摘要:为了有效利用碳纤维复合材料的力学特性,采用碳纤维复合材料对某汽车控制臂进行了轻量化设计。首先建立了原钢质控制臂有限元模型,通过模态实验验证了其准确性,并对钢质控制臂进行了刚度分析和强度分析。然后基于钢质控制臂几何特征进行碳纤维复合材料控制臂几何重构,考虑其质量、振动特性、刚度、强度和工艺约束等,对碳纤维复合材料控制臂进行自由尺寸优化、尺寸优化和铺层次序优化,获得了最佳碳纤维复合材料铺层形状、厚度和铺层顺序。最后通过与原钢质控制臂性能对比可知,控制臂纵向刚度和侧向刚度分别增加了13.6%和1.4%,同时强度和振动特征均大幅提升,质量降低了63.7%,取得了显著的轻量化效果。
关键词:控制臂;碳纤维复合材料;尺寸优化;铺层次序优化;轻量化
汽车轻量化是节能减排的必然需求,也是汽车产业可持续发展的必经之路。碳纤维复合材料作为新型轻量化材料,具有密度小,比刚度、比模量大,可设计性强等特点,适用于电动汽车结构件的轻量化设计,引起了学者的广泛关注[1-3]。蒋荣超等[4]使用碳纤维复合材料对扭转梁悬架中的钢制横梁进行替换,并通过复合材料结构优化设计对横梁截面进行了改进设计,最终取得了显著的轻量化效果。HARTMANN等[5]将碳纤维复合材料应用于电池箱结构,以改善其振动和刚度性能。马芳武等[6]研究了碳纤维复合材料B柱,在保证其各项性能的前提下,减轻了B柱加强板的质量。LIU等[7]设计开发了复合材料结构的保险杠构件,以满足碰撞安全性和轻量化要求。综上所述,碳纤维复合材料应用车身构件较多,在底盘关键部件设计的应用还不够充分。
控制臂是汽车底盘的重要零部件,直接影响悬架系统的性能,关乎汽车的操稳性和舒适性。在控制臂轻量化设计过程中,保证其结构性能尤为重要,因此,国内外学者对碳纤维复合材料控制臂进行了相关研究。蒋荣超等[8]基于灰色关联分析进行了碳纤维复合材料控制臂铺层参数优化,实现减重的同时提高其控制臂结构性能。杨绍勇等[9]探究了基于铺层设计特性的复合材料承载结构件优化方法,并以控制臂为例进行其结构优化,通过与钢质结构相比较验证其方法的可行性。KIM等[10]基于微种群遗传算法探究了不同铺层顺序对碳纤维复合材料控制臂屈服性能和刚度性能的影响。刘越等[11]结合正交试验设计方法对基于等刚度原理设计的碳纤维复合材料控制臂进行了优化设计,与原钢质控制臂相比较,所设计的轻量化碳纤维复合材料控制臂满足其目标。
本文以控制臂为研究对象,综合考虑工艺和铺层设计要求,对碳纤维复合材料控制臂进行了自由尺寸优化、尺寸优化和铺层顺序优化,在保证性能目标的同时,得到最佳的控制臂结构设计方案,最后通过与原钢质控制臂各项性能对比分析,验证其轻量化设计的可行性。
1、 原钢质控制臂有限元分析
1.1 原钢质控制臂有限元模型
原钢质控制臂是由上、下连接板以及周边连接板和衬套焊接而成,利用球铰(外点)与转向节相连,通过衬套(前点和后点)连接在副车架上。将悬架控制臂经过几何简化、几何清理和抽取中面等,采用5 mm的2D单元进行网格划分。焊接部分采用共节点处理,与转向节和副车架连接点到控制臂本体之间采用RBE2刚性单元连接,最终有限元模型如图1所示。
图1 原钢质控制臂有限元模型
通过赋予其材料属性,对钢质控制臂有限元模型进行自由模态仿真,得到其固有频率。采用力锤激励方式进行模态试验,使用橡皮绳将其悬吊来模拟其自由边界条件,并在其上布置测试点以获取其几何轮廓,试验布置形式如图2所示。得到的固有频率仿真与试验结果如表1所示。通过对比可知,二者基本一致,模态振型基本吻合,说明所建立的有限元模型满足工程分析需要。
