一、序言
前段时间公司安排,把《确认与验证》附录给做个培训。
这个培训说起来简单,但是在3个多小时里面把这些事情说清楚却是很难,当然了,读读条款也用不了2个小时 。后来想,是不是画画关系图,来对某些关系复杂的验证进行说明是不是要容易一些?有了这个想法,那就画吧。
1.1 同步验证的一些说明
先来弄清楚几个概念。我刚开始工作,接触工艺验证的时候,就经常在验证方案看到“同步验证”,领导说这个就是和正常生产同步进行的验证。可是在这次附录出来以后,“同步验证”进行了单列,于是就仔细读了读,发现定义的同步验证和最初的同步验证的概念已经不一样了。先来看看,法规是怎么说的:“极个别情况(因药物短缺可能增加患者健康风险;因产品的市场需求量极小而无法连续进行验证批次的生产)”,这里的关键词应该是“极个别情况”,这个极个别情况也就是括弧里面的那两个条件了,而不再是和正常生产同步这个概念了。
1.2 验证的分类原则及分类
1.2.1 分类原则
其实从98版GMP实施的时候经常听说的验证有:前验证、同步验证、再验证、变更后验证,在10版GMP实施的时候,听说了回顾性验证,还亲自动手编了一个,在确认与验证附录出来以后又有了:首次验证、持续工艺确认、和改了性质的同步验证,没有回顾性验证,但有回顾审核。这样一来,现在存在的和工艺有关的验证就有:前验证、首次验证、变更后验证、再验证、持续性工艺确认、同步验证。
1.2.2 验证的分类
根据各个验证出现的时期,将他们进行了一个简单的分类
工艺开发阶段:前验证
商业化生产初始阶段:首次验证
商业化生产阶段:变更后验证、再验证、持续工艺确认
同步验证作为一个特殊的情况,根据需要将会出来在商业化生产的不同时期。
二、各阶段的验证
2.1 工艺开发阶段的验证
进行简单分类以后根据验证出现的时期和验证的是否有特殊(极个别情况出现),将首次验证分为:一般首次验证(正常情况)和同步首次验证(极个别情况);将再验证分为:一般再验证和同步再验证。根据以上分类和验证的一下先后逻辑,制作了一下各图。
第一阶段:工艺开发阶段
工艺开发阶段(技术转移、新产品引进……),来自研发的中试工艺或其他途径引进的新工艺,在进入商业批次前,会因为商业化生产设备的不同,可能会引起关键工艺参数的改变。这个时候通过前验证对关键工艺参数进行一定的摸索,在对关键工艺参数进行适当的修正通常是有必要的。通过前验证的报告(或结果)对工艺参数进行修订以后的工艺规程,可以作为下一阶段的工艺草案或批准成为正式的工艺规程。
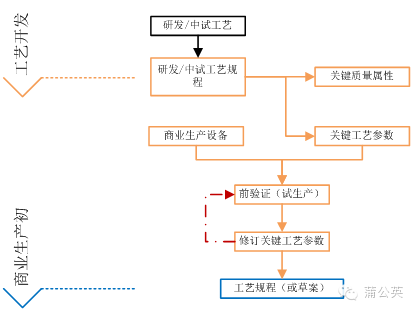
2.2 商业化生产初始阶段的验证
第二阶段:商业化生产初始阶段
根据验证出现的时期和验证的是否有特殊(极个别情况出现),将首次验证分为:一般首次验证(正常情况)和同步首次验证(极个别情况)。
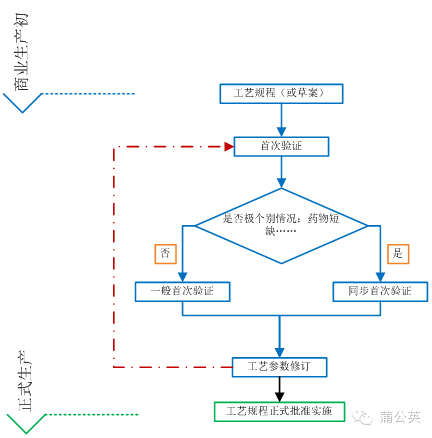
2.3 商业化生产阶段的验证
第三阶段:商业化生产阶段
首次验证结束以后,就进入了正式的(商业)生产阶段,这是生产工艺已经被正式的批准实施,需要基础的工艺数据已经被采集。
