铝合金是地壳中含量最为丰富的绿色金属,不但轻、比强度高,而且易于成形,吸能效果好,耐腐蚀,循环利用价值大,因此被当作汽车轻量化的理想材料之一。铝合金最初是作为热交换器部件材料在汽车上应用,继而用于汽车轮毂、发动机汽缸活塞及缸体等部件。2012年以后,发达国家强化了行人保护法规,他们企业在汽车制造时覆盖件大量采用铝合金板材。2020 年,北美汽车引擎盖铝化率接近 75%,车门、行李箱盖、顶棚的铝化率超过 25%。以奥迪、捷豹、F-150 卡车、TESLA-S 品牌的新能源汽车为代表的车身全铝化推动了铝合金板材在结构件上的应用。
中国汽车铝合金板材应用最先始于上汽通用的别克君威、君越,以及一汽大众的奥迪等车型,随后,华晨宝马 5 系列、北京奔驰 C 系列、长安福特蒙迪欧、东风雪铁龙 C6、广汽本田讴歌 TLX 覆盖件也陆续使用铝合金板材。上汽荣威 950 和长城 VV7( 引擎盖) 是较早采用铝合金汽车板材的国产自主品牌。近年来,中国新能源汽车的快速发展推动了铝合金汽车板材的广泛应用。特斯拉、蔚来、小鹏、理想、北汽极狐、广汽、吉利极氪、威马、东风岚图等采用铝合金板材制造覆盖件、结构件及电池系统。作者预计,2025 年国内高端铝合金汽车板材用量将超过 100 万吨。
铝合金汽车板从合金成分上可分类为 5XXX 系、6XXX 系和 7XXX 系。5754、5182、5023 用于内覆盖件及结 构 件; 6016、6014、6022、6111 用 于 外 覆 盖 件;7075 用于热成形的结构件。欧美国家、日本等汽车工业发达国家从 20 世纪 70 年代起开始研发铝合金汽车板; 80 年代初期,加拿大铝业公司和瑞士铝业公司分别研发出高 Cu 的 6111 铝合金和低 Cu 的 6016 铝合金汽车板; 90 年代中期,美国铝业公司开发出不含 Cu 的 6022 合金汽车板。近几年,诺贝丽斯持续推出AdvanzTM系列不同汽车板产品。日本轻金属公司、神户制钢公司开发出了高成型性汽车板 N532、KS5J30( 5023) 。国内铝合金汽车板的研究始于 2000 年,相对发达国家较晚,国内的汽车公司长期依靠进口铝合金汽车板。
近年,中国铝业集团公司为实现高端铝合金汽车板的国产化,由中铝材料应用研究院牵头联合中铝集团下属的西南铝、中铝瑞闽两家企业,在合金板材制备技术及汽车部件的应用技术方面持续研究开发,研制了各种外覆盖件用 6XXX 系、内覆盖件及结构件用 5XXX 系、热 成 形7XXX 系等系列化铝合金汽车板; 并联合汽车公司对结构设计、成型、连接和表面处理等应用技术开展研发,为国产铝合金板材在汽车上的应用形成了系统的解决方案。同时,中铝集团投资新建了铝合金汽车板专业化生产线,实现了高端铝合金汽车板的国产化,在多种车型上实现成功应用。同时,中铝集团牵头制定了我国第一部汽车用铝及铝合金板、带材国家标准( GB/T 33227-2016) 。
本文将对国产铝合金汽车板的研制及应用技术的研究工作进展进行综述。
覆盖件外板用 6XXX 系铝合金汽车板
汽车外覆盖件要求具备良好的外观和抗凹性,通常采用 6XXX 系铝合金板材,表 1 为美国铝业协会标准指定的 4 种 6XXX 系铝合金的成分范围。
为满足汽车外覆盖件的应用需求,对 6XXX 系铝合金汽车板的包边性能、漆刷线、烘烤强化与加工工艺及组织的关系开展了系统研究。表 2 展示了作者所在单位中铝材料应用研究院开发的典型外覆盖件用 6XXX 系铝合金汽车板的基本性能。
