Potting Material Failure
密封陶瓷失效
Potting materialis the urethane component that is poured into the filter frame during filterassembly; the filter media is then placed into the potting material to create aleak free bond between the paper element and the filter frame.
密封材料是在过滤器组装过程中注入过滤框架的聚氨酯成分;然后将过滤介质放入密封材料中,在纸元件和滤芯框架之间形成无泄漏粘结。
A case studyinvolved occasions when leaks were found at this bond only a few months afternew filters were installed and initially passed a leakage test. It wasdetermined the manufacture of the potting material supplied to the filterassembler/manufacture had changed their formulation. The new formulation hadinsufficient quality control before it was released for use. The inferiorpotting material over time would shrink, eventually pulling on the filter elementand breaking the bond and seal.
有案例显示在安装新过滤器并通过泄漏测试仅几个月后,在过滤器的密封胶处发现了泄漏。最后发现过滤器组装商/制造商的密封材料供应商的制造改变了配方。新配方在放行使用前质量控制不足。随着时间的推移,劣质的密封材料会收缩,最终拉动过滤元件,破坏粘合和密封。
When selecting afilter manufacturer, it is prudent to inquire about their quality controlmeasures and those applied to their material suppliers. It is also imperativethat the purchase agreement includes a requirement that if at any time thefilter manufacturer suspects a possible universal problem, all end-users of theimpacted filters be notified.
在选择过滤器制造商时,谨慎询问其质量控制措施及其对物料供应商的控制措施。此外,采购协议还必须包括一项要求,即任何时候一旦过滤器制造商怀疑可能出现质量问题,应通知受影响过滤器的所有最终用户。
Insufficient Amount of Gel in the Filter Track
过滤器凹槽凝胶量不足
There have beensome cases observed in which the HEPA/ULPA filters are delivered from thefactory with an insufficient amount of gel in the track such that the knifeedge does not penetrate the gel sufficiently, resulting in air bypass leakage.
在一些情况下,从工厂交付的HEPA/ULPA过滤器,其凹槽中的凝胶量不足,因此刀刃不能充分插入凝胶,导致空气旁路泄漏。
Loss of Gel Adhesion
凝胶粘附性丧失
Loss of geladhesion is not a common failure mode. Adhesion between the gel and othersurfaces may becompromised if the surface incontact with the gel is contaminated with foreign substances or oils. Off-ratiomixing of the gel, or other manufacturing errors or defects with the gel itself,can lead to surface blooming and exudation of unbound components that caninterfere with the surface tack (stickiness) of the gel.
凝胶粘附力丧失不是常见的失效模式。如果凝胶接触的表面受到异物或油的污染,凝胶与其他表面之间的粘附可能会受到影响。凝胶混合比例,或凝胶本身的其他生产错误或缺陷,可能导致表面溢出和渗出的未结合的成分,可能会干扰凝胶的表面粘附(粘性)。
Knife Edge Alignment
刀刃插入程度
The idealposition for the installed filter is with the knife edge at the center of thegel track. In some cases, the knife edge contacts the metal edge of the geltrack; this may result in air bypass (a seal leak) in the immediate area. Spacersor guides may be used to position the filter properly.
已安装的过滤器的理想位置是刀刃刚好插入凝胶凹槽的中间。在某些情况下,刀刃接触凝胶凹槽的金属边缘——这可能导致附近区域的空气旁路(密封泄漏)。可以使用垫片或导轨以正确安装过滤器。
Degradation of Filter Gel Performance
过滤器凝胶性能退化
There have beenobservations in pharmaceutical applications in which the filter gel materialsappeared to have degraded into a flowable, viscous material rather than a firmgel. This behavior has been studied extensively in the industry and is theresult of several factors that contribute to this failure mode. This failure isprimarily due to thediffusion of unbounded gelcomponents migrating to the surface of the gel. Therefore this migration is adegradation of gel performance; technically it is not a degradation of thebonded gel polymer since the polymer bonds are not broken. The filtermanufacturers have each developed their own gel systems to reduce the risk ofthis mode of gel performance degradation, and it is advised to work with thefilter vendor to understand the appropriate gel system and filter design forthe specific application.
