铁素体薄壁对接焊缝(壁厚一般为3~6 mm)在制造期间,受余高等结构信号影响,常规超声检测较为困难,缺陷信号信噪比低,检测效率低。因此,薄壁对接焊缝一般采用射线检测,射线检测对该类焊缝有着较高的灵敏度,尤其对微小的体积型缺陷有着良好的分辨力。但是在工程应用过程中,会出现由于结构限制或墙体阻挡等无法实施射线检测的情况,超声检测成为唯一可替代的体积检测方法,而常规超声检测方法亦存在无法满足需求的情况。
相控阵超声检测(PAUT)技术具有声束聚焦灵活可控,在不改变探头布置的前提下,可对检测对象进行多角度、多方位扫查的特点,能将信号显示为直观的扇扫图像,从而降低缺陷漏检概率,提高检测可靠性。
笔者采用相控阵超声探头对含有缺陷的模拟试件进行检测,并与射线检测的结果做对比,总结出薄壁铁素体焊缝的相控阵超声检测验收准则。
1、薄壁对接焊缝的规范要求
薄壁对接焊缝的无损检测方法一般为射线检测,依据标准RCC-M-2007《压水堆核岛机械设备设计和建造规则》或NB/T 20003.3-2010《核电厂核岛机械设备无损检测 第3部分:射线检测》,射线检测适用于任意厚度的全焊透对接焊缝和角焊缝,标准中还规定了检测薄壁对接焊缝相应的射线源、像质计、透照方式、图像质量等检测工艺要求。相关验收准则如表1所示。
表1 不同标准中薄壁焊缝的射线检测适用范围及验收准则
|
|
|
|
适用于各种厚度的均匀或非均匀的全焊透对接焊缝和角焊缝
|
具有下述任何一种情况的焊缝均为不合格:
① 任何形式的裂纹、未熔合、未焊透、咬边;
② 壁厚≤6 mm时缺陷最大尺寸大于1.5 mm的单个气孔或者单个夹渣。
|
|
适用于任意厚度1、2、3级同质或异质的全焊透对接和角接接头
|
具有下述任何一种情况的焊接接头均为不合格:
① 任何裂纹、未熔合、未焊透、咬边;
② 壁厚≤6 mm时最大尺寸大于1.5 mm的任何单个圆形缺陷;
③ 壁厚≤6 mm时最大尺寸大于1.5 mm的任何单个条形缺陷。
|
同时,当前核电领域主要规范均规定了超声检测的适用范围(均要求全焊透对接焊缝壁厚≥6 mm),如RCC-M-2007规范适用范围为厚度≥10 mm的对接焊缝;NB/T 47013-2015《承压设备无损检测》适用于厚度≥6 mm筒体的对接焊缝;NB/T 20003.2-2010适用于厚度不小于8 mm焊件的全焊透对接焊缝,不同规范的对接焊缝超声检测适用范围如表2所示。对于壁厚小于6 mm的薄壁对接焊缝,超声检测方法及质量等级要求没有规范可以依据。
表2 不同规范的对接焊缝超声检测适用范围
规范名称 |
章节 |
适用范围 |
RCC-M-2007 |
MC2600 |
全焊透焊缝:适用于厚度≥10 mm焊件的全焊透对接焊缝和角焊缝 |
NB/T 47013-2015 |
第6章 |
筒体对接焊缝:适用于厚度≥6 mm锅炉、压力容器对接、角接及T型接头 |
NB/T 20003.2-2010 |
第18章 |
厚度不小于8 mm焊件的全焊透对接焊接接头和角接焊接接头 |
2、薄壁对接焊缝的相控阵超声检测技术
相控阵超声检测工艺
超声检测薄壁对接焊缝时,受焊缝余高的影响,超声一次波声束只能覆盖焊缝根部区域。笔者采用相控阵超声分区域覆盖检测,其中采用较大的声束角度覆盖一次波和二次波区域,采用较小声束角度覆盖三次波和四次波区域,相控阵探头声束覆盖示意如图1所示。
图1 薄壁对接焊缝的相控阵探头声束覆盖示意
