火力发电厂承压部件上管座众多,主要有温度测点、压力测点、疏(放)水、排空、蒸汽取样等,管座均连接在主蒸汽及再热蒸汽管道和集箱上,其工作温度高、压力大。近年来,因火电机组的调峰要求,高温、高压管座和套管角焊缝处频繁发生泄漏事故,其中温度管座的套管失效概率较大。为保证测温的准确性,温度管座需要插入承压部件内部,温度套管顶端受到蒸汽冲刷,长时间运行易产生疲劳失效,造成机组非计划停机,给现场人员的人身安全带来隐患。有学者指出,P91钢主汽管道上热电偶插座裂纹的产生原因为焊接结构设计不合理,采用增大坡口根部角度的方法并保证全焊透可以避免裂纹的产生,但焊缝缺陷返修实施难度很大,且返修对主汽管道损伤太大;采用增加管座结构的方法进行改造,可以大大降低焊接及热处理工艺的操作难度,但温度管座与套管的角焊缝是未焊透结构,只能对角焊缝处进行表面探伤,无法对焊缝内部的缺陷进行检测。
火电厂温度管座的失效往往是各种因素综合影响而导致的。材料选择不当、装配不当、焊接工艺执行不到位、焊缝埋藏缺陷无法被及时检测等原因,均会导致管座失效,因此管座的安全服役是综合优化的结果。针对这一情况,来自江苏大唐国际吕四港发电有限责任公司和中国大唐集团的科学技术研究总院有限公司的蒙殿武、马志宝等研究人员对温度管座的结构、焊接工艺、选材、检测方法等方面进行了系统研究,开展了相关试验,并提出了综合优化的概念,为火电厂新建机组管座设计、失效管座技术改造提供理论指导。
1.1主汽门温度套管脱落
2016年国内某电厂600MW机组高压主汽门入口温度保护套管脱落,主汽门材料为ZG15CrMo钢,壁厚约为80mm,温度套管材料为1Cr18Ni9Ti钢,温度套管与主汽门管座孔为过渡配合,焊接结构未开坡口,焊接材料为A132钢,焊脚尺寸约为5mm(见图1)。经检查发现,位于坡口面约50%的焊道外观有明显的裂纹扩展痕迹,约30%有明显的撕裂痕迹。该焊接结构未开坡口,焊脚尺寸及焊接材料不符合相关标准要求,当机组启停和调峰频繁、温度变化次数增加时,该温度套管受到周期性热应力,在焊缝根部产生裂纹,在运行过程中裂纹不断扩展,最终导致温度套管脱落。
1.2主蒸汽管道上温度套管开裂
国内某电厂600MW机组的主蒸汽管道上温度套管发生开裂,开裂温度套管的宏观形貌如图2所示,可见裂纹位于焊缝与母管熔合线附近,主蒸汽母管材料为A335P91钢,壁厚为47mm;温度套管材料为1Cr18Ni9Ti钢,结构形式为温度套管直接埋入主蒸汽管道中,且为未焊透结构。该温度套管的结构为直埋式未焊透结构,焊缝根部应力集中程度较大,焊缝根部坡口角度较小,焊接时摆丝困难,容易形成夹杂、未熔合缺陷。母管与套管材料不同,为异种钢焊接,焊接后实施热处理的难度较大,在交变应力的作用下,沿焊缝与母材侧熔合线产生裂纹,导致温度套管发生早期开裂。
2、温度管座失效影响因素
2.1 异种钢焊接接头
温度管座的材料一般为不锈钢,管道、集箱或缸体一般为铁素体耐热钢,因此温度管座就出现了异种钢焊接的结构设计。据统计,奥氏体异种钢接头发生早期失效的时间约为7×104h,镍基合金异种钢接头发生早期失效的时间约为106h。异种钢的热膨胀系数存在差异,导致焊接接头内部应力较为复杂,低合金侧容易产生氧化缺口,因此异种钢焊接接头易发生早期失效。
2.2 结构
目前直埋式温度管座一般都为未焊透结构,其焊缝根部角度较小,焊接时摆丝困难,容易形成未焊透或未融合缺陷,这种结构容易产生内部缺陷,且很难被检测出来,使焊接质量难以得到有效控制。
2.3 焊接工艺
焊接工艺不当,没有进行预热和焊前热处理,焊缝根部存在严重未焊透现象,未做焊后热处理,均会导致温度管座发生早期失效。
2.4 装配工艺
装配工艺不当会导致管座发生振动,并产生应力集中;还会使温度管座的锥形套与管壁内孔的锥形面未紧密接触,管座直段在介质冲击作用下发生振动,最终使温度管座根部发生疲劳断裂。
2.5 管系布置
机炉外管往往没有设计图纸,施工单位在施工过程中因地制宜进行布置,但如果布置不当造成热膨胀受阻、支吊架调整不到位,会使管座产生拘束应力,并引发开裂。
2.6 加工工艺
温度管座变径处存在退刀槽和截面突变,没有进行圆滑过渡,存在应力集中,容易导致该部位发生泄漏。
3、综合优化
3.1管座结构
温度管座按结构形式分为直埋式、管座式和螺纹式(见图3~5)。直埋式温度管座是将管座直接埋入承压部件内部焊接而成,可分为根部非焊透结构和全焊透结构;管座式温度管座是用短节接管相连接,可分为安放式和插入式;螺纹式温度管座是在管道开孔处或管座内壁加工螺纹,套管与管座用螺纹连接,并在管座表面进行焊接密封。
