【摘要】白车身弯曲刚度对于整车性能影响极大,在研发过程中长期以来都是靠经验进行弯曲刚度性能优化。但由于白车身零部件数量多、结构复杂,这种传统经验方法在优化效率和优化效果方面很不理想。文章介绍了一种基于应变能(ESE)结果的优化方法,可以有效提升白车身弯曲刚度的优化效率和优化效果,并以某款车型为例,详细对比了以上两种优化方法。对比结果显示,这种基于应变能的优化方法在优化效率和优化效果方面明显优于传统方法。阐述的基于应变能ESE的优化方法,可以有效保证白车身弯曲刚度性能的快速达成,缩短白车身研发周期,具有显著的经济效益和社会效益。
1、引言
在汽车行业整车开发过程中,白车身弯曲刚度是影响整车性能的重要参数之一[1]。白车身弯曲刚度不足,会造成整车性能恶化,包括:
(1)在行车过程中引起车身的门框、窗框、发动机舱口以及行李箱口的变形,并引发异响;
(2)低刚度必然伴有低的固有振动频率,易发生结构共振及声响[2];
(3)降低白车身结构接头的连接强度[3];
(4)影响安装在底架上总成的相对位置[4];
(5)直接影响或间接影响汽车行驶的平稳性、舒适性和操纵性能[5]。
因此,为了避免上述问题,对于研发车型,必须合理定义白车身弯曲刚度目标值,并在项目前期就开展白车身弯曲刚度CAE分析及优化工作,以便于及时发现问题并对现有结构进行优化[6]。
本文提出了一种快速精确找出影响乘用车白车身弯曲刚度性能关键位置的方法,减少对白车身设计师的设计经验要求。这种方法极大的提高了白车身弯曲刚度优化效率,有效保证整车开发目标和开发节点的达成。
2、传统白车身弯曲刚度CAE 分析优化流程
2.1 传统白车身弯曲刚度CAE分析流程
2.1.1 网格划分及建立连接关系
将白车身总成CAD数据(图1)导入到CAE软件中,进行网格划分并建立粘胶、焊接、螺接的连接关系,得到白车身总成CAE模型(图2),白车身总成CAE模型中含有白车身总成各钣金零件的外形、材料、厚度和连接关系信息。
图1 白车身总成CAD模型
图2 白车身总成CAE模型
2.1.2 建立约束关系
约束右后减振器座沿x轴、y轴和z轴平动自由度,约束左前减振器座、左后减振器座和右前减振器座沿y轴和z轴平动自由度,如图3所示。
图3 白车身弯曲刚度CAE模型约束
2.1.3 建立载荷
在白车身近B柱位置左右两侧前门槛梁位置沿-z方向分别对称施加2 224 N集中载荷,如图4所示。
2.1.4 CAE模型提交计算
以上CAE模型完成后,提交CAE线性求解器软件(例如NASTRAN软件)进行计算。
图4 施加集中载荷
2.1.5 白车身弯曲刚度计算
(1)测试点选取
CAE模型计算完成后,打开计算结果文件(例如op2结果文件)分别在左侧门槛梁和右侧门槛梁中线位置(图5)提取z向位移绝对值最大点,其Z向位移分别记为Z_left和Z_right,如图6所示。
图5 门槛梁中线位置
图6 测试点选取
(2)弯曲刚度计算
弯曲刚度计算值:
式中,Kbending为弯曲刚度。
工程实际中乘用车白车身左右结构并非完全对称,虽然会导致Z_left和Z_right对应点不处于同一x轴坐标。但是由于白车身左右结构差别一般不大,因此左右x轴坐标差异一般较小,以上弯曲刚度计算公式仍然适用。
2.1.6 将弯曲刚度计算值与目标值对比
(1)若白车身弯曲刚度计算值大于目标值,则说明白车身弯曲刚度性能达标,不需要进行优化;