相控阵超声多角度扫查的特性,为薄壁结构的超声检测提供了较好的解决方案,并且在显示判别方面更为直观,扇形扫查区域覆盖如图2所示。
图2 扇形扫查区域覆盖示意
通过相控阵超声声束仿真,可以看出当使用45°~75°范围的扇扫,探头前端距离焊缝中心线5~9 mm时,相控阵扇形声束的二次波和三次波可完全覆盖整个焊缝区域,同时一次波和四次波扇形声束可以部分覆盖焊缝区域,如图3所示。
图3 探头前端距离焊缝中心线5 mm和9 mm时的声束覆盖示意
为了提高检测效率,试验中采用单轴的直线扫查,替代传统的两轴栅格扫查。由于现场焊接的对接焊缝余高宽度不一致,故灵活选取探头前端距离焊缝中心线的距离(5~9 mm),可以适应不同的焊缝余高宽度,保证一次沿焊缝方向的扫查能够完整覆盖整个被检区域。
相控阵探头设计
一般来说,探头频率越高,晶片越大,探头的声束指向性越好,缺陷分辨率越高。同时,单个晶片的尺寸越小,可获得更强的声束偏转能力与更大的声束有效角度范围,还可以减少栅瓣,避免伪信号的产生。因此,对于薄壁对接焊缝,通常采用小晶片尺寸阵列和高频率探头,利用扇形多次反射波实施检测。以6 mm厚钢板对接焊缝为例,为保证在二次波至三次波深度范围内有更好的检测效果,可设置相控阵探头声场-6 dB焦柱范围为4~16 mm,不同角度的相控阵探头声场强度分布如图4所示。
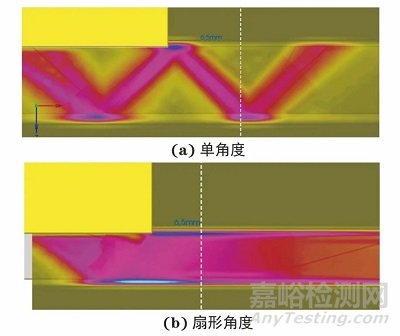
图4 不同角度的相控阵探头声场强度分布
通过对薄壁管各参数进行声场仿真,确定采用频率为5 MHz,晶片间距为0.31 mm的相控阵探头,楔块公称角度为60°。
3、声场仿真
模拟试件缺陷设计
为了研究相控阵超声的缺陷检出能力,设计制作了17块含不同缺陷的铁素体薄壁对接试件,所有试件厚度均为6 mm,且均保留焊缝余高。其中气孔和夹渣缺陷设计尺寸(直径)为1.2~1.5 mm,未熔合缺陷的设计长度为5 mm和10 mm。
试块中含27个气孔缺陷、18个夹渣缺陷和6个未熔合缺陷,共计45个体积性缺陷和6个非体积性缺陷。
缺陷仿真计算
仿真计算采用与实际检测一致的相控阵检测工艺,灵敏度设置参照CIVA仿真计算结果,采用2 mm直径长横孔设置TCG曲线。17个模拟试件中不同类型缺陷(如气孔、夹渣以及未熔合)信息与仿真灵敏度计算结果如表3所示。
表3 模拟试件缺陷及其仿真与检测结果
通过声场仿真,可知当前相控阵检测工艺可以检测出模拟试件所设计的缺陷。其中,气孔的仿真与实测信号如图5所示,未熔合的仿真与实测信号如图6所示。
图5 气孔的缺陷仿真与实测信号
图6 未熔合的缺陷仿真与实测信号
4、相控阵超声检测试验及应用
模拟件检测试验
试验过程中使用参考试块上2 mm直径长横孔作为反射体,对一次波到三次波范围内的孔,采用TCG模式设置灵敏度曲线。通过试验确定采用45°~75°的扇扫角度范围,来实现所有角度的TCG曲线标定。
然后采用标定后的TCG曲线对模拟试件中45个体积型缺陷和6个非体积型缺陷实施超声相控阵检测,模拟试件缺陷检测结果如表3所示。可见当前模拟试件中所有缺陷均可被检出,体积型缺陷的实测灵敏度与声场仿真灵敏度符合度为80%,非体积型缺陷的实测灵敏度与声场仿真灵敏度符合度为100%。气孔和夹渣缺陷的相控阵超声典型信号如图7所示,未熔合缺陷的相控阵超声典型信号如图8所示。
图7 气孔和夹渣缺陷的相控阵超声典型信号
图8 未熔合缺陷的相控阵超声典型信号