Hirth 等研究表明,6016 合金板材中 Si 含量过高会增加裂纹起源点,导致包边性能下降。Li 等研究指出,6014 合金板材的包边性能随着 Mg 与 Si 含量的提高而减低,并通过板材拉伸断裂应变的变化给出了合理的解释。Zhang 等研究了 6016 板材包边性能与晶粒尺寸的关系,随着晶粒细化,促进微裂纹扩展的剪切带变弱,板材包边性能显著提升,如图 1 所示。Ikawa 等研究了板材包边性能与织构的关系,发现 Taylor 因子较高的立方织构、ND45-立方织构利于提升包边性能。
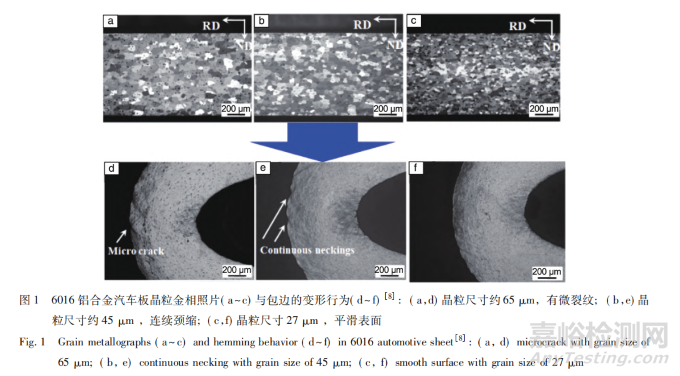
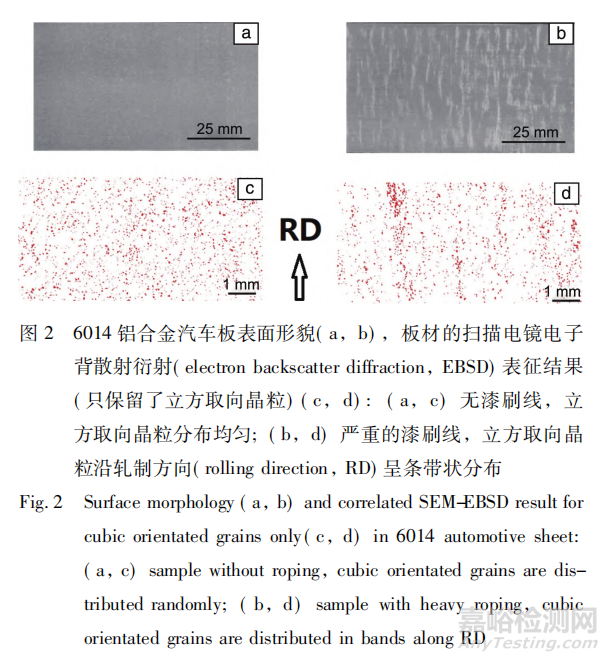
漆刷线是指铝合金汽车板经冲压、涂装后沿轧制方向呈现的条纹。如果程度严重,将影响汽车美观,需要严格控制在二级以上。大多数学者认为,漆刷线是由于立方取向晶粒沿轧制方向连续分布所致( 图 2) 。
6XXX 系铝合金汽车板烤漆后的强度取决于 β″析出相的大小与密度,可以通过合金成分及热处理工艺来调控。室温停放过程中,6XXX 系铝合金容易发生自然时效,形成富 Si 的团簇,烤漆时不利于 β″相的析出,烘烤强度较低。对其预时效可以获得 30 个原子以上的较大团簇,其 Mg 和 Si 含量比接近 1( 图 3a) ,与烤漆 T6P 过程析出的 β″相成分相近( 图 3b) 。因此,这些团簇可以作为烤漆过程 β″相的核促进析出,有利于增加 β″相的密度,提高烤漆后的强度。
覆盖件内板用 5XXX 系铝合金汽车板
5XXX 系铝合金是一种不可热处理强化铝合金,Mg为主要合金元素,起固溶强化作用。相比 6XXX 系铝合金,其成形性能更好,因而成为汽车内覆盖件、结构件的首选材料。表 3 为美国铝业协会标准指定的 3 种 5XXX系铝合金的成分范围,常用的 5XXX 系铝合金汽车板牌号为 5754、5182,5023 合金含 0. 20% ~ 0. 50%的 Cu,是为提高烤漆强度开发的新合金。表 4 为中铝材料应用研究院所开发的 5XXX 系汽车板的基本性能。
5XXX 系铝合金汽车板的屈服强度是影响其成形回弹的重要指标,可以通过 Mg 的固溶量及晶粒尺寸进行调控。5754、5182 铝合金汽车板的屈服强度与晶粒尺寸之间的关系如图 4 所示,服从 Hall-Petch 关系:σy =σ0+kyd-1/2,其中: σy为屈服强度,σ0是摩擦应力,d 为晶粒尺寸,ky为晶界阻力常数。对 5754、5182 铝合金汽车板的退火温度分别为 360,500 ℃,其 σ0与 ky数值如表5 所示。随着 Mg 含量提高,摩擦阻力、晶界阻力增大,表明固溶的 Mg 原子对位错运动的阻力更大,激活相邻晶粒位错源开动所需的应力更高。
5XXX 系铝合金汽车板在冲压成形过程中,表面易出现成形纹,需严格控制。图 5 为 5XXX 铝合金汽车板的代表性应力-应变曲线及冲压成形时的典型成形纹。成形纹路分为 A 型和 B 型两种。A 型即吕德斯带,在冲压板材的表面表现为火焰状花纹,在应力-应变曲线上表现为屈服应变平台,可以用屈服点伸长率( yield point elongation,YPE) 来表征,是位错被 Mg 原子Cottrell 气团钉扎所引起。B 型在冲压板材的表面表现为平行的直线状花纹,对应于应力-应变曲线的锯齿状部分,起源于塑性变形过程中 Mg 原子动态应变时效,即 PLC( Portevin-Le Chatelier) 效应。
