摘 要:框架类铸件易变形,尺寸控制难度较大。以一款六缸柴油机曲轴箱为例,从产品结构、工艺布置、温度场分布和浇注系统设计等方面,介绍扁长框架结构铸铁件弯曲变形的潜在影响因素和预防措施。结合CAE 仿真和三维光学扫描技术,对形变进行量化分析,为相似产品工艺设计提供参考。
关键词:框架结构;弯曲变形;CAE 仿真;三维光学扫描
引言
框架类铸件在生产过程中容易产生变形,通常呈现为整体弯曲变形和局部收缩变形两种模式。其中弯曲变形主要是因为铸件在冷却凝固过程中受力不均,残余应力超过屈服强度产生的塑性变形[1]。以一款在潮模砂造型线生产的六缸发动机曲轴箱为例,从产品结构、工艺布置、凝固温度场分布和浇注系统设计4 个方面对比分析扁长的框架结构铸件生产变形的潜在原因和预防措施。
1、 框架铸件变形问题描述
开发一款6 缸发动机曲轴箱,铸件材质为HT250,为提升工艺出品率,根据产品尺寸和造型线砂箱尺寸,采用一箱3 件的工艺布置方案。其中3 件铸件在型腔内的状态不完全一致,依次为1#、2#和3#,其中2#和1#中心对称布置,3#与2#同向布置,如图1 所示。
图1 一箱3 件工艺布置示意图
初始工艺将内浇道布置在下平面瓦口对面位置,生产一批次铸件,对同一箱浇注的3 件铸件进行扫描检测,结果显示3 件铸件均产生不同程度的弯曲变形,其中2#轻微变形但满足铸造公差要求;1#和3#变形量大,超出铸造公差要求,且超差数据有规律分布。为排除组芯合模造成的错型干扰,在上模、主体芯组、下模成型的铸件区域分别取点检测,并统计数据进行对比分析,瓦口侧检测数据如图2 所示,数据统计分析见表1。
表1 瓦口侧扫描数据对比分析表
图2 瓦口侧扫描检测图
下平面侧检测数据如图3 所示,数据统计分析见表2。
表2 下平面侧扫描数据对比分析表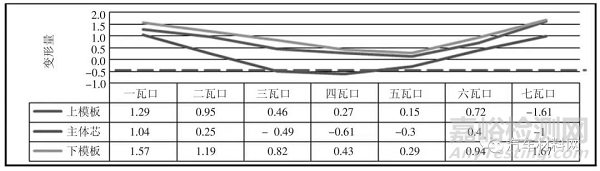
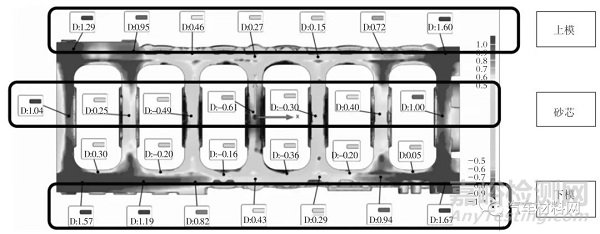
图3 下平面侧扫描对比结果
综合分析以上统计数据,结果显示:由上模、砂芯、下模成型的铸件尺寸超差趋势一致,瓦口侧两端近似持平、中间向外凸出,平面侧中间近似持平、两端向外翘起,铸件整体呈现出弯曲变形。实际测量两端与中间的最大差值达到2.0 mm。
2、 潜在变形原因分析
2.1 产品结构造成的内应力
该框架铸件材质为HT250,长度近1000 mm、宽度约350 mm、厚度仅100 mm,均布6 处镂空大缸,连接板最大宽度48 mm,R30 mm 圆角过渡,为典型的扁长框架结构,瓦口侧结构相对孤立,下平面相互连接,如图4 所示。
图4 铸件结构示意图
为研究产品结构自身对弯曲变形的影响,对单一铸件进行了凝固模拟和应力分析。结果显示,铸件自身出现瓦口侧中间高,两端低的弯曲变形趋势,如图5 所示。主要是因为单一铸件在凝固收缩时,中间镂空部位由砂芯填充,相对孤立的瓦口收缩受阻,相互连接的下平面凝固过程中线性收缩,在下平面形成拉应力促使铸件产生弯曲变形。
图5 单一铸件凝固模拟示意图
2.2 工艺布局温度场分析
