感应淬火具有高效、清洁、节能等特点,是国家重点推广应用的技术。目前,感应加热技术已经广泛应用于热处理行业,越来越多企事业单位研究和使用感应热处理技术。我公司在齿轮的表面热处理过程中取得了较好的效果,生产效率非常高,产品质量均匀稳定,生产成本大幅下降,但在大模数(m=10~14)齿轮感应淬火生产中存在硬化层分布不合理问题,长期困扰正常生产。另外,在使用过程中齿轮还会出现裂纹、早期疲劳、脆裂等问题,其中造成齿轮断裂的主要原因为齿顶、齿沟硬化层分布不合理。本文针对模数为10以上齿轮感应淬火工艺进行了一种新的工艺方法尝试,取得了较好效果[1]。
1、 大模数齿轮感应淬火硬化层分布情况
齿轮材料使用S48C-V钢,该种牌号为日本牌号,要求脱氧处理,氧含量[O]≤20ppm(1ppm=10﹣6),与中国牌号47Mn钢化学成分接近。S48C-V钢化学成分见表1。齿顶硬化层深度要求4.0~9.8mm,齿根硬化层要求1.9~2.9mm,表面硬度55~60HRC,基体硬度229~277HBW。齿轮结构如图1所示。该齿轮的主要工艺过程为:下料→锻造→正火→粗车→精车→滚齿→感应淬火→回火→抛丸→精车→精滚齿→拉键槽→装配。感应淬火过程中的加热采用集中加热方式,使用电源功率为350kW,频率为2500Hz,加热后采用7.5%浓度AQ251淬火冷却介质淬火[2],淬火压力为0.3MPa,低温回火4h。
表1 S48C-V钢化学成分(质量分数) (%)

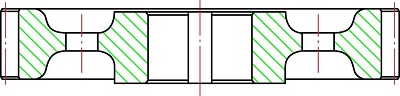
图1 传动齿轮结构示意
感应淬火后硬化层分布情况如图2所示。从腐蚀齿轮试样情况来看,齿顶硬化层深度较深,齿沟硬化层深度较浅,仿形效果较差。借助显微硬度计检测硬化层深度,齿顶硬化层深度为11.5mm,齿沟硬化层为1.0mm,节圆处硬化层深度8.0mm,硬化层分布效果较差,硬化层分布不合理,齿顶硬化层深度过深而齿沟硬化层深度过浅,无法满足图样技术要求(齿顶硬化层4.0~9.8mm、齿沟硬化层1.9~2.9mm)。一方面,此种硬化层分布齿部几乎完全淬透,齿部中心位置没有硬度较低、韧性较好的基体承受传动过程中的冲击,齿轮脆性大大增加;另一方面,齿沟硬化层过浅,没有足够的抗弯曲疲劳强度,容易出现早期脆性断裂、打齿、疲劳损坏等问题。
图2 硬化层分布
2、硬化层分布影响因素分析
通常影响硬化层分布的因素有加热、冷却、原材料特性等。原材料检测合格,排除原材料因素造成的影响。加热影响主要有加热温度和加热层深度,通过红外测温仪检测表面淬火时的温度,检测结果为870~890℃,满足工艺要求。通常硬化层深度主要是由加热层和淬火冷却决定的,加热层主要与频率和加热时间有关,频率越高,集肤效应越明显,硬化层越浅,频率越低,硬化层越深,同时需要配合制定合理的加热时间。
感应加热过程中电流透入深度计算式为
式中 d——电流透入深度(mm);
ρ——材料电阻率(Ω·m);
μ——材料磁导率(H/m);
f——电流频率(Hz)。
电阻率和磁导率是随着温度的变化而变化的。通过计算可知,800℃时2500Hz频率下电流的透入深度约为10mm,该电流透入深度比较合理,说明频率选择合理。但是,实际淬火后硬化层深度仍无法满足要求。通过深入分析发现,感应加热时由于该件模数较大,在2500Hz频率下齿顶加热速度较快,因此很快达到要求的加热层,而齿沟距离感应器较远,温度较低,加热效果如图3所示。为使齿轮的齿顶、齿沟等位置同时达到淬火温度,需要延长加热时间,这就造成齿顶加热时间过长,热量传导至更深的位置,造成齿顶硬化层过深;如不延长加热时间,则会存在硬化层分布问题(见图2),齿沟硬化层深度无法满足技术要求。
图3 单一频率集中加热效果
经分析发现,出现这种现象的原因主要是由于齿轮模数大、齿顶齿沟加热不同步,该种模数齿轮已经不适合整体感应加热淬火,在同一频率下齿顶、齿沟加热无法兼顾。因此,该种大模数齿轮适合采用单齿感应淬火,以较低的频率加热齿沟、较高的频率加热齿顶。单齿感应淬火对齿面和齿沟同时进行扫描感应淬火,齿面、齿沟硬化层分布非常均匀一致,可解决硬化过深问题。然而,经分析计算,单齿淬火生产1件齿轮的时间为25min左右,整体感应淬火生产1件齿轮的时间为3min,因此单齿感应淬火的效率非常低,无法满足生产效率的需求。
3、 试验方案
为解决上述问题,我公司技术人员通过多次讨论分析,决定借鉴双频感应淬火技术,提出一种新的感应加热方式。双频感应淬火技术可实现齿顶、齿沟不同频率加热,可较好地解决硬化层深度分布的问题[3]。但是,我公司设备无法实现同步双频感应淬火,依据在用设备特点,制定出分段、不同步、不同频率加热方案,见表2。
表2 分段、不同步、不同频率加热方案
4、 试验验证
按照改进后制定的感应加热方案进行试验,采用分阶段感应加热淬火工艺,第一段采用2000Hz频率,加热30s,加热温度至750℃左右;第二阶段切换至高频12000Hz,加热22s,加热温度达到850℃;第三阶段再次切换频率至2500Hz,加热15s,加热温度达到880℃后进行淬火,加热效果对比如图4所示。从图4a可看出,改进前,采用单一频率加热时,齿顶、齿沟已完全热透,造成齿部硬化层过深;从图4b可看出,改进后加热效果明显,齿顶、齿沟均已达到淬火温度,而齿部并未热透,淬火后硬化层不会过深。
a) 改进前加热效果
b)改进后加热效果
图4 改进前后加热效果对比
淬火后对试验齿轮进行剖切,并对改进前后硬化层分布进行对比,如图5所示。从图5b可看出,改进后硬化层分布效果良好,齿顶硬化层深度6.5mm,齿沟硬化层深度2.3mm,节圆处硬化层深度4.2mm,满足要求,各位置硬化层均达到要求。
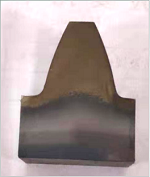
a)改进前硬化层分布
b)改进后硬化层分布
图5 改进前后硬化层分布对比
5、 结束语
按照上述试验方案先后生产齿轮10000余件,产品质量稳定,未出现齿轮故障问题。实践证明,采用分段、不同频率感应加热淬火方式,可较好地解决大模数齿轮硬化层分布不合理问题,为大模数齿轮生产提供了新思路。
参考文献:
[1] 冯显磊,李炎,胡良波,等.推土机齿轮常见裂纹分析与预防[J]. 金属加工(热加工),2015(23):58-61.
[2] 回艳. AQ251淬火冷却介质的特点及使用[J]. 金属加工(热加工),2012(3):54-55.
[3] 黄显臣. 齿轮的双频感应加热淬火[J]. 国外汽车,1990(2):64-66.
