This is an example pharmaceutical development report illustrating how ANDA applicants can move toward implementation of Quality by Design (QbD). The purpose of the example is to illustrate the types of pharmaceutical development studies ANDA applicants may use as they implement QbD in their generic product development and to promote discussion on how OGD would use this information in review.
FDA官网中一个有关药物开发报告的实例,用以说明申请人如何实施质量源于设计(QbD)。 该实例的目的是说明ANDA申请人在其仿制药开发过程中实施QbD时,可使用的药物开发研究的类型,同时促进探讨OGD在审评中如何使用该信息。
本文主要概述了制剂的处方开发关键要点和一个处方开发案例。
2.3.4 Final Blending and Lubrication Process Development 最终混合和润滑工艺开发
Initial Risk Assessment of the Final Blending and Lubrication Process Variables 最终混合和润滑工艺变量的初始风险评估
The initial risk assessment of the overall manufacturing process presented in Table 32 identified the risk of the final blending and lubrication step to impact tablet dissolution as high. The lubrication process variables that could potentially impact tablet dissolution were identified and their associated risk was evaluated. Table 42 presents the initial risk assessment of the final blending and lubrication step.
表 32 呈现的整体生产工艺的初始风险评估确定了最终混合和润滑步骤为影响片剂溶出的高 风险。确定了可潜在影响片剂溶出的润滑工艺变量并评估了它们相关的风险。表 42 呈现了 最终混合和润滑步骤的初始风险评估。
Based on the results of Formulation Development Study #2, the extragranular magnesium stearate and talc levels were fixed to 0.6% and 2.9%, respectively. The composition of Generic Acetriptan Tablets, 20 mg, was shown previously in Table 29.
基于处方开发研究#2 的结果,外加硬脂酸镁和滑石粉浓度分别固定为 0.6%和 2.9%。仿制药 20 mg Acetriptan 片的组分如之前的表 29 所示。
Due to the low solubility of acetriptan, it is important to ensure that the blend is notover-lubricated, leading to retarded disintegration. NIR monitoring of the lubrication process isnot feasible due to the low amount of lubricant added; therefore, a traditional method with the blending endpoint based on lubrication time is needed
由于acetriptan的溶解度低,重要的是保证不过度润滑混合物,导致崩解延迟。NIR监测润滑 工艺是行不通的,由于加入的润滑剂数量少;因此,需要使用基于润滑时间的混合终点的传 统方法。
A study was performed to investigate the effect of magnesium stearate specific surface area and number of revolutions during lubrication on tablet hardness, disintegration, and dissolution. For this study, a 25.0 kg blend was manufactured in a pilot scale blender (150 L) using acetriptan Lot #2. The blend was roller compacted to give a ribbon relative density of 0.75. The ribbon was then milled and subdivided into five 5.0 kg batches. For each batch, the granules and talc were blended for 100 revolutions in a 16 qt V-blender at 20 rpm prior to lubrication with magnesium stearate. Then, magnesium stearate was added and blended according to the experimental design as shown in Table 43. After lubrication, samples were pulled from the 10 locations shown in Figure 23 to verify blend uniformity. The lubricated blend was then compressed using 10 kN of force to manufacture tablets. Ejection force was monitored. Compressed tablets were checked for appearance and the tablet press tooling (punches and dies) was evaluated for evidence of picking/sticking and binding. Additionally, tablets were subjected to friability, assay and content uniformity testing. Table 43 shows the lubrication parameters and results for each batch (not all data shown).
进行了一项研究以研究润滑中的硬脂酸镁比表面积和转数对片剂硬度,崩解和溶出的影响。 该研究,使用 acetriptan 批号 2 在中试规模混合机(150 L)中生产了 25.0 kg 混合物。碾压混合 物以产生带状物相对密度为 0.75。然后粉碎带状物,细分为各 5.0 kg 的 5 批。对于每批,在 与硬脂酸镁润滑前,在 20 rpm 转速的 16 qt V 型混合机中,颗粒与滑石粉混合 100 转数。 然后,根据如表 43 所示的实验设计加入硬脂酸镁并混合。润滑后,从如图 23 所示的 10 个 位置取样以验证混合均匀。然后使用 10 kN 力压缩润滑后的混合物来生产片剂。监测脱模力。 检查压制片的外观,评估压片机模具(冲头和冲模)粘冲和粘附的证据。此外,片剂进行脆碎 度,含量和含量均匀度检查。表 43 显示了每批的润滑参数和结果(未显示所有数据)。
The ejection force increased slightly with decreased lubrication time and lower specific surfacearea but did not exceed 150 N during the study. Tablet elegance was not an issue as allcompressed tablets had a smooth surface and lacked any visible striations on the sides of the tablet. There was no evidence of product sticking on the punches within the letters and numbers. There was also no evidence of binding to the die cavities.
