探究半导体失效的原因通常需要去除覆盖层材料,以暴露出失效的电路元件,以便在电子显微镜(EM)中进行高分辨率成像。机械切割和抛光等处理技术会诱导机械应力而产生额外的缺陷,并且与离子研磨技术一样,它们缺乏所需的定点特异性。
聚焦离子束(FIB)可以在特定地点进行加工,但是对大型加工任务而言非常缓慢。利用激光刻蚀除去需要位点周边的绝大部分物质,然后采用FIB切割抛光获得横截面,这两方面技术的结合最终达到超大尺寸样品加工要求的速度与精度。这一结合的最新发展阶段就是利用激光刻蚀与PFIB刻蚀协同处理以进一步提升分析通量,效率与灵活性。
FIB系统广泛用于制备电路元件截面,以便电子显微镜等仪器的后续分析。FIB技术具有纳米级精度和可精准操控性,这使得操作者能够对电路中微小特征精准测试分析。然而,高精度降低了FIB的铣削速率,特别是镓(Ga)源FIB,在去除覆盖材料的过程中速度缓慢和时间漫长。等离子体源(PFIB)早在十年前就已推出市场,PFIB束流高于传统液态镓源束流速度,从而提高FIB铣削速率的同时也获得铣削精度上可以接受的妥协。但在同一时期,随着设备制造商开发出先进的异构集成和封装技术,将多个芯片集成封装在一起,故障分析面临的挑战也越来越大。封装时感兴趣区有可能藏于数层电路或者数个晶体管下,为解析感兴趣区所必需移除之覆盖层体积已经由立方微米至立方毫米剧增,同时元件自身也逐渐变小。
激光刻蚀提供的最大铣削速率比镓源FIB快约100,000倍,比PFIB快约2,000倍,同时仍保持针对特定位点的足够铣削精度。将激光刻蚀(初始切削材料)与PFIB(最终切割和抛光)相结合可以将制备大尺寸横截面所需的总时间减少95%,在某些情况下甚至更多。如图1显示了镓源FIB、PFIB和激光刻蚀的光斑大小与材料去除率之间的关系。相邻表格提供了这3种技术在最大铣削和最终抛光束流条件下材料去除率的数值比较。
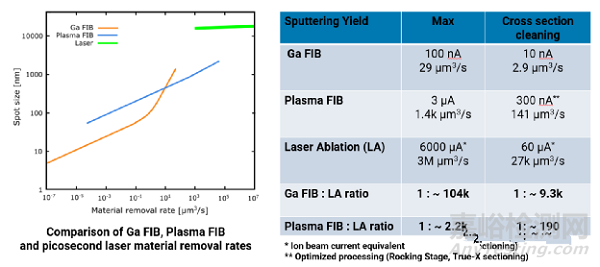
图1
如图1:(左)所示,镓源FIB、PFIB和激光刻蚀占据不同的区域,其特点是光斑尺寸(光束直径)和材料去除率之间的制衡。一般来说,较高的束流或束流强度会更快地去除材料,但精度较低。表格(右)比较了材料在三种技术下最大束流和典型抛光条件下的束流(或激光的离子束等效电流)和材料去除率关系。此外,还显示了镓源FIB与激光刻蚀、PFIB与激光刻蚀的去除率之比。
第一个将激光刻蚀与FIB集成的系统是通过将激光集成到FIB室中实现的。在这种配置下,系统一次只能使用一个功能,而其他功能处于空闲状态。我们运用了一种新方式来实施集成显微镜技术,通过独立的激光刻蚀(microPrep PRO、3D-Micromac AG)和PFIB(TESCAN Solaris X)系统提供并行处理。这两种系统均不因其他系统工作而闲置。激光刻蚀系统能够制备多种联用工具的试样,不管它们组合在一起的是多种FIB或其他多种故障分析仪器。最后结果均为提高分析通量及产率,减少各次分析之费用。
激光刻蚀系统提供约10微米的铣削精度(束斑尺寸)和厘米距离内约3微米的光束定位精度,使其快速准确地去除立方毫米的材料。基于电路设计的CAD数据或各种FA工具的2D图像叠加的相关对准技术有助于在两个系统中以高精度找到感兴趣区。独立系统中的并行处理有几个好处,超短激光脉冲最大限度地减少了激光引起热影响区,从而减少了必须通过PFIB中的最终抛光去除的材料量。单独在激光刻蚀系统中切削材料可避免PFIB仓内污染的风险,其中污染物会干扰仪器本身和分析结果。试样可同时在多种气体环境下被激光加工,并可采用解决方案使系统间发生传递而不与周围环境接触。激光刻蚀工具中的平台为精确的自动化运动提供了6个自由度,从而可以在必要的情况下实现复杂图案的铣削。激光刻蚀时倾斜样品的容量对补偿光束能量高斯强度分布所造成的锥度尤为有利。尽管它可以使用FIB抛光消除,但在激光刻蚀操作期间避免它可以大大减少FIB抛光所需的时间。消除锥度对半导体样品横截面(例如TSV、锡焊球等)过程中堆叠重复结构精确对齐是非常重要的。
PFIB系统针对高深度大尺寸铣削进行了优化,它提供高达3µA的束流,每秒可去除多达1,400µm3的材料。用于最终抛光的较低离子束电流(300nA)仍可去除高达141µm3/s,即使在具有挑战性的样品上也能提供原始横截面。最具挑战性的样品是那些需要不同切削速率的硬质和软质复合材料的样品。较硬的材料切削得慢,往往会遮挡下面的区域,产生独特的垂直形貌,描述性地称为“窗帘”。复合材料中较硬纤维或颗粒散布于较软基材上(金属互连,Si与半导体样品电介质等)所产生的窗帘伪影,可能掩盖了后续图像的关键细节。切削操作时,我们可藉由小角度重复摆动试样可降低窗帘的伪影。角度的微小改变使得离子束能很好的进入到材料下较坚硬的屏蔽区域并且光滑铣削过程。窗帘效应对束流/铣削速率很高的FIB来说可能是个挑战,正如大通量工作流程高速铣削需要的那些。针对这一问题,配置在PFIB系统中的摆动台给出了可解决的自动摆动模式。
