1、 概述
质量风险管理(QRM)的概念最初应用于金融和保险行业,首次系统地推广并应用于制药行业,最早在2005年由国际协调委员会(ICH)发布的ICH Q9《质量风险管理》指南中[1]。QRM是保证产品质量的关键组成部分,风险控制是风险管理体系中的重要的环节,风险评估又是风险控制关键要素。通常风险评估过程需要使用各种统计工具。目前常用的风险评估工具有如下几种[2]:1)失效模式及效应分析(FMEA);2)风险排列和过滤(RRF);3)预先危害分析(PHA);4)危害分析和关键控制点(HACCP);5)故障树分析(FTA);6)其他类:包括流程图、图形分析、鱼骨图、检查列表等。其中,FMEA是较为经典和使用频次较高的风险评估工具,FMEA是一种前瞻性的评估方法,在高风险预防体系中被广泛使用。通过对过程深入理解和风险分析,通过风险评估并采取适当措施降低风险,属于“事前预防”而非“事后纠正”[3]。
在药品开发和生产过程中运用FMEA等质量风险管理方法,通过分析“风险因素”评估其失效模式的影响,针对高风险因素制定优化、改进、监控或变更等措施,实现影响产品质量风险和安全隐患的排查和消除,从而提高系统运转稳健性和效率。原料药作为药品的核心成分,直接影响药物的安全性和有效性,二者也是评价药品质量的终极指标。原料药企业推广使用FMEA等质量风险管理工具,并应用于工艺开发过程的管理,将有助于工艺的风险控制,保障能够持续生产出预期质量的产品,最终实现企业自身发展的的同时,也能够满足广大患者的临床需求。
2、 QRM流程与 FMEA实施策略
2.1 QRM流程
典型的质量风险管理流程包括5个程序[4],见图1。这其中的每一步都要通过沟通和协调来形成信息的交流,而整个过程离不开风险评估工具的应用。
图1 风险管理实施流程
2.2 FMEA实施策略
FMEA是 ICH Q9中推荐使用的风险管理工具。它以影响产品失效的“要素”为评估对象,通过预先分析评估对象的功能、形式和后果等方面,分析潜在失效的原因和严重程度,并计算风险优先数(RPN)。根据RPN和其他相关因素,评估风险并确定风险等级,然后采取相应的改进措施来降低或消除风险[5]。这样可以确保产品或流程的安全性和可靠性。参考风险管理的一般流程,制定FMEA的实施策略,见表1。
