目前,轻质材料尚无公认的定义。一般认为,密度不大于5.0g/cm3,用以制造武器装备主体结构和工程结构的材料为轻质材料。轻质材料是武器装备轻质化发展、满足不断增加的有效载荷质量和空间余度的重要物质基础。按照物理化学属性以及在武器装备结构上的使用特点,轻质材料主要分为铝合金、钛合金、镁合金和复合材料四大类。
近年来,轻质材料研究蓬勃发展,对其综合性能提出更高要求:
1)要求材料具有更高的比强度、比模量;
2)具有良好的环境适应性;
3)要求材料有足够的损伤容限;
4)具有可靠的抗过载能力和高温性能;
5)良好的工艺性能和可承受的经济成本。
轻质材料,同时也是武器装备重要结构材料,其中铝合金、钛合金和复合材料已成为除钢以外的第二、第三、第四大结构材料。在武器装备机械化、信息化复合发展中,轻质材料的应用是实现武器装备结构轻质化以及高可靠性的基本保障,对于武器装备速度与机动性、生存与突防等性能具有重要影响。总的来说,轻质材料的发展与武器装备的性能提高是相辅相成、相互促进的。目前能够看到许多轻质材料已经在航天装备、航空装备、兵器装备、船舰装备及其他装备上的应用。
设计选材原则
几乎所有的材料在使用或贮存过程中都会产生不同程度的腐蚀损伤,导致由其构成的装备结构破坏,性能下降或功能失效。在装备设计之初,合理地选择材料,并采取恰当的表面防护措施,是有效控制腐蚀,保证装备安全、可靠服役最重要也是最基本的方法。
由于材料在装备上的使用部位和工况条件不同,对某一具体材料的力学性能、疲劳性能、耐腐蚀性能和工艺性能等的要求也不相同,因此,选择材料应全面考虑材料的综合性能,包括:
① 耐腐蚀性能满足预期的使用要求;
② 物理、力学和加工工艺性能等满足设计要求;
③ 经济可承受性或高的效费比。
需要指出的是,材料的耐腐蚀性能与使用环境的腐蚀严酷性密切相关,不同的环境对构成装备的材料会产生不同程度的影响。因此,选择材料应首先考虑环境因素。另外,为了满足装备强度和刚度等设计要求,工程技术人员还应结合设计因素来考虑选材。
设计选材流程
如何从一系列候选材料中选择一种力学性能与耐腐蚀性能最为匹配的材料是一项相对困难的工作。选择材料不仅仅是基于装备某些关键性能选择所需材料的过程,还需考虑寿命周期内材料的耐腐蚀性能、腐蚀防护与控制方法、可维护性、成本等多种因素。图1给出了“六步法”设计选材流程,可以帮助工程设计人员在设计阶段早期建立初始候选材料列表,并通过全面的腐蚀分析确定最佳材料体系和热处理状态,尽可能将与腐蚀有关的维护工作最小化,从而降低全寿命期总费用。
1、经验甄选材料
选材的第一步是基于过去使用经验或教训甄选初始候选材料并淘汰那些可能存在严重腐蚀问题的材料。从全寿命期费用控制出发,应尽可能避免考虑任何在过去类似应用中具有较高腐蚀敏感性的材料,尤其是在经济可承受基础上实施表防设计和相关维护程序,腐蚀问题仍然无法有效控制的材料。工程设计人员可通过检索分析相关手册、数据库、研究报告等提供的环境适应性数据信息,或者咨询专业环境试验研究机构的专家,以充分了解、掌握和确定材料和环境的特定组合是否存在腐蚀问题。
另外,分析相似装备在选材方面的经验或教训对于腐蚀防护设计非常重要。通过搜索装备腐蚀故障案例和成功的实践经验,有助于确定类似应用中抗环境腐蚀性能表现不好的材料,也有助于确定具有良好耐腐蚀性能的材料。这些信息可作为材料选择的重要依据,用于剔除候选材料列表中的不良选择,或者确定添加到候选列表中的其他新材料。