在某些材料中,包括碳化硅、聚酰亚胺、玻璃等,产生的阶梯是另一种伪影。这是由于材料的去除率与离子束的入射角有关。去除率通常在切线入射时最高,如在横截面的表面,而在垂直入射时最低。复合材料中较硬纤维或者颗粒分散在较软基材(金属互连、Si和半导体样品的电介质,等等)中造成窗帘伪影可能会掩盖后续影像中的关键细节。在切削操作中,通过小角度反复摆动样品可以减少窗帘伪影。角度的细微变化使离子束能够很好地进入材料下较硬的屏蔽区域,平滑了铣削过程。窗帘效应对于束流/铣削速率较快的FIB而言可能是一个挑战,就像大通量工作流程中高速铣削所需的那些。为了解决该问题,PFIB系统上配置的摆动台提供了一种可以求解的自动摆动模式。
具体案例
图2至图6显示了使用激光刻蚀和PFIB来曝光电路元件以进行成像和分析的示例。每个示例都包括每次操作所花费的时间以及相对于单独使用PFIB制备样品所节省的总时间。
1.先进芯片集成
图2
图2:中间的图像显示了一个超大的横截面,宽几百微米,深几百微米,穿过集成电路和连接到插入器的焊锡球和触点。左边和右边的图像显示了该截面的细节,左边是IC的放大倍数更高的图像,右边是锡球和接触垫之间的空隙。横切过程在激光刻蚀仪器中耗时10分钟,在PFIB中耗时90分钟,与单独使用PFIB相比节省了70%的时间。
2.锥度校正
图3
图 3:(右)显示了在高带宽存储器(HBM)器件中硅穿孔(TSV)堆栈的数百微米深和宽的横截面,它说明了系统切割贯通每个TSV中心的精确垂直横截面的能力。在激光刻蚀过程中倾斜样品以补偿锥角对于减少最终PFIB铣削操作要去除的材料量至关重要,从而减少横截面所需的总时间。横截面在激光刻蚀仪器中耗时10分钟,在PFIB中耗时120分钟,与单独的PFIB相比,节省了80%的时间。
3.FIB层析成像的激光刻蚀准备
图4
图4:FIB的层析成像通过FIB逐层切片的方式,从捕获的一系列图像中重建了样本体积的3D模型。准备工作首先使用激光刻蚀从一个立方体/矩形体的三面去除材料,如“俯视图”(左)所示。在此视图中,最终将与FIB连续剖切的面位于立方体形状的底部。在“正视图”(中间)中,样品已旋转90°以显示横截面。插图(右)放大了横截面的一个区域以显示其切削质量。使用激光烧蚀制备样品需要10分钟,与PFIB 相比节省了70%的时间。
4.有机发光二极管面板
图5
图5:手机和其他移动设备的显示器含有关键的微结构,在样品制备过程中容易被机械应力损坏。这种精致的样品需要一种特殊的处理方法:在PFIB进行最后切削和抛光之前,在边缘的一个几毫米长的区域被有意地用激光削尖。左上方的第3张图像显示了激光刻蚀切口。下图显示了经过PFIB切削和抛光后长约0.5mm截面(PFIB可以切割和抛光长达1mm的截面)。最右边的顶部图像显示了最终横截面的更高倍放大图。横切面在激光刻蚀中花费了74分钟,在PFIB中花费了165分钟,与单独PFIB相比节省了95%的时间。
5.微机电系统
图 6
图 6:MEMS设备对样品制备过程中的机械损伤特别敏感。在这个例子中,激光刻蚀被用来打开一个窗口,进入封装的 MEMS 设备进行检查和分析。
在一个封装内互连多片的高级异构集成与封装工艺应用正急剧增加。对这些封装的失效分析,一般都要求将覆盖材料从指定位置去除,以便揭露可疑电路,以便对其检查分析。需要清除的物质数量可能会非常大。FIB系统虽然有针对特定电路元件所要求的精度,但速度较慢,特别是在使用镓源时。在PFIB快了很多,但是对高级异构集成与封装需要大截面仍将视为慢。激光刻蚀的速度很快但是不准确,不能针对单一的电路元件进行纳米精度的刻蚀。采用激光刻蚀除去绝大部分材料,利用FIB刻蚀抛光最后横截面,可极大地减少制备所用总时间。在FIB系统中植入激光刻蚀功能的体系实质上效率不高,原因在于每次仅能利用一个功能。
这项技术的最新迭代是在单独激光刻蚀与PFIB上并行处理的,它通过允许在这两种工具上同时处理而增加通量与产率。通过有关图像对齐程序,并与CAD叠加导航相融合,实现了上述工具。并行配置时,一台激光刻蚀系统可提供多台FIB等FA工具。该方法的优点是消除了污染FIB系统所带来的危险,即污染物对成像产生干扰并对系统进行分析或者破坏。我们演示了一些大型而优质的横截面实例,并且计算了比单独用PFIB准备所节省的时间。所示实例所节省的时间由70%至95%不等。