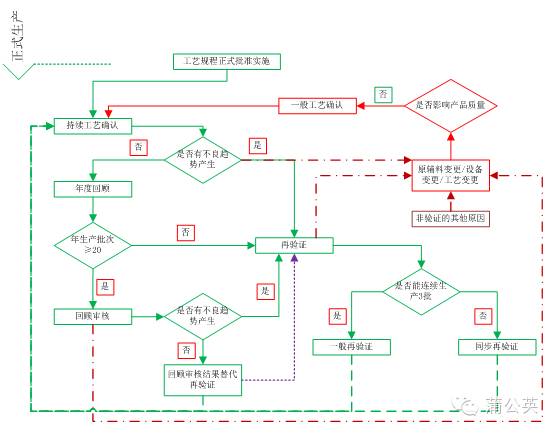
2.3.1 持续工艺确认
接下来就进入了持续工艺确认的阶段,大家都知道日常生产最重要的一点就是要是每一批的生产都处在验证状态,持续工艺确认的目的也许就是让大家随时的确认生产是不是处于验证状态吧。在这个阶段需要注意的就是数据的变化趋势,当出现渐变性趋势的时候,就需要对引起变化趋势的原因进行调查,调查的结果可能会导致再验证或变更。如果没有渐变的趋势,那在年终或其他周期性回顾分析的时候,可以使用持续工艺确认的数据和结果。
如果年生产的批次不少于20批,可以使用回顾分析的结果对工艺进行回顾审核,如果生产数据没有不良趋势的产生,将可以使用回顾审核的结果来替代再验证。但是批次少于20时,因为回顾分析数据量的要求,将不能使用回顾审核来替代再验证,那么这个时候,需要根据公司规定的再验证周期进行再验证。当然了,在使用回顾审核的替代再验证的时候,可能会因为各公司质量管理人员的心里承受能力,而会在一段时间后进行再验证,至于这个一段时间是多久,根据心理承受能力来决定。
2.3.2 周期性再验证
在进入周期性的再验证的时候,需要根据能进行的生产批次来决定再验证的类别。当年生产批次很多,连续生产三批没有压力的话,就进行一般性质的再验证,这个时候需要保证连续三批成功的再验证。当然了能不能少于三批,就需要根据回顾分析的结果和对产品工艺的认知深度来进行评估了,还有就是要考虑少于三批以后,被外来审计的挑战。当产品的每年批次很少,连续生产3批以后销售存在困难的时候,可以根据实际的情况,制定同步再验证方案,这个时候需要质量部门对该方案的合理性进行审核,并需要加大对同步再验证产品的关注程度。
不管是进行再验证、还是使用回顾审核来替代再验证得出结果以后,就会进入下一个持续工艺确认,如此反复,以保证产品的生产始终处于再验证状态。这个时候的工艺规程也不是一成不变的,工艺规程中的工艺参数可以根据对产品和工艺知识的理解进行更新。所以个人感觉最好的就是这个规定,工艺持续改进有了一个法规基础。
2.3.4 变更后再验证
在正式生产以后,可能会因为确认或验证的结果、设备变更、物料供应商变更等问题引起生产工艺的变更,这个时候就需要评估工艺的变更会不会对产品的质量造成影响,如果有影响就需要进行工艺变更后的验证。这个验证可以根据实际情况制定有针对性的验证方案,比如一个包衣片,包衣机进行了变更,这个时候在包衣之前工序的产品质量是没有变化的,甚至之后的包装的密封性应不会被影响到,收到影响的就是包衣片的质量或者说成品的质量,所以在制定方案的时候,可以针对包衣工序专门的制定,同时加大对成品质量稳定性的关注力度,这个进行的可以是同步的工艺验证。当这些变更不会对产品质量造成影响的时候,只要进行一般的工艺确认就可以了,进行确认的目的是为了防止可能会出预计外的某种不良的事件发生。
三、总结
将以上三个阶段的验证进行组合,并添加变更后验证的内容以后,整个流程树如下图所示。
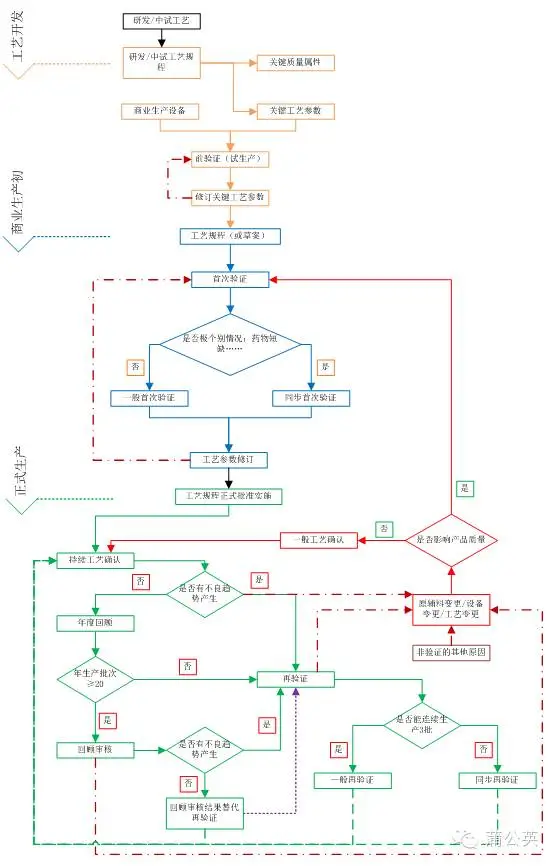
这次画出来的图个人感觉不错,就弄上来嘚瑟一下。要是您觉着有用呢,就给个赞;要是觉着有问题呢,就提出来,我好再修改修改。