某批次热机械轧制钢板(TMCP)材料为Q420GJC钢,厚度为55mm。按照 GB/T 2975—2018《钢及钢产品力学性能试验取样位置及试样制备》,在钢板1/4厚度处取直径为10mm的圆棒拉伸试样,并按照GB/T 228.1—2021《金属材料 拉伸试验 第1部分:室温试验方法》进行拉伸试验,并在钢板1/4厚度附近位置取样,再次进行2次拉伸试验,3次力学性能测试的结果如表1所示。由表1可知:初始测得的屈服强度为375MPa,抗拉强度为543MPa,其中屈服强度比标准要求的下限410MPa低了35MPa;2次复验测得的屈服强度分别为401MPa和418MPa,比初始测得的屈服强度增大了约40MPa,且2次复验测得的抗拉强度也相差41MPa。
该钢板的力学性能差异较大,对拉伸试验过程进行排查,排除了人为和试验设备的原因。针对这一问题,研究人员进行了一系列理化检验,研究了该Q420GJC钢板力学性能不合格以及测试结果差异大的原因,并提出了相关改进建议,以避免对钢板产品性能的判定出现争议。
1、 理化检验
1.1 化学成分分析
对该Q420GJC钢板进行化学成分分析,结果如表2所示,可见钢板的主要化学元素的含量均符合产品标准规定,因此可以排除钢板取样、制样或炼钢过程化学成分控制偏离的原因。
1.2 不同厚度位置的拉伸试验
考虑到钢板厚度为55mm,且力学性能测试结果的差异较大,有可能是圆棒拉伸试样的取样位置存在偏差所致,因此在钢板7个不同厚度位置取样进行拉伸试验,取样位置如图1所示,其中位置1位于上表面下方12mm处,位置2位于上表面下方14mm(1/4厚度)处,位置3位于上表面下方17mm处,位置4位于钢板心部(1/2厚度),位置5位于下表面上方17mm处,位置6位于下表面上方14mm(3/4厚度)处,位置7位于下表面上方12mm处。
将试样加工成直径为10mm的圆棒试样,此外还加工了一个全厚度矩形截面拉伸试样,对试样进行拉伸试验,结果如表3所示。由表3可知:位置1~7的屈服强度和抗拉强度变化趋势总体一致,其中位置1和位置7的力学性能最好,其屈服强度分别为459MPa和488MPa,抗拉强度分别为604MPa和631MPa;钢板1/4厚度处(位置2)和3/4厚度处 (位置6)的屈服强度分别降低至415MPa和432MPa,抗拉强度分别降低至575MPa和587MPa;钢板中心(位置3和位置5)的屈服强度和抗拉强度继续降低,其中屈服强度分别降至394MPa和409MPa,已经低于标准要求的下限(410MPa),钢板中心处(位置4)的屈服强度和抗拉强度最低,分别为372MPa和531MPa;全厚度矩形拉伸试样的屈服强度和抗拉强度分别为438MPa和589MPa,大于钢板1/4厚度处和3/4厚度处的屈服强度和抗拉强度,且满足标准要求。
1.3 不同厚度位置的硬度测试
从钢板上表面沿钢板厚度方向每隔2mm取样,进行维氏硬度测试,直到覆盖钢板全厚度,钢板厚度方向的硬度分布曲线如图2所示。图2中的曲线形状呈现出两头高、中间低的“碗”形分布特征,其中钢板上、下表面的硬度最大,约为220HV;钢板1/4和3/4厚度处的硬度降至183HV和194HV;钢板心部处的硬度最低降至165HV,比钢板表面硬度降低了55HV。硬度测试结果与力学性能测试结果基本吻合,符合碳钢硬度与抗拉强度成正比关系的一般规律。