2、环境分析与评估
工程设计人员应开展装备寿命期环境剖面分析,全面了解候选材料可能遭遇的各种环境因素及其影响,作为选材的依据。这些环境既包括装备所处的外部环境,主要为自然环境,如高原高寒环境、湿热海洋环境、干热沙漠环境等,导弹产品主要指库房贮存环境,也包括装备不同结构部位所形成的局部环境,如飞机、舰船、车辆等舱内环境,或者产品工作时可能经受的特殊环境条件。
表1 装备用材料使用环境分类
武器装备寿命期(运输、贮存/后勤供应、执行任务/作战使用等)可能遇到的环境因素非常复杂,所有可能经历的环境条件都不应忽视。例如,通过海上运输的地面车辆需考虑盐雾的侵蚀作用,多地域作战装备应考虑环境叠加效应。接头、垫圈、紧固孔等结构细节容易产生缝隙,滞留水分或电解液, 可形成引起特殊腐蚀形式的微环境,如电偶腐蚀、缝隙腐蚀等,选材时也应予以考虑。一旦对预期使用环境有了较为清晰的了解和认识,可通过回答表2所列的环境问题来剔除不相干的腐蚀形式。
表2 排除无关腐蚀失效模式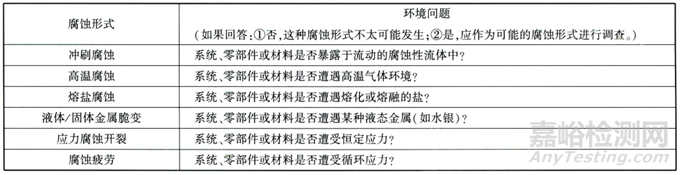
3、基于潜在腐蚀模式评估材料
选材的第三步是基于可能存在的腐蚀失效模式评估候选材料的耐腐蚀性。由于设计人员对材料可能出现的各种腐蚀形式缺乏直观明确的认识和理解,如何确定设计选材需考虑的腐蚀形式并不是件容易的事情。推荐优先采用经环境试验验证或经多年工程应用证明可靠的材料,但应考虑材料热处理或使用环境的改变可能导致其他形式的腐蚀。大多数材料应用会受到一种或多种主要或次要腐蚀形式的影响,如表3所列。
通过上述腐蚀分析淘汰存在严重腐蚀问题的候选材料后,还应平衡材料的耐腐蚀性能与其他性能的关系。一般来说,金属材料的耐腐蚀性能可用平均腐蚀速率(失重法)、腐蚀深度(金相法)、抗拉强度保持率、断后伸长率保持率、断裂韧度保持率、应力腐蚀破裂临界应力强度因子Kiscc、疲劳强度(寿命)等来表征。由于材料在装备上的使用部位和经受的工况条件不同,选材中对材料强度、刚度、腐蚀疲劳、应力腐蚀、断裂韧性等指标的要求也不同。既不能片面追求单一性能的优越,也不能不分主次所有性能一视同仁,应认识到没有面面俱到的材料,通常强度越高,材料对环境作用往往越敏感。为了使材料耐腐蚀性能满足装备使用要求,应根据具体结构功能、构型、受力特点和维修难易,对材料各种耐腐蚀性能指标进行综合考虑,灵活选材。非承力结构和次承力结构用材,建议重点考虑材料的平均腐蚀速率、腐蚀深度、静强度等指标,承力结构用材还应考虑应力腐蚀破裂、腐蚀疲劳等问题。对于腐蚀关键部位和不易维修的部位,原则上应选择高耐蚀的材料以及腐蚀倾向小的热处理状态。
铝合金优选原则示例:铝合金等结构材料的特征要素是强度,推荐选择抗拉强度保持率、断后伸长率保持率和晶间腐蚀等级作为选材指标。优选标准以一定的环境条件和暴露时间下指标应达到的合格判据表示,优选原则是三个指标须全部达到合格判据,只要有一个指标不满足则不通过。一般来说,严酷环境下使用的材料耐腐蚀性等级应高于良好、一般环境下使用的材料。
表4 铝合金优选原则
4、结构设计因素
选材的第四步是考虑结构设计因素的影响。型号设计人员不仅要掌握候选材料的环境腐蚀特性,还应运用腐蚀观点来考虑结构设计。有时装备结构选用的材料单独来看都是满足耐蚀要求的,组合在一起却发生严重的腐蚀问题,甚至在远小于设计应力作用下发生断裂故障,究其原因就是设计因素考虑不足导致的选材不当。下面主要从电偶连接、缝隙、应力等设计因素讨论对选材的要求。