图2 原钢质控制臂自由模态试验布置图
表1 钢质控制臂自由模态仿真与试验结果对比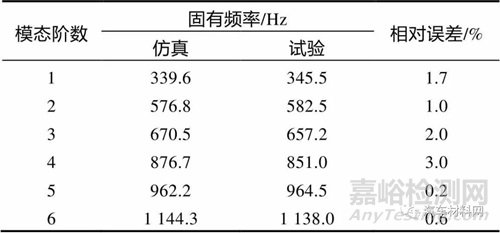
1.2 原钢质控制臂刚度分析
控制臂是连接车轮与车身的关键零部件,在汽车直线运动过程中主要承受纵向力,在转弯过程中主要承受侧向力,因此,其纵向刚度和侧向刚度可作为性能分析的评价指标。在对控制臂进行刚度分析时,添加约束条件如图3所示,约束类型设置为单点约束(Single Point Constraint, SPC),分别在控制臂外点施加沿X和Y方向1 000 N载荷,考察外点在两个方向的最大变形量,以计算其纵向刚度和侧向刚度,分析结果如表2所示。
图3 原钢质控制臂刚度分析边界条件
表2 钢质控制臂刚度分析结果
1.3 原钢质控制臂强度分析
汽车在行驶过程中,悬架控制臂相对于车身并非静止状态,而是绕着前、后点安装位置的连线上下摆动[12]。如果控制臂与车身安装点采用固定约束,约束点的反力会影响控制臂强度分析结果。为了有效解决该问题,采用惯性释放的方法对其进行强度分析。在进行惯性释放分析时,将控制臂的外点设置为“虚支座”,即约束该节点的全部自由度,约束类型设为SUPPORT1[13]。
悬架控制臂受力情况较为复杂,通过多体动力学仿真计算获取汽车在前加速、前制动、左转、右转等4种工况下的受力载荷,控制臂在不同工况下各连接点受力载荷如表3所示。
通过有限元强度分析可知,前制动工况下的最大应力为472 MPa,其应力分布如图4所示。其余三种工况最大应力远小于前制动工况,前加速工况和右转工况的最大应力均小于左转工况的最大应力。因而,在后续碳纤维复合材料控制臂优化分析时需特别注意前制动工况。
表3 钢质控制臂载荷条件 单位:N
图4 前制动工况下原控制臂应力云图
2、 碳纤维复合材料控制臂结构设计
由于原钢质焊接型控制臂组成结构较为复杂,同时考虑到碳纤维复合材料力学性能优异,将在保持原有安装方式和位置的基础上对其进行几何重构。首先以原控制臂结构外轮廓为边界构成封闭几何,然后创建U型截面单层板结构外形[14],几何重构过程如图5所示。
图5 控制臂几何重构过程
基于OptiStruct对重构的控制臂几何模型进行碳纤维复合材料结构优化,采用T300/环氧树脂复合材料,其基本性能如表4所示。依次经过自由尺寸优化、尺寸优化和铺层顺序优化获得最佳的碳纤维复合材料控制臂结构。
表4 碳纤维复合材料基本性能
2.1 自由尺寸优化
自由尺寸优化属于概念设计阶段,即将不同铺设角度视为不同的超级层,每一铺设角度的超级层系统默认均有4个叠加层组,从而实现超级层厚度可连续变化。超级层设为45°、-45°、0°、90°四种角度,通过Symmetric Smear方式模拟铺层形式,实现对称铺设且忽略铺层顺序对复合材料力学性能的影响。在自由尺寸优化阶段,还需要设置制造约束,例如每一铺设角度在总厚度中的百分比、层压板的总厚度等[15]。初步设定超级层总厚度为16 mm,即4个铺层角度的超级层厚度均为4 mm,自由尺寸优化问题具体设置如下:
1)设计变量:每个单元的超级层厚度;2)目标:纵向刚度和侧向刚度加权柔度最小;3)约束:一阶固有频率≥220 Hz;45°和-45°铺层形状和厚度保持一致;每一超级层铺设角度所占比例为10%~60%。
