摘要:表面处理技术既能保持基体材料的原本特征,又可以赋予产品表面各种新的性能要求,以提升产品表面的物理和机械性能。文章阐述了汽车零部件制造领域常用的机械加工零件、冲压件、铸造件、锻造件等不同工艺生产金属零部件适用的表面处理方法,分析电镀、抛丸、喷砂、喷丸、喷涂处理后零部件应选择的试验方案,为需要进行表面处理的汽车金属零部件开发验证提供了参考和依据,以确保表面处理的效果与质量。
关键词:汽车零部件;金属件;表面处理方法;划割试验
汽车制造行业零部件数量和种类繁多,金属零部件的占比大约为60%~70%,而其中大部分金属零部件都需要进行表面处理。通过表面处理,既能保持基体材料的原本特征和性能,又可以赋予零件表面新的性能要求,同时可以改变零件表面况状和性质,提升产品表面的物理和机械性能。目前,在汽车零部件制造领域应用较为广泛的表面处理技术可以分为两大类:一类是包含电镀、电泳、钝化等方法的化学处理方法;另一类是包括抛丸、喷砂、喷涂等方法的机械处理方法[1]。不同类型的表面处理技术与方法、作用与目的有差异,工艺过程也完全不同,因此,在汽车零件验证项目中编制的试验方案也不尽相同。如果试验方案制定的不合理或不完整,将会直接影响新零件开发项目的质量和进度。
1、 表面处理的作用
表面处理是在基体材料的表面上通过各种物理、化学等方法,形成一层与基体的机械、物理和化学性能不同的表层工艺方法。对金属零部件进行表面处理有以下几个主要目的:
1、装饰性
表面处理可使表面变得光亮,提高产品美观度。例如:汽车的车标、保险杠、门手柄、窗框、车轮毂等裸露在外的金属零部件都需要外观亮泽美观,镀铬、镀锌以后产品的美观度大大提高,更容易受到消费者的喜爱。
2、改变零件表面的性能
提高零件表面的耐腐蚀性能、耐磨性能、耐疲劳、抗氧化等方面的性能[2],例如:发动机中的活塞、活塞环、连杆等需要承受冲击负荷的运动部件。通过表面渗碳、渗氮处理可以提高零件表面的硬度、耐磨性和耐疲劳性能,而零件芯部依旧保持良好的塑性和韧性,而螺栓、螺钉、螺母、垫片等紧固件在加工之后通常会进行镀锌、镀镍、氧化发黑等表面处理,以提高产品的耐腐蚀性能和抗氧化性能。
3、改变零件表面的光洁度与平整度
铸造和锻造的毛坯件表面通常较为粗糙,可以通过抛丸、抛光等处理去除掉零件表面的毛刺、氧化皮、锈蚀等,从而提高零件表面的平整度。
4、改变表面的传热或隔热性能
针对需要传热或散热的一些零部件,可以用高导热的材料在零件表面进行填充处理,以提高零件的导热性能,或者通过使用隔热材料进行表面处理来提高零件隔热性能。
5、改善表面导电性或绝缘性
电气相关导电零部件或需要进行焊接的零部件,均要求具有良好的导电性能,可以通过添加铜、铝、银等电导率高的元素进行合金化或是在基体材料表面电镀一层电导率高的金属材料,从而提高零件的导电性。对于表面需要绝缘的金属材料,可以通过在表面喷涂绝缘漆,或是在表面粘附绝缘塑料薄膜、橡胶、树脂等绝缘材料来实现。
6、改善零件表面的附着力
对于后续需要进行喷涂、喷漆等作业的零部件,通常可以通过喷砂、磷化、电化学处理等表面处理方法,改善基层材料表面的平整度,进而提高涂层与基体材料之间的附着力。
2、 表面处理方法及试验方案
汽车常用金属零部件的加工工艺主要有机械加工、冲压、压铸、锻造、粉末冶金等,通过不同工艺加工出的金属零部件,其材料的物理与机械性能完全不同,零件表面处理的目的也不同,因此,所适用的表面处理方法不同,相应的零部件的验证试验方案也不同。汽车金属零部件最常用的表面处理方法有电镀、抛丸、喷砂、喷丸、喷涂等,具体分析如下:
