当前,人们希望由动力电池驱动的电动汽车的续航里程将进一步增加,但在电池尺寸和重量不增长的情况下,在有限的空间中储存的能量越多,受损电池过热的风险就越高。基于内阻小、扩容相对方便、成组效率高的特点,方形电池呈现了对终端创新极强的承接能力。无论是CTP/CTC技术,还是大电芯,方形电池都能在其中释放出最大的应用潜力。大尺寸、无模组、长薄化的发展方向为本就占据主导地位的方形电池打开更大的市场。科德宝密封技术公司(Freudenberg Sealing Technologies)正在推出一种新产品,该产品可大幅减少方形电池起火并防止热传播,即热失控的连锁反应。
汽车行业正在经历从内燃机到电动驱动的技术转变。汽车行业上一次类似的技术变革发生在20世纪90年代初,当时从纯机械转向微芯片控制的电子系统。随着电动驱动器数量的增加,安全和可持续性法规也将增加,这将不可避免地导致汽车制造商将负责的法律要求也逐渐增加。
动力电池不可避免热失控发生的风险[1-4]。这种所谓的热失控是电池的灾难性故障,其中化学能在几秒钟内以不受控制的方式释放。通常观察到>1000°C的短期电池高温。根据电池热失控及传播机理,可提高单体电池性能,防止热失控的发生;同时在成组技术方面可采取热失控阻断技术,在单个电池热失控时不扩散到其它单体。热失控阻断技术主要在热传播和扩散的路径进行处理,以达到阻断电池单体发生连锁热失控反应的目的。
电池间间隔物(inter-cell spacers )的使用是阻止热传播的有效手段。特别是增压(超过350 kW),对设计应用高能量的电池施加额外的电化学和热应力。高能电池因此也必须作为大功率电池发挥作用。因此,下一代电动汽车的安全挑战将显着增加。
电池间隔层的必要性和功能
电池间隔层的一个重要功能是柔性机械预载。除了由电池充放电循环引起的可逆体积变化之外,电池还会出现由于老化而变厚的现象,称为膨胀。结合这两种效应,电池厚度可以用锯齿形曲线来描述,如图1。锯齿形的幅度取决于例如电池的总厚度和阳极的硅含量。
这些电池典型的厚度变化必须只发生在一定的压力范围内。需要50至100kPa的最小压力,以防止充电期间嵌入的Si颗粒增加而引起的掺杂硅的阳极材料的退化。通常上限不得超过约1000kPa,以避免充电期间锂(Li)沉积和/或Li枝晶形成。
电池增厚对电池间间隙的影响,如图2所示。
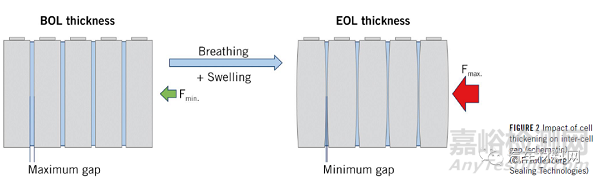
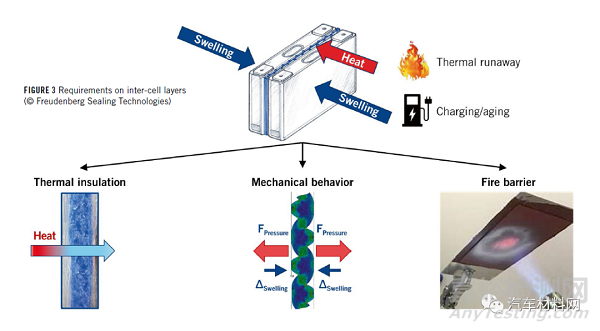
典型的电池间隔层必须满足三个特征,如图3所示:
热绝缘型。在热失控的情况下保护相邻电池不被扩散。
机械性能。确保初始压力约为50-150 kPa,可逆地吸收电池充放电循环和膨胀,并防止压力超过1.5-2 MPa,如图4所示。
防火屏障功能。保持了电池间层的结构完整性,因此在热失控过程中,火焰不会直接影响相邻的电池。
机械性能设计
在电池间隔层开发设计的初期,重点放在机械性能上。开发了在每一侧配备有弹性中间层的设计,如图5。在压缩过程中,中间层经历弯曲和剪切,如所示图4。通过保险杠的有限热接触来防止传播。对于镍锰钴电池NMC 622电池(60 %镍、20 %镁和20 %钴),产品显示出可接受的热屏蔽效果。然而,对于使用具有较高Ni含量的NMC电池系统,必须改进热屏蔽效果。
功能耦合
在电池间隔层的开发中,必须解决好机械和隔热性能之间不可避免的折衷。这两个功能层彼此之间是强耦合的,并且几乎总是导致一种折衷。对于单层和多层电池间隔,这种折衷的处理是不同的。
