近些年来,汽车行业为了缩短研发周期,降低研发成本,提高汽车产品的质量与安全性,广泛地将虚拟仿真技术应用到汽车研发设计中。在侧面碰撞过程中,前排座椅侧面安全气囊对车内人员胸部和腹部的保护至关重要,安全气囊的弹出对前车门防撞杆结构、车门内护板扶手产生很大撞击力,因此需要考察在低温(-30℃)气囊点爆时,汽车侧门饰板是否有失效现象。在设计门饰板时,CAE(工程设计中的计算机辅助工程)工作人员首先进行虚拟仿真计算,预测侧气囊弹出时,门饰板的运动和变形情况,随后进行实际点爆,发现仿真分析结果与门饰板的实际受损情况不同。修改仿真分析结果,使现有模型贴近车辆的实际受损情况,在点爆时可为门饰板提供较准确的仿真模型,但仍会与实际情况存在一定的差异,因此CAE工作人员期待能够获得更加精确的碰撞测试数据。
研究人员采用DIC(数字图像相关法)技术,测试了在低温气囊点爆过程中,门饰板受气囊冲击时的变形情况。该技术是一种非接触式光学测量新技术,在试验中使用2台高速相机,进行三维光学的测试,测试结果既可以获得材料在不同应变速率下的应变曲线,又可以获得门饰板在气囊点爆中准确的三维变形云图及数据。此外,还开发了数据分析软件,实现仿真分析结果与实测数值的精确比对,逐点验证了仿真分析结果的准确性。
1、试验方法与设备
1.1 高应变速率拉伸试验
试验设备:2台高速相机(分辨率为1024像素×1024像素,采集频率不小于7000帧率)、DIC软件、液压伺服型高速拉伸试验机。
试验方法:根据仿真分析结果的要求,测试-30℃时拉伸应变速率分别为 0.01,0.1,1,10,100s-1的应力-应变曲线。测试时,根据高速拉伸试验机试样夹持位置与相机的距离、试样的尺寸标定2台相机,完成试样的三维光学测试。
1.2 低温气囊点爆试验
试验设备:2台高速相机、DIC软件、气囊点爆控制器、环境舱。为了模仿整车状态,不影响车门的刚度,直接在白车身车门上切割出窗口,露出门饰板关键区域,并用油漆笔手工绘上白色散斑(见图1)。
试验方法:按照该车型低温气囊点爆试验要求,固定座椅位置,确定相机离门饰板中心的距离,根据测试距离和关键区域尺寸标定2台相机;标定成功后,锁定相机夹角,根据相机与试样的距离及当前视野中试样的选定区域确定最终散斑尺寸;随后调整光源的亮度和位置,调试拍照参数(相机拍摄范围及曝光时间);将气囊点爆控制器与相机拍摄触发线联动,同步触发相机和气囊;关闭拍照系统,整个车身在温度为-30℃的环境舱中保温4h;保温结束后,打开环境舱门,打开拍照系统,按调试好的参数设定相机。所有的操作需在3min内完成,测试后保存所有照片数据。
2、试验结果与分析
2.1 高应变速率拉伸试验
从门饰板上取样,试样的平行段长度为15mm,不同速率下门饰板材料的应力-应变曲线如图2所示。由图2可知:当应变速率从0.01s-1增大到100s-1时,抗拉强度增加了180%,最大应力对应的塑性应变减少了75%。可以看出随着应变速率的增加,材料的力学性能发生改变。当应变速率较低时,材料的塑性较好;随着应变速率不断升高,材料的脆性增加,强度变大,断后伸长率下降。在气囊点爆时,该门饰板受到气囊展开冲击的最大应变速率为100s-1,因此采用高应变速率下的应力-应变曲线代替传统的静态拉伸曲线(应变速率<10-2s-1),可以更加准确地进行仿真计算。
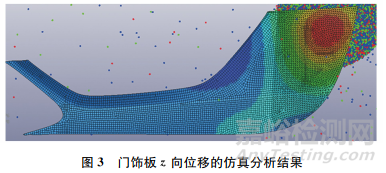
将图2中的数据代入到仿真分析软件中,并输出门饰板关键区域的仿真分析结果,因为门饰板受到座椅气囊弹出而发生变形,所以主要分析门饰板各结点向车门外的变形位移(z向位移),z向为垂直纸面方向,然后按照DIC软件的要求导出门饰板z向位移的仿真分析结果(见图3)。
2.2 低温气囊点爆试验
2.2.1 对齐仿真结果及数据导出
将门饰板低温点爆试验的实际图像导入到DIC软件中,并依据仿真分析的区域划分三角形网格;然后调节云图小平面的尺寸和距离,使三角形的结点距离为5mm;最后输出该区域z向位移的实测云图,结果如图4所示。拉动时间标尺,整个区域的颜色将发生连续的变化,最右面的立柱条数值对应门饰板的z向位移,在7.588mm位置红色最深,表示门饰板变形最大,该位置在板的中上偏右部位,与仿真分析结果大致相同,但中心位置相差约10mm。