在制药应用中,有观察结果显示,过滤器凝胶材料会降解为可流动、粘稠的材料,而不是一种的固体凝胶。这种行为在业界得到了广泛的研究,是导致这种失败模式的几个因素的结果。这种失败主要是由于不受控的凝胶成分扩散到凝胶表面。因此,这种迁移是凝胶性能的退化;从技术上讲,它不是粘结凝胶聚合物的降解,因为聚合物键没有断裂。过滤器制造商都开发了自己的凝胶系统,以降低这种凝胶性能下降模式的风险,建议与过滤器供应商合作,了解适合特定应用的凝胶系统和过滤器设计。
It should also be noted that when gel materials in pharmaceuticalapplications are observed to lose or change color, this does not necessarilyequate to degradation in gel performance. Cleaning and sanitizing chemicalsoften used in pharmaceutical cleanrooms can discolor the gel by bleaching thecoloring agent in the gel, but do not usually break the bonded silicone polymers.
还应该注意的是,当制药应用中的凝胶材料被观察到失去或改变颜色时,并不一定等同于凝胶性能的降低。制药洁净室中常用的清洁和消毒化学品可以通过漂白凝胶中的着色剂使凝胶变色,但通常不会破坏粘合的硅胶聚合物。
Even though gel systems mightappear on first observation to be similar to one another, they can have otherproperties which make them very different when subjected to operatingconditions in the pharmaceutical industry. However, all gel systems need tomeet the required physical properties to perform the task of sealing the filterframe to the filter housing, such as adhesion and stiffness to allow the correctknife edge penetration and sealing.
尽管凝胶系统乍一看可能彼此相似,但在制药行业的操作条件下,它们可能有其他特性使它们非常不同。然而,所有凝胶系统都需要满足所需的物理性能,以执行密封过滤器框架到过滤器外壳的任务,如粘附力和刚度,以允许正确的刀口渗透和密封。
Identified factors that contribute to this modeof degradation of gel performance include the following:
导致这种凝胶性能退化的因素包括:
The amountof cross-linked (bonded) gel material should be optimized since it isdesirable to minimize the amount of polymer that is unbounded. This needs to bebalanced with the mechanical properties required for the gel to properly sealthe filter. Controlling the ratio of the components and the mixing operationduring manufacturing is critical to a properly cross-linked gel.
交联(键合)凝胶材料的数量应足够,以减少无键合聚合物的数量。这需要与凝胶适当密封过滤器所需的机械性能相平衡。在生产过程中,控制成分的比例和混合操作对正确的交联凝胶至关重要。
The molecularweight of the gel system is important. A higher molecular weight gel systemcomponent reduces the diffusion of unbounded polymer. A narrow distribution ofmolecular weight is most desired. This needs to also be balanced withproperties such as viscosity of starting components and final surface tack ofcured gel.
凝胶系统的分子量很重要。更高分子量的凝胶体系组分减少了无粘结聚合物的扩散。最需要的是分子量的窄分布。这还需要与诸如起始成分的粘度和固化凝胶的最终表面黏度等性能进行平衡。
As much as possible, minimize exposure of the gel to PAO and other nonvolatile oil-basedtest aerosols as excessive PAO may accelerate the rate of unbounded polymerdiffusion by swelling the gel and increasing free volume. Although the liquidtest aerosol will not break apart bonded polymer material, it does act as asolvent to increase the migration of unbounded polymer components. Testing atlow aerosol concentrations, good aerosol distribution, minimizing the amount oftime that the filter is subjected to the aerosol challenge, and alternativetest methods are steps that can be taken.
尽可能减少凝胶暴露于PAO和其他非挥发性油基测试气溶胶中,因为过量的PAO可能会使凝胶膨胀并增加自由体积来加速无黏结聚合物的扩散速度。虽然液体测试气溶胶不会分解粘结的聚合物材料,但它作为一种溶剂,增加了未粘结聚合物组分的迁移。建议在较低的气溶胶浓度、良好的气溶胶分布、尽量减少过滤器受气溶胶影响的时间以及其他测试方法下进行测试。
The gel components need to be manufactured andmixed under a rigid quality controlsystem. This needs to include strict control of the manufacturing andmixing environments, testing of all relevant chemical and physical propertiesof every batch of gel material including limiting any impurities.
