摘 要 铝合金整体副车架具有质量轻、结构强度高以及后续装配工序数少等特点。以某大型中空封闭截面结构铝合金后副车架为对象,设计了3种不同的低压铸造成形工艺方案,并采用AnyCasting软件进行了充型及凝固过程模拟。结果表明,在采用十字型进水的第3种成形工艺方案下铝合金熔体具有较好的充型能力及较优的凝固顺序。基于确定的成形工艺方案进行了铝合金后副车架样件试制,对关键部位进行了微观组织表征与力学性能测试。结果表明,铸件表面光洁平整,无流痕、欠铸等缺陷,内部组织致密,无缩孔、缩松缺陷;α-Al晶粒细小,二次枝晶臂平均间距为18 μm;取样部位抗拉强度为281 MPa,屈服强度为245 MPa,伸长率为5.52%,性能满足使用要求。
关键词 后副车架;铝合金;低压铸造;微观组织;力学性能
汽车行业的飞速发展促进了全球经济繁荣,同时也对资源环境产生了巨大的压力,节能减排已成为汽车工业可持续发展的重要方向。副车架是底盘系统质量占比最大的零件之一,对其进行轻量化设计意义重大。传统副车架多采用钢质材料,而使用铝合金副车架进行替代可以实现减重30%~40%,能大幅提高整车的动力与燃油经济性[1-4]。
当前铝合金副车架的成形工艺主要有铸造、挤压、锻造、铝管液压成形等[5],其中铸造是生产铝合金副车架的主要方式之一。与其他工艺相比,铸造能够生产形状结构相对复杂的零件,并且一次成形,生产效率高、加工工序少、成本也较低[6]。其中低压铸造优势明显,其充型过程更易于控制;铸造过程中压力更大,可以保证充型的完整性,并且在压力作用下凝固,能够使组织更加致密,保证铸件具有良好的力学性能。
本研究以某大型中空封闭截面结构铝合金后副车架为对象,设计了3种不同的低压铸造成形工艺方案,并对其进行仿真分析,选取优化方案进行试验验证,以期为低压铸造铝合金副车架的生产提供参考。
1、 低压铸造工艺方案设计
1.1 铸件分析
某汽车后副车架结构见图1,为中空封闭截面结构,轮廓尺寸为814.86 mm×1 134.6 mmm×356.5 mm,平均壁厚为4 mm,最小壁厚为0.4 mm,质量为21.6 kg,是一种高强韧的大型复杂薄壁零件。整体使用铝合金铸造,减重比达到33%。铸件外观要求:无明显的流痕与裂纹,表面不能有气泡;铸件力学性能要求:抗拉强度≥270 MPa,屈服强度≥220 MPa,伸长率≥5%,测试标准为DIN50125。此外,铸件上4个与车身相连的衬套孔处要进行X光检测,不允许有缩孔、气孔存在,执行标准为ASTM E155。
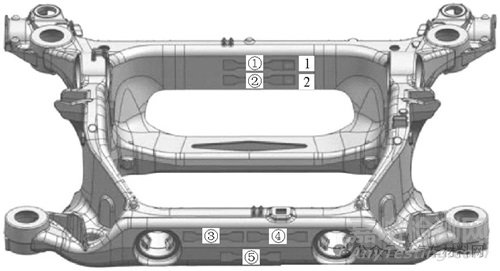
图1 铝合金后副车架及取样部位
Fig.1 Aluminum alloy rear subframe and the sampling position
1.2 试验材料
铸造铝合金中,Al-Si系合金有良好的流动性,铸造性能好,并且耐磨、耐腐蚀,常用于轮毂和副车架等汽车零部件的生产[7]。选择A356.0铝合金,其抗拉强度高,伸长率好,适合副车架生产,其化学成分见表1。
表1 A356.0铝合金的化学成分
Tab.1 Chemical composition of A356.0 aluminum alloy %
在铝合金后副车架本体上取样进行微观组织表征以及力学性能测试,取样部位见图1,浅灰色部位用于拉伸试验测试,将其从上至下依次编为①~⑤号。拉伸试样示意图见图2。1、2号部位用于微观组织检测,共取两个试样,每个试样测量5组数据以减少测量误差,要求二次枝晶臂平均间距小于25 μm。
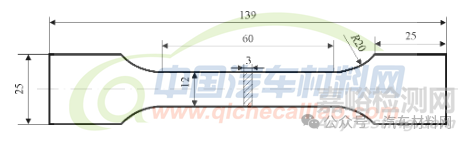
图2 拉伸试样尺寸示意图
Fig.2 Dimensions of the tensile specimen
1.3 工艺方案设计
该产品为中空结构且形状复杂,整个内腔只能用砂芯成形。为了提高生产效率与产品品质,整体使用金属型模具,分型面的选择和重力铸造一样。为了便于取出铸件与下放型芯,开型后铸件应留在包紧力较大的上型中。此外,分型面还要考虑浇注系统与排气孔的布置,综合考虑,将分型面开在投影面积最大的部位。