(1)电偶腐蚀因素
异种材料连接在装备结构上随处可见,一般来说当相互接触的两种材料电位差超过250mV就会产生明显的电偶腐蚀。因此,选材时不应孤立考虑材料的耐腐蚀性,而应将与其接触的其他材料视为一体来考虑。设计人员可参考各种材料在海水中的电偶序,从电位差、阴阳极面积比等方面筛选合适材料。如果无法避免两种电位相差较大的材料连接,如铝-钢、铝-钛、 铝-碳纤维复合材料、钢-钛等,就应采取有效的隔绝措施。
(2)缝隙腐蚀因素
紧固件连接(如螺接、铆接、销接等)和焊接产生的缝隙在装备上极为普遍,为缝隙腐蚀提供了条件。结构设计上应尽可能避免狭缝结构,采用无缝隙连接技术,如焊接代替螺铆连接,用连续焊、胶接点焊代替点焊,尽量采用湿装配和密封剂消除缝隙,装配完成后建议喷涂面漆进一步填补缝隙。由于缝隙腐蚀对结构安全危害大,在选材时应重点考虑,优先选用钛合金、耐点蚀好的铝合金、高铬钢等。
(3)应力因素装备结构大多会承受一定的工作应力,同时热处理、加工制造和装配过程还会产生程度不同的残余应力,在腐蚀环境中存在发生应力腐蚀破裂和腐蚀疲劳的隐患。应力腐蚀破裂只在特定的材料-环境体系中发生,潮湿工业大气和海洋大气环境是引起应力腐蚀的敏感环境。结构选材中应尽量避免所选材料与使用环境构成应力腐蚀的特定体系,如果综合权衡后仍然要选择这种材料,应根据材料的KISCC合理确定设计许用应力。另外,由于材料的腐蚀疲劳极限往往低于机械疲劳极限,并随使用时间的延长大大下降,因而选材时应参考腐蚀疲劳极限选择适用材料,充分考虑环境的影响。
5、选择腐蚀防护方法
选材的下一个步骤是选择恰当的腐蚀防护方法,确保材料的良好表现。特殊情况下,某些高耐蚀材料不需要专门的表面防护方法,如钛合金、不锈钢等。然而,大多数金属材料及非金属材料都需要进行表面防护以隔绝外界(使用)环境的侵蚀作用。一般严酷环境使用的材料往往需要综合多种腐蚀防护方法来提供足够的抗环境腐蚀能力,例如,铝合金通常采用阳极化+底漆+(中间漆)+面漆的多层防护体系(阳极氧化简称阳极化)。
图2提供了全寿命周期避免或减缓材料腐蚀的腐蚀控制策略,这些策略对于有效控制腐蚀都是必要的。
图2 全寿命周期腐蚀控制策略
①在材料表面施加有效屏蔽层,以防止腐蚀环境与材料直接接触,如前面提到的铝合金涂层。涂层体系的选择取决于与基材的相容性、零部件的可达性、表面加工质量等,对于不可达区域,应该使用更耐用或更持久的涂层。
②微环境抑制技术。温度、湿度是影响材料腐蚀速率的重要参数,在工程许可范围内,采取密封、降温、放置干燥剂、定期通干燥空气排除湿气等措施,可以降低内部微环境的腐蚀性。利用缓蚀剂来改善材料所处的环境也是一种通用的方法。另外,有计划的维护保养和清洗作业将延长材料的使用寿命。
6、有计划开展腐蚀验证试验
材料的腐蚀损伤是一个慢作用时间累积过程,而自然环境试验是真实可靠验证考核材料环境腐蚀行为规律最基础的试验。传统的实验室加速环境试验虽然试验周期短,但对多重环境因素的耦合效应模拟不足,对环境的长期累积作用考核不充分,试验结果的有效性需要自然环境试验数据来佐证、评估。因此,考虑装备研制进度,综合采用实验室加速环境试验和自然环境试验手段,快速准确掌握新材料、新工艺、新结构环境损伤特征及关键性能退化规律,是支撑装备全寿命环境适应性设计/改进的重要方法。下面推荐在实验室综合/组合试验的基础上,开展基于标杆样品的短期自然环境试验,外推预测长期自然环境试验结果的一种方法路径,其实施步骤如下:
(1)至少选择两种与待试新材料具有相似组成结构的标杆样品,一种具有相对较好的环境适应性,一种具有相对较差的环境适应性。标杆样品是指能够代表某一类材料的性能特点,在给定环境条件下腐蚀特性已知,用于辅助评估新材料环境适应性的基准材料。
(2)针对预评估环境特征,分析确定要考虑的环境因素,如温度、湿度、太阳辐射、腐蚀介质种类及干湿交替等,基于环境当量等效转化技术设计多因素综合/组合加速试验谱,尽可能体现材料主要环境影响因素的耦合作用。
(3)将选取的标杆样品与新材料同时开展实验室多因素模拟加速试验研究,每个循环周期后取样(标杆样品和新材料)在相同的试验条件下进行性能测试,试验直至任意标杆样品或新材料失效,或达到规定的腐蚀损伤程度,或性能发生明显变化时为止。
(4)将选取的标杆样品与新材料同时开展1-2年的自然环境试验,按周期取样(标杆样品和新材料)在相同的试验条件下进行性能测试,绘制性能-时间历程变化曲线,用于验证实验室加速试验结果的有效性。
(5)对比实验室加速试验和自然环境试验下标杆样品与新材料的耐蚀性能优劣顺序是否一致、腐蚀损伤模式及变化规律是否一致或相似;利用标杆样品的标尺刻度作用,预判新材料耐蚀性能区间。
(6)在标杆样品与新材料腐蚀损伤规律和耐蚀性能优劣顺序基本一致的前提条件下,采用适宜的概率统计分析方法对新材料耐蚀性能进行一定置信度下的容差下限(上限)估计,实现对新材料环境适应性的预测评估。否则,实验室加速试验结果不可接受,需要重新设计试验。
适用性原则是指所选择的材料必须能够适应工况,并能达到令人满意的使用要求。满足使用要求是选材的必要条件,是在进行材料选择时首先要考虑的问题。
材料的使用要求体现在对其化学成分、组织结构、力学性能、物理性能和化学性能等内部质量的要求上。为满足材料的使用要求,在进行材料选择时,主要从零件的负载情况、材料的使用环境和材料的使用性能要求三个方面考虑。零件的负载情况主要是指载荷的大小和应力状态。材料的使用环境指材料所处的环境,如介质、工作温度及摩擦等。材料的使用性能要求指材料的使用寿命、材料的各种广义许用应力、广义许用变形等。只有将以上三方面进行充分的考虑,才能使材料满足使用性能要求。
材料及成型工艺选择的步骤、方法及依据
材料及成型工艺的选择步骤如下:首先根据使用工况及使用要求进行材料选择,然后根据所选材料,同时结合材料的成本、材料的成型工艺性、零件的复杂程度、零件的生产批量、现有生产条件和技术条件等,选择合适的成型工艺。
1、选择材料及其成型工艺的步骤、方法
分析零件的服役条件,找出零件在使用过程中具体的负荷情况、应力状态、温度、腐蚀及磨损等情况。
大多数零件都在常温大气中使用,主要要求材料的力学性能。在其他条件下使用的零件,要求材料还必须有某些特殊的物理、化学性能。如高温条件下使用,要求零件材料有一定的高温强度和抗氧化性;化工设备则要求材料有高的抗腐蚀性能;某些仪表零件要求材料具有电磁性能等。严寒地区使用的焊接结构,应附加对低温韧性的要求;在潮湿地区使用时,应附加对耐大气腐蚀性的要求等。
(1) 通过分析或试验,结合同类材料失效分析的结果,确定允许材料使用的各项广义许用应力指标,如许用强度、许用应变、许用变形量及使用时间等。