凝胶成分需要在严格的质量控制体系下生产和混合。这需要包括对生产和混合环境的严格控制,对每批凝胶材料的所有相关化学和物理特性的测试,包括任何杂质限度。
Miter jointintegrity of the frame is critical for filter performance. It needs to contain anygel failure from leaking into thecleanroom. Use the correct sealing compounds at the miter joints to preventleakage at the joints.
过滤器框架的完整性是至关重要的过滤器性能。这包括任何凝胶失效导致泄漏到洁净室。在框架处使用正确的密封化合物以防止泄漏。
Silicone gels are moreresistant than urethane gels to oxidizing chemicals normally seen in thecleaning and sanitizing ofpharmaceutical cleanrooms, and thus are generally the preferred gel system.Oxidizing chemicals can attack the urethane gel and create a hardened surface.Semiconductor cleanrooms generally do not use these oxidizing chemicalsroutinely and urethane gels are common in those rooms. Silicone gels willgenerally not degrade in the presence of these oxidizing chemicals. However,there may be some specific applications, such as when acid or caustic chemicalsare present, that the silicone gels may be subject to hydrolysis (rather thanoxidation) and it may be possible that a urethane gel system might be apreferred system.
硅酮凝胶比聚氨酯凝胶更能抵抗通常在医药洁净室的清洁和消毒中看到的化学物质的氧化,因此通常首选硅酮凝胶系统。氧化性化学物质会攻击氨基甲酸乙酯凝胶,造成表面硬化。半导体无尘室一般不经常使用这些氧化性化学物质,在这些房间里普遍使用聚氨酯凝胶。硅凝胶通常不会在这些氧化性化学物质的存在下降解。然而,可能有一些特定的应用,如当酸性或腐蚀性化学品存在时,硅凝胶可能会水解(而不是氧化),此时,氨基甲酸酯凝胶系统可能是首选体系。
Gaskets
垫片
Filters may be mated to installation structuresusing gaskets to form a reliable pressure boundary seal and to avoid air bypassof the filter element. A variety of gasket materials is available includingneoprene, polyurethane, silicone sponge, etc. Gaskets may be applied manuallywith brushed-on adhesive or pressure sensitive adhesive. Gasketsections should be joined by a flexible adhesive. Alternatively, liquidgasket material can be directly applied in a continuous length along the filterperimeter and allowed to expand into foam and cure in place forming aone-piece, continuous gasket.
过滤器可以使用垫片与安装结构配合,以形成可靠的压力边界密封,并避免过滤器元件的空气旁路。可选用氯丁橡胶、聚氨酯、硅海绵等多种垫片材料。垫片可以手动涂上刷涂胶或压敏胶。垫片部分应该用柔性粘合剂连接。或者,液体垫片材料可以直接沿着过滤器周长使用,并允许膨胀成泡沫并固化,形成一个整体的,连续的垫圈。
Silicone Gel
硅凝胶
Silicone gel has been used toseal filters successfully for many years. It exhibits good qualities, servicelife, and resistance to oxidation. Care needs to be taken when selectingsilicone gels to anticipate the environment to which they will be exposed. Siliconegel should not be used where frequent or prolonged exposure to acids or basesis reasonably anticipated. Silicone gels are generally more resistant tooxidizing chemicals used for cleaning and sanitizing pharmaceutical cleanrooms(such as bleach, sterilant, phenolic cleaner/disinfectant) than are urethanegels.