图 6 为 5754 与 5182 铝合金汽车板 YPE 与晶粒尺寸的关系。随着晶粒尺寸增大,YPE 减低,有助于削弱吕德斯带。与 5754 合金相比,5182 合金的 YPE 较高,更加容易产生吕德斯带,这是由于后者退火后产生更多的Mg 原子 Cottrell 气团。工业上可以通过增大晶粒尺寸,提高退火后的冷却速率及施加应变来消除吕德斯带。
为了进一步提升轻量化效果,可以在 5XXX 系铝合金中添加 Cu 或 Zn 元素,通过烤漆实现析出强化。图 7 表明含 Zn 的 5182 铝合金在烤漆过程中析出了 Mg 和Zn 富集的 η'相,提高了材料强度。
热成形铝合金汽车板及热成形技术
铝合金汽车板与钢板相比塑性较低,对于形状复杂的零部件难以成形,特别是高强铝合金容易出现开裂、回弹等问题。为了解决铝合金成形问题,业界开发出热成形工艺,即将铝合金板加热到一定温度,显著提高其塑性,进而制造形状复杂的零部件。适合于热成形的铝 合 金 板 材 有 5754、5083、5182、6111、7075 等牌号。
5083 合金板材通过气胀热成形在本田的 Legend 高级乘用车上得到应用。Bariani 团队研究了采用 5083 铝合金板材通过热成 形 制 造 引 擎 盖,发 现 成 形 温 度 为450 ℃时,成形性良好。Zhao 等研究了 Al-4. 5% Mg( 质量分数) 铝合金板材的热成形行为,图 8 为延伸率随温度、应变速率的变化曲线: 在温度 753 K、应变速率10-1 /s 条件下,延伸率接近 200%。在高温及适当的应变速率下,Mg 原子拖曳位错运动,可以促进变形,同时动态回复也有利于热变形。王义林等研究了 7075 铝合金在不同温度和应变速率下的变形行为。在高温拉伸过程中,加工硬化和动态回复相互竞争,而在较高的变形温度和较低的应变速率下,动态回复占主导地位,材料延伸率 得 到 提 高。Lin 等开 发 出 热 成 形-淬 火(hot forming cold-die quenching,HFQ) 一体化技术,用于制造形状复杂的汽车零部件,显著提高其强度。吴新星等研究了采用 7075 铝合金汽车板制备 B 柱加强板的热成形技术,试制的零件尺寸精度满足要求,抗拉强度大于 550MPa。中铝集团的 7075 铝合金板材通过热冲压成形制备了某型汽车的多个高强零部件,其中热成形 B 柱加强板如图 9 所示。作者团队开发出热成形用 5XXX 系、6XXX系铝合金汽车板及热成形工艺,正在开展应用研究。
铝合金汽车板的冷成形技术
成形极限图( forming limit diagram,FLD) 描述了板材在不同应变条件下达到颈缩或断裂的极限应变,被用于评价板材的成形性能的优劣,并作为铝合金汽车板冲压数值模拟的失效判据。获取 FLD 的方法有实验测量和理论计算方法。实验测量方法包括缺口单向拉伸法、Marciniak 法和 Nakazima 胀形法,其中 Nakazima 胀形法应用最广泛,被国际标准 ISO12004和国家标准 GB/T15825. 1—2008采用; 理论计算方法有 Swift 提出的扩散颈缩模型、Hill 提出的局部颈缩模型、Stören 和Rice 提出的分叉理论模型及 Marciniak 和 Kuczynski 提出的凹槽理论( M-K 模型)等。迄今为止,M-K 模型是FLD 理论计算中应用最广泛的方法。
