介绍
治疗性分子有时被冻干以达到可接受的作为商业药品的保质期。然而,冻干是一个昂贵的过程,处理时间长,因此减少冻干周期时间是工业关注的一个领域。随着ICHQ8(R2)的推出,从监管的角度和质量的角度来看,质量源于设计(QbD)的应用正在成为一种期望。QbD的目标是在过程中质量控制,而不是在过程结束时离线监控。冻干过程基于传热传质的基本原理,因此非常适合应用QbD原理设计。
过程分析技术(PAT)和设计空间是QbD的两个关键要素。随着PAT技术的进步,现在有许多在线监测工具可用于监测和/或控制冻干过程的各个步骤。此外,关注冷冻干燥过程QbD的论文数量正在增加,这强调了冷冻干燥过程非常有利于QbD原则的应用。本文的目的是描述一个简单而实用的程序,基于传热传质理论,适当考虑设备限制,为初级干燥步骤构建一个设计空间,识别产品质量属性(PQAs)和关键质量属性(CQAs)之间的差异。简而言之,并非所有的PQAs都是关键的。初级干燥通常是冷冻干燥过程中最长和最关键的步骤,这可能导致产品因塌陷而失去优雅外观。通常,初级干燥的设计空间旨在将产品温度保持在低于塌陷温度(或共晶温度)的安全范围内。用差示扫描量热法(DSC)测量为Tg′或用冷冻干燥显微镜测量为Tc。然而,大多数情况下,崩解并不会对工艺过程中和工艺后的稳定性产生不利影响,虽然产品外观的丧失是产品质量的丧失,但外观可能不会对功效或安全性产生直接影响。同样,应尽量减少工艺持续时间以减少产品成本,尽管产品成本对制造商和客户都很重要,但通常不是“关键”重要性。因此,在我们看来,初级干燥的“设计空间”需要承认产品温度对外观和工艺成本的影响,但也要通过适当的实验,建立维持CQAs的空间。定义设计空间,目标是获得对药品质量的工艺参数的理解,从中制定适当的控制策略。最后,作者还提供了他们对要求冷冻干燥工艺设计空间的挑战和实际意义的想法(这是一个在文献中很少受到关注的主题)。
构建初级干燥设计空间:一种简化方法
从产品质量和过程经济的角度来看,优化初级干燥步骤是工业的重点,因为在所有冰都被除去之前过早地进行二次干燥将导致产品融化,而在所有冰都被除去之后,在初级干燥中保持太长时间将导致不必要的长干燥时间和工艺成本。如图1所示,定义冻干工艺设计空间的过程首先从绘制质量通量与腔室压力的关系开始。阴影空间被定义为新的形式和呈现的未开发空间(图la)。工业冻干机通常不能控制室压力低于约50mtorr ,通常大于300 mtorr也没有意义。因此,驱动步骤的设计应使腔室压力在上限和下限之间,例如50和300 mTorr。人们可以将50到300 mTorr之间的压力区域称为知识空间(即,数据要么存在于文献中,要么存在于内部经验中,如图1b)。从这一点开始,我们的目标是在这个知识空间中为给定的处定义设计空间。首先确定操作空间,并在此基础上定义设计空间。首先,每个冷冻干燥机可以支持一个有限的升华速率(即,最大允许升华速率),超过这个速率,过程就会失控(即,失去室压控制)。图1c中的红色虚线表示实验室规模的干燥器的堵塞流量限制,超过该限制将失去压力控制。粉色虚线表示生产规模,可以位于实验室规模干燥线的两侧。了解生产规模冷冻干燥机的局限性和能力是建立冻干工艺设计空间的关键,这确实需要制造商的承诺,以完全表征升华速率极限作为每个生产规模冷冻干燥机的腔室压力的函数,以建立操作空间。给定干燥器的最大允许升华速率由冰升华试验确定,其中所有架子都装载冰,并且腔体压设置为0 mTorr;在这里,升华率可以通过可调谐二极管激光吸收光谱(TDLAS)测量,也可以通过容器系统的腔室压力、板层温度和传热系数来计算。根据升华速率和冻干机的设计和几何形状,箱体压平衡到某一值(即可达到的最小室压)。堵塞流量的极限主要取决于冷冻干燥机的设计和几何形状。