培养基模拟灌装验证是无菌制剂生产过程中必不可少的验证,在洁净厂房、公用系统、灭菌设备验证合格的前提下,且操作人员熟练掌握了岗位SOP 后进行的。培养基灌装作为无菌灌装的模拟实验,可以直观、方便、准确地反映出无菌灌装过程的污染情况及问题。本文以全自动冻干粉针剂车间10ml 西林瓶生产线为例分析,所生产的产品均为非最终灭菌工艺生产的无菌产品;车间、生产线、人员的无菌保证则至关重要,所以应对冻干粉针剂的生产过程进行培养基模拟灌装验证,以证明生产车间可持续稳定的生产出合格的药品。
1、本文的主要观点
本文主要探讨的是培养基模拟灌装验证中的风险点及验证方法。
1.1 风险分析
培养基经过配制除菌过滤后,由灌装岗位灌至经335 ℃ 灭菌的西林瓶中半压塞( 胶塞121 ℃ 灭菌F0 值≥ 15),装入冻干机内,将制品按既定曲线进行抽真空后压塞,出箱轧盖。生产过程中设备自动化程度较高,人员依赖少;为了确保人员、机器、物料、操作规程、环境能达到无菌保证要求,从各个方面对无菌生产工艺过程影响无菌保证的风险要素进行分析,以确定无菌培养基模拟灌装工艺验证的范围和程度。
1.1.1 风险评估工具:
采用RAC 打分方法对验证前识别的风险点进行评级。
RAC 风险评价指数矩阵法:采用科学的RAC 风险评价指数矩阵法对出现的风险进行分级:风险程度(R)=风险概率(P)× 风险严重度(S)。通过规定风险严重性等级及风险概率的定性等级,进行不同的等级组合对风险进行分级。如:
1.1.2 风险概率等级
A 级- 频繁- 几乎经常出现,连续发生;B 级- 容易- 在整个产品的生命周期中将出现若干次,经常发生;C级- 偶然- 在整个产品的生命周期中可能出现,有时发生;D 级- 很少- 不能认为不可能发生,可能发生;E 级- 不易- 出现的概率接近于零,可以假设不发生。
1.1.3 风险严重度等级
Ⅰ级- 非常危险性的- 质量管理活动某一部分或某些部分失败;已有证据证明产品不符合要求导致患者死亡;Ⅱ级- 危险性的- 已有证据证明质量管理活动某一部分或某些部分受到威胁;Ⅲ级- 处于危险与安全之间(临界)的- 质量管理活动可能受到潜在威胁,无法证明是否已造成损害或产品不符合要求导致患者死亡;Ⅳ级-安全的- 无损害。
1.1.4 风险定性分级
用矩阵指数的大小作为风险分级的准则。一级风险:指数为1 ~ 5,是不能接受的风险,必须降低;二级风险:指数为6 ~ 9,是不希望有的风险,必须适当地降至尽可能低,需要相关的组织决策确定是否可以接受;三级风险:指数为10 ~ 17,是有条件接受的风险。条件允许的情况下,必须适当地降至尽可能低,需要相关的组织评审后可以接受;四级风险:指数为18 ~ 20,是完全可以接受的风险,不需要相关的组织评审。
风险评估总结:根据此验证风险的评估结果,此过程未出现一、二级风险,但存在三、四级风险,针对存在的三、四级风险,对该风险点采取相应的风险控制措施。基于现行管理体系,对所有风险均采取了预防措施。通过本文验证证明操作的可行性及风险是否可控。应将所有中等及以上风险重点监控,并随时防止低风险升高。
1.2 人员及干扰项目设计
根据风险分析结果,模拟灌装试验除对配制、药液传递、灌装、轧盖的整个工艺过程进行模拟外,还应在培养基模拟灌装过程中增加人员干预项,对设备运行异常的调试和设备故障的维修过程、灌装间的人员数量限制、人员手部消毒频次、灌装时限等进行挑战实验。
1.2.1 可接受标准
本文模拟灌装批量为30000 支,超过10000 支,故根据《2010 版GMP 附录一无菌药品》中的要求,培养基模拟灌装试验的目标是零污染,当出现污染时应遵循以下要求:
有1 支污染,需调查;有2 支污染,需调查后,进行再验证。发生任何微生物污染时,均应当进行调查。
1.2.2 灌装机速度
根据设备验证结果日常灌装速度拟定为240 ~ 480瓶/min,日常生产时,灌装过程约为6h,本文模拟最差条件,模拟最长生产时限为16h。
1.2.3 验证过程中的干扰和中断情况
培养基灌装尽量模拟所有正常生产中的活动,如测装量、加塞,开关门,最多人数、灭菌物品在接近有效期、最低速度等操作,为评估这些活动对无菌性的影响,因此在培养基灌装时将模拟以上干扰活动。