影响板材 FLD 的因素有板材的厚度、力学性能、晶粒尺寸与织构等。Keeler 和 Brazier提出了 FLD 曲线最低点 FLD0( %) 与板材厚度 t ( mm) 、加工硬化指数 n 的经验公式:
随着板材厚度及加工硬化指数的增加,成形极限提高。
Wu 等通过晶体塑性理论结合 M-K 模型计算了 6111-T4 板材的 FLD,并研究了织构对成形极限的影响,如图 10 所示。作者采用该方法预测了 6016-T4P 汽车板材的成形极限,如图 11 所示,计算结果与实验结果吻合度高。
开裂、褶皱以及回弹是铝合金汽车板冲压面临的主要问题,需要采用精确模拟仿真技术进行预测,并通过优化模具设计及冲压工艺来解决。研究在复杂加载条件下铝合金汽车板的力学性能与摩擦性能,建立高精度本构模型和摩擦模型,是实现精确模拟仿真的核心技术。
屈服准则是本构模型的重要内容之一,作者团队通过双向拉伸实验对 6014 铝合金汽车板的屈服准则进行了研究,结果如图 12a 所示,表明 Barlat89、Yld2000-2d 屈服准则具有较高的精度,理论计算值与实验值吻合较好。精确的强化模型是另外一个重要内容,作者通过拉-压实验研究了反向加载条件下 6014 铝合金汽车板的强化规律,建立了 Y-U 随动强化模型,如图 12b 所示,与实验结果基本一致。
降低冲压模具与板材之间的摩擦力是提高合金冲压成形性的有效途径,其中,建立精确的摩擦模型成为最大挑战,国内外学者先后提出了一系列模型,其中,Hol等建立了考虑压力、速度、涂油量以及材料性能的摩擦模型,在覆盖件冲压成形模拟和模具开发中获得了较好的应用效果。作者通过建立的本构模型和摩擦模型,开展了对 6014 铝合金汽车板冲压制备发动机罩外板的模拟,结果如图 13 所示。模拟结果与实际冲压的发动机罩外板在形状、应变、开裂位置方面基本一致,并通过工艺优化成功开发出无成形开裂缺陷、尺寸精度高的发动机罩外板。
铝合金汽车板的连接技术
铝合金汽车板与钢板相比,电阻点焊性能较差,因此自冲铆( self piercing riveting,SPR) 、拉铆、clinch-铆接、热熔自攻铆接等机械连接成为重要的连接方法。其中,自冲铆是目前应用最广泛的连接工艺,不仅适用于铝合金板材之间的连接,而且可实现铝合金板材与钢板等其他异种材料的可靠连接。
图 14 为 SPR 工艺示意图,整个过程分为压紧、冲裁、扩展和冲铆完成 4 个阶段。其工艺复杂,影响接头的连接性能的因素诸多,包括板材性能与尺寸、铆钉种类与形状、模具及铆接工艺等。通过物理实验进行铆接工艺研究和优化较为困难,常采用模拟方法来优化。Porcaro 等使用 LS-DYNA 有限元软件模拟了铝合金板材的 SPR 过程中板料及铆钉的变形。Bouchard 等建立了 SPR 工艺损伤模型和断裂模型,采用 Forge2005 有限元软件计算获得了与实验结果相近的接头残余应力、内部损伤和接头强度等。Atzeni 等采用 DEFORM-2D 软件研究了凹模凸台高度和铆钉材料对铆接接头质量的影响。杜爱民等采用 Simufact 软件建立 SPR 仿真平台,并通过实验平台验证了仿真平台的有效性。彭桂枝基于 Archard 磨损模型与 Deform-3D 软件,建立了两层 5754铝合金板材 SPR 安装过程的模具磨损的有限元模型,获得了工艺参数与模具磨损深度之间的变化关系。