设计了3种浇注系统,见图3。方案1的充型方式与流道设计较简单,直接从4个衬套口注水,同时在中部大圆孔底部添加两处进水口。方案2在副车架上下两侧分别设有两个Y型浇口,并在中部横梁两侧加装小浇口,同时为了防止在衬套孔处出现缺陷,设置冒口进行补缩。方案3采用十字型进水,开有多个内浇道使铝液从副车架四周同时进入,上下两侧使用梳型流道平稳进水,左右两侧流道为横梁与圆孔底部供给铝液,同时在4个衬套口处加上冒口,在顶部多个薄壁位置处设置溢流槽。
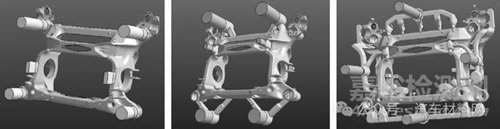
(a) 方案1 (b) 方案2 (c) 方案3
图3 副车架3种不同的浇注方案
Fig.3 Different pouring schemes for rear subframe
2、 模拟仿真分析
借助数值仿真技术对铸造工艺方案进行验证优化,可以得到产品充型与凝固顺序,推测发生缩孔、缩松的部位,优化浇注系统与生产工艺参数,为工艺设计提供参考,减少资源消耗,且提高开发合格率[8-12]。
2.1 模拟仿真前处理及参数设置
将后副车架网格大小大致划分为3 mm,其余部位自动过渡。在AnyCasting软件中设置后副车架材料为A356.0铝合金,模具材质为H13钢,砂芯选择覆膜砂。A356.0合金相关热物性参数见表2。
表2 A356.0铝合金的热物性参数
Tab.2 Thermophysical parameters of A356.0 aluminum alloy
3种浇注方案使用相同的初始、边界条件,设置上模初始温度为320 ℃,下模初始温度为350 ℃,侧模初始温度为400 ℃,砂芯初始温度为25 ℃,浇注温度定为710 ℃。低压铸造的浇注过程一般分为升液、充型、增压、保压、卸压5个阶段,为了提高铸件质量,将增压阶段细分为结壳段增压、结晶段增压,详细加压曲线见图4。其中,OA段为升液段,金属液沿升液管逐渐上升至型腔处,为了便于型腔内气体排出,此时金属液应平稳上升。AB段为充型段,金属液逐渐充满整个型腔,当金属液充满铸件型腔后,立即进行增压,使型腔内的合金液在一定压力的作用下凝固结晶,这个阶段被称为增压阶段,即BD段,又分为结壳增压段(BC)与结晶增压段(CD)。BC段的目的是使铸件表层在一定压力下先形成一层硬壳,保证后续过程不易出现黏砂现象。CD段金属液由液态转变为固态开始结晶,此时压力越大,补缩效果越好,故该段的增压速率较大。DE阶段为保压段,将最大压力维持一定时间,在此阶段中金属液逐渐凝固,EF为卸压阶段。
图4 低压铸造工艺加压曲线
Fig.4 Pressurization curve of the LPDC process
2.2 充型及凝固过程模拟
3种浇注方案下后副车架充型过程见图5。3种方案的充型过程中铝液温度均高于540 ℃,没有出现凝固现象。方案1与方案2在充型时最上层金属液的最低温度在液相线温度以上,流动性好,总充型时间分别为2.3 s与2.5 s。方案3因为流道、浇口较多,在充型率为95%时上层金属液温度已经接近液相线温度,但由于最后充型位置为冒口、溢流槽等,对于铸件本体的影响不大,总充型时间为2.6 s。方案1与方案2的充型顺序类似,受铸件本体形状与模具中摆放位置影响,铝液最先从中间部位的内浇道充型,而后底部两个浇口部位进水,充型率接近75%时,才有铝液从上部浇口进入。由于中间浇口位置不同,导致两种方案的充型过程有差异,方案1的中间浇口位置更接近下部浇口,铝液集中在型腔下部,在上部浇口充型时,上部型腔内铝液高度与浇口高度不匹配,会导致上部铝液汇流部位,即图5b中①号区域产生冲击,液流发生回旋,易产生气孔与氧化夹渣,影响成品质量,其最后充型位置在上部横梁与中部小孔位置。方案2的中间浇口开在中央横梁部位,在上部浇口开始充型时,横梁处铝液有一定高度,见图5e中②号区域,汇流冲击小,液流相对平稳,其最后充型位置在上部两支耳与衬套孔的冒口处。方案3充型液流最为平稳,因为其内浇道较多,上下侧使用梳型流道注水,共有10个内浇道。此外,左右两侧浇道分上下两部分,下部从中间横梁与大圆孔底部充型,上部通往支耳处,并设置许多溢流槽,使得铝液顶部冷污合金熔体进入溢流槽,从而有效避免在铸件内部形成夹渣、卷气等缺陷。
