TC17钛合金是一种富含β稳定元素的α+β型两相钛合金,名义成分为Ti-5Al-2Sn-2Zr-4Mo-4Cr,具有强度高、断裂韧性好、淬透性好和锻造温度范围宽等优点,能够满足损伤容限设计需求,被广泛地应用于航空发动机压气机盘、整体叶盘、鼓筒等关键转动件中。大量的航空零件失效分析结果表明,属于疲劳失效的零件约占80%,对重要部件的疲劳寿命进行准确预测与评估是保证航空发动机飞行安全的关键。此外,实际构件中往往存在诸多尺寸发生突变的部位,如凹槽、通气孔、装配螺栓孔等,这些几何不连续部位往往存在着明显的应力集中,使裂纹的萌生概率和扩展速率增大,对构件的强度和寿命产生重大影响。目前,已对TC17钛合金开展了大量的疲劳性能研究,但大多数都是光滑试样的疲劳性能试验,而少有TC17钛合金圆形开孔平板的疲劳性能试验。
来自中国航发商用航空发动机有限责任公司的彭霜、孙智君等研究人员对TC17钛合金圆形开孔平板试样进行低循环疲劳试验,获得了不同应力集中系数下开孔特征的低循环疲劳数据。在室温环境下,对两种不同应力集中系数下的TC17钛合金圆形开孔平板试样进行疲劳试验,两种试样的应力集中系数Kt分别为2.52和2.1,最大名义应力分别为590,700MPa,根据标准ASTM E466-21《金属材料 疲劳试验轴向力控制方法》,试验条件为轴向加载,应力比为0.1,频率为20Hz,波形为正弦波,终止条件为试样完全断裂。不同试样的疲劳寿命分布如图1所示,由图1可知:对于Kt为2.52的试样,其疲劳寿命存在1个数量级差异,但长寿命与短寿命分布相对集中;对于Kt为2.1的试样,短寿命试样的疲劳寿命分布相对集中,长寿命试样的疲劳寿命分布较分散,长寿命与短寿命试样的疲劳寿命存在明显差异;两种不同规格试样的实际应力水平相当,但二者疲劳寿命存在较大差异,Kt为2.52圆孔试样的疲劳寿命较长。研究人员对该批次试样疲劳性能差异进行了系统性分析,以期对后续开孔平板疲劳试验的开展具有一定的指导作用。
1、理化检验
1.1 金相检验
在整体叶盘外缘的试验环处截取疲劳试验板状试样,板状试样厚度为4mm,宽度为20mm,长度为112mm,平行段长度为14mm。Kt为2.52试样的中心圆孔直径为2mm,Kt 为2.1试样的中心圆孔直径为6mm,将中心圆孔线切割后,打磨圆孔表面,去除氧化层,以保证加工要求,并对孔边进行锐角倒圆。试样材料为TC17钛合金,横、纵截面的显微组织形貌如图2所示,由图2可知:其材料组织为β相+断续晶界α相,组织均匀,未见冶金缺陷。
沿试样圆孔的纵向切割,观察孔内壁及平板表面的加工质量(见图3)。由图3可知:各试样孔内壁加工均匀性较差,存在较大的随机性;部分试样内壁较光滑,可见多处加工刀痕缺口,但未见明显机械加工变形层,试样孔边倒圆角处存在加工凸起或缺口,且部分试样孔边倒圆角附近可见严重机械加工变形层,厚度约为2μm。部分平板试样加工表面可见缺口与严重变形层,较深的缺口深度约为14μm,变形层厚度最大约为19μm。试样孔内壁加工状态较板材表面好,试样板材表面变形层更厚,存在的加工缺口更深。钛合金属于缺口敏感型材料,孔内壁加工缺口、孔边倒圆角处损伤、机械加工产生的变形层等均会对疲劳裂纹的起源有促进作用。
1.2 扫描电镜(SEM)和能谱分析
采用扫描电镜对TC17钛合金疲劳试样的断口进行观察,采用光学显微镜对试样组织、中心孔内壁的完整性进行观察。
