为了明确铝阳极与锌阳极在工艺水舱等特殊环境下谁更适合使用。依照NACE TM 0190中牺牲阳极的电化学测试方法,对比研究了Al-Zn-In-Si阳极与Zn-Al-Cd阳极在高温低氧的高盐度海水中的电化学性能。在55℃低氧海水中,随着溶液盐度升高,铝阳极的电位有所负移,电化学效率急剧下降,腐蚀形貌越发不均匀;锌阳极的电位变化情况近似铝阳极,但电化学效率变化不大,且腐蚀形貌比较均匀。在特殊环境下,从电化学性能来看,锌阳极更适用。并且,不同盐度的溶液中,锌阳极与铝阳极的电位接近,不存在电位极性反转的情况。
引言
在海洋工程、船舶工程和石油加工业等领域的蓬勃发展中,技术的创新和工程的拓展不仅带来了机遇,也带来了特殊环境下的挑战。这些环境包括高温、低溶氧、高盐度等极端条件,这对金属结构和设备的耐腐蚀性能提出了更高的要求。特别是在热交换器、海底热输油管线、原油贮罐等工作场合,由于经常处于高温、高盐的环境下,常规阳极的电化学性能表现出明显的恶化,这严重限制了牺牲阳极在特殊环境中的可靠应用。
铝合金阳极因其驱动电位适中、大电容量和高电流效率等特点,在海洋工程领域,尤其是海上油气田建设中,得到了广泛的应用。然而,某些高温环境下,如生产水舱、原油储罐底层等,铝阳极的表现却不尽如人意。在这些特殊环境中,阳极表面易发生钝化现象,形成坚硬的腐蚀产物,从而不仅加剧了局部腐蚀的问题,还导致了电流效率的下降以及使用寿命的缩短。这一现象不仅让金属设施的阴极保护设计变得更加复杂,也强调了对阳极材料性能优化的迫切需求。
相对于铝合金阳极,锌合金阳极密度大、电化学容量低、经济性差,限制了其在海洋环境中的广泛应用。然而,在压载舱、潮差区等某些特殊环境,依然能看到锌阳极的身影。普遍认为,高温条件下,锌阳极的工作电位正移,甚至会出现阴阳极逆转,从而加速金属的腐蚀。同时,随着温度的升高,锌合金阳极易诱发晶间腐蚀,导致电流效率降低,减少阳极寿命。
为了应对高温环境下牺牲阳极所面临的诸多问题,有必要深入研究不同类型的阳极材料在特殊环境下的电化学性能,以寻找最佳的阴极保护方案。本文通过比较分析铝阳极(Al-Zn-In-Si)和锌阳极(Zn-Al-Cd)在高温高盐低氧环境中的电化学性能,评估这两种类型的阳极在极端环境中的适用性。
试验-电化学性能测试
1、试样制备
从每个待测阳极上切取25 × 25 × 25 mm立方体样品。使用25号钻头在立方体一个面中心钻一个13 mm深的孔,并用10-24号丝锥螺纹。攻丝后的样品浸入除油清洗液中浸泡5min,随后用蒸馏水洗净擦干。试样在浓硝酸(HNO3)中短暂浸渍,去除表面的黑色残留物,随后用蒸馏水冲洗,用丙酮擦拭试样表明,在121 ± 11℃下烘干15min。烘干后的样品放在干燥皿中冷却至室温,并在分析天平上称重。在称重样品后,用涂层掩盖多余的表面区域,涂层在试验后可以很容易地除去。铜电量计的阴极铜片在干燥皿中冷却,并在分析天平上称重。试样制备完成后进行拍照,记录试样的原始形貌。安装导电棒,并在导电棒上标记阳极试样编号,阳极试样与导电杆连接的地方,用绝缘材料密封。