根据配方和工艺条件的不同,高于堵塞流量限制的d冻干(如图1c所示的堵塞流量状态)可能会触发压力控制失控的警报,从而导致板层温度和腔室压力在警报限制之间循环,进而可能导致批次的损失。腔室压力极限和堵塞流线之间的空间定义了操作空间(用水平线阴影的区域,图1c),其中的工艺参数应定义为在冷冻干燥机的操作极限内进行工艺。目前,操作空间是由最终用户定义的,但冷冻干燥机制造商可能应该考虑提供这些数据作为新冷冻干燥机OQ/IQ测试的一部分。这些数据对于了解冷冻干燥机在开始使用时的能力和容量以及在以后的时间点评估和比较其性能将非常有用。总的来说,在设计、开发和放大冷冻干燥过程时,如果有这些现成的数据,该行业肯定会受益。
此外,假设初级干燥过程中所需的产品温度或目标产品温度选择为21℃(即低于塌陷温度的“安全边际”),用黑色虚线表示(图1d)。请注意,相应的板层温度是由腔室压力和升华速率决定的,但没有显示在该图上。-21℃的产品温度线在130 mTorr时与堵塞流线相交;因此,在这种情况下,可实现的最小腔室压力为130 mTorr。如果期望的产品温度是-21°C,那么在过低的温度下运行工艺,例如<-24°C,将导致不必要的结果初级干燥时间非常长,因此下方的黑色虚线表示产品温度的下限(图1d)。然而,人们不能直接控制产品温度;相反,间接控制产品温度的是板层温度和腔室压力。因此,板层温度等温线(图中三角形和菱形)进一步定义了腔室压力和板层温度组合,可能用于实现-21°C和24°C之间的产品温度。绿色阴影区域被定义为设计空间,而蓝色阴影区域被定义为控制空间,这是设计空间中的一个区域(图1f),而不是单个点。这一特点反映了控制系统无法在固定点控制腔室压力或板层温度(例如,需要允许货架温度为±3°C,腔室压力为±15 mTorr)。如前所述,这些数据应由冷冻干燥机制造商提供,但由用户在操作资格测试中确认。当然,实际设定点(即控制点)的过程在控制空间内(图1f)。
图1所示。构建冻干工艺初级干燥步骤的设计和控制空间:(a)未开发空间,(b)知识空间,(c)操作空间,(d)产品最高和最低允许温度极限,(e)板层温度等温线,(f)设定点设计和控制空间。
设定值的选择应在设计空间内使工艺在较短的周期时间内朝着高升华率区域运行。同时要考虑正常的批内和批间差异,通常,设计空间是通过计算和实验来评估的,这些计算和实验关注的是平均行为。然而,产品温度和升华速率的显著差异确实存在于给定的批次中,差异取决于产品和冻干机。虽然确实是平均升华率决定了冻干机过载的可能性(即堵塞流),产品质量取决于单个产品温度历史,并且不足以确保平均产品小瓶具有可接受的质量。基本上所有的产品瓶,或者至少几乎所有的,必须保持可接受的质量(“几乎”的含义取决于失去质量属性的后果)。因此,必须存在一个适当的安全范围,这意味着设定值应该远离产品在不损失产品质量的情况下可以承受的最高温度,再次假设设计空间是基于平均行为。目前,解决这一问题的常用做法是将温度上限设置为“安全边际”,通常比测量的坍塌温度低至少2°C。然而,这种做法要比严格地表针正常批次内变化和放大差异对产品行为的影响,并将这些定量结果纳入设计空间的评估中要好得多。对工艺变量变化对产品温度历史和质量变化的影响进行统计处理的努力尚处于起步阶段。
一般来说,过程被控制在控制空间内;然而,在设计空间的任何地方,该过程都将产生可接受的产品质量。同样,这里提出的方法并不是唯一的方法,而是可以用于实现定义设计和控制空间的最终目标的几种方法之一。图1中定义的设计和控制空间只是一个示意图,用于说明该方法的总体情况。实际的设计和控制空间将取决于配方、冷冻干燥机和容器封闭系统。此外,设计空间应该在科学的基础上认识到这一过程及其对PQAs的影响,而不是仅仅依赖于“已证实的可接受范围”。
