随着汽车电气装备的增加,整车的电气功能和功能配置日益复杂,对电线束的设计是否合理及最优的要求逐渐提高。同时,在整车成本逐渐下降的趋势下,电线束的成本压力也逐渐增大。鉴于上述原因,验证电线束设计是否合理,如何优化电线束系统使之达到最优化设计,这两项工作的关注度逐渐提高。
本文介绍电线束系统设计验证的主要方式, 详细讲解线束走向验证、配电设计验证、搭铁设计验证、电压降测试等几方面的验证方法。分别从电线束设计验证的必要性、设计验证的几种方式、电线束系统设计验证的主要方法3个方面重点论述,同时结合实例,对电线束设计验证进行部分深入讲解。
1、 电线束系统设计验证的必要性
电线束连接车辆上所有的控制器、执行器、传感器,在整车中承担着电源分配、信号传递的作用。拿人体做类比,电线束相当于车辆中的血管和神经系统,因此,电线束设计是否合理,直接影响到整车的电气功能安全性及车辆使用可靠性。
如果电线束设计不合理,无法满足实车负载的要求,那么会出现熔断丝寿命过短、熔断丝异常熔断、导线过载发烟甚至起火等事故。
如果电线束设计冗余量过大,则不利于整车成本控制,不利于整车质量及燃油经济性。
综上,电线束设计合理、合适,电线束设计最优化,成为越来越多的主机厂和线束厂商关注的重点。
结合产品正向开发模式,通过设计-验证-优化的闭环方式(图1)使整个设计过程完整、可控、最优。
2、电线束设计验证发展及分类
设计验证也可称作“DV试验”,DV,即Design Verification。
电线束的设计验证,主要通过测试来验证设计方案的合理性,而随着CATIA、CHS、IPS等软件的普及和利用率逐渐提高,部分验证工作也可以通过系统仿真实现。
按测试工具分类,设计验证可以分为:软件仿真、台架试验、实车测试3种方式。
1) 软件仿真,优势是可以在正向设计阶段实施。通过软件仿真验证线束装配性是否合理,整车线束拓扑结构是否合适,配电原理设计及电器件布置是否合理等。但是软件仿真都是通过计算的参数进行模拟仿真,无法实现实车情况和实际车辆使用各类工况的测试验证。
2) 台架测试,一般在电器件C样件阶段实施,此时电器件的功能完善,状态接近于量产样件,性能比较稳定,测试结果可靠性高。在电气台架上,通过台架模拟实车用电器的使用工况,来针对实际零件测试,具有测试结果可靠性高、接近实车工况的优点,但是在台架上无法完成线束走向布置检查,部分实车条件无法模拟(例如整车搭铁点电流分布情况)。
3) 实车测试,一般在电器件C样件且整车OTS状态时实施。实车测试兼顾了线束布置验证和配电设计验证两方面,可以实现电线束系统的实车布置合理性评估、配电设计验证、搭铁点电流分布等设计验证。但是实车测试需要整车资源,在投资上也是最高的。实车测试中,会发生过载或滥用电气功能等情况,对车辆也有损害,测试后车辆一般都会报废,资源重复使用率不高。
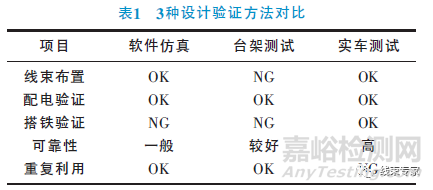
表1总结了各个测试方法的优劣,目前大多数主机厂都会采取台架测试,少数主机厂会采用实车测试。
3、电线束设计验证测试项目介绍
电线束设计验证测试项目主要可以分为两大类:线束布置方案验证、配电原理设计验证。
再根据测试项目细化,形成图2形式的测试项目列表。
3.1 走向检查
在软件仿真或实车状态下进行线束走向检查,主要检查线束外保护设计合理性,可以通过整车分区,分别对各区域展开针对性内容的检查。表2为线束走向检查项目举例。
3.2 装配性
针对某些存在线束连接装配的位置检查线束装配性(例如保险杠线束与车身连接的过程、发动机线束与前舱线束连接的过程),整车电线束方便装配,经常维修处便于拆卸为装配性合理的表现。
3.3 电气负载测试