上述仿真分析结果与实测结果中变形最大的位置大致相同,说明实测云图区域已满足仿真分析的验证需求。将仿真分析结果导入DIC软件中,并将实测云图与仿真分析结果对齐,结果如图5所示。对齐后,实际点爆试验与仿真分析同时开始,实测结果中网格结点的坐标原点位于仿真分析结果的坐标原点上,该DIC软件保证了实测云图和仿真分析输出的各个结点位置及变形具有可比性。
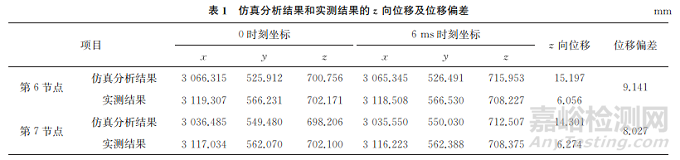
分别导出仿真分析结果和实测结果的z向位移及位移偏差,输出的数据包含结点序号、坐标和z向位移,随机抽取第6,7结点进行分析,结果如表1所示,其中位移偏差是实测结果与仿真z向位移数据直接相减而得。由表1可知:DIC软件可以进行每个时刻、每个结点的实测与仿真结果的对比;对齐后的0时刻坐标偏差范围为±5%。可见对齐存在一定偏差,因此为了获得更加准确的结果,对齐时要尽量保证准确。
实际上DIC软件偏差的计算是依据映射原理,将实测结果映射到仿真分析结果上(见图6),可见零件在实际运动中的各个结点均与仿真分析结果不一致。实测结果与仿真分析结果存在一定的差异,原因是对齐时有误差,且零件的实际变形情况与仿真分析的模拟变形情况不一致。因此在分析结果时建议先查看实测云图视频和仿真分析的完整动画,如果两者变形本身差异很大,可以不关注逐点数据的偏差,只需要导出变形数据即可。
2.2.2 位移和应变的最大值
在门饰板的仿真分析中,还需要观察z向位移和米塞斯真应变的最大值及对应坐标。米塞斯真应变是基于体积不变原理下的材料内部等效真应变,该应变来自空间三维真应变的综合作用。米塞斯真应变的图像处理与z向位移的操作类似,把所有的z向位移和米塞斯真应变输入到数据分析软件中,重新整理和排列后,输出不同结点每个时刻的数据,最后软件自动搜索最大值,并显示最大值的坐标及其出现时间(见表2)。
由表2可知:仿真分析结果与实测结果的最大值及其坐标均有差异;实测的z向位移较仿真分析的z向位移约小4mm,最大值出现的时间约晚于仿真分析的2倍;实测的米塞斯真应变远大于仿真分析结果,而此时该区域没有发生破裂,说明即使应变很大,零件也不会破裂。
为了确认在气囊点爆过程中,最大值数据的合理性,从DIC软件中导出最大值的时间-位移和时间-应变曲线(见图7),曲线中位移和米塞斯真应变的最大值均出现在门饰板的运动过程中间,而且最
大值下降时没有立刻降到左面起点以下,有数据相邻点,所以此次DIC试验是有效的。
把z向位移及米塞斯真应变最大值坐标输入到DIC软件中,分别显示实测结果与仿真分析结果的最大值位置(见图8)。由图8可见:通过 DIC图像处理,可以清楚地了解仿真分析结果与实测结果的差异,实现图像上的准确对比。根据这些数据可更新仿真分析模型,甚至优化仿真算法。
3、综合分析
采用DIC软件进行测试,可以拍摄门饰板在受气囊冲击时的完整变形过程,了解实际试验中门饰板的变形运动轨迹,并获得材料测试级别的位移及应变数据,这些数据在后期与仿真分析结果对齐后可以直接进行对比。对比位移和应变的图像位置可知,实际试验中门饰板的最大位移和应变都处于最上区域,在卡扣区域附近,而仿真分析结果的最大位移和应变所在区域则处于左下区域,不在卡扣区域附近。实际点爆试验中,卡扣发生脱落,说明实测结果更加靠近真实失效区域。对比位移和应变的数值可知,仿真分析得到的z向位移大于实测z向位移,但仿真分析得到的米塞斯真应变远小于实测米塞斯真应变。对米塞斯真应变的测试结果进行分析,发现当应变较大,但应变速率不高时,应变也不会达到断裂失效应变,门饰板不会发生破坏,这与实际点爆试验中门饰板没有发现裂纹的情况一致。但应变过
大会导致卡扣脱落,因此后期要对卡扣区域进行进一步的分析和测试。
4、结论
(1)运用DIC技术以及三维光学测试技术,既可以获得汽车门饰板材料在不同应变速率下的应变曲线,又可以获得门饰板在气囊点爆中准确的三维变形云图及数据。通过三维变形云图,可以直观地观察零件在撞击过程中的变形情况。
(2)试验中获得的变形数据,能够表征出毫米级微观区域材料的空间三维位移和应变。在实测结果与仿真分析结果的采样频率和网格相同的情况下,将实测结果与仿真分析结果对齐,可以逐点验证仿真分析结果的准确性。
(3)使用数据处理的检索方法,将不同时刻所有结点的位移和应变重新整理、排列,输出每个时刻不同结点的数据,搜索出最大位移和应变,以及最大值对应的坐标,可以实现最大值的数值及图像位置一一对应,从而进一步优化仿真模型,为提高仿真分析结果的准确性提供数据支持。