1.4 金相检验
在拉伸试样的邻近位置截取全厚度金相试样,经研磨、抛光后,用4%(体积分数)硝酸乙醇溶液腐蚀,然后在光学显微镜下对钢板不同厚度处的显微组织进行观察,结果如图3所示。由图3可知:钢板上、下表面附近的组织为贝氏体+少量针状铁素体;1/4厚度处的组织是针状铁素体+珠光体,且中间夹杂着少量粗大多边形铁素体;1/2厚度处的组织是铁素体+珠光体,其中粗大多边形铁素体含量较多,晶粒尺寸较大;3/4厚度处的显微组织主要是贝氏体+少量铁素体,该处的晶粒尺寸比上、下表面附近的晶粒尺寸大。
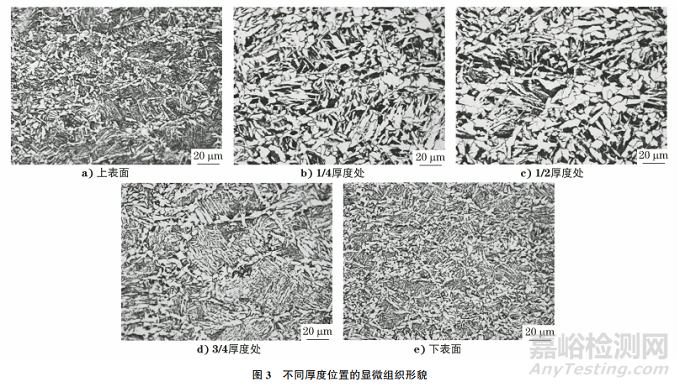
2、 综合分析
基于该实验室的试验机能力以及GB/T 2975—2018的要求,对于厚规格(厚度大于50mm)TMCP钢板,通常采用1/4厚度处的圆截面拉伸试样进行拉伸试验,而此次试验中,该位置圆棒拉伸试样的屈服强度波动较大,上述位置2和位置3的拉伸试样取样位置仅相差3mm,屈服强度相差21MPa。虽然钢板全厚度矩形拉伸试样的屈服强度满足产品规定,但钢板1/4厚度处的圆棒力学性能已无法代表钢板的整体性能。从钢板不同厚度位置的硬度分布曲线上也能发现,钢板1/4厚度处的硬度变化非常大,这与力学性能测试结果相吻合。从金相检验结果可知,不同厚度位置的组织差异较大,1/4厚度处的显微组织无法代表全厚度的组织形态。考虑到实际试样加工过程中的位置偏差不可避免,采用1/4厚度处的圆棒拉伸试样在特殊情况下会影响产品的性能判定。因此,对于 TMCP钢板,当机加工和试验机能力允许时,应使用全厚度试样,或在产品协议中对拉伸试样的类型进行明确规定,否则容易引起性能异议。
按照钢板的化学成分和轧制工艺,正常情况下钢板的显微组织应为贝氏体,且不同厚度位置的组织应相对均匀一致,而该钢板不同厚度位置的显微组织截然不同,产生该异常现象的原因可能是轧制过程中某个控制步骤出现了偏差,如终轧温度偏高、冷却速率较慢等,从而影响了钢板内部组织的相变过程,导致贝氏体转变仅发生在钢板的上、下表面处,钢板内部发生的是铁素体和珠光体转变,最终使钢板在不同厚度位置形成了差异较大的显微组织。要探究发生该异常的确切原因需要对钢板整个轧制工艺过程进行更深入的调查。
3、 结论与建议
(1)该钢板力学性能异常原因是钢板轧制过程中某些控制步骤出现偏差,导致钢板内部在厚度方向上的显微组织分布不均匀,造成1/4厚度处圆棒试样的力学性能不稳定,无法有效代表钢板的整体性能。
(2)对于TMCP厚规格钢板,供货双方宜在产品协议中对拉伸试样的类型进行规定,当产品性能有争议时,应采用全厚度矩形拉伸试样进行仲裁。此外,在新产品开发或发生产品性能质量纠纷时,可对钢板不同厚度处的力学性能进行全面分析。
作者:张华
单位:宝山钢铁股份有限公司 制造管理部
来源:《理化检验-物理分册》2023年第6期