作者团队系统研究了汽车发动机罩内板 5182 合金板与结构件 5754 合金板的 SPR 连接过程和板材的力学性能对接头性能的影响。对穿孔试样拉伸过程模拟与拉伸实验载荷-位移曲线进行对标,确定材料断裂的极限应变,如图 15 所示。建立 SPR 接头变形模型,采用 DEFORM 软件获得了模拟接头的横断面,如图 16 所示,与实际铆接接头断面形貌基本一致,接头互锁值、底厚值等关键参数的计算值与实验值的误差在 5%以内,模型精度较高。通过数值模拟方法已优化出多种汽车零部件的 SPR工艺。
铝合金汽车板的表面处理技术
铝合金汽车板零部件的涂装一般采用“前处理+电泳+喷涂”的工艺,前处理工序直接决定了涂装后的漆膜结合能力和耐腐蚀性能,尤为重要,也一直是研究的热点。目前汽车公司采用的前处理工艺主要有磷化、锆系薄膜化、硅烷化 3 种。
磷化的原理是磷酸锌盐在铝合金表面沉积。铝合金自身容易氧化,通常在溶液中加入一定的氟离子去除表面氧化膜,并且将多余的铝离子以沉淀的形式析出,防止磷酸铝盐生成,影响磷化膜在表面的生长。铝合金汽车板在出厂前一般要进行清洗、钝化处理,去除表面较厚的氧化膜,并形成薄而致密的钛锆钝化膜,这层钝化膜会对基材的磷化处理产生一定影响。作者团队研究了钛锆钝化膜重量对 6016 铝合金汽车板磷化的影响( 图 17) ,当铝合金表面钛锆钝化膜处于较低或中等重量水平时,磷化结晶体尺寸适中,并且能够将表面全覆盖;当钛锆钝化膜处于较高重量水平时,磷化结晶体尺寸明显增大,并且覆盖度明显下降,较多的钛锆钝化膜会抑制磷化反应。
铝合金的锆系薄膜化处理是锆酸盐与铝合金发生化学转化反应在表面形成一层纳米级的氧化锆。相比于磷化膜,锆系薄膜制备减少了镍盐、磷酸盐对环境的污染,而且不需要表面活性调控工序,因而效率提高。王正曦等研究了 5182 铝合金的锆系薄膜化过程,发现锆化膜优先在含 Fe 第二上生成。近年来业界的研究主要集中在锆系薄膜化工艺方面,如添加了稀土 Ce 增加转化膜的致密性,添加了钼酸盐、钒 酸 盐 增 加 膜 层 的 自愈性。
硅烷化处理是硅烷水解后硅醇与羟基发生脱水缩合,硅醇和硅醇发生缩合形成硅氧烷。硅烷化处理与锆系薄膜化相比,由于 Metal—O—Si—O 共价键呈立体网状结构,因此具备更好的漆膜结合能力和防腐效果。
结语
为满足新能源汽车对高性能铝合金板材的需求,作者所在团队中铝材料应用研究院开展了 5XXX、6XXX、7XXX 系铝合金汽车板材的成分-工艺-金属组织-基本性能及应用性能的关联性研究。通过这些研究,结合工业化生产,实现了覆盖件外板用 6014、6016 铝合金板材、覆盖件内板或结构件用 5182、5754 铝合金板材、及热成形 7075 铝合金板材的大批量应用。
今后,为推动铝合金汽车板在新能源汽车上更大规模的应用,需要开展以下研究工作: ① 开展面向高成形性、高烤漆强度的基于“团簇”的成分设计的研究,满足新能源汽车零部件结构更复杂、重量更轻的要求; ② 开展先进成形与连接、绿色表面处理等应用技术的研究,提升铝合金汽车零部件的制造能力与环境保护水平;③ 开展内外板用铝合金系列一体化的新材料研究,使铝合金汽车零部件容易回收; ④ 开展铝制零部件的绿色同级回收技术、短流程制备技术的研究,实现新能源汽车绿色发展。