表1 FMEA的实施策略与说明
3、 FEMA应用分析
以安徽省阜阳市临泉县XX药厂的原料药A 的工艺为案例,该工艺在小试转中试放大过程中,出现了产品质量不稳定、收率波动范围大等系列问题。探索将FMEA工具应用到原料药 A 工艺开发中,以提高工艺稳健性,降低日后商业化大生产规模下可能出现的生产风险。
3.1 组织风险管理活动
在原料药A的工艺开发风险分析过程中,需成立一支由经验丰富的研发、工艺、设备、质量等相关技术或管理人员组成的工艺评估小组,明确小组成员各自的职责,并参与整个风险管理活动。
研究小组将依据历史研究数据、生产经验和科学知识,采用多种方法,如个别打分、集体讨论或交流协商的方式,对工艺进行评估,识别出潜在的质量和安全风险。
3.2 风险评估
将所有的可能会影响到产品质量的因素根据以往经验进行风险评估,例如处方变量、过程变量、仪器变量、环境因素、入的因素等研。FMEA方法可将风险量化,以RPN值评分。
3.2.1 评估准备
采取RPN计算分数评估原料药A工艺过程中各工序要素的风险等级,从三个维度 S、O、D 评估失效模式的影响效果,针对S、O、D进一步细化风险等级标准并赋分(可根据具体情况赋分,如10分、5分或3分),需明确细化评价内容、分值差异及其标准,工艺风险等级划分原则,见表2。
表2 工艺风险等级划分原则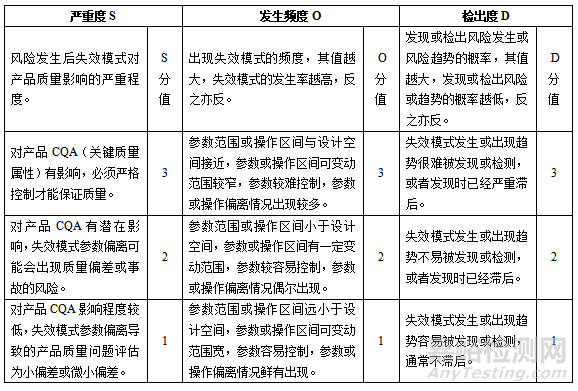
RPN计算公式为:RPN=S×O×D。RPN值越高代表该要素风险越高,实际在运用过程中,必须设定具体的经验阀值,并规定:当某一要素的RPN值超过阀值时,被认定为关键要素,反之,则为一般要素。以原料药A为例,设定RPN值≥8时,该参数/条件可被认定为关键工艺参数/条件,此时需采取措施以控制和预防风险发生,风险消减直至风险接受;RPN<8,则为一般工艺参数/条件,此时,无需采取特殊措施。风险分级表,见表3。
表3 风险分级表
3.2.2 风险确认
(1)工艺流程梳理