使用多层解决方案,可以将这些冲突的目标分成两个不同的层。一层及其材料针对机械变形行为进行优化,而另一层及其材料针对热绝缘进行优化。
较硬的绝缘层允许多层结构部分补偿电池老化时的绝缘损失。尽管有这些优势,这种解决方案也存在这种强耦合的问题。坚硬的绝缘层降低了可压缩性,厚的机械层降低了绝缘效果。
机械和热性能设计
为了平衡两层之间的竞争,每一层都被明确地分配了一个主要功能,但是也考虑了次要的需求。遵循这些原则,机械层由专门设计的弹性体制成,以实现高变形性和低压缩性。第一代产品的弯曲特性已经过优化,可提供更高的压缩比,从而为绝缘层节省空间。弹性体的热行为可以在一定限度内得到改善:
通过插入气泡发泡。它们中断了导致隔热的热路径,但是对机械强度有负面影响。
可以集成由绝缘颗粒组成的填充物,其中气体被捕获在机械上更稳定的固体颗粒中。这可以是玻璃微球或多孔材料。如果这些空气夹杂物小于空气的平均自由程(约70 nm),则不会有更多的热能通过这些空气夹杂物传递。这种所谓的纳米多孔颗粒具有大约< 70 nm的空气内含物,适合作为绝缘颗粒。尽管目前还没有更好的绝缘材料,但它们对弹性体导热性的影响受到它们与弹性体材料热形成串联和并联连接的混合物的影响。
用导电性较低的填充材料替代功能添加剂。作用原理与上面解释的一致。
因此,与第一代产品相比,这种弹性体的导热系数可以降低3倍,同时还能改善机械性能和迟滞性能。对于高能量容量的电池,吸热效应不再被认为是有价值的。
关于热绝缘层,机械性能不允许变形性有太大的自由度,以便不损害膨胀的老化电池的绝缘。分层结构带来独特的热串联连接,这使得它能够充分利用其在整体结构中的优势。
模块化系统中串联布置的实现
当前一代的电池间隔层实现了上述的多层方法。该设计包括具有改进的可变形结构的夹层结构,图6。
安装粘合剂层(A),用于将多层电池间层粘合到方形电池的侧表面。
机械层图6(B),是电池间隔多层的中央核心。主要功能是在操作过程中在模块中的电池之间提供压缩力和可变形性。如所示图4对于典型的方形电池,机械层必须设计成具有1.5至2.5 mm的变形能力,以实现大约100 kPa的寿命开始(BOL)压缩,并将寿命结束(EOL)压缩限制到大约1.0 MPa。科德宝主要使用硅酮弹性体,这种弹性体具有可连续挤出的优点,在设计上有很大的自由度,并且可以通过添加填料轻松调整材料特性。
粘合剂层图6(C),单独负责将各层相互粘合。
隔热层图6(D),被理想地设计成阻止热量通过细胞间隙传递。非常好的热障达到0.03 W/(m*K)。纳米多孔颗粒与玻璃纤维非织造布一起用作基材产生了良好的效果。
功能验证
功能验证在电池间隔层的开发设计中是必不可少的。使用所谓的流量计和热板测试的测试台测试被证明对于间隔层的成分是必要的。有了流量计,从项目一开始就可以分析材料和设计的导热性。
为了研究在实际条件下的传播预防,已经建立了微型模块测试。热失控在一个电池中触发,即所谓的有热源电池。测量延迟时间,直到相邻的无热源电池开始热失控。在最佳的情况下,第二电池由电池间层保护,从而防止热传播。迄今为止,科德宝已经开发了几种电池间隔层,在微型模块测试中成功抑制了传播。因此,科德宝展示的模块化系统可用于开发定制解决方案。
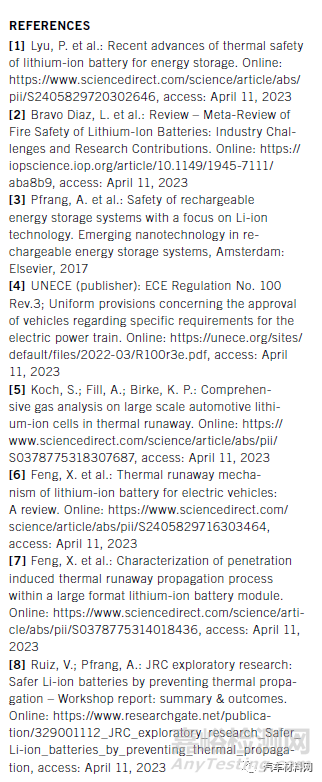
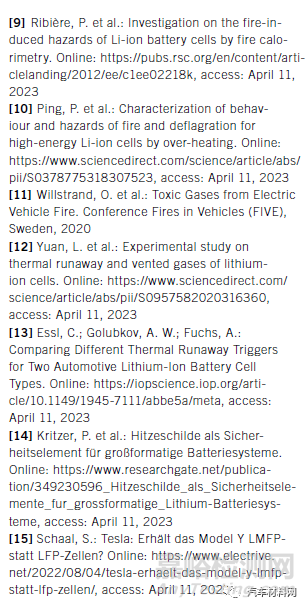