(1)加塞频次。日常生产生产批量为18.4 万支,胶塞桶每桶装约10000 只20-D3 丁基胶塞,共约18 桶。
(2)检测装量频次。日常生产批量为18.4 万支,灌装开始至灌装结束最长时限约6h,灌装过程中每30 分钟检测一次装量,需共测装量12 次左右。
(3)故障维修干扰。日常生产时,灌装过程中会有一些非计划性的、不可避免的设备故障维修活动,由于设备定期维护保养,设备故障一般在较短时间内能够解除。
(4)更换陶瓷泵干扰。日常生产时,灌装过程中会发生一些极端情况如:陶瓷泵漏液、抱死情况等,需更换陶瓷泵。
(5)拆卸零部件干扰。日常生产时,灌装过程中会有一些拆卸零部件活动。
1.3 使用的培养基类型
采用浓度为2.98% 胰酪大豆胨液体培养基进行本文模拟灌装验证。
1.4 模拟灌装装量、包材及批量
本文验证采用灌装量装为4ml 培养基/ 瓶。采用20-D3 胶塞、10ml 西林瓶、19.8*7.0 铝盖作为内包材。生产批量为3.0 万支/ 批。
1.5 模拟灌装最差条件的确定
本文验证采用灌装装量为4ml 培养基/ 瓶。培养基生产验证过程中应当保存生产过程中的视频资料。本文验证挑战配液系统,胶塞铝盖等灭菌后的最长时限挑战,本文验证为再验证。为指导模拟灌装操作,分别模拟不同的干扰条件,在干扰的同时,进行培养基灌装操作,所有的干扰样品均在这3 个时间段进行。
2、验证方法
2.1 物料确认
所有物料均由批准的供应商处采购,检查符合标准要求并放行使用,在合格有效期内。
2.2 物料进入洁净区的转移
进入洁净区的物料严格按SOP 进行操作。
2.3 工服、胶塞、铝盖、器具灭菌确认
(1)测试方法:检查湿热灭菌过程中自动打印记录的控制参数和监测曲线。
(2)接受标准:灭菌设备自动打印记录附在批生产记录中,控制参数和监测曲线一致,灭菌参数符合工艺要求。
2.4 培养基液体配制
(1) 测试方法。胰酪大豆胨液体培养基按29.8g → 1000mL 的比例加入注射用水(20 ~ 25℃)中,搅拌10min 使全部溶解。
(2)接受标准。培养基批号和用量符合要求。
2.5 培养基液体过滤
(1)测试方法,使用1 个无菌取样瓶对缓冲罐内的培养基进行取样,送质检中心检查无菌。
(2)接受标准。无菌生长。
2.6 无菌培养基灌装
(1)测试方法。培养基液体通过配液管路系统传递至灌装间缓冲罐中,进行培养基灌装。灌装半压塞样品通过自动进出料系统进入冻干机进行冻干工艺模拟。
(2)接受标准。灌装前的操作应不得对生产过程产生污染。
2.7 环境监测
(1)测试方法。对生产过程中的沉降菌、浮游菌、表面微生物等进行测试。
(2)接受标准。生产过程中沉降菌、浮游菌、表面微生物等的测试结果符合相应洁净级别的动态标准要求。
2.8 模拟冻干
(1)测试方法。冻干机灭菌周期连续生产同一品种每周对冻干机进行一次在线灭菌,首次生产前或超过灭菌效期时进行灭菌。
(2)接受标准。准确、详细记录模拟冻干过程中的全部干预操作。
2.9 轧盖
(1)测试方法。全压塞产品通过轨道系统传入。
(2)接受标准。与密封性无关的缺陷样品均应进行下一步培养。
2.10 样品传递
模拟灌装合格的培养基经过冻干、轧盖工序传交接给质检中心、整个物料传递过程应无遗漏。
2.11 微生物培养与检查
(1)测试方法。每天由实验室人员逐支检查无菌情况。
(2)接受标准。灌装数量少于5000 支时,不得检出污染物;灌装数量在5000 ~ 10000 支时:有1 支污染,需调查,可考虑重复试验;有2 支污染,需调查后,进行再验证;灌装数量超过10000 支时:有1 支污染,需调查;有2 支污染,需调查后,进行再验证。
3、结语
本培养基灌装验证是对设备、环境以及人员操作的一种系统验证,是判断无菌保证水平的关键手段,其目的是为了证明生产线是否具备无菌工艺生产产品的能力、参与生产人员是否具备无菌灌装的资格以及是否符合GMP的要求。通过培养基模拟灌装试验以及灌装培养基的西林瓶染菌率能否达到规定的合格标准,来确认无菌灌装室的洁净环境以及进行无菌灌装过程中所采用的各种防止微生物污染的方法和规程的可行性,从而为保证所生产产品的无菌性提供依据。
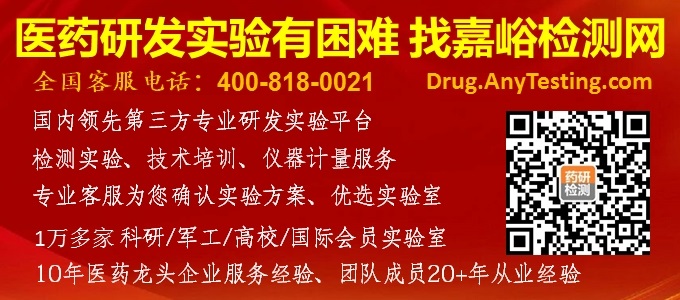