不考虑浇注系统,仅对3 件铸件进行凝固分析,温度场分布如图6 所示,其中1#和3#铸件一侧为2#铸件形成的热环境,另一侧为砂芯砂型形成的冷环境,不平衡的温度场影响铸件单一的凝固顺序。铸件冷却较快的一侧受压应力产生内凹变形,冷却较慢的一侧受拉应力产生外凸变形[2]。而处于中间的2#同时受到两侧铸件产生的温度场的影响,凝固环境相对平衡,基本保持单一的凝固顺序。
图6 一箱三件凝固温度场示意图
2.3 浇注系统布置分析
对于采用一箱多件、立置浇注的工艺布置方案。横浇道和内浇道位置的设定,有两种方案可选择:一是内浇道布置在瓦口主轴承位置,二是内浇道布置在下平面。
分别对内浇道设计在瓦口侧和平面侧的两种方案,进行凝固应力模拟分析,对比两种内浇口布置方案的变形趋势。结果显示,内浇口在瓦口侧的3 件铸件均未产生明显的变形。而内浇口在下平面的3 件铸件1#和3#出现明显的变形,变形趋势均为外凸,2#未产生明显变形,仿真计算结果与实物尺寸检测结果趋势一致,如图7 所示。
图7 浇注系统与铸件变形趋势示意图
原因分析:在凝固中后期,薄壁铸件和内浇道优先凝固,粗壮的横浇道开始凝固,线性收缩产生通过内浇道对铸件施加向内的拉应力,使得铸件呈现出如图8 所示的歪曲变形。
图8 浇注系统对铸件变形作用示意图
综合上述三方面潜在变形原因和影响趋势,可得出如下的对应关系。产品结构存在固有的潜在变形趋势,温度场对不同位置铸件的形变影响为两侧促进、中间抑制,浇注系统在平面侧促进变形、在瓦口侧抑制变形,详见表3。
表3 铸件变形影响因素矩阵表
注:与变形正影响用“+”表示,与变形负影响用“-”表示,无影响用“/”表示;
当产品三种影响因素都为正关系时,铸件变形趋势相互叠加,加剧铸件弯曲变形。当三种影响因素为正负关系时,铸件变形趋势相互抵消,抑制铸件弯曲变形。
3、 生产验证与尺寸检测
通过理论分析和仿真计算,发现在相同的工艺布局下,内浇道布置位置是铸件弯曲变形的主要影响因素,据此进行工艺改进,将内浇道布置在瓦口主轴承位置,生产一批次铸件,对同一箱浇注的3 件铸件进行外观扫描检测,结果显示尺寸全部合格,偏差在±0.5 mm 以内,铸件中间与两端没有明显的弯曲变形,扫描对比结果如图9 所示。
图9 内浇口布置在瓦口主轴承的铸件扫描对比结果
4、 结论
通过理论分析、CAE 仿真并结合实际生产验证和测量分析,得出如下结论:
(1)扁长的框架结构铸件在凝固时易产生使铸件弯曲变形的内应力。
(2)不平衡的温度场加剧铸件变形,相对平衡的温度场能减缓铸件变形,工艺设计时应结合产品结构选择合理的工艺布局。
(3)浇注系统在冷却凝固收缩过程中也会产生使铸件弯曲的拉应力。内浇道布置在瓦口侧会抵消铸件自身变形,尺寸精度高;内浇道布置在平面侧会加剧铸件自身变形,造成尺寸超差。
(4)框架类铸件工艺开发,应统筹考虑产品结构、工艺布局等对铸件尺寸的影响,合理设计浇注系统,提高铸件尺寸精度。也可根据产品结构和工艺布局设计反变形,必要时增加工艺辅助结构,抑制变形[3]。
参考文献:
[1] 陈国桢,肖刻则,姜不居.铸件缺陷和对策手册[M].北京:机械工业出版社,1996.
[2] 柳百成,黄天佑.中国材料工程大典-材料铸造成型工程[M].北京:化学工业出版社,2005.
[3] 周照峰.一种框架形铸件的铸造工艺设计[J].现代铸铁,2017(04):40-41.