2、试验装置
仪器设各:恒流源、铜电量计、饱和甘汞参比电极、电流表、电子天平、电压表、多参数水质分析仪、辅助阳极(不锈钢圆筒,面积=400cm2)、生化培养箱。
溶液:乙醇、清洗液(每升水含20克铬酐和30ml磷酸的溶液)、人造溶液(成分如表1所示)。
表1 溶液配置参数(每升水含量)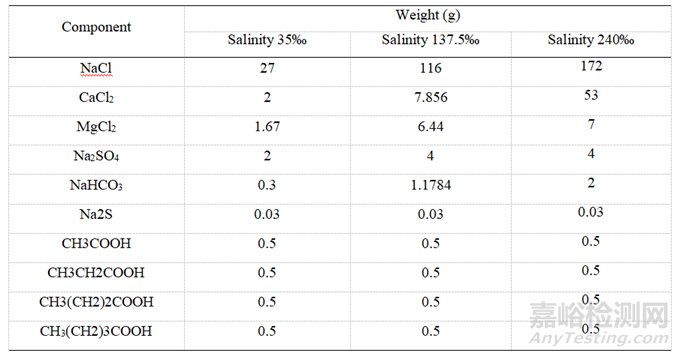
3、试验步骤
依照NACE-TM0190中牺牲阳极的电化学测试方法。将牺牲阳极试样及测试设备如图1进行安装,同一成份的1个试样串联连接。辅助阴极采用不锈钢圆筒,内外均为工作面,辅助阴极固定在离底面10 mm以上的位置,阳极试样悬吊在阴极环的中心部位。安装铜电量计阴极,使阴极在两个阳极中间,不接触两个阳极。用多参数水质测量仪测量溶液的盐度并记录,将溶液倒入容器,放入生化培养箱。当溶液温度达到55℃后,向溶液中通入氮气,至溶解氧低于0.1 mg/L后关闭氮气,将阳极试样放入溶液中,密封容器上盖,生化培养箱放置低亚硫酸钠用于除去箱内的氧。阳极试样浸入介质环境中3h后测量阳极的开路电位。将试验装置用导线连接,电流方向为牺牲阳极进,阴极出。检查整个回路的电流方向是否正确。调整电流为22.3 ± 0.2 mA,用毫安表测量,换算成试样表面的电流密度为0.62 mA/cm2,确认无误后接通电源。试验过程中保持电流恒定,每天使用饱和甘汞参比电极测量阳极工作电位。该试验法试验周期为336h。试验结束后,去除试样表面的密封胶,将铜电量计的阴极铜片取下,用蒸馏水清洗干净。将阳极样品浸入82 ± 6 ℃的清洗液中10min,去除腐蚀产物。将处理后的阳极试样和铜电量计的阴极铜片按要求烘烤、称重。拍照、记录阳极试样清洗腐蚀产物后的照片。
图1 牺牲阳极电化学测试连接方式
结果与讨论
1、铝阳极测试结果
如表2所示,铝阳极样品由电感耦合等离子光谱测定其成份,活性物及杂质含量符合要求。通过实测成份计算阳极的实际理论电容量,结果如表3所示。
表2 铝阳极成份
表3铝阳极实际理论电容量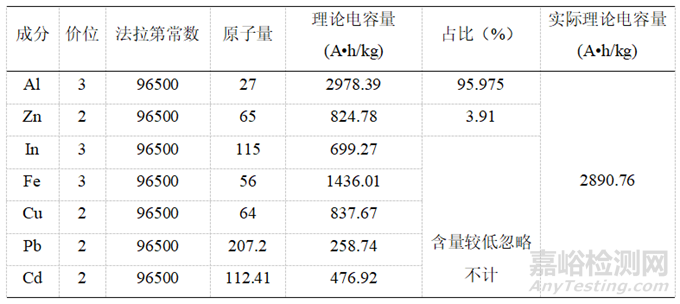
经过14天的强制电流电解,各溶液环境下的阳极失重结果如表4所示,根据铜电量计的重量变化,计算出阳极的实际电容量。阳极试样的实际电容量按下式计算:
式中:
Q—牺牲阳极试样的实际电容量,A•h/kg;
k—系数,1mol铜的电容量K=843.3 A•h/kg
M1、M2—试验前、后铜电量计阴极铜片重量,g;
m1、m2—试验前、后阳极试样重量,g。
电化学效率由实际电容量除以上表中的理论电容量算得。
表4 铝阳极实际电容量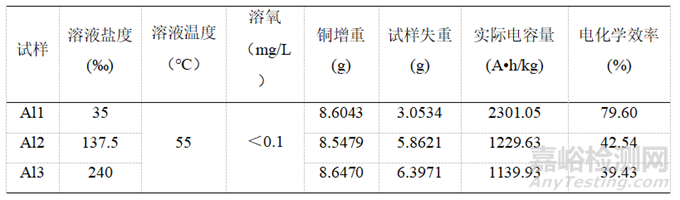
