基体之间形成了良好的冶金结合。熔合线附近的组织为近垂直于基体方向定向生长的平面晶和柱状晶,这是因为熔合线附近温度梯度较大,过冷度较大,金属液的形核方式为非均匀形核,而涂层的凝固速率较低,使温度梯度与凝固速率的比值较大,导致晶粒的长大速率大于形核速率,因此形成了粗大的平面晶和柱状晶。不同MoS2添加量涂层的相应部位的组织基本相似,底部由柱状晶和平面晶组成,中部和上部由短棒状、鱼骨状和放射状的树枝晶组成。涂层底部的组织最粗大,该区域是熔池中温度梯度最大且成分过冷最小的区域,因此晶粒的长大速率最快;涂层中部的温度梯度较大,树枝晶的生长条件较好,因此该区域形成了粗大的树枝晶;涂层上部的温度梯度最小,成分过冷最大,温度梯度与凝固速率的比值较小,晶粒的形核速率大于长大速率,因此该区域的组织较细小。
表1 图5中不同位置的EDS分析结果
以添加质量分数3%MoS2的涂层为例,对其中部不同位置的微区成分进行分析。由图5和表1可以看出:涂层中白色和灰色的树枝晶(位置A和位置D)的微区成分基本相同,以镍元素和铁元素为主,并含有少量铬元素和硅元素,其中铁元素一部分来源于基体,另一部分来源于Ni60A合金粉末;黑色树枝晶(位置B)中含量最高的是铬元素,同时还存在钼元素和硫元素,推测黑色树枝晶中含有MoS2、NiS硫化物,随着MoS2添加量的增加,涂层中的黑色区域增多;基体(位置C)的主要形成元素为镍元素,可知树枝晶分布在γ-Ni固溶体上。
2.4 对显微硬度的影响
由图6可见,涂层的显微硬度均远高于基体,这是因为涂层内部存在Cr2B硬质化合物,同时基体对涂层的稀释起到固溶强化的效果。随着MoS2含量的增加,涂层的硬度呈现出下降的趋势,其原因是MoS2作为一种固体自润滑剂其硬度极低,因此会降低涂层的显微硬度。在结合区内除MoS2添加量为1%的涂层外,其他涂层的显微硬度均随着MoS2含量的增加呈先升高后降低的趋势。先上升的原因为,在激光熔覆的过程中MoS2会分解成为钼元素和硫元素,钼元素能够固溶到组织内部,表现出固溶强化的效果;后下降的原因为结合区下部靠近基体,被基体稀释的程度太大导致显微硬度下降。
2.5 对摩擦磨损性能的影响
添加质量分数1%,3%,5%,7%,9%MoS2的涂层的平均磨损质量损失分别为9.9,15.8,22.0,26.0,27.6g,均远低于基体的平均磨损质量损失(40.8g)。随着MoS2添加量的增加,涂层的磨损质量损失增大,这主要归因于显微硬度的降低,显微硬度越低,则耐磨性越差。由图7可以看出:基体的摩擦因数曲线波动剧烈,平均摩擦因数为0.45;当MoS2质量分数为1%和3%时,涂层的摩擦因数曲线波动较小,当MoS2 质量分数为3%时,摩擦因数最低,其平均值为0.43;当MoS2质量分数为5%,7%和9%时,涂层摩擦因数曲线波动较明显,且当MoS2质量分数为7%和9%时的曲线波动最剧烈,分析认为当MoS2含量过高时,涂层内部出现MoS2团聚现象,在摩擦磨损过程中当对磨环与MoS2团聚体接触时,摩擦因数会急剧降低,当团聚体被消耗后摩擦因数又再一次升高。由表2可知,随着MoS2添加量的增加,涂层的平均摩擦因数呈先减小后增大的趋势,这是因为随MoS2添加量增加,涂层中NiS和MoS2含量增加,NiS具有很好的减摩性能,而MoS2又是天然的固体自润滑材料,因此摩擦因数降低;但是当MoS2含量增加至一定量后,涂层的显微硬度降低,在摩擦磨损过程中涂层表面会存在剧烈的磨粒磨损,磨粒在涂层表面和摩擦副之间运动会阻碍摩擦过程的进行,因此摩擦因数又升高。
表2 添加不同质量分数MoS2的MoS2/Ni60A涂层的平均摩擦因数
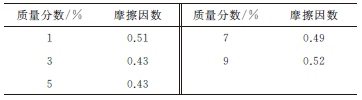
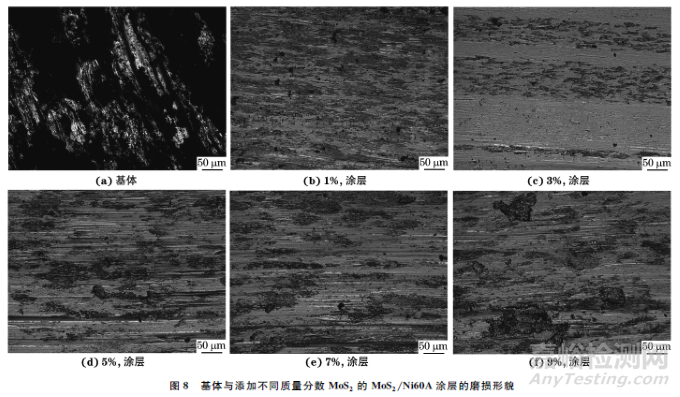
由图8可见,基体的磨损表面产生了较深的犁沟,且黏着和氧化现象严重,其磨损形式为剧烈的磨粒磨损、黏着磨损和氧化磨损。当添加质量分数为1%的MoS2时,涂层表面形成了局部的固体润滑膜,磨损表面存在一些微小的犁沟,主要磨损形式为磨粒磨损。当添加质量分数为3%的MoS2时,固体自润滑膜分布在整个磨损表面,表面存在少量的犁沟,磨损机理为轻微的磨粒磨损。当添加质量分数为5%,7%,9%的MoS2时,虽然在磨损表面上也形成了润滑膜,但是由于涂层的显微硬度较低,磨损表面产生了大量粗且深的犁沟以及剥落坑,这是由于对磨环对涂层表面的反复摩擦和挤压使涂层次表面萌生了疲劳裂纹,同时摩擦磨损过程中产生的热量无法及时消散,导致对磨环与涂层表面之间产生了黏着效应,最终在黏着力和机械剪切力的反复作用下,涂层脱落形成剥落坑;此时涂层的主要磨损形式为剧烈的磨粒磨损和黏着磨损。
3 、结 论
(1) 采用激光熔覆技术制备的添加质量分数分别为1%,3%,5%,7%,9% MoS2的MoS2/Ni60A涂层表面成形良好,与35CrMnSi钢基体形成了良好的冶金结合。涂层的主要物相为MoS2、γ-Ni固溶体、NiS、Cr2B。涂层底部与熔合线处的组织为粗大的平面晶和柱状晶,而涂层中、上部组织主要为短棒状、鱼骨状和放射状的树枝晶。
(2) 随着MoS2添加量的增加,涂层的显微硬度呈降低趋势,磨损量增加,摩擦因数先减小后增大,当MoS2质量分数为3%时,涂层的摩擦因数波动最小,且平均摩擦因数最小,为0.43,其主要磨损机理为轻微的磨粒磨损。
