在药厂的GMP认证中,如何优化药品生产环境通常被作为一项重要指标来进行考察。从制药车间的布局设计、空气净化设计以及耐腐蚀处理三个角度探讨了如何优化制药车间生产环境的技术问题。
1、引言
制药车间,特别是原料药车间,按照工业分类和工程领域的划分,属于化工车间。从本质上说,制药车间的根本任务和其他各类化工车间是一样的,就是完成物质的转化过程。而这种物质的转化过程,按照化学工程术语,通常称之为化工过程。这些化工过程一般由多步化学反应组成,其生产步骤有其特定的流程顺序,过程有繁有简;其生产原料,基本上是酸、碱、有机化工原料及有机溶媒。因此,随着初始原料转化为具有各种使用价值的药品制剂,还需要同时优化制药车间的生产环境,从而保证药品制剂的质量。
在药厂的GMP认证中,药品生产环境的优化处理方案通常被作为一项重要的指标来进行考察。众所周知,做好硬件设施管理是实施药厂GMP管理的基本条件,而制药车间的GMP则是基本条件的基础条件,GMP制药车间这个特殊生产环境的各种环保指标,诸如空气、湿度、无尘、墙地面的耐腐蚀性等问题的处理是否科学,是车间和制剂室是否达到GMP整体效果的重要因素。现就GMP制药车间生产环境的优化提出几点浅见,与大家交流。
GMP对制药车间的区域布局类型有两种划分指标:一种区域划分指标是将制药车间的区域布局分为一般生产区、控制区和洁净区。一般生产区属非洁净区,控制区是指洁净度低于10万级的区域,洁净区是洁净度在万级或百万级以上的区域,这一区域布局划分指标是根据药品质量要求以及药品质量受生产流程影响的密切程度确定的。对药品质量有直接影响的生产流程段,洁净度要求就高,应确定为洁净区;而间接影响药品质量的生产流程段,洁净度要求低,应确定为一般生产区。故可将这一指标称为洁净度划分指标。
另一指标要求制药车间区域划分要严格实现人流与物流分开,也就是要有明确的人流通道和物流通道,可将这一指标称为通道划分指标。
制药车间的布局设计应该同时满足上述两种区域划分指标的要求。为与洁净度划分指标确定的3个区域相配套,制药车间布局相应地区分出人流通道、物流通道和工艺走廊。此外,当非洁净区的人和物进入到控制区或洁净区时,应对人和物做除尘处理,从而提升人和物的洁净等级,即物要去除外包装(属于除尘处理);人要换鞋更衣(也可看作除尘处理)。由于提升人和物洁净等级的方法不同,必须将人流与物流分开。经过净化的人和物,达到与控制区或洁净区相同的洁净度,就可以在工艺走廊“合二为一”了。设计者在设计制药车间的平面图时,在技术上要充分体现出其严格的区域划分思路和有效的洁净措施设计思路。笔者以为,在设计规模较小、岗位较多的制药车间布局时,首先要确定出人流、物流通道。因为道路一通,样样皆通,通道布置得合理,区域布局就有序。其次再辅以严格的洁净措施和区域过渡设施以有效提升人和物的洁净等级。总之,制药车间必须实现优化合理的车间布局设计,才能保证药品生产达到GMP的整体效果。
制药车间的空气洁净程度要达到GMP的指标,可以通过两种措施来实现。
一是在设计中要合理确定进、排风布局方案,从而有效控制制药车间的压差与回风。设计者要实现和维持制药车间洁净的空气环境,必须设计出相应措施保证车间内维持洁净的动态风流,并通过调节进风量与排风量的大小来调整室内压力。设计者在设计制药车间进、排风布局时,有三种排风方案可供考虑:一是车间的风排到走廊并在走廊进行集中回风,这种排风方案缺点是走廊易发生交叉污染;二是车间和走廊分别设计各自的回风系统,但车间的压差大于走廊,这种方案仍然不能避免走廊发生交叉污染;三是车间和走廊分别设计各自的回风系统,但车间的压差小于走廊,这是值得推广的一种技术方案,因为这种方案实现了车间内粉尘原地回风排走,有效避免了在走廊出现交叉污染。
二是设计有效的除尘系统。设计者不仅要在宏观上控制好制药车间的压差与回风,还要针对局部产尘设备设计有效的除尘系统,即在局部产尘设备前设计围挡装置,并利用吸尘罩集中处理含尘空气。设计者在设计固体制药车间的空气净化方案时,更应考虑这一点,因为固体制药车间洁净区内的气流是乱流,粉尘可以扩散到任何地方。
在除尘后的空气的处理方式上,设计者可以考虑以下四种方案:
(1)除尘后的空气经过过滤器过滤再送回房间,并在远离尘源的地方回风(图1)。