测试过程中依据标准要求,测试阳极试样在22.3mA恒流电解下的电极电位,结果如图2所示。其中,横坐标0处代表阳极的开路电位。
图2 铝阳极在55℃下不同盐度的海水中工作电位-时间曲线
测试结束后,按照标准程序对样品进行清洗、烘干,去除表面腐蚀产物后的形貌如图3所示。
图3 铝阳极在55℃下不同盐度海水腐蚀后的形貌
2、锌阳极测试结果
同样,锌阳极样品由电感耦合等离子光谱测定其成份(表5),活性物及杂质含量符合要求,通过实测成份计算阳极的实际理论电容量(表6)。
表5 锌阳极成分
表6 锌阳极实际理论电容量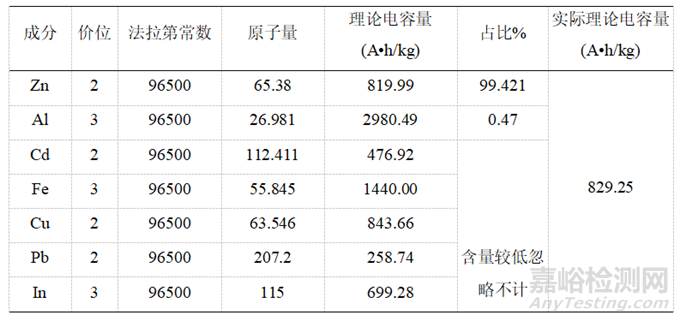
同铝阳极计算过程一样,由阳极失重及电量计增重计算的阳极实际电容量和电化学效率如表7所示。
表7 锌阳极实际电容量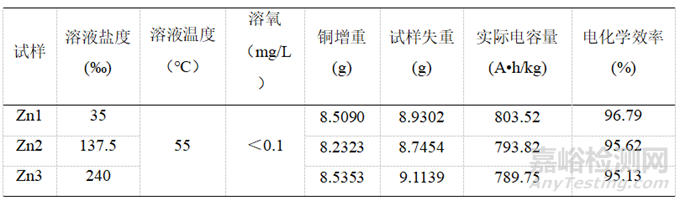
阳极试样在22.3mA恒流电解过程中的电极电位以及开路电位结果如图4所示。
图4 锌阳极在55℃下不同盐度海水中工作电位-时间曲线
测试结束后,按照标准程序对样品进行清洗、烘干,去除表面腐蚀产物后的形貌如图5所示。
图5 锌阳极在55℃下不同盐度海水腐蚀后的形貌
3、讨论
锌是最早用来做阴极保护的牺牲阳极材料,但由于锌阳极密度大、电化学容量较低、驱动电压较低,经济性上不如铝阳极。因此,现在海洋工程上多用铝阳极。此外,锌阳极为低合金化,改造空间不多。而且普遍认为,55℃以上,锌阳极的电位会正移并超过碳钢的电位,造成极性逆转,因此锌阳极一般用于50℃以下的环境。这就导致工程应用上对锌阳极的研究非常少。
目前工程应用的锌阳极,绝大多数为Zn-Al基,在此基础上添加Mg、Cd等元素。本文中的锌阳极为工程上常见的Zn-Al-Cd阳极,铝阳极也是普遍使用的Al-Zn-In-Si阳极。常温海水中,两种阳极的开路电位和工作电位有0.05~0.1 V的差值,铝阳极较负。在55℃低氧条件下的三种盐度溶液中,锌阳极与铝阳极的开路电位均比较接近,工作电位依然是铝阳极较负,但最大差值未超过0.1 V。测试中并未发现锌阳极极性逆转的现象,而且锌阳极与铝阳极的电位差异不大。
对比图2和图4可以看出,高温低氧环境下,随着溶液盐度增加,铝阳极和锌阳极的开路电位和工作电位均逐渐降低。由于两种金属表面均自然形成氧化物的钝化膜,氯离子浓度越大,诱发点蚀的机率越大,表面钝化膜的破损点也就越多。相应的电极电位下降,表现出来金属的活性增加。相比较,锌阳极的开路电位与工作电位相差较大,在相同的阳极电流密度下,锌阳极的去极化能力不如铝阳极,这与锌失电子的能力和数量有关。
