为给某锁筒机构导向基座和导向杆摩擦副配对选材,研究了轧制态、固溶态、固溶+时效态2A12铝合金与时效态17-4PH不锈钢组成的摩擦副在干摩擦和抹润滑脂润滑条件下的摩擦磨损性能。结果表明:轧制态2A12铝合金的抗拉强度和显微硬度高于固溶态和固溶+时效态,远低于时效态17-4PH不锈钢;在抹润滑脂润滑条件下,轧制态2A12铝合金与17-4PH不锈钢配副的平均摩擦因数以及轧制态铝合金的平均体积磨损率明显低于干摩擦条件下,并且低于相同润滑条件下固溶态和固溶+时效态2A12铝合金;2种润滑条件下3种状态铝合金的磨损机制均以磨粒磨损为主、黏着磨损为辅,不锈钢的磨损机制为轻微磨粒磨损。锁筒机构可以选择轧制态2A12铝合金与时效态17-4PH不锈钢进行配对,通过涂抹润滑脂来减少摩擦磨损卡滞现象。
1、 试样制备与试验方法
1.1 试样制备
试验材料:2A12铝合金轧制棒材,规格为ϕ45mm,17-4PH不锈钢锻件,规格为ϕ50mm。
使用线切割机将2A12铝合金轧制棒材加工成尺寸为ϕ45mm×130mm的试样,置于箱式电阻炉中进行固溶处理,固溶处理工艺为500 ℃保温2h水冷,然后置于电热鼓风干燥箱中进行时效处理,时效处理工艺为190℃保温10h空冷。
使用线切割机将17-4PH不锈钢锻件加工成尺寸分别为ϕ50mm×80mm和ϕ20mm×130mm的试样,置于箱式电阻炉中进行固溶处理,固溶处理工艺为1040℃保温1h油冷,再进行时效处理,时效处理工艺为480℃保温4h空冷。
1.2 试验方法
将不同状态铝合金试样以及时效态不锈钢试样均加工成尺寸为ϕ20mm×14mm的金相试样,经磨抛,腐蚀液腐蚀后,在光学显微镜下观察显微组织。其中,2A12铝合金使用的腐蚀液由体积比1∶5∶15的氢氟酸、硝酸和盐酸组成,17-4PH不锈钢使用的腐蚀液由体积比1∶2的硝酸和盐酸组成。
将不同状态铝合金试样以及时效态不锈钢试样均加工成标距段尺寸为ϕ10mm×50mm的标准拉伸试样,根据GB/T 228.1—2010,使用电子万能试验机进行室温拉伸试验,屈服前的拉伸速度均为1mm·min-1,屈服后为25mm·min-1,各测试3个平行试样取平均值。
按照GB/T 4340.1—2009,采用数显维氏硬度计测试铝合金试样的显微硬度,载荷为2.942N,保载时间为15s,不同状态试样各测3个点取平均值。按照GB/T 230—2018,采用洛氏硬度计测试不锈钢试样的洛氏硬度,各测3个点取平均值。根据GB/T 1172—1999,将不锈钢试样的洛氏硬度转化成为显微硬度。
在铝合金试样上截取尺寸为7mm×7mm×30mm的方块试样,表面粗糙度Ra为0.40μm;在不锈钢试样上截取尺寸为ϕ40mm×ϕ16mm×10mm的圆环试样,外圆表面粗糙度Ra为0.40μm。按照GB/T 12444-2006,在摩擦磨损试验机上进行圆环-方块摩擦磨损试验,试验温度为室温24℃,相对湿度为(50±5)%,方块试样压在圆环试样上,载荷为245N,圆环试样转速为200r·min-1,相对方块试样的线速度为0.42m·s-1,试验时间为120min。采用2种润滑方式,一是干摩擦,二是试验前涂抹XG/LT二硫化钼锂基润滑脂,试验过程中不再加润滑脂。在摩擦试验过程中由仪器自动记录力矩随时间的变化,通过力矩计算摩擦因数,平均摩擦因数取试验60~120min时摩擦因数的平均值。摩擦因数计算公式如下:
采用三维激光扫描电子显微镜观察试样表面摩擦磨损形貌。按照GB/T 12444—2006,用游标卡尺测量方块试样表面的磨痕宽度,在整个磨痕长度方向的中间及两侧1/4长度处进行测量,取平均值。计算方块试样平均体积磨损率,公式如下:

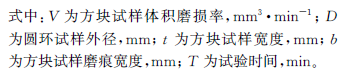
2、 试验结果与讨论
2.1 显微组织