2.1 电镀
电镀是将金属基材浸于含有镀层金属化合物的液态溶液中,当镀液通电以后,镀层金属析出并沉积在基体材料上的一种表面处理方法[3]。电镀是车身冲压覆盖件和螺栓、螺母、垫片等金属紧固件较为常用的一种表面处理方法,要求基材具备良好的导电性,以提高零件的防腐蚀能力和提高美观度。根据不同的目的,可以选用不同的镀层材料,如:镀锌、镀铬、镀铜、镀镍、镀锡等不同电镀材料各有优缺点,应根据使用目的和要求选择适用的类型,具体差异如表1所示。
其中镀锌在电镀中的占比可达40%~50%,是应用最为广泛的一种电镀方法。镀锌零件的防腐蚀能力和镀层厚度有直接关系[4],镀层厚度为5~8 μm时,通常零件的中性盐雾试验要求为48 h无白锈、72 h无红锈;镀层厚度为8~13 μm时,中性盐雾试验要求为72 h无白锈、120 h无红锈。镀锌时,在阴极析出金属的过程中还会有氢气析出,氢原子侵入基体材料会产生氢脆现象,氢脆的零件在后期使用过程中存在断裂的风险,可能会引起较为严重的事故,从而影响产品的安全性。尤其是强度大于10.9级的紧固件,在电镀后钝化前需要进行去氢处理,因此,还需依据《紧固件检验氢脆的方法》(GB/T 3098.17)进行氢脆试验,相关要求如表2所示。
表1 不同镀层材料电镀比较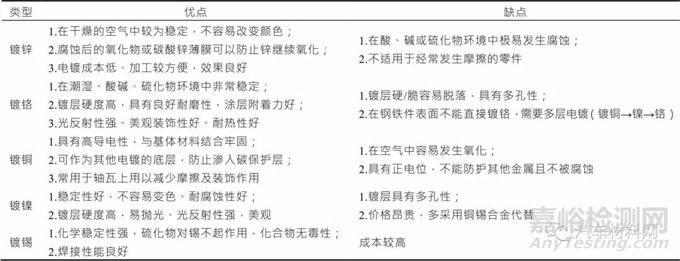
表2 镀锌紧固件盐雾试验要求
2.2 抛丸
抛丸是依靠离心力原理,通常用直径为0.2~3.0 mm的不同材质(不锈钢丸、铸钢丸等)弹丸抛向零件的表面,清除表面的油脂、污垢、氧化皮、腐蚀物、氧化物和其他杂质,去除零件机加工毛刺、消除零件内应力、减少热处理后零件变形、提高零件表面耐磨性能及承受压力的能力等[5]。不同于抛光让零件表面变得光滑,抛丸使工件表面变得更加粗糙,为后续的喷涂或喷漆工序提供良好的基层表面,不仅可以提高涂层与基体的附着力,而且还可以提高零件的寿命。
抛丸处理后的零件需要进行外观检查、清理等级测试、表面粗糙度测试、表面覆盖率测试等项目,如表3所示。首先需进行目视检查,确保零件表面无锈点、氧化皮、污垢等杂质,再根据抛丸后零件表面因清理不彻底而出现的阴影和色差面积比例,将质量等级划分为最彻底清理级、很彻底清理级、较彻底清理级、非彻底清理级四个级别。除此之外,还要检测零件表面的粗糙度数值和表面覆盖率(在抛丸工件表面的规定部位中的弹痕占据面积与要求抛丸面积之间的比值)。
表3 抛丸零部件试验方案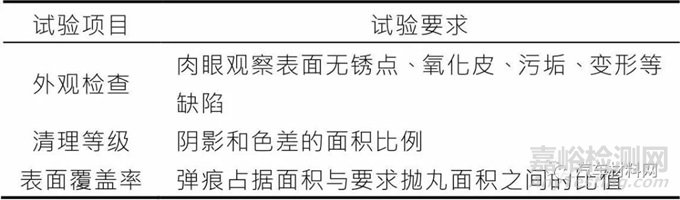
2.3 喷砂
喷砂是借助压缩空气形成的高速喷射束,将铁砂、金刚砂等砂料快速地喷射到零件表面上,清除表面的杂质,提高零件表面清洁度,从而改变表面的粗糙度。喷砂还可以改变零件的外表和形状以及表面的硬度、耐磨性等性能,提高零件表面的附着力。选用不同直径的喷砂材料可以得到不同的表面粗糙度数值。因为喷砂的清洁效果较好,所以当零件表面处理要求较高时,优先选择喷砂。
先要对采用喷砂处理的零件表面进行外观检查,尤其是确保那些不容易被喷到的角落部位没有漏喷。另外还要检测表面的清洁度,测量表面粗糙度,对基材表面进行清洁度和粗糙度检查时,要在良好的光照或照明条件下进行,避免因光照不良出现漏检。