3种浇注方案下后副车架凝固过程见图6。3种方案的凝固过程类似,基本符合顺序凝固原则,都是从铸件上部的支耳以及3个横梁的中部开始冷却。这些位置远离浇口且壁厚较薄,最后凝固部位均位于4个衬套口与中央横梁的两侧以及下端横梁的圆孔处。此外,在整个凝固过程中,浇口的温度均在铝液固相线温度之上,具有一定的流动性,整个凝固过程中一直发挥着补缩作用。方案1的4个衬套孔与浇口直接相通,该处的补缩能力强,不易产生缺陷,但在中央横梁两侧与后部横梁圆孔部位极易出现孤立液相区,见图6d中①号区域,产生缩孔、缩松缺陷。对于方案2,虽然浇口不与衬套口直接相连,但在衬套口上部设置冒口,大圆孔顶部也设置溢流槽,能满足补缩需求。另外,由于中间浇口开在中央横梁的两侧,在铸件冷却凝固时,该处铝液受到一定压力,也不易产生缩孔、缩松缺陷,故此方案要优于方案1,但是在下部横梁的圆孔处由于没有采取补缩措施,仍然容易产生缺陷,见图6e中的②号部位。方案3针对上述问题对浇注系统进行了改进,不仅在衬套口上部设置冒口,同时在铸件顶部设置多个溢流槽,还在下端横梁圆孔处增加了冒口,因此其凝固顺序最好,得到的铸件品质也最高。
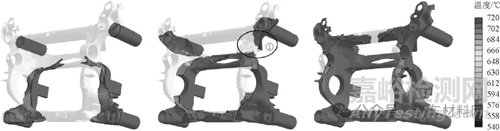
(a) 方案1,充型率50%(b) 方案1,充型率75%(c) 方案1,充型率95%
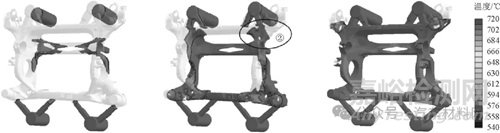
(d) 方案2,充型率50%(e) 方案2,充型率75%(f) 方案2,充型率95%
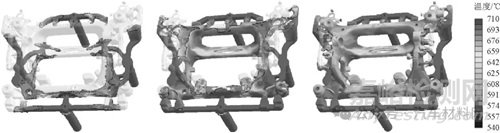
(g) 方案3,充型率50%(h) 方案3,充型率75%(i) 方案3,充型率95%
图5 模拟仿真得到的后副车架充型过程
Fig.5 Simulated filling process of the rear subframe
(a) 方案1,凝固25% (b) 方案2,凝固25% (c) 方案3,凝固25%
(d) 方案1,凝固50% (e) 方案2,凝固50% (f) 方案3,凝固50%
图6 模拟仿真得到的后副车架凝固过程
Fig.6 Simulated solidification process of the rear subframe
3、 样件试制及验证
3.1 内部品质及显微组织分析
由分析得出工艺方案3最优,因此选择此方案进行样件试制。控制铝液温度为700~720 ℃,在保温炉中通入氮气进行精炼,并加入Al-10Sr变质块进行变质处理,Sr含量控制在0.01%~0.02%,铝液密度为2.64~2.70 g/cm3。铸件经切冒口、震砂后进行535 ℃×6 h+200 ℃×6 h的T6热处理。热处理后的铸件以及衬套孔处X射线探伤结果见图7,可以看出铸件外观光滑平整,无流痕存在,也没有发生浇不足与冷隔等缺陷,表面光洁度和尺寸精度较高。X射线探伤结果也表明4个衬套孔处没有细小的裂纹存在,内部组织致密,无气孔、缩孔和缩松等缺陷,铸件的内部品质较高。
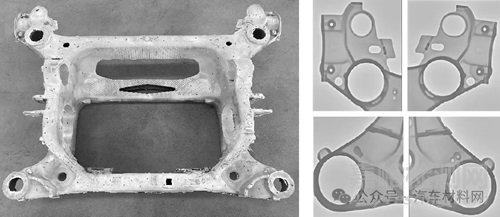
(a) A356.0铝合金后副车架实物图(b) 衬套孔处X射线探伤结果
图7 A356.0铝合金后副车架实物图与X射线探伤结果
Fig.7 A356.0 aluminum alloy rear subframe and X-ray
inspection results