硅胶已被成功地用于密封过滤器多年。它具有良好的质量、使用寿命和抗氧化性。在选择硅酮凝胶时,需要谨慎对待,以适应它们将暴露的环境。硅凝胶不应该使用在预计经常或长时间接触酸或碱的地方。硅酮凝胶通常比聚氨酯凝胶更能抵抗用于医药洁净室清洁和消毒的氧化化学物质(如漂白剂、灭菌剂、酚醛清洁剂/消毒剂)。
Urethane Gel
聚氨酯凝胶
Polyurethane gel materialsare commercially available and often used when low outgassing properties arerequired (such as in semiconductor cleanrooms), where silicone cannot betolerated, or where the use of silicone gel is known to be a problem. Polyurethanegel has proven to be a good alternative to silicone gel in some applications.Polyurethane gel does exhibit the formation of a thin surface skin over timeand may undergo surface oxidation or limited shallow stress crack formation (asit is exposed to PAO); however, these aging effects have been shown to notcompromise sealing of the filter over time. Aging of the gel may be acceleratedif the gel is exposed to high doses of vapors from oxidative cleaning agents.Urethane gels in general tend to be more resistant to degradation in applicationsin which acid or bases are present than are silicone gels. Filters with gelolder than about five years, or that show signs of gel aging, should bereplaced and not reinstalled if removed from the system.
聚氨酯凝胶材料可以从市场上买到,通常用于需要低排气性能的场合(如半导体无尘室),不能容忍硅胶,或使用硅凝胶存在问题。在一些应用中,聚氨酯凝胶已被证明是硅凝胶的良好替代品。随着时间的推移,聚氨酯凝胶确实会形成一个薄的表皮,可能会发生表面氧化或形成有限的浅应力裂纹(因暴露于PAO中);然而,这些老化效应已被证明不会随着时间的推移损害过滤器的密封。如果凝胶暴露在高剂量的氧化清洁剂蒸汽中,凝胶的老化可能会加速。
In summary, in order tominimize the risk of gel degradation in pharmaceutical applications, it isgenerally advised to select a silicone gel system with the followingcharacteristics:
综上所述,为了最大限度地降低凝胶在制药应用中的降解风险,一般建议选择具有以下特点的硅胶系统:
High molecular weight
高分子量
Lower percentage of unbounded gel components
低百分比的无粘结凝胶成分
Manufactured and mixed under a rigid quality control system, withproperly designed miter joints in the frame
在严格的质量控制系统下制造和混合,在框架中适当设计的人字接头
Exposure to a minimum amount of PAO during filter testing
在过滤器测试期间使暴露的PAO量最低
There may be specificapplications in which urethane gels might be appropriate. It is advised to workwith the filter vendor to select the most appropriate gel for the specificapplication.
在特定的应用中,聚氨酯凝胶可能是合适的。建议与过滤器供应商合作,为特定的应用选择最合适的凝胶。
Figure 8.1 illustrates the superior adhesionproperties of a silicone gel.
图8.1说明了硅胶优越的粘附性能
Figure 8.1: Example of the Superior Adhesion Properties of a SiliconeGel
图8.1:硅凝胶优越的粘附性能示例
Photo credit: Ronald Roberts, Bayer U.S.
Figure 8.2 shows an example of the liquificationof filter gel.
图8.2为过滤器凝胶液化的一个例子
Figure 8.2: Example of the Liquification of Filter Gel
图8.2过滤器凝胶液化的例子
Figure 8.3 illustrates urethane gel developing to ughening and cracking on the surface.
图8.3说明了聚氨酯凝胶增韧和开裂的表面。
Figure 8.3: Example of Urethane Gel Developing Toughening and Crackingon the Surface
图8.3 聚氨酯凝胶表面增韧开裂实例
Photo credit: Ronald Roberts, Bayer U.S.
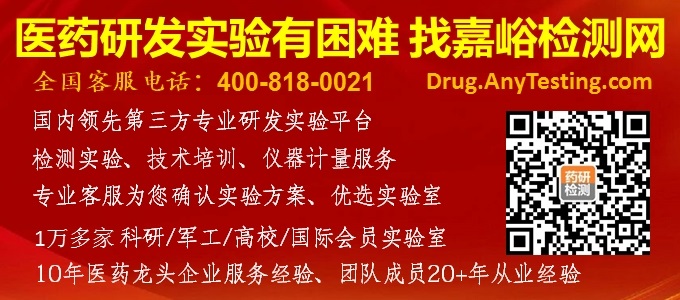