经过自由尺寸优化后得到各角度铺层最优形状,即不同铺设角度超级层厚度的分布,如图6-图8所示,其中铺层角度±45°的厚度分布云图相同。
图6 超级层角度0°的厚度分布
图7 铺层角度±45°的厚度分布
图8 铺层角度90°的厚度分布
2.2 尺寸优化
经过自由尺寸优化确定了控制臂各铺层角度的不规则厚度分布,每一铺层角度均由4种不同形状组成。为了确定不同铺层角度各铺层形状厚度,对各不同铺层角度的铺层厚度进行尺寸优化,具体设置如下:
1)设计变量:各铺层形状块的厚度;2)目标:质量最小;3)约束:一阶固有频率≥220 Hz;铺层角度为45°和-45°;层形状和厚度保持一致;可制造的每一铺层厚度为0.25 mm;纵向刚度>2 500 N.mm-1;侧向刚度>50 000 N.mm-1。
通过自由尺寸优化确定了最终总厚度为 15.5 mm,其中各铺层角度不同形状的铺层厚度结果如表5所示。
表5 各铺层角度不同形状的铺层厚度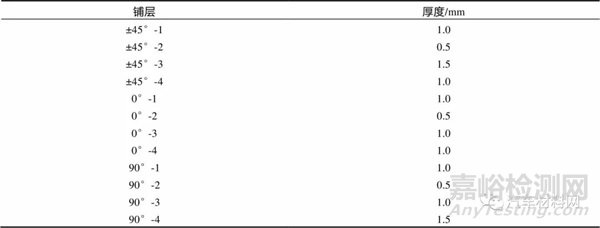
2.3 铺层顺序优化
碳纤维复合材料具有明显的各向异性,不同的铺层顺序对其性能影响不同,通过铺层顺序优化来提升控制臂的各项性能,根据尺寸优化结果进行铺层顺序优化,具体设置如下:
1)设计变量:各铺层形状块的厚度;2)目标:纵向刚度和侧向刚度加权柔度最小(刚度最大);3)约束:一阶固有频率≥220 Hz;铺层角度-45°和45°成对出现;同一铺层角度连续铺设不超过2层;强度各工况最大应力≤460 MPa。
最终确定碳纤维复合材料控制臂按照不同形状铺设的层合板表示为[(±45°/90°/0°)6/(±45°/90°)2]s,其中s表示对称。
3、 对比分析
通过自由尺寸优化、尺寸优化和铺层顺序优化获得了最佳的碳纤维复合材料控制臂结构,相比于最初钢结构控制质量3.75 kg降低到了1.36 kg,控制臂质量降低了63.7%,实现了汽车控制臂的轻量化设计。通过有限元分析获得四种工况下碳纤维复合材料控制臂的应力分布,其中前制动工况应力最大,如图9所示。可以看出,前制动工况最大应力值为162 MPa,相比于钢质控制臂强度得到大幅提升。
图9 前制动工况应力分布云图
设计优化后的碳纤维复合材料控制臂侧向刚度和纵向刚度位移分布如图10所示,外点X和Y方向位移分别为0.363 mm、0.013 26 mm,从而确定其纵向刚度和侧向刚度分别为2 755N.mm-1、 75 415 N.mm-1,相比原钢质控制臂纵向刚度和侧向刚度分别增加了13.6%和1.4%,可以看出侧向刚度基本不变。
图10 碳纤维复合材料控制臂刚度分析结果
图11 碳纤维复合材料控制臂一阶振型云图
此外,设计优化后的碳纤维复合材料控制臂固有频率较原钢质控制臂均有所提升,改善了其振动特性。其中,碳纤维复合材料控制臂一阶模态振型云图如图11所示,一阶固有频率为506.7 Hz,相比于原钢质控制臂提高了33%。
4、 结语
本文以原钢质控制臂为基础,进行了碳纤维复合材料控制臂的轻量化设计,并通过自由尺寸优化、尺寸优化和铺层顺序优化相结合的方法对碳纤维复合材料控制臂进行优化设计,得到了最佳的控制臂结构设计方案,最后通过与原钢质控制臂的各项性能结果进行对比分析,验证其轻量化设计的可行性。考虑到碳纤维复合材料优异的力学特性,对原钢质控制臂进行了结构简化,通过复合材料结构设计,使得控制臂质量相比于原钢质结构降低了63.7%。基于Optistruct的复合材料优化三部曲,获取了满足各项性能的碳纤维控制臂结构的铺层形状、铺层厚度和铺层顺序。通过性能对比分析,碳纤维复合材料控制臂的强度、刚度及振动特性均有显著提升,为汽车零部件轻量化设计提供了参考。