(2)若白车身弯曲刚度计算值低于目标值,则说明白车身弯曲刚度性能不达标,则需要执行白车身弯曲刚度CAE优化流程。
以上即为传统白车身弯曲刚度CAE分析流程。
2.2 传统白车身弯曲刚度CAE优化流程
2.2.1 依靠经验找出白车身薄弱点
若白车身弯曲刚度不达标,则需要进行优化设计,使其满足目标要求。白车身设计师根据设计经验来判断影响白车身弯曲刚度性能的薄弱点,并针对这些薄弱点进行结构优化(例如增加零部件壁厚、增设加强筋、增加结构胶)。
2.2.2 重新验算优化方案下的白车身弯曲刚度
将优化后的白车身CAD数据重新执行白车身弯曲刚度CAE分析流程,计算结构优化后的白车身弯曲刚度。
2.2.3 结果对比
将结构优化后的白车身弯曲刚度值与目标值对比:
(1)若白车身结构优化后的弯曲刚度值大于目标值,则说明白车身弯曲刚度性能达标,优化完成;
(2)若白车身结构优化后的弯曲刚度值仍然低于目标值,则说明白车身弯曲刚度性能不达标,需要重新执行步骤2.2.1~2.2.3。
由于白车身总成包含的零部件数量很大,要精确选取影响白车身弯曲刚度性能的薄弱点难度非常大。若白车身设计师经验不足,则难以抓住真正的白车身弯曲刚度薄弱点进行优化,优化后的结构往往仍然难以满足目标值,必须重新优化,导致以上2.2.1~2.2.3步骤需要反复进行,整车开发目标和开发时间节点难以保证。
2.3 基于ESE的白车身弯曲刚度CAE优化流程
2.3.1 ESE结果输出
ESE结果可以显示结构中吸收能量最集中的部位和该工况下能量的分布。ESE集中的区域,表示在该工况下此位置变形大、能量集中、刚度不足,是优化关注的重点。在传统白车身弯曲刚度CAE分析流程的基础上,在步骤2.1.4中,对完成的CAE模型增加ESE结果输出,如图7所示,其它保持不变,提交CAE线性求解器软件(例如NASTRAN软件)进行计算。
图7 增加ESE输出
2.3.2 查看ESE结果
在后处理软件中(例如HyperView中),查看白车
身弯曲刚度计算结果中的ESE结果,并选取某个ESE阈值以上的区域作为优化备选区域。ESE阈值过小,则优化备选区域过大,优化效率较低;反之,则优化备选区域过小,同时由于白车身生产工艺及成本的限制,优化空间较小。根据工作过程中大量车型的经验总结,针对乘用车白车身弯曲刚度性能优化而言,一般筛选出ESE计算值大于0.2的区域,这些区域视为白车身弯曲刚度性能的薄弱点,可以同时兼顾较高的优化效率和优化空间,如图8所示。
图8 应变能大于0.2的区域
2.3.3 对照ESE结果进行结构优化
结合白车身的生产工艺(包括钣金冲压工艺、白车身焊装、涂装、总装工艺)要求,针对2.3.2中ESE大于0.2的区域进行结构优化(例如增加零部件壁厚、增设加强筋、增加结构胶等);
2.3.4 执行白车身弯曲刚度CAE分析
将优化后的CAE模型重新执行白车身弯曲刚度CAE分析流程;
2.3.5 结果对比
将白车身优化后的弯曲刚度与目标值对比:
(1)若白车身结构优化后的弯曲刚度大于目标值,则说明白车身弯曲刚度性能达标,优化完成;
(2)若白车身结构优化后的弯曲刚度仍然低于目标值,则说明白车身弯曲刚度性能不达标,需要重新执行步骤2.3.3~2.3.4。
以上这种基于ESE的白车身弯曲刚度CAE优化方法,通过首先筛选出白车身结构中ESE大于0.2的区域,将这些区域视为白车身弯曲刚度性能的关键薄弱点并进行着重优化,大幅度降低了对白车身设计师的设计经验的要求,提高了优化效率,有效保证了白车身弯曲刚度性能目标的实现。