各试样疲劳裂纹起源位置如表1所示,按照疲劳循环周次,将Kt为2.52的试样从低往高依次排列,得到1# ~11#为较短寿命试样,12#~25#为较长寿命试样,11#与12#试样的疲劳寿命存在较大差异。对各试样断口进行观察,其微观形貌如图4所示。对于短寿命试样:部分疲劳裂纹起源位置为圆孔上、下端面倒圆与孔内壁转接(即孔边倒圆角)处,如2#,4#,5#,9#,11#试样;部分疲劳裂纹起源位置为孔内壁加工损伤处,如1#,3#,6#,7#,8#,10#试样,其中8#试样孔内壁可见多条较深的横向加工刀痕,裂纹起始于孔内壁较深的加工刀痕处。对长寿命试样,裂纹均起源于孔内壁亚表面,各裂纹源区与孔内壁距离不一样,最大距离为84μm。
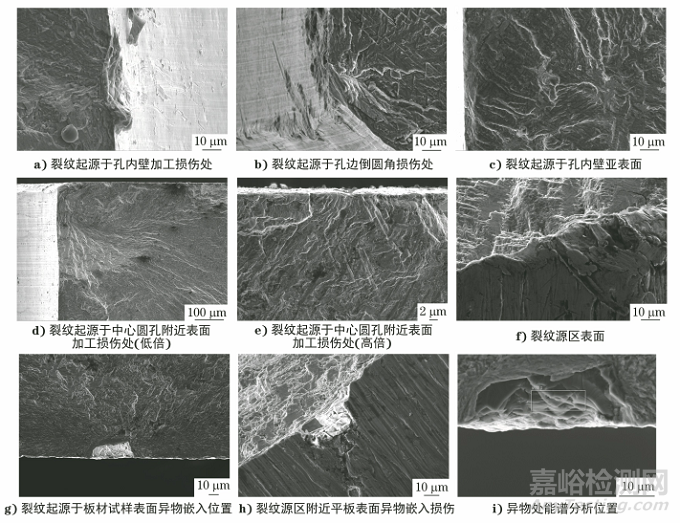
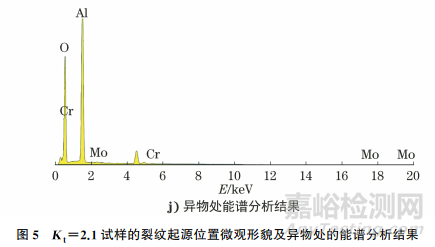
按照疲劳寿命,将Kt=2.1的试样从低到高依次排序,可见1#~21#试样的疲劳寿命分布相对集中,且寿命较短,22#~28#试样的疲劳寿命相对较长,1#试样与28#试样的疲劳寿命差异较大。对Kt=2.1的疲劳试样断口进行观察,形貌如图5所示。根据裂纹起源位置不同,可以将试样分为以下4类:①裂纹起源于孔内壁加工损伤处[见图5a)],大多数试样的裂纹均起源于孔内壁加工损伤处;②裂纹起源于孔边倒圆角损伤处[见图5b)],9#,18#,19#,21#试样的裂纹均起源于孔边倒圆角损伤处;③裂纹起源于孔内壁亚表面 [见图5c)],24#,26#,27#试样的裂纹均起源于孔内壁亚表面,裂纹源区与孔内壁距离分别为88,69,97μm;④裂纹起源于圆孔附近表面加工损伤或砂粒嵌入位置,如17#,28#试样裂纹起源于中心圆孔附近表面加工损伤处[见图5d)~5e)],源区附近平板表面可见明显表面加工损伤[见图5f)],22#,25#试样裂纹起源于板材试样表面异物嵌入位置[见图5g)],源区附近平板表面可见明显异物嵌入引起的损伤[见图5h)],同时对异物进行能谱分析,表明异物主要含Al、O元素[见图5i)~5j)],为氧化铝砂粒嵌入。对于寿命较短的试样(1#~21#),裂纹多数起源于孔内壁加工损伤或孔边倒圆角损伤处;对于寿命较长的试样(22#~28#),裂纹多数起源于孔内壁亚表面处或试样表面(非孔内壁)缺陷处。
1.3 粗糙度检测
采用粗糙度检测仪对试样中心圆孔内壁进行粗糙度检测,粗糙度是反映试样表面质量及表面微观几何误差的一个重要标准,能够实现表面加工沟壑尺寸的定量表征,在外加载荷的作用下,沟壑底部会产生明显的应力集中,影响试样的疲劳性能。分别选取Kt=2.52与Kt=2.1的试样,对断后试样的中心圆孔内壁进行粗糙度检测,检测方向为中心圆孔轴向,检测结果如图6所示(图中Rv为一个取样长度内,最大的轮廓谷深;Rz为一个取样长度内,最大轮廓峰高和最大轮廓谷深之和的高度),各试样内壁Ra(一个取样长度内,轮廓纵坐标绝对值的算术平均值)均小于3.2μm,相较而言,Kt=2.1试样孔内壁的粗糙度控制较好,Kt=2.52个别试样孔内壁Rp(一个取样长度内,最大的轮廓峰高)较高。各试样疲劳寿命与内壁粗糙度变化无明显的线性关系,可能与试样表面损伤随机分布或表面残余应力作用等因素有关。
1.4 残余应力测试
采用X射线衍射技术测试试样中心圆孔内壁的轴向表面残余应力。
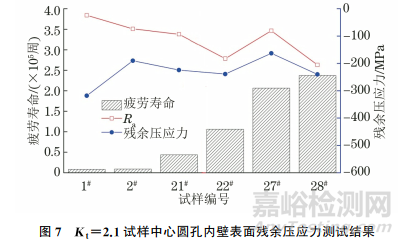
选取6个Kt=2.1的试样,对疲劳试验断后试样中心圆孔内壁表面进行残余应力测试,测试应力方向沿孔轴向,结果如图7所示,各寿命不同的试样表面均存在较大残余压应力,但不同试样的残余压应力分散性较大,1#试样表面残余压应力绝对值高达318MPa,27#试样表面残余压应力绝对值为163MPa。已有研究表明,残余压应力绝对值低于100MPa时,疲劳寿命接近表面无残余应力的试样,随着残余压应力的增大,Nf/N0逐渐增大(Nf为试样的疲劳寿命;N0为表面无残余压应力试样的平均寿命),当表面残余压应力达到-400MPa时,疲劳寿命延长100倍。残余压应力作用导致试样疲劳寿命延长,但各试样表面残余压应力分布差异较大,对疲劳寿命的影响程度不一样,导致疲劳寿命分散,故圆孔内壁表面残余压应力作用是导致试样疲劳寿命差异较大的主要原因之一。从图7可以看出:试样孔内壁残余压应力与疲劳寿命并未表现出线性变化,可能与试样孔内壁表面损伤、表面粗糙度等有关,残余压应力较大与表面粗糙度较小的试样呈现出较长的疲劳寿命。
