摘要:本文将副车架的铸铁材料更改为铝合金材料,对副车架的结构进行了优化,并利用Nastran有限元分析软件对新结构的强度、刚度以及模态性能进行了验证。分析了其铸造和机加工难点,并对铸造工艺以及机加工方案进行了设计。加工完成后,对副车架进行了疲劳耐久试验以及耐腐蚀性试验。试验结果验证了该副车架满足开发要求,达到减重的目的。
引言
汽车副车架是底盘的重要部件之一,支撑前后车桥和悬挂,使用副车架能够提高汽车的舒适性和安全性[1]。现在汽车厂商广泛使用铝合金材料替代钢材料来达到轻量化的目的[2],通过三维软件建模以及有限元软件进行分析校核可以高效完成副车架的设计工作[3]。然而,铝合金副车架的结构特点决定了其铸造和机加工的难度大幅增加,不合理的加工方法可能会导致气孔、缩松、夹渣以及变形等质量问题[4]。本文首先对原有结构进行了优化设计,并通过有限元分析对其强度、刚度以及模态性能进行了验证。然后根据副车架的铸造和机加工难点,分别设计了铸造工艺和机加工方案,加工完成的副车架没有出现加工问题。最后通过台架疲劳耐久试验和耐腐蚀性试验对副车架进行了验证。
1、副车架结构优化设计
将铝合金材料直接替换铸铁的副车架无法保证其性能要求,所以需要进行优化设计。其优化过程主要经过多轮拓扑优化、CAD设计以及CAE分析等,副车架优化后的结构如图1所示。
图1 副车架优化后的结构
针对副车架结构主要有以下几个改动:①副车架底部增加盖板,形成封闭腔结构,增加了刚度与模态性能;②对肋板进行了改进设计,使其满足性能要求。新设计的副车架质量为11.76 kg,相比原来的17 kg,减重比例达到30.8%。
2、副车架有限元仿真分析
副车架材料采用铝合金ZL114A-T6,其材料参数见表1。将副车架三维模型导入Nastran有限元分析软件中,网格划分的单元类型为CTETRA(二阶四面体)。
表1 副车架材料参数
2.1 副车架强度分析
选择1 g垂直加载、3.5 g垂直加载、左前轮3 g垂直加载、右后轮3 g垂直加载、左转、右转、刹车、刹车左转以及刹车右转等9种汽车运行工况对副车架进行强度分析,根据工况分别对副车架各硬点位置施加不同的载荷。
通过静强度分析,发现在刹车工况下,其强度分析数值相较于其他工况最高,分析结果见表2,分析云图如图2所示。
表2 刹车工况强度分析结果
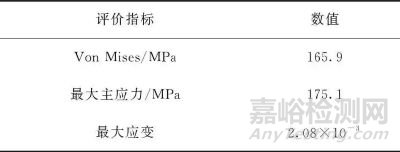
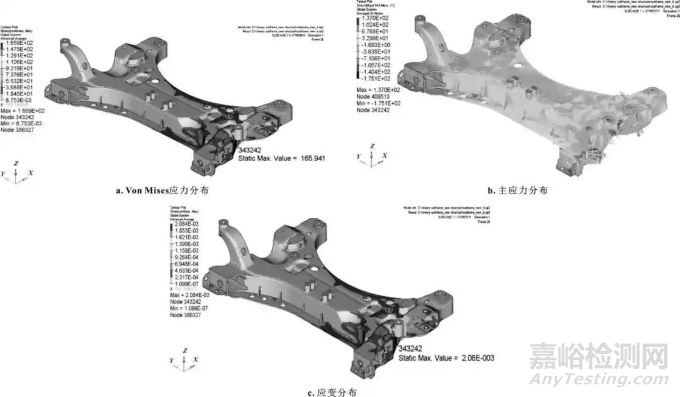
图2 刹车工况强度分析云图
由图2和表2分析结果可知,该副车架满足强度设计要求。
2.2 副车架刚度分析
对副车架有限元模型设定边界条件,其刚度约束如图3所示,通过对其关键部位的硬点刚度进行分析以评价硬点刚度的性能。
图3 副车架刚度约束
由图3的有限元分析结果发现,副车架各个安装点的刚度均达到目标要求,其中最大变形发生在下控制臂右后安装点。下控制臂右后安装点刚度分析结果见表3,其X向、Y向、Z向位移云图如图4至图6所示。
图4 下控制臂右后安装点X向位移云图
表3 下控制臂右后安装点刚度分析结果
图5 下控制臂右后安装点Y向位移云图
图6 下控制臂右后安装点Z向位移云图
2.3 副车架模态分析
本文主要考虑了低阶固有频率对副车架的影响,其自由模态和约束模态一阶弯曲振型云图分别如图7和图8所示。
图7 副车架自由模态一阶弯曲振型云图
图8 副车架约束模态一阶弯曲振型云图
由以上振型云图可知,自由模态一阶弯曲频率为281.9 Hz,约束模态一阶弯曲频率为372.7 Hz,都大于250 Hz,满足设计要求。
3、副车架加工工艺设计
3.1 副车架铸造工艺设计
针对副车架铝合金铸造工艺,目前国内外流行的主要有高圧铸造、挤压铸造和重力铸造等[2]。高压铸造工艺是通过高压下高速冲型,使得液态铝合金凝固结晶,得到的毛坯表面光洁度好,强度和硬度都比较高,有较好的力学性能,但是延伸率较低,而且无法对其进行热处理;挤压铸造是通过将液态金属倒入敞口模具中,使其形成初步形状再施加高压完成毛坯制作,其力学性能好、尺寸精度高,后期可以进行热处理;重力铸造是在重力的作用下注入铸型,晶体组织不够致密,但可以通过后期热处理来增强力学性能。出于制造成本和数量的综合考虑,本文选择工艺成熟、成本较低的重力铸造方式。
砂型重力铸造的砂型模具目前有传统方法和3D打印两种方式完成。传统的砂型制造流程一般为:CAD设计→工艺仿真→模件制作→工装夹具制作→砂型模具制造→铸造。3D打印的砂型铸造流程为:CAD设计→工艺仿真→砂型模具3D打印→铸造。通过3D打印砂型模具有效简化了传统砂型制造的流程,大大提高了生产效率,因此本文选择3D打印砂型工艺。