(2) 找出主要和次要的广义许用应力指标,以重要指标作为选材的主要依据。
(3) 根据主要性能指标,选择符合要求的几种材料。
(4) 根据材料的成型工艺性、零件的复杂程度、零件的生产批量、现有生产条件、技术条件选择材料及其成型工艺。
(5) 综合考虑材料成本、成型工艺性、材料性能、使用的可靠性等,利用优化方法选出最适用的材料。
(6) 必要时选材要经过试验投产,再进行验证或调整。
上述只是选材步骤的一般规律,其工作量和耗时都是相当大的。对于重要零件和新材料,在选材时,需要进行大量的基础性试验和批量试生产过程,以保证材料的使用安全性。对不太重要的、批量小的零件,通常参照相同工况下同类材料的使用经验来选择材料,确定材料的牌号和规格,安排成型工艺。若零件属于正常的损坏,则可选用原来的材料及成型工艺;若零件的损坏属于非正常的早期破坏,应找出引起失效的原因,并采取相应的措施。如果是材料或其生产工艺的问题,可以考虑选用新材料或新的成型工艺。
2、选材依据
(1)负荷情况
工程材料在使用过程中受到各种力的作用,有拉应力、压应力、剪应力、切应力,扭矩、冲击力等。材料在负荷下工作,其力学性能要求和失效形式是和负荷情况紧密相关的。
在工程实际中,任何机械和结构,必须保证它们在完成运动要求的同时,能安全可靠地工作。例如要保证机床主轴的正常工作,则主轴既不允许折断,也不允许受力后产生过度变形。又如千斤顶顶起重物时,其螺杆必须保持直线形式的平衡状态,而不允许突然弯曲。对工程构件来说,只有满足了强度、刚度和稳定性的要求,才能安全可靠地工作。实际上,在材料力学中对材料的这三方面要求都有具体的使用条件。在分析材料的受力情况,或根据受力情况进行材料选择时,除了考虑材料的力学性能外,还必须应用材料力学的有关知识进行科学的选材。
表1 几种常见零件的受力情况、失效形式及要求的力学性能
工作条件
|
常见失效形式
|
主要力学性能要求
|
应力种类
|
载荷性质
|
其他
|
普通紧固螺栓
|
拉应力
切应力
|
静载荷
|
|
过量变形、断裂
|
屈服强度
抗剪强度
|
传动轴
|
弯应力
扭应力
|
循环冲击
|
轴颈处摩擦,振动
|
疲劳破坏、过量变形、轴颈处磨损
|
综合力学性能
|
传动齿轮
|
压应力
弯应力
|
循环冲击
|
强烈摩擦,振动
|
磨损、麻点剥落、齿折断
|
表面:硬度及弯曲疲劳强度、接触疲劳抗力;心部:屈服强度、韧性
|
弹簧
|
扭应力
弯应力
|
循环冲击
|
振动
|
弹性丧失、疲劳断裂
|
弹性极限、屈服比、疲劳强度
|
油泵柱塞副
|
压应力
|
循环冲击
|
摩擦,油的腐蚀
|
磨损
|
硬度、抗压强度
|
冷作模具
|
复杂应力
|
循环冲击
|
强烈摩擦
|
磨损、脆断
|
硬度、足够的强度、韧性
|
压铸模
|
复杂应力
|
循环冲击
|
高温、摩擦、金属液腐蚀
|
热疲劳、脆断、磨损
|
高温强度、热疲劳抗力、韧性与红硬性
|
滚动轴承
|
压应力
|
循环冲击
|
强烈摩擦
|
疲劳断裂、磨损、麻点剥落
|
接触疲劳抗力、硬度、耐磨性
|
曲轴
|
弯应力
扭应力
|
循环冲击
|
轴颈摩擦
|
脆断、疲劳断裂、咬蚀、磨损
|
疲劳强度、硬度、冲击疲劳抗力、综合力学性能
|
连杆
|
拉应力
压应力
|
循环冲击
|
|
脆断
|
抗压疲劳强度、冲击疲劳抗力
