目前许多变速器的关键结合面都已改成了平面密封胶,大部分情况下,都是人工干预进行涂抹,对于不同的结合面有着不同的技术要求,针对盲孔、通孔及销子孔等不同的产品,所采用的涂胶方式有不同的要求。人工手动涂抹存在着很大的误差,误差较大的可在气密检测工位被检出,进行返修,费时费力;误差较小的在试车、气密检测位置都不会被发现,最终会在市场以漏油的方式体现,影响产品的质量,甚至影响公司的声誉,因此,智能涂胶技术得到了普及应用。
将涂胶头集成于三轴机器人上,通过控制机器人胶针的轨迹从而调整胶线的轨迹。能够兼容不同机型的高度、涂胶轨迹及绞线宽度等,可通过工位上的读写头,识别当前工位的机型,自动识别出当前机型的涂胶轨迹。为了保证涂胶的精度,采用了伺服定量涂胶技术,将伺服电动机安装在胶泵与胶管之间,通过控制伺服电动机的转速控制涂胶量,将机器人的运动速度与伺服电动机控制的出胶体积进行匹配,从而达到使用一台机器人、一台涂胶泵和一个涂胶头,即可满足上百种机型、多种涂胶轨迹及多种涂胶宽度的需求。最后通过使用照相技术在线检测,检测装置对胶线图形、宽度进行二维检测,与标准胶线进行匹配,如果不合格则报警,人工干预调整胶线,保证生产出合格的产品(见图1)。
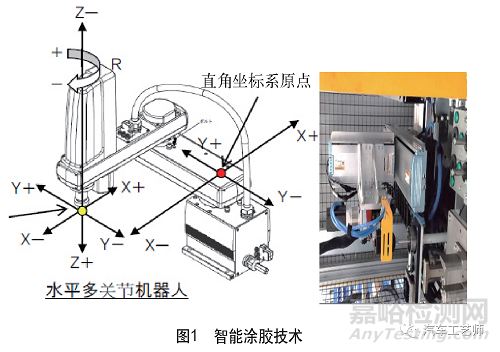
工艺优势
传统人工涂抹平面密封胶很难控制胶线的粗细及合理的轨迹,容易造成大量密封胶的堆积,挤压后在壳体表面形成严重的胶痕。为保证良好的外观,需要人工干预将其擦拭干净,擦拭过程中面积大、范围广,大大影响装配的效率。而智能涂胶技术,针对特定产品的胶线有着特定的宽度和特定的轨迹,使产品有着良好的一致性,从而保证了产品的质量,统一了产品的外观。在满足技术要求的前提下,既节省了成本,又大大提高了装配效率。
以往的涂胶技术只能满足单一产品的生产需求,若需兼容多种产品,需每次更换胶头或者增加多个工位,换型效率低,节拍时间长,同时,兼容的机型少,成本高。而智能涂胶技术,柔性程度高,可兼容多种机型,自动识别当前的机型,完成机型与程序的配对,实现智能涂胶。
传统胶线涂抹完成后,依靠人眼观测,缺胶、少胶完全依靠人工,涂胶质量存在隐患,尤其是胶线的轨迹,不唯一、易偏离、返修率高。而智能检测技术,通过对比检测胶线的轨迹及精度,一次涂胶合格率≥99.8%,成本大大降低,提高了一次性装箱合格率。
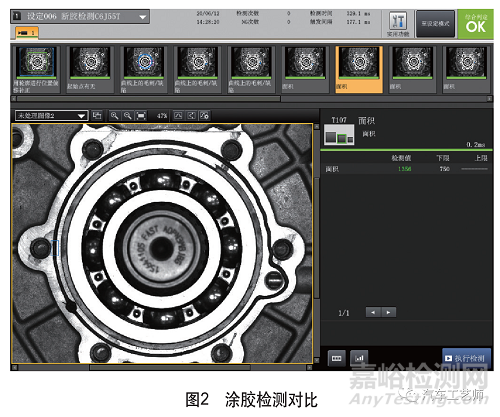