出尘设备停止工作时除尘系统也可停止工作。优点是系统方式灵活,节能效果显著;缺点是风机费用较高,运行维护复杂。此种方式适合产尘量大的系统。
图1 排风回收系统示意图
(2)除尘后的空气直接排至室外后不进行回收(图2)。
除尘设备与出尘设备同时停止工作,此时可调节回风口,增加回风量,保证房间处于一个正常的压力状态。优点是系统简单;缺点是不节能。这种方式适合于产尘量小的设备。
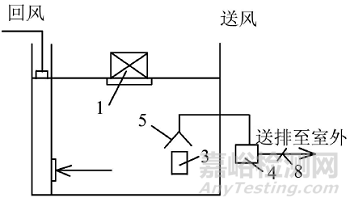

图2 分散排风系统示意图
(3)除尘后的空气由集中的排风系统排出室外,利用产尘点与百叶风口之间的吸尘罩和管道直接收集粉尘(图3)。
优点是可避免因除尘机组积尘而产生风量波动和室内压力值的波动,使系统保持稳定的风量平衡;缺点是不节能,需要较大的新风量。
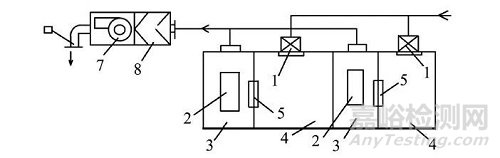

图3 集中全排排风系统示意图
(4)除尘后的空气由集中排风系统排向室外,利用转轮式换热器回收排风产生的热量(图4)。
优点是非常节能,能量回收率高达70%-90%;缺点是系统初始投资大,占用建筑面积和空间多,压力损失也大,无法完全避免交叉污染。
图4 能量回收原理排风示意图
4、制药车间构配件及设备耐腐蚀性要符合GMP标准
合成药物生产中使用各类酸、碱及其它具有腐蚀性的介质等化工原料,腐蚀是另一个突出的问题。制药车间的腐蚀包括对厂房构配件的腐蚀和设备腐蚀。
因此,不仅要选择具有耐蚀特点的设备材质以避免设备腐蚀;制药厂房的各种构配件(基础、墙、柱、楼地板)及其表面也要具有极强的耐蚀性。如果采用一般水泥混凝土,由于水泥中的某些组分与腐蚀介质(特别是液体性介质)在一定条件下易发生化学反应而解体,丧失原有的力学强度,破坏建筑构件,危及建筑物的安全。
作为工业厂房的制药车间,无论是单层厂房,还是多层或混合层数厂房[1],易受到介质腐蚀的构配件一般包括外墙、抗风柱、地面等围护构件[2]以及基础和基础梁等承重构件[2]。对于上述经常接触腐蚀性介质的厂房构件,可以从以下几个方面加强耐腐蚀性:独立柱基础(或杯形基础)采用防腐混凝土浇筑,条形砖基础表面涂刷沥青耐酸漆;梁、柱可以采用防腐混凝土浇注。近年来国内外运用高分子材料的某些特性,或者使用抗蚀性聚合混凝土,浇注成树脂整体无缝楼地层,该种材料中的抗腐蚀因子的抗腐蚀性稳定,应作为大力发展和推行的一项建筑抗腐蚀新技术。
不仅主要的结构构件要做好环保技术处理外,接触高腐蚀性介质的制药厂房在地面、墙面的装修上也要处理好耐蚀的技术问题。下面推荐一种制药厂房室内楼地面的装修施工工艺设计。
4.1室内地面
素土夯实找坡→C15混凝土垫层(120mm)→1∶2水泥砂浆找平(20mm)→环氧玻璃钢(二底二布)隔离层→5mm环氧胶泥结合层(当基层上有玻璃钢隔离层时,宜涂刷一遍与衬砌用树脂相同的胶料,然后进行块材的铺砌)[3]→30mm耐酸砖面层(2~3mm环氧胶泥挤缝)。(图5)
图5 耐酸砖地面做法大样
4.2室内楼面及设备基础平面
25mm细石砼找平层→环氧玻璃钢(二底二布)隔离层→5mm环氧胶泥结合层(当基层上有玻璃钢隔离层时,宜涂刷一遍与衬砌用树脂相同的胶料,然后进行块材的铺砌)[3]→30mm耐酸砖面层(2~3mm环氧胶泥挤缝)。(图6)
图6 耐酸砖楼面做法大样
如果制剂车间在内墙面的装修上需要考虑耐腐蚀的技术问题,则可以考虑如下的技术措施:采用HS-923型水溶性环氧树脂做底层,RC-5抗裂性防腐蚀涂料做面层。其施工工艺为:表面处理→涂水溶性环氧树脂第一道→涂水溶性环氧树脂第二道→涂RC-5抗裂性防腐蚀涂料。
5、注重制药车间设计的整体环保效果
GMP的核心思想是强调药品质量取决于药品生产过程,而任何一个环节都会影响药品质量。因此,优化制药车间生产环境的设计必须坚持系统论的观点,应当注重布局、空气净化、耐腐蚀性、厂房设备、人员素质等多个因素的优化组合,以求达到最佳的整体效果。
参考文献
[1] 孙玉红.房屋建筑构造[M ].北京:机械工业出版社2008.
[2] 郑贵超赵庆双.建筑构造与识图[M ].北京:北京大学出版社2009.
[3] 中国石油和化学工业协会.GB50212-2002建筑防腐蚀工程施工及验收规范[M ].北京:中国计划出版社2002.