由图1可见:轧制态、固溶态、固溶+时效态3种状态的2A12铝合金显微组织都由基体α(Al)固溶体及其上分布的颗粒状S(Al2CuMg)相和条状Al6FeMnSi相组成;时效态17-4PH不锈钢的显微组织为回火马氏体和弥散分布析出相。
2.2 拉伸性能与显微硬度
由表1可见:轧制态2A12铝合金因发生形变强化,其抗拉强度和显微硬度最高;固溶处理消除了形变强化,使得组织均匀,因此固溶态2A12铝合金的强度和显微硬度低于轧制态,但时效处理后强度和显微硬度又有所提高。时效态17-4PH不锈钢的显微硬度与强度远高于2A12铝合金。
表1 不同状态2A12铝合金和时效态17-4PH不锈钢的力学性能
2.3 摩擦磨损性能
由图2可见:在整个摩擦磨损过程中,轧制态2A12铝合金与17-4不锈钢在抹润滑脂润滑条件下的摩擦因数均明显小于在干摩擦条件下;固溶态、固溶+时效态2A12铝合金与17-4不锈钢在抹润滑脂润滑条件下的摩擦因数在摩擦磨损前期明显小于干摩擦条件下,而在摩擦磨损中后期与干摩擦条件下相近。
计算得到轧制态、固溶态、固溶+时效态2A12铝合金与17-4PH不锈钢在干摩擦条件下的平均摩擦因数分别为0.23,0.22,0.24,铝合金试样的平均体积磨损率分别为0.346,0.328,0.581mm3·min-1;在抹润滑脂润滑条件下的平均摩擦因数分别为0.11,0.22,0.22,铝合金试样的体积磨损率分别为0.008,0.207,0.176mm3·min-1。可见:轧制态2A12铝合金与17-4PH不锈钢在抹润滑脂润滑条件下的平均摩擦因数以及轧制态铝合金的平均体积磨损率均明显低于在干摩擦条件下,并且低于相同润滑条件下固溶态和固溶+时效态2A12铝合金。
2A12铝合金在轧制过程中会形成高密度位错,产生点阵畸变、空位或气孔等微缺陷;在摩擦磨损过程中这些缺陷能有效吸附、存储润滑脂,使得摩擦表面形成稳定润滑转移膜,并且在膜破裂时能快速形成新的润滑膜。因此,轧制态2A12铝合金在抹润滑脂润滑条件下的摩擦因数一直较低,平均体积磨损率最小。
2.4 磨损形貌
由图3可见:3种状态2A12铝合金试样在干摩擦条件下的表面划痕明显,为金属间的划伤、擦伤与犁沟,主要发生磨粒磨损,同时表面还出现少量磨损脱落的黏附物,说明存在少量黏着磨损;在抹润滑脂润滑条件下3种状态铝合金试样表面主要存在划痕,局部散落着颗粒状附着物,其磨损机制仍以磨粒磨损为主、黏着磨损为辅。
17-4PH不锈钢的显微硬度远高于2A12铝合金,二者的表面粗糙度Ra都为0.40μm,其相互间的磨损过程主要为17-4PH不锈钢对铝合金进行磨粒磨损。此外,由于铝合金的熔点很低,在摩擦热作用下铝合金表面局部易发生熔焊、黏结而产生少量黏着磨损。
与3种状态2A12铝合金在干摩擦及抹润滑脂润滑条件下摩擦磨损后,时效态17-4PH不锈钢表面出现轻微划痕,如图4所示,其磨损机制均主要为轻微磨粒磨损。
3、 结 论
(1) 对比3种状态铝合金,轧制态2A12铝合金的抗拉强度和显微硬度最高;时效态17-4PH不锈钢的显微硬度和强度则远高于3种状态铝合金。
(2) 在整个摩擦磨损过程中,轧制态2A12铝合金与17-4PH不锈钢在抹润滑脂润滑条件下的摩擦因数均明显小于在干摩擦条件下的摩擦因数;固溶态、固溶+时效态2A12铝合金在抹润滑脂润滑条件下的摩擦因数在摩擦磨损前期小于干摩擦条件下,中后期增大,与干摩擦条件下相近;轧制态2A12铝合金与17-4PH不锈钢在抹润滑脂润滑条件下的平均摩擦因数以及轧制态铝合金的平均体积磨损率明显低于在干摩擦条件下,并且低于相同润滑条件下固溶态和固溶+时效态2A12铝合金。
(3) 在干摩擦及抹润滑脂润滑条件下摩擦磨损后,3种状态2A12铝合金的表面划痕、黏附物明显,磨损机制以磨粒磨损为主、黏着磨损为辅;17-4PH不锈钢表面划痕较轻微,磨损机制为轻微磨粒磨损。
(4) 综合考虑锁筒机构使用要求和摩擦磨损性能研究结果,锁筒机构可以选择轧制态2A12铝合金与时效态17-4PH不锈钢进行配对,通过涂抹润滑脂来减少摩擦磨损卡滞现象。