依据表1中RCC-M-2007或NB/T 20003-2010规范射线检测验收准则,对于壁厚不大于6 mm的薄壁对接焊缝不允许存在尺寸大于1.5 mm的单个气孔或者单个夹渣。同时,基于表3中对于尺寸大于1.5 mm的单个气孔或者单个夹渣的仿真和相控阵实测结果分析,22个ф1.5 mm气孔缺陷中有18个幅值>ф2 mm-15 dB,7个ф1.5 mm夹渣缺陷中有5个幅值>ф2 mm-13.2 dB,且所有气孔和夹渣类缺陷实测结果均大于ф2 mm-24 dB。因此,对于壁厚不大于6 mm薄壁对接焊缝的超声相控阵检测初步验收准则如下:
(1)应记录灵敏度大于等于ф2 mm-24 dB的缺陷;
(2)凡判定为裂纹、未熔合和未焊透的缺陷显示,评为不合格;
(3)灵敏度大于等于ф2 mm-15 dB或者长度≥5 mm的缺陷显示,评为不合格。
现场焊缝相控阵超声检测
在国内某核电厂进行PAUT技术验证,其大部分薄壁对接焊缝处于结构限制或墙体阻挡状态,另外约1000 m焊缝未受限制,对未受限制焊缝实施了射线检测。其中,相控阵超声检出且RT评判为超标缺陷的缺陷数量为309个,按照上述的初步验收准则判定,其结果如表4和表5所示,对于所有309个RT超标缺陷,PAUT的综合判废率为77%(72.5%+4.5%)。
表4 RT超标缺陷PAUT反射波幅判定结果(≥ф2 mm-15 dB)
RT超标缺陷类型: |
非体积型缺陷 |
体积型缺陷 |
PAUT判废线 |
≥ф2 mm-15 dB |
PAUT检出的RT超标缺陷数量 |
40 |
269 |
PAUT判废缺陷数量 |
36 |
188 |
PAUT判废率 |
90 |
69.9 |
PAUT判废率(合计) |
72.50% |
表5 RT超标缺陷PAUT最大允许指示长度判定结果(5 mm)
PAUT超标缺陷反射波幅 |
<ф2 mm-15 dB |
PAUT最大允许指示长度 |
5 mm |
PAUT检出的RT超标缺陷数量 |
309个 |
PAUT判废缺陷数量 |
14个 |
PAUT判废率 |
4.50% |
薄壁对接焊缝验收准则
射线检测与相控阵超声检测属于两种不同的体积检测方法,其中射线检测对于体积性缺陷检出率较高,超声检测对于非体积性缺陷检出率较高。同时,壁厚不大于6 mm的薄壁对接焊缝受余高及焊缝内外表面状态等影响,结构信号及变形波信号较多,缺陷较难判定。因此,结合模拟试件试验及现场焊缝的试验结果分析,认为当前的相控阵超声初步验收准则可作为最终验收准则用于薄壁对接焊缝的现场检测。
工程应用
采用该相控阵超声检测技术对国内某核电厂几千米的薄壁对接焊缝实施自动检测,并检出了大量缺陷,这些缺陷均经过了打磨去除、修补、计算等处理。其中,某典型缺陷PAUT信号及形貌如图9所示,经数据分析得到一段长46 mm的断续显示,采用砂轮机逐层(每层0.5 mm)去除焊缝,打磨约2 mm后发现多个夹渣和气孔缺陷,可以看出其打磨结果与相控阵检测结果完全一致。
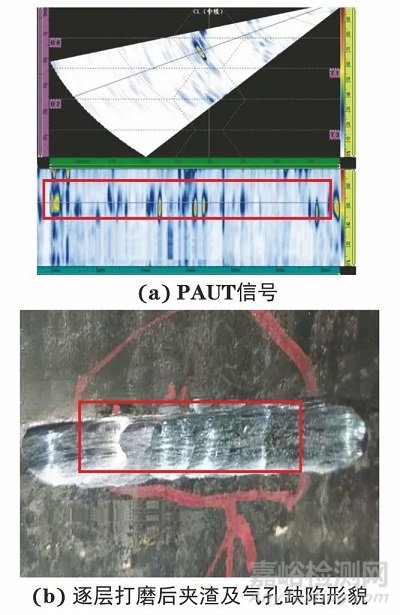
图9 某典型缺陷的PAUT信号及形貌
5、结语
通过声场仿真、大量模拟试件缺陷检测以及现场焊缝RT检测,结合现场焊缝中相控阵缺陷显示信号与逐层挖凿后气孔、夹渣的一致性试验结果,给出了薄壁对接焊缝相控阵超声验收准则,对特定情况下的超声检测结果验收具有很好的指导作用,对类似结构焊缝的超声检测结果验收具有借鉴意义。