当润滑时间减少和比表面积降低时,脱模力略微增加,但在研究中不超过150 N。片剂美观 度不是问题因为所有的压制片表面光滑,片剂两端无任何可见的条纹。在字母和数字范围内, 无产品粘冲的证据。也没有与模腔粘附的证据。
For each batch, the % RSD was less than 3% indicating that blend uniformity was acceptable following lubrication of the granules. Overall, the blend assay was between 98.3% and 101.7% for all samples pulled during the study. The tablet hardness observed was 9.0 ± 0.2 kP which is well within the target range of 8.0-10.0 kP. Tablets exhibited rapid disintegration (< 4 min) and dissolution (> 95% in 30 min). The results indicated that adequate lubrication of the granules was insensitive to both specific surface area (5.8-10.4 m2/g) and lubrication time (3-5 min) within the ranges studied.
对于每批,% RSD 低于 3%表明颗粒润滑后,混合物均匀度是合格的。总体而言,研究中取 样的所有样品的混合物含量为 98.3%~101.7%。观察到的片剂硬度为 9.0 ± 0.2 kP,位于目标 范围 8.0~10.0 kP 内。片剂显示出快速崩解(< 4 min)和溶出(> 95%,30 min)。结果表明润滑 适度的颗粒对研究范围内的比表面积(5.8~10.4 m2/g)和润滑时间(3~5 min)都不敏感。
Over the course of the study, friability did not exceed 0.2% w/w. Tablet assay was close to target and well within the acceptable range of 95.0-105.0% w/w. Tablet content uniformity was acceptable with a % RSD less than 4%.
在研究过程中,脆碎度不超过0.2% w/w。片剂含量接近于目标,处于合格范围95.0~105.0% w/w内。片剂含量均匀度合格,其% RSD低于4%。
Summary of Final Blending and Lubrication Process Development
最终混合和润滑工艺开发的总结
Within the ranges studied, magnesium stearate specific surface area (5.8-10.4 m2/g) and number of revolutions (60-100) did not have a significant impact on the drug product quality attributes studied.
在研究的范围内,硬脂酸镁比表面积(5.8~10.4 m2/g)和转数(60~100)对研究的制剂质量属性 无显著影响。
Updated Risk Assessment of the Final Blending and Lubrication Process Variables
更新的最终混合和润滑工艺变量的风险评估
Table 44 presents the risk reduction for the final blending and lubrication step as a result of the development studies. Only the process variables that were initially identified as high risk to the dissolution of the final drug product are shown.
表 44 呈现了由于开发研究,降低了最终混合和润滑步骤的风险。仅显示了初始确定为最终 制剂溶出高风险的工艺变量。
2.3.5 Tablet Compression Process Development
压片工艺开发
Initial Risk Assessment of the Tablet Compression Process Variables
压片工艺变量的初始风险评估
Based on the initial risk assessment of the overall manufacturing process shown in Table 32, the risk of the compression step to impact content uniformity and dissolution of the tablets was identified as high. Process variables that could potentially impact these two drug product CQAs were identified and their associated risk was evaluated. The results of the initial risk assessment of the compression process variables are summarized in Table 45.
基于整体生产工艺的初始风险评估,如表 32 所示,确定压缩步骤为影响片剂含量均匀度和 溶出的高风险。确定了可潜在影响这两个制剂 CQAs 的工艺变量并评估了它们的相关风险。 表 45 总结了压缩工艺变量的初始风险评估的结果。
The following experiments were undertaken to investigate the relationship between the input material attributes (i.e., ribbon relative density) and process parameters related to compression and the final drug product quality attributes. Three batches of final blend (Batch No. 53-55, 15.0 kg each, drug substance Lot #2) were manufactured in a 50 L blender for the compression studies. The ribbon relative density for these three batches was 0.68, 0.75 and 0.81, respectively. The roller compaction studies concluded that within this range, the necessary compression force will not exceed the maximum allowable tool tip pressure recommended by the manufacturer.