从电容量和电化学效率的测试结果来看,铝阳极随着环境盐度增加,电容量和电化学效率急剧下降,这也与图3的表面形貌相契合。众所周知,高温环境下,铝阳极会加剧晶间腐蚀,电容量和效率较常温环境有所降低。而溶液盐度对铝阳极的电化学性能的影响同样明显。晶间腐蚀是由于晶界与晶内的在环境中的活性不同,形成了微观原电池,晶界溶解后造成晶粒脱落。一般氯离子浓度较高的溶液会首先诱发铝合金的孔蚀,从而促使晶间腐蚀的发生。对比锌阳极在三种盐度下的测量结果,电容量和效率的差别不大,随着盐度增加,仅有轻微的下降趋势,对应图5的表面形貌,也是只能看出有轻微的不均匀腐蚀倾向。在高温低氧的高盐度海水中,锌阳极的电化学性能表现稳定,与标准中常温环境中的电容量差别不大。这说明环境因素,并未诱发锌阳极的晶间腐蚀,即晶界与晶内的活性相近。造成这种明显差异的原因较多,可能与锌阳极的低合金化、杂质对晶体影响较小、锌的阳极反应活性较低等均有或多或少的关系。
从工程应用的角度出发,首先我们关心的锌阳极不适宜55℃以上的海水环境的观点,在测试中却并未发现锌阳极极性逆转的现象。高温环境下,铝阳极与锌阳极的工作电位都会正移,并且电位正移的幅度相近。从测试结果来看,锌阳极也可用于55℃以上的海水环境,但驱动电压会进一步降低,且略低于铝阳极。从电容量和腐蚀形貌来看,高温低氧高盐环境(如油田生产水、海水冷却水、海水淡化余液等)中,使用锌阳极进行阴极保护更加安全。虽然从经济性考虑,即使锌阳极的电化学效率超过90%,其电容量也不及同环境下的铝阳极,但铝阳极的晶间腐蚀严重,实际应用中,其电容量存在较大的不确定性,可能同批次的产品,两两之间的电容量会有较大差别,阴极保护设计阶段难以准确计算阳极用量,必须适当增加阳极的富余量。而锌阳极由于腐蚀较均匀,电容量变化小,设计阶段可以准确估算阳极用量。
值得注意的是,在55℃、3.5%盐度溶液中,锌阳极的驱动电位约0.2 V(以阴极保护电位-0.8 V计算),如保护裸钢,驱动电位稍显不足,特别是裸钢表面不易形成钙镁沉积层,变相增加阳极消耗。在高流速溶液中,驱动电位可能进一步降低。此外,其他研究中发现,随海水温度升高,碳钢的自腐蚀电位随之负移。某些环境中,可能存在锌阳极欠保护的风险,这种风险也可能发生在铝阳极身上。因此,在高温、低氧等特殊环境中,需要单独测试阴极、阳极的电化学参数,选用适合的阳极。或者采用涂层联合阴极保护的方法,减少欠保护的风险。
结论
1)本文中的铝阳极(Al-Zn-In-Si)在高温低氧环境中,随着盐度升高,电化学容量和电化学效率显著降低,这可归因于高盐(高氯离子)环境,更易诱发和加剧铝阳极的晶间腐蚀。
2)相较于铝阳极,锌阳极(Zn-Al-Cd)在不同盐度的高温低氧海水中,电容量和电化学效率变化较小,未出现极性逆转现象,表现出更稳定的性能,使其成为在特殊条件下的可行选择。
3)尽管锌阳极在测试中未出现极性逆转,但在某些特定条件下,如高流速溶液或温度变化,仍需关注其驱动电位是否足够。在工程应用中,需要考虑涂层联合阴极保护等策略,以减少欠保护风险。
引用本文:
陈亚林,黄卫国,盛家程,隋普升.高温低氧环境下铝、锌阳极在高盐度海水中的性能研究[J].环境技术,2023,41(10):76-81+89.