技术应用
需提前选择好涂胶轨迹,采用图3所示点位跟踪控制进行编程,通过控制A1、A2、A3来点动控制机器人的三个轴(点位跟踪:先选择点位进行跟踪,点动到预设定的P点,选择点位,再点击跟踪),从而控制涂胶头的位置。先使涂胶头依照选择的轨迹运动一圈,保存涂胶头的运动轨迹,然后调整控制伺服电动机的转速,控制涂胶量,不断优化涂胶速度、轨迹和涂胶量,最终选择最佳涂胶参数,确保一次到位。
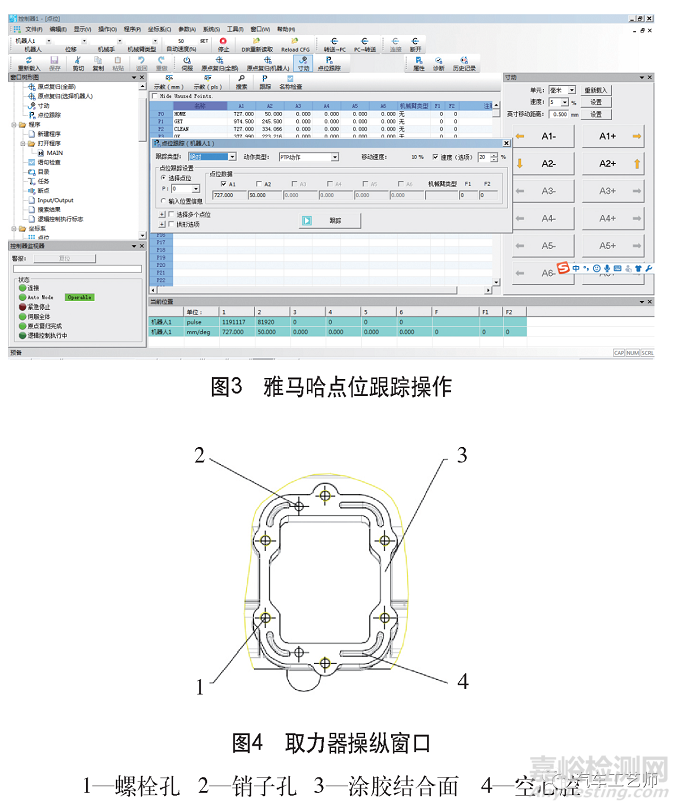
发动机边杆
1.方案示例
涂胶位置偏多,此处以取力器结合面加工方案展开说明。图4所示变速器壳体取力器位置,由于变速器占比大,无法直接在变速器上涂胶,则选择在取力器盖板(见图5)上涂胶(取力器原理类似)。
2. 效果验证
检测主要依靠标准涂胶胶线的标定,在进行大量(大于50台)变速器涂胶后,通过多次修改尝试,最终选择出最优的胶线轨迹、胶线宽度及胶针运动速度,将其输入对比软件,最终采用轮廓位置偏移补正,图6所示绿色标志为对比片段(由无多数个对比片段的组合最终形成完整的胶线轨迹),通过CCD相机的图像识别功能,利用强大的计算能力,识别胶线的轮廓度以及胶线的宽度(2mm)。通过检测技术反馈给机器人及涂胶系统,自动调整胶针运行速度,以及电动机速度,使涂胶胶线合格,如无法对比修正则报警,需求人工识别调整。
通过一年的实践检验,智能涂胶技术运行正常,密封良好,无泄漏现象,而且节省了密封胶的用量,浪费现象明显减少。后续可以试验更小的用胶宽度与密封性的关系,为将来定量用胶量打好基础(见图7)。
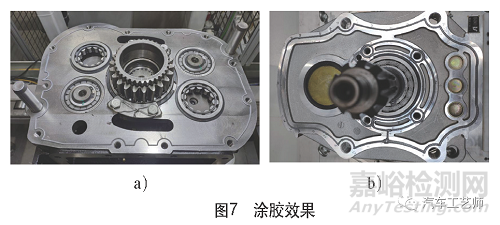
结语
目前,所用胶针内孔直径一般为0.5mm和1mm,而涂胶宽度为1~2.5mm不等,胶线的宽度主要取决于胶针内孔的直径、伺服电动机的转速以及胶针的运动速度。胶线的轨迹更多依据产品结合面相对的结构,避免装配后胶线被压于空心腔内。对于盲孔应绕着孔内壁走胶,避免绕圈的浪费现象,若多次尝试某处或多处气密检测仍然泄露,可能盲孔存在沙眼等现象,应在相应盲孔位置绕圈涂胶。如果为通孔,直接在通孔位置绕圈涂胶。涂胶位置为后轴承盖、一轴轴承盖时,应尽量避开回油孔(槽)位置,防止过多的平面密封胶将回油孔(槽)堵住,影响润滑,降低产品寿命。此智能涂胶技术的研究与应用将会为后续产品的自动化涂胶奠定良好的基础。
