Z2CND17-12奥氏体不锈钢为法国RCC-M《压水堆核岛机械设备设计和建造规则》中的牌号,其近似牌号为GB/T 14975—2012 《结构用不锈钢无缝钢管》中的022Cr17Ni12Mo2钢。该材料因具有良好的力学性能、耐腐蚀性能、组织稳定性和抗中子辐照性能,被广泛用于核电站设备中。某核电机组检修过程中发现材料为Z2CND17-12钢的阀门引漏管发生多次开裂。阀门引漏管的主要作用是将阀门泄漏的介质引流至泄压箱,阀门介质主要为含硼水,引漏管从安装至断裂共运行约5a,引漏管的规格为21.3mm×2.77mm(外径×壁厚),管内压力为0.2MPa。来自福建宁德核电有限公司和西安热工研究院有限公司的叶永魁等研究人员采用一系列理化检验方法对该阀门引漏管的开裂原因进行了分析,并提出了相关建议。
1、理化检验
1.1宏观观察
截取开裂引漏管的宏观形貌如图1所示。横向裂纹断面的宏观形貌如图2所示。由图1~2可知:开裂引漏管内表面存在多条环向裂纹;裂纹断面无宏观塑性变形,呈脆性断裂特征;裂纹面上存在黄褐色腐蚀痕迹。
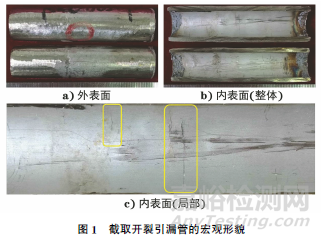
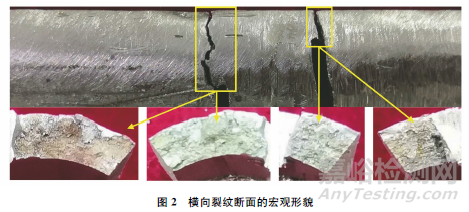
1.2化学成分分析
对开裂引漏管试样进行化学成分分析,结果如表1所示。由表1可知:试样的化学成分分析结果符合RCC M M3304—2007 《用于1,2级和3级设备的奥氏体不锈钢钢管(热交换器管除外)》对Z2CND17-12钢的要求。
1.3金相检验
在试样开裂部位制取纵向试样,在光学显微镜下观察,结果如图3所示。由图3可知:试样的显微组织为奥氏体,晶粒度均为6~8级,未见异常;近内、外壁显微组织未见明显差异。试样裂纹均由内壁向外壁穿晶开裂,裂纹存在很多分枝,裂纹尖端多呈树枝状分叉,为应力腐蚀裂纹的特征;外壁未见异常。
1.4维氏硬度测试
按照GB/T 4340.1—2009 《金属材料 维氏硬度试验 第1部分:试验方法》对金相试样进行维氏硬度测试,测点位置如图4所示,测试结果如表2所示。由表2可知:试样的硬度略高于GB/T 14975—2012对Z2CND17-12钢的要求;裂纹附近及远离裂纹处的硬度未见明显差异。

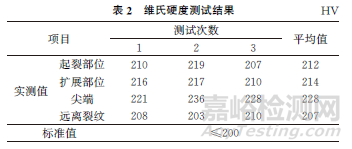
1.5扫描电镜(SEM)分析
截取开裂引漏管试样,其内表面及横向裂纹断面的SEM形貌如图5~6所示。由图5~6可知:试样内表面存在腐蚀裂纹和腐蚀坑,腐蚀裂纹中充满腐蚀产物,外表面未见异常;横向裂纹打开后的裂纹断面呈脆性穿晶开裂特征,无疲劳断裂特征,裂纹面上有一层腐蚀产物。
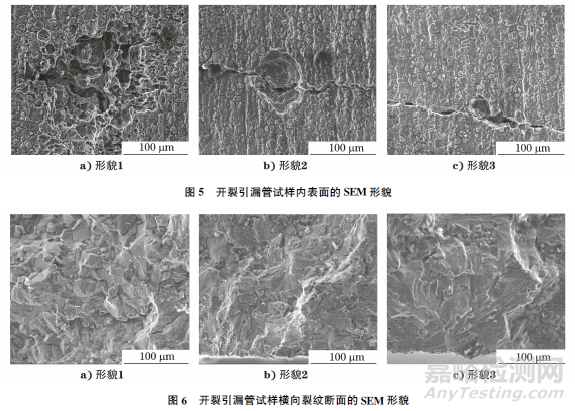
1.6能谱分析
试样内表面断口和横向裂纹断面的能谱分析位置如图7所示,分析结果如表3所示。由表3可知:内表面及横向裂纹断面均存在腐蚀性元素氯。
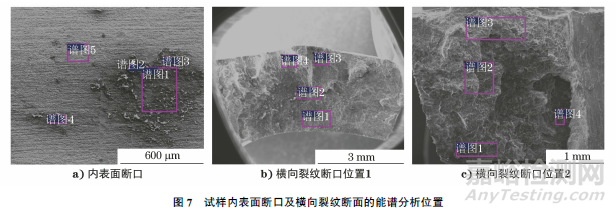
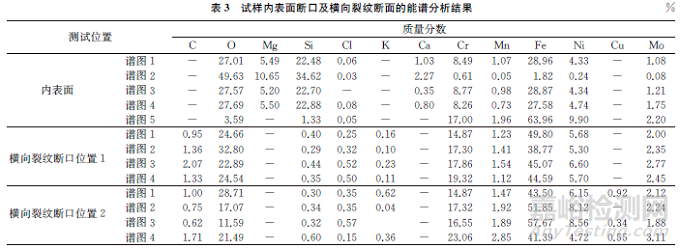
2、综合分析
引漏管材料的硬度高于标准要求,化学成分及显微组织未见异常。引漏管内表面存在多条环向裂纹,微观下存在因腐蚀形成的腐蚀裂纹和腐蚀坑;裂纹面无宏观塑性变形,呈脆性穿晶开裂,无疲劳断裂特征,裂纹面上存在黄褐色的腐蚀产物;由内壁向外壁发生穿晶开裂,存在很多分枝,尖端多呈树枝状分叉;内表面及裂纹面均存在腐蚀性元素氯。裂纹特征均属于应力腐蚀裂纹。
应力腐蚀是材料、环境、应力相互作用的结果。材料对应力腐蚀的敏感性与材料的强度、显微组织、杂质含量、所受应力的大小以及腐蚀介质等因素有关。
硬度超标表明开裂引漏管试样残留较高的残余应力,是应力腐蚀开裂的根源。内壁均有腐蚀坑,表明管内存在少量氯离子引起的点蚀。阀门内部流动的一回路介质,是严格控制氯离子的除盐水,但不能排除少量渗漏的一回路水中氯离子的富集,也不排除在人为去污擦拭过程中引入氯离子的可能。
综上所述,引漏管开裂的原因为应力腐蚀,腐蚀介质为氯离子,在应力和腐蚀介质氯离子的共同作用下,发生了应力腐蚀开裂。
3、结语
引漏管开裂的原因为应力腐蚀,腐蚀介质为氯离子。建议严格控制引漏管内的氯离子含量,并使用经过充分固溶处理的引漏管,以降低应力腐蚀的敏感性。