上述方法解决了通常的目标,即为避免坍塌的初级干燥创造一个设计空间,其中的临界温度可能通过DSC (Tg’)或冷冻干燥显微镜(Tc)进行评估。产品坍塌不仅导致缺乏优雅外观,还可能导致高残留水和更长的重构时间。高残留水反过来又会影响产品的稳定性。然而,必须认识到,小瓶中的坍塌通常发生在远高于Tg′的地方,在某些情况下甚至远高于Tc此外,尽管坍塌确实会破坏优雅外管,但它通常不会对稳定性产生不利影响。因此不会降解,甚至坍塌提高稳定性的例子。这些观察结果的含义是双重的。首先,为了提供风险评估的数据,人们应该故意在实验确定的坍塌温度以上冻干,以验证坍塌确实发生了,如果发生了,在什么温度下发生。其次,需要评估远高于Tg′或Tc的冷冻干燥对产品降解的影响,无论是在加工过程中还是在加速储存稳定性试验期间。如果,如一般所发现的那样,对产品降解没有不利影响,或者对于快速重构对适当患者护理至关重要的产品,重构没有严重延长,则在产品中进行远高于崩解估计或崩解观察的初级干燥不会导致CQA的损失。因此,尽管人们可能希望避免塌陷以保持产品的外观,但外观对患者的后果是轻微的,避免塌陷的特殊措施是不必要的。
因此,基于冷冻干燥机的传热传质特性、配方/呈现、以及密封系,人们可以开发一个工艺设计空间,同时全面了解关键工艺参数(CPPs)及其对质量属性的影响。虽然这里只展示了一次干燥设计空间,但人们可以很容易地采用类似的方法来构建冷冻和二次干燥的设计空间。此外,PAT工可用于监视和控制每个步骤的控制空间内的CPPs,以确保质量是在过程设计和控制中建立的,而不是在过程结束时离线监视。在几种CPPs中,一次干燥终点的确定是最关键的。相对便宜和强大的技术,皮拉尼计等仪器可用于实时监测初级干燥时间,并评估所有小瓶何时用冰升华完成,并且提高板层温度进行二级干燥是“安全的”。预定义的皮拉尼- CM(电容压力计)差分可用于从初级干燥推进到二级干燥,从而消除了定义固定初级干燥时间所需要的猜测。
为什么要创造设计空间?
通过申请设计空间获得的监管是,如果需要,工艺参数设定值可以在设计空间内自由移动,而不需要大量的监管备案。工艺设计空间也将显著减少由于板层温度和腔室压力与设定值的轻微偏移导致工艺偏差的数量。然而,问题出现了,对于一个声称设计空间的过程,验证程序是什么样子的?验证通常在设定点进行,并进行稳健的研究以确定失败的边缘。然而,如果有人要求设计空间,那么QbD范式下的验证程序将意味着持续的改进和验证(即,正在进行的活动),而不是公司执行的一次性活动。三个验证批号的一般经验法则将不再定义为验证程序;相反,基于科学和基于风险的方法的产品和过程理解可以用于控制和验证生产规模的过程,这是基于代表性的缩小模型进行的研究。传热传质理论的数学计算经过适当的参数化和与实验的对比检验,可用于构造和“验证”设计空间的边缘。
如果过程由于持续改进和验证而发生变化,那么CQAs是否也会发生变化?通常会在设计空间内更改流程,以解决可能影响产品质量的问题。在QbD方法下,在产品和过程开发的整个生命周期中获得的知识可用于决定是否需要更改过程和CQAs。最后,持续的过程监测和控制将有助于防止过程失控,从而导致产品质量损失。
本文为翻译文章,原文献:SAJAL MANUBHAI PATEL, MICHAEL J. PIKAL. Lyophilization Process Design Space.
Published online 14 August 2013 in Wiley Online Library (wileyonlinelibrary.com). DOI 10.1002/jps.23703
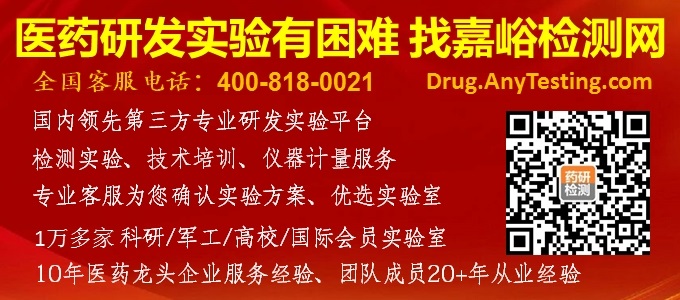