3、传统优化方法和基于ESE优化方法比较
3.1 背景说明
图9为某款车型的白车身CAE模型,白车身弯曲刚度CAE计算值为13 779 N/mm,而目标值定义为14 000 N/mm,不满足目标要求,因此需要针对白车身现有结构进行优化(例如增加零部件壁厚、增设加强筋、增加结构胶),使白车身弯曲刚度达到目标值。
图9 某款车型的白车身CAE模型
3.2 传统白车身弯曲刚度CAE优化方案
3.2.1 白车身结构薄弱位置选取
白车身设计师根据设计经验认为,零部件A和零部件B(图10、图11)是影响白车身弯曲刚度的薄弱部件,结合白车身的生产工艺要求,白车身设计师将零部件A由壁厚0.7 mm增加至1.0 mm,将零部件B由壁厚0.7 mm增加至1.0 mm,作为优化后的白车身结构数据。
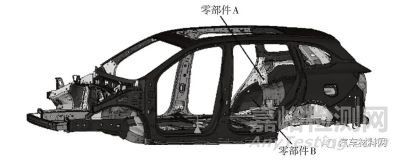
图10 零部件A和零部件B
图11 零部件A和零部件B结构
3.2.2 白车身弯曲刚度计算
对3.2.1中优化后的白车身数据重新执行白车身弯曲刚度CAE分析流程2.1.1~2.1.6,计算优化后的白车身弯曲刚度值,其结果汇总如表1所示。
3.3 基于ESE的白车身弯曲刚度CAE优化方案
3.3.1 增加ESE结果输出
在白车身弯曲刚度CAE分析流程阶段,就增加ESE结果输出(图7)。
3.3.2 基于ESE结果查找白车身结构薄弱点
在后处理软件中(例如HyperView中),查看白车身弯曲刚度计算结果中的ESE结果,筛选出ESE计算值≥0.2的区域,这些区域视为影响白车身弯曲刚度性能的关键薄弱区域,如图12所示。
图12 某车型车身ESE≥0.2的区域
3.3.3 结构优化
将分别属于3.3.2中ESE≥0.2区域1和区域2的零部件C(图13)和零部件D(图14)作为优化对象,并结合白车身的生产工艺要求,将其壁厚由1.0 mm增加至1.2 mm,作为优化后的白车身结构数据。
图13 零部件C
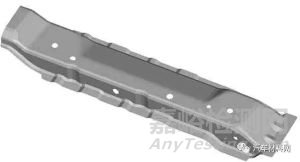
图14 零部件D
3.3.4 优化效果对比
对3.3.3中优化后的白车身结构数据执行白车身弯曲刚度CAE分析流程,计算优化后的白车身弯曲刚度值,其结果汇总如表1所示。
表1 白车身弯曲刚度CAE优化方法结果汇总
从表1可见,基于应变能的白车身弯曲刚度优化方法在优化效率和优化效果方面均优于传统优化方法。
4、 结束语
从表1结果对比可见,基于应变能的白车身弯曲刚度CAE优化方法,可以快速识别现有白车身结构中弯曲刚度性能的关键薄区域,并结合白车身的生产工艺要求针对薄弱点进行结构优化,大幅度降低了对白车身设计师的设计经验要求,提高了优化效率,有效保证了白车身弯曲刚度性能目标的实现。
参考文献
[1]吕建刚,何忠波,张培林,等.车辆结构与原理[M].北京:国防工业出版社,2007.
[2]王秋晨.汽车试验在产品研发中的作用[J].环球市场信息导报,2017(27):142-143.
[3]曾春华,郑十践.疲劳分析方法及应用[M].北京:国防工业版社,1991.
[4]江迎春,陈无畏.基于NASTRAN的汽车转向节有限元分析[J].客车技术,2007(6):9-12.
[5]武一民,崔根群等.转向节结构有限元分析[J].拖拉机与农用运输车,2004(6):8-9.
[6]郑金华.多目标进化算法及其应用[M].北京:科学出版社,2007.
