某衬筒零件材料为退火态,其热处理工艺为高频淬火+回火,衬筒的淬火区域为倒角端头处下沿20~25mm,硬度要求为60~63.3HRC,淬火区马氏体等级按照相关文件要求应不大于7级。范语萱和李波两位研究人员采用一系列理化检验方法对该衬筒零件的断裂原因进行分析,以避免该类事故再次发生。
1、 理化检验
1.1 宏观观察
衬筒的断裂区为端头倒角区,整个衬筒外表面紧靠倒角区一周可见约5mm宽的磨损痕迹,衬筒整体宏观形貌如图1所示。衬筒的断面粗糙,断口约占整个圆周的42%,其余部分为零件原始表面(见图2)。
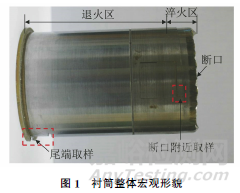
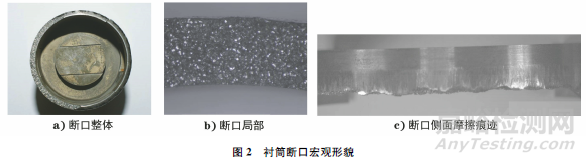
1.2 化学成分分析
对衬筒材料进行化学成分分析,结果如表1所示,由表1可知:衬筒材料满足GB/T 1298—2008《碳素工具钢》对T10A钢的要求。
1.3 扫描电镜分析
用扫描电子显微镜(SEM)对衬筒的断口进行分析,可见断口为典型的沿晶特征(见图3)。在轴向距断口约10mm处取样,发现断口形貌与原始断口形貌一致,呈沿晶特征(见图4)。在衬筒尾端取样,断口呈解理+韧窝形貌(见图5)。
1.4 金相检验
垂直于断口切取金相试样,截面经磨抛、腐蚀后,在光学显微镜下观察,发现其显微组织为较粗大的马氏体,按相关工艺文件进行评定,针状马氏体评级为10级(见图6)。
1.5 显微硬度测试
衬筒端头断口附近的硬度为60.0~61.0HRC,符合相关技术要求。
从断口一侧向内依次进行显微硬度测试,根据GB/T 1172—1999 《黑色金属硬度及强度换算值》,结合显微硬度测试结果绘制淬火区硬度-距离曲线(见图7),可知淬火区深度约为21.2mm。
1.6 不同热处理参数对衬筒材料性能的影响规律
为了评估该零件在目前型号飞机上的稳定性及可靠性,掌握该材料热处理后的各项性能,对衬筒材料开展热处理工艺试验。分析不同热处理工艺参数对衬筒材料马氏体等级、力学性能、冲击性能等的影响规律,试验结果如表2所示。
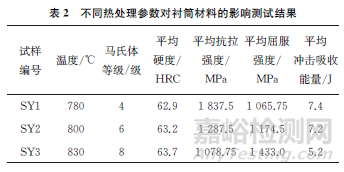
2、 综合分析
衬筒断裂区为端头倒角区,整个衬筒外表面紧靠倒角区一周存在宽约5mm的严重磨损区,说明衬筒端头受到与其配合部件的摩擦作用。断面粗糙,可见反光小刻面,说明弹舱门作动衬筒为脆性断裂。
断口分析结果表明:衬筒断口为典型的沿晶特征,轴向距断口约10mm处的断口与原始断口形貌一致,呈沿晶特征;在衬筒尾端取样的断口呈解理+韧窝形貌,说明在淬火区域的材料脆性较大,韧性较低,断裂表现为脆断特征。
金相检验结果表明:材料的显微组织为较粗大的马氏体,针状马氏体评级为10级,不符合该衬筒零件热处理的要求(热处理后马氏体组织按上述工艺文件评定,不应超过7级)。
通过对不同热处理工艺参数下衬筒材料的马氏体等级、力学性能、冲击性能进行试验,可知随着淬火温度的升高,马氏体等级随之上升,硬度也随之增加,更为粗大的马氏体组织造成材料脆性增加,材料几乎没有发生塑性变形,没有经历明显屈服阶段,抗拉强度实测值随之降低,材料在更早的阶段发生断裂。在冲击载荷作用下,冲击吸收能量的实测值随之降低,即材料的抗冲击性能下降,而压缩屈服强度的实测值随之升高。
硬度测试结果表明:衬筒端头断口附近的硬度为60.0~61.0HRC,结合显微硬度测试结果绘制淬火区深度曲线,淬火区深度约为21.2mm。靠近端头的显微硬度比远离端头的显微硬度高,根据GB/T 1172—1999标准换算可知,淬火区部分硬度偏高。
综上所述,衬筒端头经过局部淬火处理后,由于温度较高,奥氏体晶粒粗化,并且材料含碳量较高,过热奥氏体中含有大量的碳,淬火后得到含有显微裂纹的粗片状马氏体,使钢的脆性增大,在使用中受到与其匹配零部件的摩擦、挤压作用,当挤压作用力达到一定程度时,衬筒发生脆性断裂。
3、 结语
通过以上分析,可确认该衬筒发生脆性断裂。断裂的原因是:当零件加热温度超过组织转变最大限制温度时,淬火温度过高,消除了奥氏体中的低碳区,使奥氏体的化学成分基本均匀,晶体缺陷显著减少,这就为马氏体组织的定向形核和长大清除了障碍,进而形成粗大马氏体组织,随着淬火温度的升高,马氏体等级随之上升,硬度也随之增加。即淬火温度过高导致马氏体等级超标,硬度提高,钢的脆性增大。