|
(2)材料的使用温度
大多数材料都在常温下使用,当然也有在高温或低温下使用的材料。由于使用温度不同,要求材料的性能也有很大差异。
随着温度的降低,钢铁材料的韧性和塑性不断下降。当温度降低到一定程度时,其韧性、塑性显著下降,这一温度称为韧脆转折温度。在低于韧脆转折温度下使用时,材料容易发生低应力脆断,从而造成危害。因此,选择低温下使用的钢铁时,应选用韧脆转折温度低于使用工况的材料。各种低温用钢的合金化目的都在于降低碳含量,提高材料的低温韧性。
随着温度的升高,钢铁材料的性能会发生一系列变化,主要是强度、硬度降低,塑性、韧性先升高而后又降低,钢铁受高温氧化或高温腐蚀等。这都对材料的性能产生影响,甚至使材料失效。例如,一般碳钢和铸铁的使用温度不宜超过480℃,而合金钢的使用温度不宜超过1150℃。
(3)受腐蚀情况
在工业上,一般用腐蚀速度表示材料的耐蚀性。腐蚀速度用单位时间内单位面积上金属材料的损失量来表示;也可用单位时间内金属材料的腐蚀深度来表示。工业上常用6类10级的耐蚀性评级标准,从I类完全耐蚀到VI类不耐蚀,见表2。
表2 金属材料耐蚀性的分类评级标准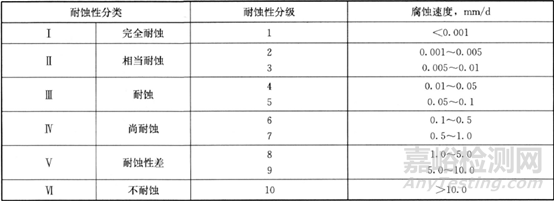
大多数工程材料都是在大气环境中工作的,大气腐蚀是一个普遍的问题。大气的湿度、温度、日照、雨水及腐蚀性气体含量对材料腐蚀影响很大。在常用合金中,碳钢在工业大气中的腐蚀速度为10^-605m/d,在需要时常涂敷油漆等保护层后使用。含有铜、磷、镍、铬等合金组分的低合金钢,其耐大气腐蚀性有较大提高,一般可不涂油漆直接使用。铝、铜、铅、锌等合金耐大气腐蚀很好。
(4)耐磨损情况
影响材料耐磨性的因素如下:
① 材料本身的性能:包括硬度、韧性、加工硬化的能力、导热性、化学稳定性、表面状态等。
② 摩擦条件:包括相磨物质的特性、摩擦时的压力、温度、速度、润滑剂的特性、腐蚀条件等。
一般来说,硬度高的材料不易为相磨的物体刺入或犁入,而且疲劳极限一般也较高,故耐磨性较高;如同时具备较高的韧性,即使被刺入或犁入,也不致被成块撕掉,可以提高耐磨性;因此,硬度是耐磨性的主要方面。另外,材料的硬度在使用过程中,也是可变的。易于加工硬化的金属在摩擦过程中变硬,而易于受热软化的金属会在摩擦中软化。
3、材料成型工艺的选择依据
一般而言,当产品的材料确定后,其成型工艺的类型就大体确定了。例如,产品为铸铁件,则应选铸造成型;产品为薄板件,则应选板料冲压成型;产品为ABS塑料件,则应选注塑成型;产品为陶瓷件,则应选相应的陶瓷成型工艺等。然而,成型工艺对材料的性能也产生一定的影响,因此在选择成型工艺中,还必须考虑材料的最终性能要求。
(1)产品材料的性能
① 材料的力学性能。
例如,材料为钢的齿轮零件,当其力学性能要求不高时,可采用铸造成型;而力学性能要求高时,则应选用压力加工成型。
② 材料的使用性能。
例如,若选用钢材模锻成型制造轿车、汽车发动机中的飞轮零件,由于轿车转速高,要求行驶平稳,在使用中不允许飞轮锻件有纤维外露,以免产生腐蚀,影响其使用性能,故不宜采用开式模锻成型,而应采用闭式模锻成型。这是因为,开式模锻成型工艺只能锻造出带有飞边的飞轮锻件,在随后进行的切除飞边修整工序中,锻件的纤维组织会被切断而外露;而闭式模锻的锻件没有飞边,可克服此缺点。
③ 材料的工艺性能。