2、综合分析
Kt=2.52与Kt=2.1试样的疲劳性能均表现出相同的趋势:①短寿命试样裂纹多起源于孔边倒圆角损伤或孔内壁加工损伤处,试样各圆孔倒圆角加工状态存在差异,部分孔边倒圆角处存在金属堆积或变形层,损伤导致材料性能弱化及应力集中,孔边倒圆角处表面状态较差以及孔边内壁存在加工缺陷是造成试样疲劳寿命短的主要原因,孔边倒圆角以及孔内壁加工表面状态对疲劳性能影响较大;②对于Kt=2.5且寿命较长的试样,其裂纹均起源于孔内壁亚表面,Kt=2.1试样的裂纹起源于孔内壁亚表面处或非孔内壁缺陷处,表明试样内壁存在较大的残余压应力。Kt=2.52且寿命较长的14个试样的裂纹均起源于孔壁亚表面,相较于Kt=2.1的试样,其亚表面裂纹起源特征具有较高的一致性,表明Kt=2.52试样圆孔内壁普遍存在较高的残余压应力;Kt=2.52试样中心圆孔直径小,加工难度大,在孔内壁更容易形成残余压应力,残余压应力作用导致试样疲劳寿命延长,故相较Kt=2.1的试样,孔内壁存在较高的残余压应力是导致Kt=2.52试样疲劳寿命整体偏长的原因之一。
将两种不同规格试样的疲劳寿命与裂纹起源位置进行统计分析,可以发现:裂纹起源于孔边倒圆角损伤处与孔内壁加工损伤处试样的平均疲劳寿命明显较低,低于整体平均值;裂纹起源于孔内壁亚表面试样的平均疲劳寿命最长,裂纹起源于板状试样表面损伤处试样的平均寿命稍短,表明板状试样表面缺陷也会降低试样的疲劳性能。对于Kt=2.52的试样,当裂纹起源于孔边倒圆角损伤或孔内壁加工损伤处时,其疲劳寿命较整体平均值低约74%,当裂纹起源于孔内壁亚表面时,其疲劳寿命较整体平均值高约59%;对于Kt=2.1的试样,当裂纹起源于孔边倒圆角损伤或孔内壁加工损伤时,其疲劳寿命较整体平均值低约71%,当裂纹起源于孔内壁亚表面时,其疲劳寿命较整体平均值高约219%,当裂纹起源于板状试样表面缺陷时,其疲劳寿命较整体平均值高约
134%。故孔内壁加工缺陷、孔边倒圆角损伤、板状试样表面加工缺陷均导致试样疲劳性能弱化,孔内壁较大的残余压应力对疲劳性能有提升作用,试样加工损伤、孔内壁较大残余压应力、残余压应力较分散等原因造成了试样疲劳性能存在较大差异。试样疲劳性能与裂纹起源位置的统计分析结果如图8所示。
疲劳性能数据受试样表面状态的影响,裂纹通常从表面萌生,当表面存在损伤时,裂纹易由表面损伤处起始,疲劳性能会显著下降且存在较大分散性,不能准确表征材料的性能,因此,在设计试样的加工工艺时,应尽量避免试样表面的加工损伤,消除表层加工硬化;另一方面,残余压应力改变了表面裂纹萌生及裂纹扩展的驱动力,残余压应力可提高疲劳性能。为了得到可靠的疲劳性能数据,减小数据分散性,必须严格控制试样表面的残余应力,建议对TC17钛合金圆形开孔平板试样进行消除残余压应力处理,以最大限度地减少表面残余压应力对材料疲劳性能的影响。
3、结论
(1)对于Kt=2.52的板状圆孔疲劳试样,寿命较短试样的裂纹多起源于孔边倒圆角加工损伤处或内壁加工损伤处,寿命较长试样的裂纹多起源于孔内壁亚表面处。
(2)对于Kt=2.1的板状圆孔疲劳试样,寿命较短试样的裂纹多起源于孔内壁加工损伤或孔边倒圆角加工损伤处,寿命较长试样裂纹起源于板状试样表面加工缺陷或孔内壁亚表面处。
(3)试样加工损伤、孔内壁较大残余压应力,以及残余压应力较分散等几方面因素造成试样疲劳性能存在较大差异。