进行了如下实验以研究输入物料属性(即带状物相对密度)和与压缩相关的工艺参数及输出 制剂质量属性间的关系。使用压缩研究中的50 L混合机生产了3批最终混合物(批号53~55, 15.0 kg每批,原料药批号2)。这3批的带状物相对密度分别为0.68, 0.75和0.81。碾压研究推 断出在该范围内,必要的压缩力将不超过生产商推荐的容许的最大工具提示压力。
Effect of Feeder Frame Paddle Speed 传送架桨速的影响
A screening study to investigate the impact of the feeder frame paddle speed (8-20 rpm) on tablet quality attributes was conducted. Since the final blend flows well, changes in feeder frame paddle speed within the specified range had no impact on tablet weight variability or content uniformity. Tablet dissolution was also unaffected by changes in feeder speed, suggesting that over-lubrication due to the additional mixing is not a concern. This process variable was eliminated from further study.
为研究传送架桨速(8~20 rpm)对片剂质量属性的影响而进行了一项筛查研究。因为最终混合 物流动性好,在规定范围内改变传送架桨速不影响片重差异或含量均匀度。改变加料机速度 也不影响片剂溶出,表明由于额外混合的过量润滑不是问题。进一步研究排除了该工艺变量。
Effect of Main Compression Force, Press Speed and Ribbon Relative Density 主压缩力,压片机速度和带状物相对密度的影响
Compression force and press speed (which is related to dwell time) can affect numerous quality attributes including hardness, disintegration, dissolution, assay, content uniformity, friability, weight variability and appearance. The density of the ribbon following roller compaction may also impact the compressibility and compactability of the granules which would then impact tablet hardness and dissolution. Therefore, a 23 full factorial DOE with three center points was performed to understand the effects of these parameters on tablet quality attributes. Pre-compression force is important to reduce entrapped air that can impact the tablet integrity. However, based on previous experience with similar formulations compressed with similar tooling (ANDA 123456), the pre-compression force was fixed to 1 kN for this DOE. Table 46 presents the study design and acceptance criteria for the responses.
压缩力和压片机速度(与停顿时间相关)可影响许多质量属性包括硬度,崩解,溶出,含量, 含量均匀度,脆碎度,重量差异和外观。碾压后的带状物密度也可影响颗粒的压缩性和压实 性,然后影响片剂硬度和溶出。因此,进行了带 3 个中心点的 23 全因素 DOE 以了解这些参 数对片剂质量属性的影响。预压缩力降低可影响片剂完整性的包埋空气是重要的。但是,基 于用类似模具压制的类似处方(ANDA 123456)的先前经验,固定该 DOE 的预压缩力为 1 kN。 表 46 呈现了研究设计和响应的可接受标准。
The press was run at the speed of the specified DOE for at least five minutes prior to any sampling. Tablet samples were then pulled at the beginning, middle and end of each run (except for Batch No. 54c which was sampled every 20 min throughout the entire run). Similar responses were observed at each sample time point; therefore, Table 47 presents the results for the middle time point (responses Y1, Y3, Y4, Y5 and Y7 not shown).
压片机以规定的 DOE 速度运行至少 5 分钟后,进行取样。在每批片剂(批号 54c 除外,该批 每隔 20 分钟取样)的开始,中间和末端取样。样品的每个时间点观察到类似的响应;因此, 表 47 呈现了中间时间点的结果(响应 Y1, Y3, Y4, Y5 和 Y7 未显示)。
Significant factors for tablet hardness 片剂硬度的显著因素
Since center points were included in the study design, the significance of the curvature effect was tested using an adjusted model and was found to be not significant. Thus, center points were included for model fitting. As shown in the following half-normal plot (Figure 39), A (main compression force) was the dominating factor affecting tablet hardness followed by C (ribbon relative density). The remaining model terms had no significant impact because they came from the normally distributed population as pure error based on Shapiro-Wilk hypothesis test results.
因为中心点包括在研究设计中,所以使用校正模型检验了曲率效应的意义,发现无意义。因 此,中心点包括了模型拟合。如以下半正态图(图 39)所示,A (主压缩力)为影响片剂硬度的 主要因素,其次是 C (带状物相对密度)。剩余的模型项无显著影响因为基于 Shapiro-Wilk 假 设检验结果,它们来自于作为纯误差的正态分布群体。
Tablet hardness was directly related to main compression force and inversely related to ribbon relative density as shown in the contour plot below (Figure 40). Both the half-normal plot and the contour plot show that there was no interaction between these two factors.
片剂硬度直接与主压缩力相关,与带状物相对密度密切相关,如下面等高图(图40)所示。半 正态图和等高图都显示这两个因素间无交互作用。
A roller compacted ribbon that exhibits a relative density toward the upper end of the acceptable range (0.81) required a greater compression force to achieve the same hardness than ribbon with a relative density toward the lower end of the acceptable range (0.68). This is because the powder mixture loses some of its compressibility and compactability after roller compaction.