原料药A为例,生产工艺包括投料、碱解、还原、淬灭分相、浓缩、结晶、离心、真空干燥8个工序,其工艺流程简图,见图2:
图2 原料药A的工艺流程图
(2)工艺参数的初步分析确认
参考原料药A的工艺流程图、工艺规程等,工艺评估小组中专业人员分析识别工艺步骤中各工序中潜在的风险要素,影响产品质量和安全的所有要素均一一列出,形成一份汇总清单表,在此基础上,按照指定的风险划分原则赋分S、O、D值并计算RPN,并根据等级分级表(表3)评价其属性,在此基础上采取适当应对策略。
详细列出各工序的工艺操作或参数,综合历史数据、生产经验或科学知识,初步制定各步工序的参数可接受范围,基于此基础再假设参数超出范围后对产品质量和安全的影响,此阶段着重以严重度S为指标,初步分析工序中各工艺操作或参数失效的影响情况。工艺参数的初步分析筛查,见表4。
表4 工艺参数清单及初步评估表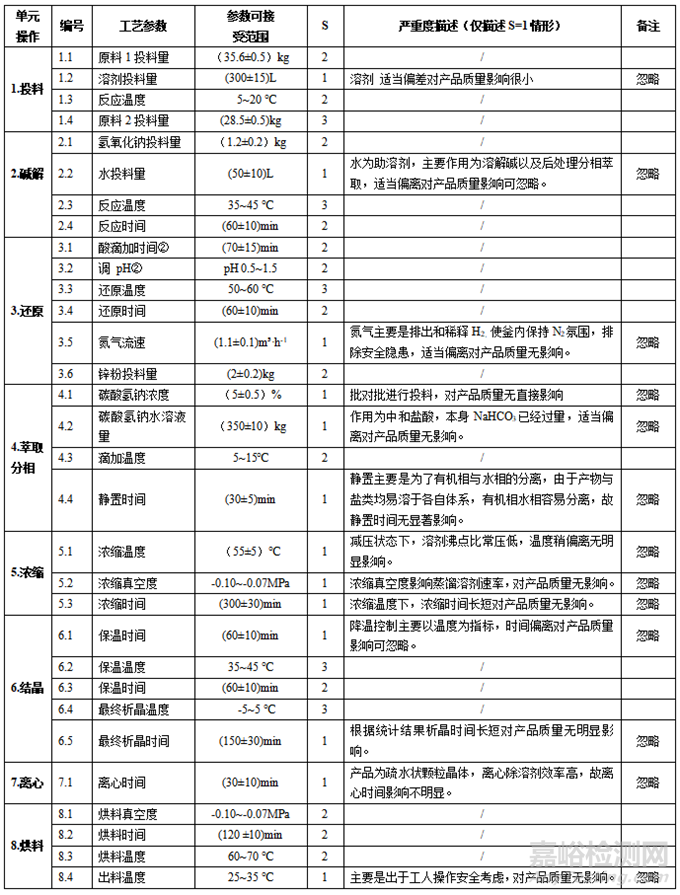
风险评价的一个重要内容就是确定风险相对较高的参数,为简化,我们忽略了表3中严重度 S值为1的工艺参数(原因已经在表3 “严重度描述”中给出了解释),也就是在接下来的风险评价中,只考虑严重度 S值为3,2的工艺参数。
3.3 风险分析和评价
经初步筛选后(不包括 S=1)得到的工艺参数纳入《工艺参数评估表》,分别描述各工艺参数 S、O和 D失效模式并赋分,计算出相应的 RPN值,参考表3中的分类原则,将工艺参数划分为关键工艺参数和非关键工艺参数。无论是关键工艺参数或非关键工艺参数在实际运行中,需根据其参数属性(关键或非关键)结合控制难度或容许偏差等依据,制定合理的“参数操作控制范围”。确定工艺参数的操作控制范围,见表5。
表5 工艺参数评估表
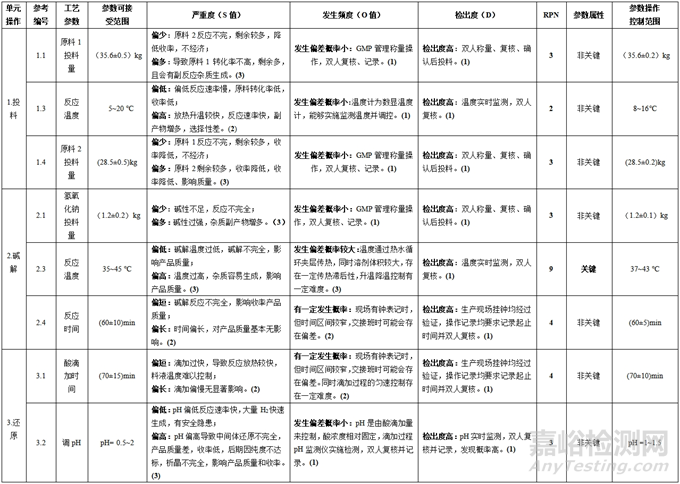
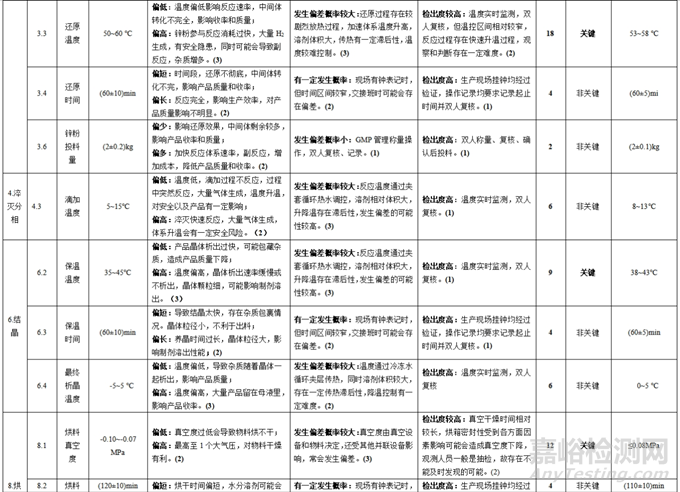

4、 风险控制
在确定生产工艺后,在注册申报及商业化生产之前,需在 GMP环境下对其进行工艺验证,以全面评估其生产条件(设备、环境、厂房等)及工艺是否符合商业化需求[6]。同时,为了确保生产的稳健性和产品质量的安全性,也需要对影响产品质量的的工艺条件/参数等进行全面的质量风险分析与评价,并对关键要素制定控制策略,以减少生产过程中的质量与安全风险。将表5中评估得出的关键工艺参数以及所采取的风险应对措施,见表6。