材料的工艺性能包括铸造性能、锻造性能、焊接性能、热处理性能及切削加工性能等。例如,易氧化和吸气的非铁金属材料的焊接性差,其连接就宜采用氩弧焊接工艺,而不宜采用普通的手弧焊接工艺;聚四氟乙烯材料,尽管它也属于热塑性塑料,但因其流动性差,故不宜采用注塑成型工艺,而只宜采用压制烧结的成型工艺。
④ 材料的特殊性能。
材料的特殊性能包括材料的耐磨损、耐腐蚀、耐热、导电或绝缘等。例如,耐酸泵的叶轮、壳体等,若选用不锈钢制造,则只能用铸造成型;选用塑料制造,则可用注塑成型;如要求既耐热又耐腐蚀,那么就应选用陶瓷制造,并相应地选用注浆成型工艺。
(2)零件的生产批量
对于成批大量生产的产品,可选用精度和生产率都比较高的成型工艺。虽然这些成型工艺装备的制造费用较高,但这部分投资可由每个产品材料消耗的降低来补偿。如大量生产锻件,应选用模锻、冷轧、冷拔和冷挤压等成型工艺;大量生产非铁合金铸件,应选用金属型铸造、压力铸造、及低压铸造等成型工艺;大量生产MC尼龙制件,宜选用注塑成型工艺。
而单件小批生产这些产品时,可选用精度和生产率均较低的成型工艺,如手工造型、自由锻造、手工焊,及它们与切削加工相联合的成型工艺。
(3)零件的形状复杂程度及精度要求
形状复杂的金属制件,特别是内腔形状复杂的零件,可选用铸造成型工艺,如箱体、泵体、缸体、阀体、壳体、床身等;形状复杂的工程塑料制件,多选用注塑成型工艺;形状复杂的陶瓷制件,多选用注浆成形或注射成型工艺;而形状简单的金属制件,可选用压力加工或焊接成型工艺;形状简单的工程塑料制件,可选用吹塑、挤出成型或模压成型工艺;形状简单的陶瓷制件,多选用模压成型工艺。
若产品为铸件,尺寸要求不高的可选用普通砂型铸造;而尺寸精度要求高的,则依铸造材料和批量不同,可分别选用熔模铸造、气化模铸造、压力铸造及低压铸造等成型工艺。若产品为锻件,尺寸精度要求低的,多采用自由锻造成型;而精度要求高的,则选用模锻成型、挤压成型等。若产品为塑料制件,精度要求低的,多选用中空吹塑;而精度要求高的,则选用注塑成型。
(4)现有生产条件
现有生产条件是指生产产品现有的设备能力、人员技术水平及外协可能性等。例如,生产重型机械产品时,在现场没有大容量的炼钢炉和大吨位的起重运输设备条件下,常常选用铸造和焊接联合成型的工艺,即首先将大件分成几小块来铸造后,再用焊接拼成大件。
又如,车床上的油盘零件,通常是用薄钢板在压力机下冲压成型,但如果现场条件不具备,则应采用其他工艺方法。例如,现场没有薄板,也没有大型压力机,就不得不采用铸造成型工艺生产;当现场有薄板,但没有大型压力机时,就需要选用经济可行的旋压成型工艺来代替冲压成型。
(5)充分考虑利用新工艺、新技术、新材料的可能性
随着工业市场需求日益增大,用户对产品品种和品质更新的要求越来越强烈,使生产性质由成批大量生产变成多品种、小批量生产,因而扩大了新工艺、新技术、新材料的应用范围。
因此,为了缩短生产周期,更新产品类型及质量,在可能的条件下就大量采用精密铸造、精密锻造、精密冲裁、冷挤压、液态模锻、超塑成型、注塑成型、粉末冶金、陶瓷等静压成型、复合材料成型、快速成型等新工艺、新技术、新材料,采用无余量成型,使零件近净型化,从而显著提高产品品质和经济效益。
除此之外,为了合理选用成型工艺,还必须对各类成型工艺的特点、适用范围以及成型工艺对材料性能的影响有比较清楚的了解。金属材料的各种毛坯成型工艺的特点见表3。