2.4 喷丸
喷丸是以压缩空气为动力和摩擦力,用直径在0.2~2.5 mm的金属材质的弹丸,清除零件表面的氧化物、锈斑、污垢等物质的方法。铸造和锻造的零件表面,通常会粘有型砂、锈斑,以及暴露在空气中形成的氧化皮等物质,从而影响产品的外观、尺寸或性能,因此,喷丸是形状复杂的铸造或锻造毛坯最常采用的一种表面处理方法。与抛丸相比,喷丸以弹丸来冲击零件表面,即使采用了不同的喷射动力和方式,表面处理的效果也基本相同,因此,试验项目也基本相同。
2.5 喷涂
喷涂通常是以压缩空气为动力,利用喷枪把调配好的液态涂料变成均匀而微小的雾滴,喷射到被喷涂零件的表面的一种涂装方法。喷涂有空气喷涂和静电喷涂等不同的方式,静电喷涂涂料的利用率更高,但对零件的基体材料有导电的要求[6]。
喷涂处理的零件通常要检查外观,测量涂层厚度、涂层表面硬度,同时进行涂层附着力测试、耐腐蚀、耐环境测试等试验项目。喷涂件表面常见的缺陷主要有起粒、流挂、桔皮、泛白、起皱等,可以通过目测或与标准样件对比来进行检查。表面硬度测试多用铅笔测试,即采用不削尖利的灰度居中(Hardness Black, HB)铅笔,以一般手写力度与测试面成45°在喷涂面上划过,再用无尘布沾水擦拭干净后观察,确保表面只允许有轻微的划痕,不可划破或露底。
涂层的附着力测试通常参照《色漆和清漆-划格试验》(ISO 2409)的划割测试,在喷涂层表面用刀片划出行距和列距都为1 mm的方格(共为10行10列),刚好划破喷涂层,然后用3M胶纸贴实于划割的表面上,等待1 min后在45°方向快速撕开,根据喷涂层脱落的面积大小来确定附着力的等级级别,具体如表4所示。另外喷涂零件的主要作用还有提高零件表面耐气候、耐溶剂、耐摩擦等性能,因此,还需根据实际情况进行高低温交变环境测试、耐溶剂测试、耐摩擦测试等项目验证。
表4 划割试验结果分级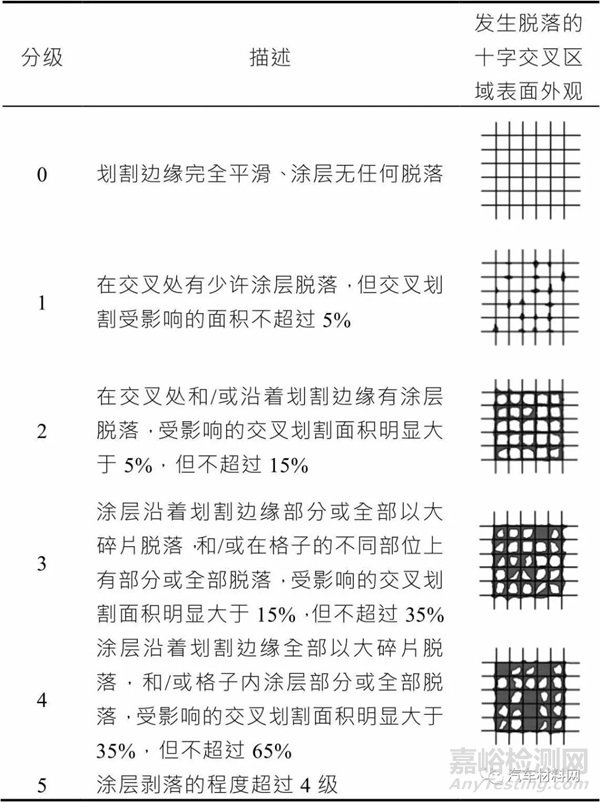
3、 结语
汽车金属零部件加工工艺和使用要求不同,可以选用的表面处理方法也不同,针对不同类型的表面处理方法,零部件开发验证时的试验方案也不同。只有制定出合理、准确和完整的试验方案,才能确保零部件表面处理的效果与质量,使表面处理零部件能够满足顾客的要求。汽车零部件的总成本占整车成本的60%~70%,对零部件及表面处理技术进行研究,降低零部件成本是各汽车零部件制造企业不断追求的目标,目前各企业不断加大对表面处理技术的研究与开发,使表面处理技术向着更加节能、环保、高效方面发展。
参考文献
[1] 刘永锋.机械工程材料的表面处理方法[J].煤炭技术, 2008,27(5):22-24.
[2] 张宇婷.表面处理技术的种类和发展[J].化工管理, 2019(31):4-5.
[3] 杨丁丁.表面处理技术在汽车覆盖件模具零件中的应用[J].模具工业,2019(5):63-65.
[4] 曲凤娇.汽车铝合金车身不同表面处理的腐蚀性能[J].有色金属加工,2021,50(4):52-54.
[5] 孙建波.钢基体表面处理技术的发展[J].热加工工艺, 2022(5):1-8.
[6] 董川东.论机械工程材料的表面处理方法[J].中国高新技术企业,2017(10):83-84.
作者:龚玉梅1, 张辉1, 苏元飞2, 徐慧1, 王鹏超1(1台州职业技术学院;2台州百思哲企业管理咨询有限公司)
来源:《汽车实用技术》