表6 关键工艺参数及控制策略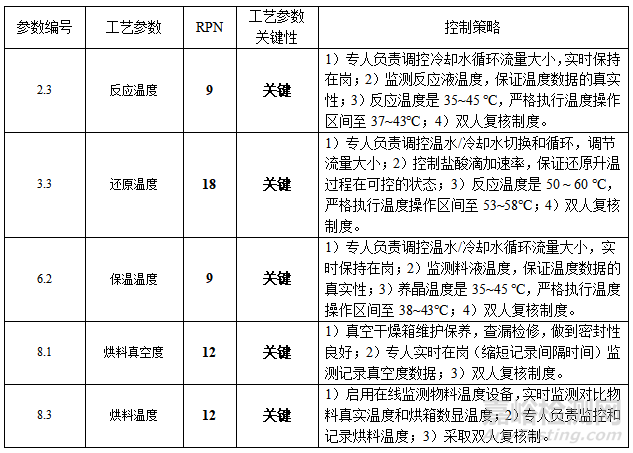
针对工艺参数评估得到关键工艺参数(高风险工艺参数),落实并执行针对高风险工艺参数的控制策略,再经过风险评估直至风险优先数RPN降至风险接受的水平,通过至少连续3个批次商业批规模的工艺验证,即说明工艺具备商业化大生产的可行性、可控性和合规性。
5、 风险回顾
工艺经过风险控制阶段的再验证,需对前期经过风险评估RPN值较高的关键工艺参数再次分析评估,对比前后差异,见表7。如果工艺改进/优化的关键参数经再验证实施后,经评估RPN值已降至风险接受,则证明建立的控制策略合理有效。风险控制采取的相关措施(变更、优化、监管等)作为技术成果文件保存记录,将是后续持续生产以及项目开发的重要借鉴和参考。
表7 关键工艺参数 RPN 再评估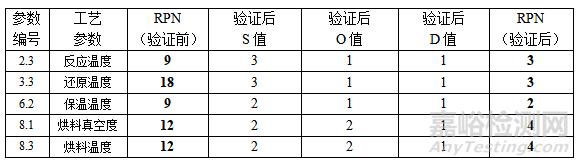
6、 结语
FMEA作为质量风险管理工具应用于原料药工艺开发过程,在工艺确认商业化生产前,即中试和工艺验证阶段,需要对工艺中的各种质量风险因素进行分析和识别,通过对可能存在的失效模式利用S、O、D三个维度评估其对产品质量和安全的潜在影响,计算出RPN数值,进一步评估确认关键的工艺参数,采取针对性的改进措施并再验证,将潜在的隐性风险化解和规避掉,风险降低直至风险接受。FMEA应用于原料药工艺开发,可以有效提高工艺的稳健性,减少或避免在日常商业化生产中可能出现风险事件的概率。
近年来,随着人们对FMEA方法认识的加深,原料药企业在工艺开发中还结合了诸如故障树分析(FTA)、偏差分析(DA)、根本原因分析(RCA)等风险分析工具,多种工具与FMEA的相互集成应用,不仅有助于进一步提高产品质量和工艺稳健性,还可以强化企业对质量管理的全面控制[7-8]。
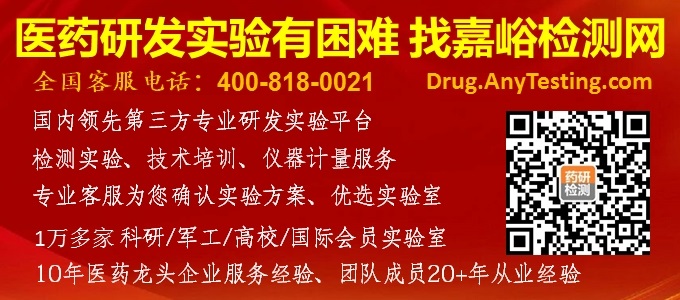