流化床制粒是一种在医药研发领域常用的制粒方法,其具有一次性完成粉末混合、制粒和干燥三个步骤的优点,因此也被称为一步制粒法。通过流化床制粒,可以显著改善药物物料的流动性和可压性,得到的颗粒粒径分布较窄且密度较小。流化床制粒方法包括顶喷技术、底喷技术和切向技术。底喷技术通常用来进行微丸包衣,切向技术可在颗粒外形成更致密的膜层,常用于颗粒掩味等,其中顶喷技术是最常用的制粒方法,能制备出疏松多孔的颗粒。接下来,我们将从以下几个方面来阐述流化床顶喷制粒在医药研发中的重要性。
(1)流化床设备结构及制备原理
流化床顶喷制粒设备主要包括进风空气处理系统、流化床主体、排风及排尘系统和控制系统。流化床主体由物料容器、扩散室、过滤系统和喷雾装置组成。顶喷技术的原理是将粉末放入至物料容器中,通过热风使物料流化,粘合剂溶液由喷嘴进行雾化后,喷至正上升处于扩散室流化的粉末上,粉末润湿并通过粘合剂的作用聚集在一起形成粒子核(又称为成核现象),再继续喷入粘合剂,颗粒之间通过形成固体桥进行生长和合并(生长指小颗粒碰撞到大颗粒,粘结在大颗粒周围,合并指两个粒径几乎一致的颗粒通过碰撞和粘合剂的架桥作用合并在一起),同时,湿颗粒之间会产生碰撞,当外部冲击力超过颗粒之间固有硬度,颗粒会破碎。当颗粒粒度符合要求,停止喷液并进行干燥,从而完成制粒过程。
(2)流化床制粒过程的影响因素
流化床制粒过程受多个因素的影响,包括进气条件、喷枪高度和气流分布板、喷雾速度和雾化压力。
①进气条件:进气条件包括进风温度、进风量和进风湿度。进风温度越高,药物粘合剂的蒸发速度越快,粘合剂的湿润效果就越差,制得的颗粒粒径就越小,堆密度就越低。然而,进风温度过高会导致粘合剂蒸发过快,无法有效制粒;进风温度过低则容易使药物粉末过湿,干燥困难,容易形成颗粒团块。因此,需结合物料的性质,筛选合适的进风温度,比如对于水溶性粘合剂,进风温度可控制在22~55℃之间,对于有机溶剂溶解的粘合剂,可控制在25~40℃之间。
②喷枪高度和气流分布板:喷枪高度和气流分布板是设备相关的因素。降低喷枪高度可以增加颗粒的粒径、堆密度和振实密度,并减少颗粒易碎性。然而,喷枪过低容易与沸腾的颗粒接触,造成喷枪堵塞;喷枪过高则使粘合剂到达药物粉末的距离过远,增加粘合剂的挥发,使得颗粒变小且细粉含量增加。
气流分布板在流化床中主要作用一是承载物料,二是均匀分布气流。气流分布板开孔的形状、大小及开孔率决定气流阻力。气流阻力越大,能耗损失大,流化质量越差。目前市面上常见的气流分布板有两种,一种是直流式,气流方向正对着床层,这种易产生沟流现象,且气流分布板中小孔易堵塞,特别是在物料粒径较小、密度大、易粘结时情况下更为明显;一种是斜孔式,这种可以让气流呈旋转式流动,消除死床现象,不易堵塞和泄露物料,但这种气流分布板成本较贵。有研究发现,在同样的实验条件下,斜孔式比直流式传热和热效率更高。
③喷雾速度和雾化压力:喷雾速度和雾化压力对颗粒的大小和粒径分布具有显著影响。较高的喷雾速度会促使颗粒快速增长,粒径和堆密度增大,颗粒之间的孔隙率减小,但过高的喷速会导致床层塌陷。降低雾化压力可以使喷出的粘合剂雾滴变大,有利于颗粒的生长和成核。有研究发现,如果物料是水溶性,可溶性成分可以溶于粘合剂雾滴中,可以进一步提升颗粒生长。此外,颗粒的大小还与制粒过程中腔体内的湿度成正相关。