由于在铸件的凸台以及厚大部位均有容易产生疏松、缩孔等缺陷的风险存在,而且铸件壁厚较薄,为异型结构,在成型收缩过程及后续热处理时,易发生扭曲,导致大平面变形。本文考虑在前后端面以及厚大位置设置冒口,冒口加快铸件厚大区域的凝固速度,避免产生内部疏松缺陷,并且采用前后多点进胶流道设计,减少进胶时间,减小壁厚较薄处的凝固速度。所设计的铸造模具结构如图9所示,排气口、冒口和浇注流道示意如图10所示。
图9 铸造模具结构
图10 排气口、冒口和浇注流道示意
铸造完成的副车架如图11所示。由图可以看出,该副车架没有出现气孔、缩松、夹渣以及变形等铸造问题。
图11 铸造完成的副车架
3.2 副车架机加工设计
需要对上述铸造完成的副车架进行机加工处理,考虑到副车架的结构特点,机加工主要有以下几个难点:①零件为薄壁筋板类零件,采用砂铸,毛坯不易找正;②零件筋板多、结构复杂、壁薄,为对称结构,壁厚只有5 mm,加工易变形;③零件上下左右前后均有孔系,为对称孔系,且工件尺寸较大、加工要求较高。针对以上难点,设计的整体加工方案分为粗加工留余量后精加工,在加工过程中采用专用工装,配辅助支撑加以装夹。粗加工过程是先以筋板面螺钉搭子、孔搭子作为粗定位基准,对顶面进行粗加工,如图12所示。之后以粗加工顶面定位,对筋板上螺钉搭子、孔搭子及周边加工部位进行粗加工,如图13所示。精加工过程重复上述顺序。经过机加工的副车架尺寸精准,没有出现变形现象。
图12 副车架顶面粗加工
图13 副车架筋板面粗加工
4、试验验证
4.1 副车架耐久性试验
加工完成的副车架应符合奇瑞Q/SQR S5-49规定的要求,为了验证其耐久性,对其进行横向力加载和纵向力加载疲劳寿命试验。
试验设备采用MTS汽车零件试验系统专用试验工装,副车架横向力加载和纵向力加载试验分别如图14和图15所示。副车架安装同实车状态,四点固定,等效安装控制臂,加载点为左右控制臂球头处,左右两边同时加载,左右载荷同步、同频、同值。
图14 副车架横向力加载试验
图15 副车架纵向力加载试验
副车架耐久性试验条件见表4。
表4 副车架耐久性试验条件
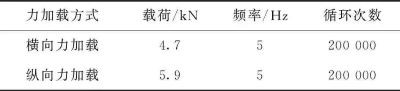
经过200 000次的横向力和纵向力加载之后,副车架没有出现裂纹,这说明该副车架耐久性好,满足Q/SQR S5-49 中规定的要求。
4.2 副车架耐腐蚀性试验
副车架常常处于恶劣的工作环境,所以有必要评估副车架的耐腐蚀性,验证其是否符合Q/SQR S5-49中规定的要求。
如图16所示,将副车架置于中性盐雾试验箱中,向其喷射中性盐雾,试验时长为240 h。
图16 副车架耐腐蚀性试验
试验完成后,观察到副车架的外观无明显腐蚀,这表明该副车架的耐腐蚀性好,符合Q/SQR S5-49中规定的要求。
5、结论
本文主要对铝合金副车架的设计开发过程进行了介绍,并通过试验验证了该副车架满足开发要求,具体结论如下:
(1)将铝合金作为副车架的材料,对副车架的结构进行了优化设计,并通过Nastran有限元分析软件验证了其强度、刚度和模态性能;
(2)对副车架的铸造和机加工方案进行了设计,加工出来的副车架无加工缺陷;
(3)对加工出的副车架进行了耐久性和耐腐蚀性试验,试验结果均满足要求。
参考文献:
[1] 姬鹏,申伟凯,武振江.基于灵敏度分析的某SUV前副车架轻量化设计[J].机械工程师,2017(11):11-14.
JI P,SHEN W K,WU Z J.Lightweight design of a SUV front subframe based on sensitivity analysis[J].Mechanical engineer,2017(11):11-14.
[2] 陈磊,程稳正,孙珏,等.铝合金铸造副车架开发[J].汽车技术,2015(2):58-62.
CHEN L,CHENG W Z,SUN J,et al.Development of aluminum alloy casting sub-frame[J].Automobile technology,2015(2):58-62.
[3] 孙志远,陈永忠,彭浩,等.汽车前副车架轻量化设计[J].汽车零部件,2020(5):1-7.
SUN Z Y,CHEN Y Z,PENG H,et al.Lightweight design for front subframe[J].Automobile parts,2020(5):1-7.
[4] 修坤,王成刚,马林,等.轿车铝合金副车架铸件铸造工艺改进[J].铸造,2017,66(1):75-77.