显示相对密度接近可接受范围上端(0.81)的碾压带状物比相对密度接近可接受范围下端(0.68) 的带状物,需要较大的压缩力以达到相同的硬度。这是因为粉末混合物在碾压后失去了其某 些压缩性和压实性。
The DOE results show that it is possible to adjust a process parameter to accommodate variability in a material attribute. In other words, the model can be used to determine the necessary compression force for a given ribbon relative density to ensure that the target tablet hardness is achieved.
DOE结果表明调整工艺参数以适应物料属性的变异性是可能的。换句话说,该模型可用于决 定给定带状物相对密度必要的压缩力以保证达到片剂目标硬度。
Significant factors for tablet friability 片剂脆碎度的显著因素
None of the factors had a significant effect on tablet friability. All of the batches showed friability less than 0.2% except for Batch No. 55c which had an average hardness of 4.2 kP and showed a higher weight loss of 0.6%. Therefore, the lower limit for tablet hardness was set to 5.0 kP. 无因素对片剂脆碎度有显著因素。所有批除批号55c外,都显示出脆碎度低于0.2%,批号55c 的平均硬度为4.2 kP并显示出较高的重量损失,为0.6%。因此,片剂硬度的下限设置为5.0 kP。
Significant factors for tablet weight variability and content uniformity 片重差异和含量均匀度的显著因素
The half-normal plot below (Figure 41) shows that press speed was the only factor that had a significant impact on content uniformity. The effect was a positive effect, meaning that the % RSD increased as press speed increased. This is also shown clearly in the main effect plot (Figure 42). The main effect plot demonstrates that no curvature was observed so further optimization of the press speed is unnecessary.
如下的半正态图(图 41)表明,压片机速度是显著影响含量均匀度的唯一因素。该作用为正作 用,意味着% RSD 随压片机速度增加而增加。这在主要作用图(图 42)中也得到清楚地显示。 主要作用图显示未观察到曲率,因此压片机速度无需进一步优化。
Although better content uniformity (i.e., lower % RSD) is achieved when the tablet press is operated at a slower speed, the press speed range investigated (20-60 rpm) did not result in out-of-specification tablet content uniformity. At 60 rpm, the % RSD observed was less than 4% and well below the limit of 5%.
虽然压片机以较慢速度运行时可得到较好的含量均匀度(即较低的% RSD),但是研究的压片 机速度范围(20~60 rpm)不会导致片剂含量均匀度超出质量标准。在60 rpm,观察到的% RSD 低于4%,低于限度5%。
Similarly, press speed had a statistically significant impact on tablet weight variability which increased with faster press speed. However, the individual tablet weight variability was well below 5% and the composite weight variability was well below 3%.
类似地,压片机速度对片重差异的影响具有统计学意义,随压片机速度增加而增加。但是, 单个片重差异低于 5%,综合片重差异低于 3%。
During production, it is desirable to maximize efficiency by setting the tablet press as fast as practically possible without adversely impacting the quality of the drug product. Based on the compression study, the proven acceptable range for press speed is 20-60 rpm.
生产中,通过尽可能设置与实际一样快的压片机速度而对片剂质量无不良影响来使效率最大 化是可行的。基于压缩研究,压片机速度已证明的可接受范围是20~60 rpm。
Significant factors for tablet disintegration and dissolution 片剂崩解和溶出的显著因素
The main compression force, press speed, and ribbon relative density did not have a significant impact on disintegration. The disintegration time was rapid and varied from 1.5 minutes to 3 minutes.
主压缩力,压片机速度和带状物相对密度对崩解无显著影响。崩解时间快速,从1.5分钟至3 分钟变化。
The following half-normal plot (Figure 43) shows that the significant factors affecting the dissolution rate of the compressed tablets were A (main compression force) and C (ribbon relative density). These two factors also showed a significant interaction, AC. The remaining model terms had no significant impact based on Shapiro-Wilk hypothesis test results.
如下的半正态图(图 43)表明,影响压制片溶出率的显著因素为 A (主压缩力)和 C (带状物相 对密度)。这两个因素也显示出显著的交互作用,AC。基于 Shapiro-Wilk 假设检验结果,剩 余模型项无显著影响。
Figure 44 illustrates the effect of main compression force and ribbon relative density on tablet dissolution. The curved contour lines show that an interaction exists because the dissolution results differed depending on the main compression force setting and the ribbon relative density. The dissolution rate decreased with increasing main compression force and increased with increasing ribbon relative density. These results are in line with the observed effect that these factors had on tablet hardness. Increasing the main compression force resulted in harder tablets and retarded dissolution even though rapid disintegration was still achieved by using 5% superdisintegrant. To avoid a potential dissolution failure, the upper limit for hardness is set to 13.0 kP since Batch No. 53c with a hardness of 13.6 kP showed dissolution of 83.8%.