参考文献
[1] 卫原平,杨青,刘涛然,等.碳纤维复合材料控制臂的轻量化设计与验证[J].玻璃钢/复合材料,2019(9):74-78.
[2] 朱国华,成艾国,王振,等.电动车轻量化复合材料车身骨架多尺度分析[J].机械工程学报,2016,52(6): 145-152.
[3] 王国旺.复合材料电动汽车电池包轻量化设计研究[D].长春:吉林大学,2020.
[4] 蒋荣超,刘越,刘大维,等.扭转梁悬架碳纤维复合材料横梁结构优化[J].汽车工程,2020,42(2):264-269.
[5] HARTMANN M,ROSCHITZ M,KHALIL Z.EnhancedBattery Pack for Electric Vehicle:Noise Reduction and Increased Stiffness[J].Materials Science Forum,2013, 765:818-822.
[6] 马芳武,熊长丽,杨猛,等.碳纤维复合材料汽车B柱加强板的优化与性能分析[J].湖南大学学报(自然科学版),2019,46(8):36-44.
[7] LIU Z,LU J,ZHU P.Lightweight Design of Automo- tive Composite Bumper System Using Modified Particle Swarm Optimizer[J].Composite Structures,2016,140 (4):630-643.
[8] 蒋荣超,慈树坤,刘大维,等.基于灰色关联分析的碳纤维增强树脂复合材料控制臂铺层优化[J].复合材料学报,2022,39(1):390-398.
[9] 杨绍勇,雷飞,陈园.基于铺层设计特征的碳纤维增强复合材料悬架控制臂结构优化[J].工程设计学报, 2016,23(6):600-605.
[10] KIM D H,CHOI D H,KIM H S.Design Optimization of a Carbon Fiber Reinforced Composite Automotive Lower Arm[J].Composites Part B,2014,58(3):400-407.
[11] 刘越,蒋荣超,刘大维,等.碳纤维复合材料悬架控制臂轻量化设计研究[J].玻璃钢/复合材料,2019(8):47-52.
[12] 张志飞,陈仁,徐中明,等.面向多目标的汽车悬架控制臂拓扑优化研究[J].机械工程学报,2017,53(4):114- 121.
[13] 扶原放,金达锋,乔蔚炜.惯性释放原理在车架结构优化设计中的应用[J].机械设计与研究,2009,25(1):65- 67.
[14] 印立,徐中明,马媛媛,等.复合材料控制臂的多区域铺层结构优化[J].机械科学与技术,2021,40(2):305-312.
[15] 柴红普.复合材料层压板典型结构优化设计研究[D].上海:上海交通大学,2011.
来源:《汽车实用技术》
作者:解莹, 郭永奇, 何庆时, 邹锐(营口理工学院机械与动力工程学院)