因无法对螺纹式结构角焊缝进行无损检测,故对管座的质量可控性较差,存在安全风险,应用较少,一般应用于高中压主汽阀上;直埋式和管座式在各类管座中应用较广泛。直埋式与管座式结构优缺点的比较情况如表1所示,可见管座式结构焊缝处的应力更小,对主管母材的热损伤小,易修复,可以对焊缝埋藏缺陷进行超声检测,因此在设计、改造、维修中应首选管座式结构。
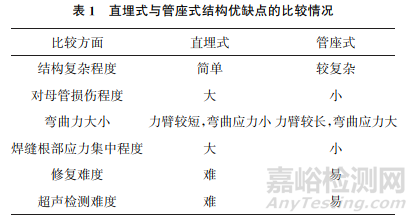
3.2管座材料
国内大部分设计院设计的温度套管材料主要有两种,一种是与管道同材料的低合金耐热钢,另一种是奥氏体不锈钢,这两种材料在各机组中所占比例相当。不锈钢温度套管的优点为,具有良好的抗氧化性、耐腐蚀性以及抗蒸汽冲刷能力;缺点为易发生异种钢接头早期失效,且镍基焊缝不易进行超声检测,很难对其进行质量监控。因此管座应选用与套管相同的材料,要综合考虑材料的强度、抗氧化性、热膨胀性、疲劳、焊接、检验检测等方面因素。
3.3管座检测方法
3.3.1 外径为32~89mm的管座
依据行业标准,当管座外露检测面长度满足规程要求时,可采用普通A型脉冲反射法对管座角焊缝进行检测。探头放置的检测面为接管外壁,依靠一次直射波和内壁二次反射波进行焊缝检测覆盖,检测过程中无须考虑管道曲面对缺陷定位的影响。
目前绝大部分机组管座的检测面长度均不满足规程要求,对于这种情况,如果管座检测面长度不小于25mm,也可使用相控阵法进行检测。
对于安放式管座,依据DL/T 1105.2—2010《电站锅炉集箱小口径接管座角焊缝 无损检测技术导则第2部分:超声检测》进行检测,可发现接管侧坡口的未熔合、未焊透缺陷,以及焊缝中的气孔、夹杂、部分反射面较好的裂纹,但若主管筒体不开坡口或坡口角度很小,则很可能漏检主管筒体坡口的未熔合缺陷。
对于直埋式管座,依据DL/T 1105.2—2010进行检测,容易漏检接管侧焊接区未熔合缺陷,这也是直埋式结构不容易进行质量控制的原因。
3.3.2 外径不小于89mm的管座
外径不小于89mm的管座在疏水、排空、测温、压力管座中应用较少,此处不进行讨论。
3.3.3 外径为22~32mm且壁厚不小于4mm的管座
对于外径为22~32mm且壁厚不小于4mm的管座,很多常规超声检测规程都没将其纳入检测范围,可用相控阵法对其进行检测。
3.3.4 外径小于22mm或壁厚小于4mm的管座
对于壁厚小于4mm的管座,体波难以传播,易形成导波,不能进行超声检测。可以采用直流磁粉检测法对其近表面缺陷进行检测。试验证实,满足提升力≥177N的直流电磁轭,能检测壁厚4mm管座的对接焊缝根部未焊透缺陷。
4、建议
4.1管座结构的选择
对于服役温度大于400℃或服役载荷大于5.9MPa的承压部件,推荐使用插入式管座;对于服役温度小于400℃或服役载荷小于5.9MPa的薄壁承压部件(壁厚小于20mm),推荐使用直埋式管座。管座角焊缝、温度测点、取样管等与管座的对接焊缝均须采用全焊透结构。
对于安装在管道上的各类管座,不宜使用螺纹式结构;对于安装在各类阀(缸)体上的各类管座,允许采用螺纹式结构。靠插入端紧密配合的温度管座,宜采用圆锥形设计,安装时保证管座与承压部件管壁顶紧。
承压部件管座形式及角焊缝结构的设计应满足无损检测对焊缝内部缺陷和表面缺陷的检测要求,接管外径不小于32mm,壁厚不小于4mm,长度不低于60mm,强度满足设计要求。
4.2材料及焊接工艺的选择
高温(服役温度不小于400℃)管座及套管宜选用与承压部件相同的材料,低温 (服役温度小于400℃)管座及套管可采用比承压部件性能等级高的材料。
焊缝坡口形式以及坡口角度的设计要满足根部焊透要求,尽量减少熔敷金属填充量,以降低焊接应力;焊接宜采用氩弧焊打底,氩弧焊或低氢焊条填充和盖面。
4.3检测方法
按DL/T 869—2012 《火力发电厂焊接技术规程》的相关要求,对焊接接头进行宏观观察、光谱检验,如焊接接头能放置便携里氏硬度计时,应进行硬度测试。铁磁性材料优先使用磁粉检测。能确定温度管座结构且结构允许的情况下应进行超声检测,并应制定超声检测操作指导书;结构不满足超声检测要求且曾发生过失效的管座,应进行结构改造,以满足检测要求。
5、结语
火电厂温度管座失效的影响因素有:管座结构、管座材料、焊接工艺、装配工艺、管系布置等,需采用综合优化思维对管座的安全性进行评价。
管座结构宜优先选择全焊透的插入式管座,套管及管座应选用与承压部件相同或相近的材料。管座的结构设计、材料选择应满足无损检测对焊缝埋藏缺陷和表面缺陷的检测要求。
综合优化概念的提出可以为提高火电厂温度管座的安全性,避免机组发生事故甚至造成人身伤亡等提供理论支持。