电气负载测试主要验证负载与导线、熔断丝的匹配关系是否合适。通常在台架或实车上测试,在车辆起动后发电机稳态输出电压的情况下(智能发电机可按额定电压输出范围的平均值设定或按商讨而定),不同的工况下,记录各个负载正常工作的电流,部分电机类负载要额外记录堵转电流、PTC保护时间等。通过实际测试得到的结果,与导线线径、熔断丝类型进行对比,确认熔断丝、导线的选择是否合适。
举例:在某车型项目中,测得喇叭的正常工作电流为10.3 A,最大电流为11.88 A。喇叭的供电回路设计状态为:MINI熔断丝10 A,配1.0 mm2的导线。
查阅喇叭ICD文件,文件中提供的测算工作电流为6 A,远小于实测电流10 A。通过实际测试,发现喇叭工作的正常电流已经超过MINI熔断丝的额定容量了,但是由于喇叭是短时工作负载,根据I2t的热量积分,熔断丝不会在喇叭工作一次后马上熔断,而会在喇叭工作若干次,累积效果达到熔断条件后,熔断丝再熔断。这样设计的直接后果是:熔断丝的寿命非常短,用户在实际使用车辆过程中要频繁更换熔断丝。
综上,结合测试结果对配电设计进行优化,选用MINI型15 A熔断丝,以规避上述问题。
3.4 电线短路测试
电线短路测试主要验证导线与熔断丝的匹配关系是否合适。通常在台架或实车上测试,在负载正常工作的条件下,对供电回路直接短路或过载,检查在测试过程中熔断丝是否及时熔断,保护导线。
过载测试时,使用电气负载正常工作电流值的135%和200%作为过载电流测试,同样需要确保导线温升在合理范围内的时期内,熔断丝需及时熔断;或在过载过程中,控制器/ 执行器及时启动过载保护,避免过载电流持续出现。
举例:在某车型项目中,在进行鼓风机回路135%过载时,发现在熔断丝熔断前,鼓风机调速模块被烧坏。
经检查,调速模块内部仅为调速电阻,而鼓风机和调速模块均没有过载保护装置,在过载时,调速电阻温升速度比导线快很多,在导线发烟和熔断丝熔断前,调速电阻烧毁。
出现上述问题后,在鼓风机内设置过载检测装置,出现过载时及时切断电流,避免调速电阻烧毁。
3.5 搭铁系统测试
搭铁系统测试主要验证线束搭铁点的电流分布情况,搭铁点出现松动时的故障现象,是否存在反向电流或潜通路,是否出现严重的电气功能故障,避免发生蝴蝶效应或严重危害驾驶安全的故障现象。通常在实车上测试,在负载正常工作的条件下,对各个搭铁点的电流分布进行测试,记录电流分布情况,分析电流与导线的匹配关系,各个搭铁点的电势是否相等。
上述测试完成后,打开整车所有负载,单独拆除每个搭铁点,观察车辆在搭铁失效时是否存在异常现象,测量被拆除搭铁点上是否存在反向电流,如果存在反向电流,结合电气原理图分析电流产生的原因。
对于预防搭铁松动,可以采用加强装配工艺检查,或使用环路搭铁的方式进行预防,这里篇幅有限,就不展开说明了。
3.6 电压降测试
电压降测试主要验证配电回路到用电器的接口处的电压是否符合用电器的电压要求。一般来说,汽车上的用电器电压范围比较宽泛,例如9~16 V都可以正常工作,此时电压降测试的意义并不能很好体现。但是对于具有怠速启停的车辆,停机后再起动时电压会急剧下降,此时就要确认好所有的用电器都能正常工作而不掉电。
对于满足用电器的供电电压需求,但是压降过大的线束回路,也要进行检查,尽可能消除压降,尽可能减少因线束回路引起的电能损耗。
4、 总结
从产品正向开发的角度出发,电线束设计验证的相关测试工作可以使开发设计工作形成闭环;从产品优化的角度出发,结合实际零件和实车的测试,可以有效实现产品设计验证及设计优化工作。随着设计品质的不断提高,设计验证工作逐渐向前期验证、系统仿真验证的方向发展。
参考:刘毅 《乘用车电线束设计验证方法》