(3)流化床顶喷制粒的放大应用
由于不同厂家生产的流化床设备在腔体内可能存在一些差异,例如腔体内的空气气流状态、扩散室的形状以及喷枪的设计等。因此,在进行放大应用时,最好选择同家厂家的设备进行小试和放大,同时还需注意以下几点以保证结果的一致性:
①床层高度:床层高度对颗粒的粒径、堆密度和振实密度有影响。随着床层高度的增加,颗粒的尺寸、堆密度和振实密度也会增加。然而,过高的床层高度会导致气流不能有效穿过物料,影响流化状态,造成颗粒在不同区域之间的差异。因此,在放大过程中,最好保持床层高度与小试时相同。需要注意的是,由于放大设备的体积较大,物料床层会变得更加紧密。一般来说,与小试相比,放大设备所制备的颗粒堆密度会增加约20%左右。
②进风风量:进风风量对物料的流化状态和干燥效率具有影响。为了确保放大结果的一致性,干燥效率应保持一致。干燥效率取决于进风风量和气流分布板的横截面积。因此,在放大时,可以按照以下公式计算进风风量:
放大后进风风量 = 小试进风风量 * (放大后气流分布板横截面积 / 小试气流分布板横截面积)
③喷雾速度和雾化压力:喷雾速度和雾化压力对颗粒的大小和粒径分布有重要影响。放大时,为了保持颗粒大小的一致性,可以根据以下公式计算放大后的喷雾速度:
放大后喷雾速度 = 小试喷雾速度 * (放大后气流分布板横截面积 / 小试气流分布板横截面积)
同时,应保持喷雾压力与小试时相同,以获得相似的颗粒大小。在放大过程中,还可以通过保持喷雾速度和雾化压力的比值与小试时一致,以减少制粒时间。例如,如果放大生产中有3个喷嘴,小试时喷雾压力为2 bar,根据上述计算得到放大后喷雾速度为100 g/min,为了保持得到相似的颗粒,放大后的喷雾压力应设为2 bar,喷雾速度可提高至100 g/min * 3 = 300 g/min,其中3表示喷嘴的数量。
④进风温度和湿度:进风温度和湿度可以影响颗粒的生长过程。在放大过程中,需要保持进风温度和湿度与小试时一致,以确保结果的可比性。
参考文献:
1、邱怡虹,陈义生,张光中,等.固体口服制剂的研发:药学理论与实践[J].化学工业出版社,2013.
2、罗家欢.考虑原料属性变化的循环流化床制粒过程建模及质量控制方法研究[D].东北大学[2023-07-01].
3、梁雪松,肖勇,吴立群,等.流化床反应器分布板开孔率计算方法初探[J].云南化工, 2006, 33(4):3.DOI:10.3969/j.issn.1004-275X.2006.04.011.
4、刘巍,汤文成.气体分布板开孔结构对流化床干燥性能的影响[J].中国工程科学, 2006, 8(2):4.DOI:10.3969/j.issn.1009-1742.2006.06.007.
5、如何解决流化床放大工艺技术难题[J].流程工业, 2021(9):4.
6、如何基于QBD理念实现流化床工艺放大
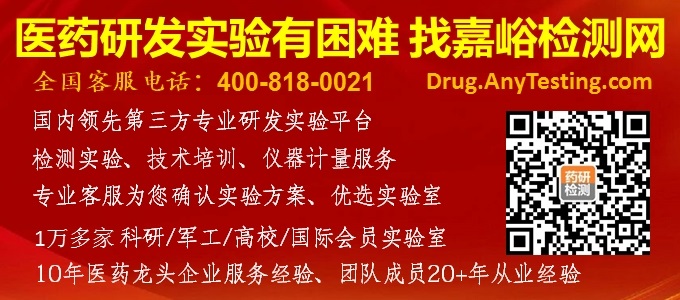