按照图2中深色部位取样,经砂纸粗磨、精磨后使用W0.5金刚石抛光,用体积分数为0.4%的HF溶液腐蚀10 s后酒精清洗、吹干,在光学显微镜下观察试样的微观组织,结果见图8。可以看到,α-Al基体为白色树枝状枝晶,而呈现灰色团状分布的是Al-Si共晶组织,大部分分布在树枝晶晶界处,细小且均匀。α-Al二次枝晶臂平均间距为18 μm左右,枝晶间距较短。这是因为铝液在凝固时受到一定压力,与模具壁紧密贴合,冷却速度快,晶粒得到较好的细化[13-14]。
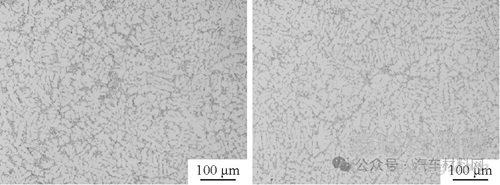
(a) 试样1 (b) 试样2
图8 测试部位金相组织
Fig.8 OM microstructure of sampling positions
3.2 力学性能分析
力学性能测试结果见表3。可以看出,5组数据的差异不大,表明后副车架力学性能较均匀,铸件抗拉强度为281 MPa,屈服强度为245 MPa,伸长率为5.52%,均达到后副车架力学性能要求。
表3 试样的力学性能
Tab.3 Mechanical properties of the specimens
4、 结 论
(1)设计了3种后副车架低压铸造工艺方案,并基于AnyCasting软件对其充型、凝固过程进行仿真,得出采用十字型进水的工艺方案3的设计更为合理,其浇注过程最为平稳,无明显的卷气与紊流,在易发生缺陷的薄壁部位都加装有冒口,铸件基本自上而下进行顺序凝固,有利于补缩,减少缩孔、缩松缺陷出现的概率。
(2)基于工艺方案3进行样件试制,结果表明低压铸造铝合金后副车架表面光洁平整,无流痕、浇不足与冷隔等缺陷,衬套孔等关键部位组织致密,无气孔、缩孔缩松缺陷,铸造内部品质较高。
(3)测试部位的取样分析得到α-Al二次枝晶臂平均间距约为18 μm,且综合力学性能优良,抗拉强度为281 MPa,屈服强度为245 MPa,伸长率为5.52%,低压铸造铝合金后副车架性能满足使用要求。
参 考 文 献
[1] 梁礼光. 轿车后副车架减重优化设计方法研究及应用[D].广州: 华南理工大学, 2014.
[2] 修坤,王成刚,马林,等. 轿车铝合金副车架铸件铸造工艺改进[J]. 铸造, 2017, 66(1): 75-77.
[3] 中国第一汽车股份有限公司.一种铝合金副车架的低压制备方法:中国, 201710099012.8[P]. 2017-07-07.
[4] 孙超. 铝合金副车架在电动汽车中应用的必然性[J]. 科学技术创新, 2018(11): 170-171.
[5] 陈来,王占坤,邹纯,等.汽车用铝合金副车架成形工艺及应用现状[J]. 铸造, 2019, 68(4): 390-395.
[6] 史东杰,张宇,王连波,等. 汽车铝合金副车架应用现状[J]. 轻合金加工技术, 2015, 43(8): 16-19.
[7] 代后山,董迎晖,袁鹤中. 低压铸造铝合金副车架的数值模拟及试验验证[J]. 特种铸造及有色合金, 2020, 40(3): 290-293.
[8] 王狂飞,王凯,王有超,等. 某缸体铝合金金属型低压铸造工艺研究[J]. 热加工工艺, 2012, 41(19): 43-44.
[9] 曲文君. 低压铸造铝合金轮毂(H0157)的优化设计[J]. 热加工工艺, 2012, 41(15): 59-60.
[10] 葛世超,梁艳,曲媛,等. 差压铸造在薄壁复杂铝合金铸件生产中的应用[J].热加工工艺, 2012, 41(1): 48-49.
[11] 张喆,洪润洲,周永江,等. 铝合金复杂管铸件树脂砂型真空吸铸工艺[J]. 热加工工艺, 2012, 41(21): 29-31.
[12] 向小汉. 车架纵梁成形模设计与制造[J]. 热加工工艺, 2013, 42(5): 113-116.
[13] 于顺阳.现代铸造设计与生产实用新工艺、新技术、新标准[M].北京:中国当代出版社, 2011.
[14] 童胜坤,尚淑珍,孙秀云,等. 低压铸造A356.2铝合金轮毂轮辐的性能[J]. 特种铸造及有色合金, 2012, 32(11): 1 030-1 033.