图 44 说明了主压缩力和带状物相对密度对片剂溶出的影响。等高曲线表明存在交互作用, 因为溶出结果随主压缩力设置和带状物相对密度而不同。溶出率随主压缩力增加而减少,随 带状物相对密度增加而增加。这些结果与这些因素对片剂硬度观察到的影响一致。主压缩力 增加导致片剂硬度增加,溶出延迟,即使通过使用 5%超级崩解剂仍然达到了快速崩解。为 避免潜在的溶出不合格,硬度的上限设置为 13.0 kP 因为硬度为 13.6 kP 的批号 53c 显示出溶 出为 83.8%。
Effect of compression run time on tablet weight variability
压缩运行时间对片重差异的影响
Batch No. 54c was sampled every 20 minutes to evaluate the potential drift in tablet weight over the course of the compression run. The results demonstrated that the weight variability was well controlled for the individual tablets within ± 5% of the target weight and for the composite sample within ± 3% of the target weight. No trend for tablet weight was observed throughout the entire compression run. Tablet samples pulled at the beginning, middle, and end of the run were tested for all DOE responses and results are shown in Table 47. 批号54c每隔20分钟取样以评估压缩运行过程中,片重的潜在漂移。结果表明重量差异可控, 单个片剂在目标重量的± 5%内,综合样品在在目标重量的± 3%内。整个压缩运行中,未观 察到片重的趋势。检验了在运行开始,中间和末端取样的片剂样品的所有DOE响应,结果见表47。
Summary of other responses 其他响应的总结
Main compression force, press speed, and relative ribbon density had no significant impact on the remaining responses. Each run produced tablets that had a smooth surface with no evidence of picking/sticking or capping. Assay ranged from 99.1% to 101.0%.主压缩力,压片机速度和带状物相对密度对剩余响应无显著影响。每次运行生产出的片剂具 有光滑表面,无粘冲或顶裂迹象。含量范围为99.1%~101.0%。
Summary of Tablet Compression Process Development 压片工艺开发的总结
Within the range studied (8-20 rpm), feeder frame paddle speed did not impact the tablet dissolution. A press speed in the range of 20-60 rpm did not show any significant impact on the responses investigated. An acceptable range for compression force was identified. Force adjustments can be made to accommodate the acceptable variation in ribbon relative density (0.68-0.81) between batches.
在研究的范围内(8~20 rpm),传送架桨速不影响片剂溶出。压片机速度在20~60 rpm范围内 显示对研究的响应无任何显著影响。确定了压缩力的可接受范围。可调整压缩力以适应批间 带状物相对密度可接受的差异(0.68~0.81)。
Proposed Tablet Compression In-Process Controls 拟定的压片在线控制方法
Based on the results of the studies undertaken to understand the process variables affecting compression, Table 48 lists the proposed in-process controls for the compression step.
基于为理解影响压缩的工艺变量而进行的研究结果,表 48 列出了拟定压缩步骤的在线控制 方法。
Updated Risk Assessment of the Tablet Compression Process Variables
更新的压片工艺变量的风险评估
The risks identified during the initial assessment of the compression step were reduced through development studies. The updated risk assessment is presented in Table 49.
整个开发研究中降低了在压缩步骤初始评估期间确定的风险。更新的风险评估见表 49。
参考文献:
Example QbD IR Tablet Module 3 Quality 3.2.P.2 Pharmaceutical Development,FDA,2012.
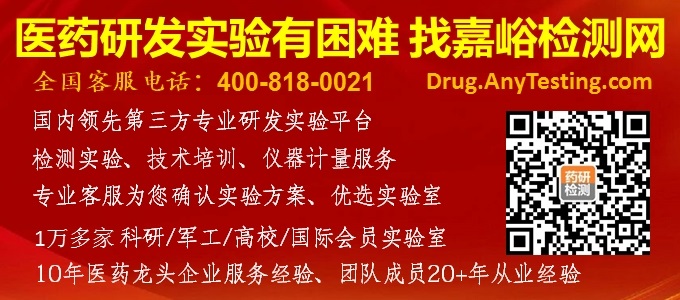