文献阅读
一篇来自FDA的CDBR专家的文献,讲述了使用实验设计(DoE)开发关键质量属性的设计空间的几种情况,并分别作了分析,非常具有参考和学习价值。
因子筛选
文献中,作者选择研究的关键质量属性为糖型,首先通过风险评估方法对工艺参数变量进行筛选(风险评估过程未展示),最终确定了11个潜在有影响的工艺参数。因此,后续DoE实验的因子和响应为:
实验设计和分析
因为有11个因子,作者选择的实验设计方法为Plackett-Burman设计,该设计拥有最小的实验次数,但是也存在更多的效应混淆。但是对于较多的因子,确是比较合理的选择。
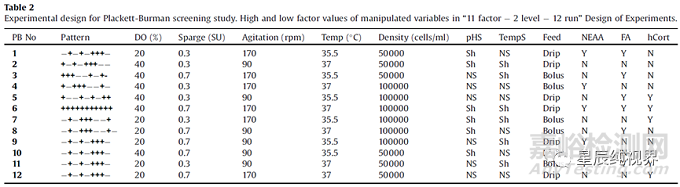
作者使用的Modde软件,按照设计的顺序进行实验,获得糖型分析结果后,对结果数据进行分析。常规分析思路还是遵循DoE的分析方法,比较R2,Q2,模型有效性和再现性,以及残差等指标。
与常规分析不同的是,作者引入了质量标准范围,从而建立了自己的一套建构设计空间的思路。该思路值得细细品味。
根据本文献的实验数据和分析思路,建构设计空间的思路可以主要分为以下四种情形,作者分别一一作了介绍。
情形1:质量标准范围内+显著模型
此类情形是最有利,所有实验运行的结果均在质量标准范围内,同时又具有一个显著的预测模型。上述案例中的CQA-G2即是此类情况。
以G2作为响应,模型的四个指标均符合要求,并且所有实验结果均在质量标准内。该显著的预测模型可以获得具有显著性影响的工艺参数,同时可以建立G2与显著性工艺参数之间的响应曲面图,如果需要还可以进行稳健性分析。
情形2:质量标准范围内+非显著模型
该情形是指所有实验运行的数据均在质量标准范围内,但是却无法建立具有显著性的预测模型。G2FaGbGN即为该中类型。
无法建立显著性预测模型的原因主要有(1)重复性实验数据较差;(2)PB设计的固有问题,即较低的自由度无法分析所有的效应,也就是交互效应无法分析。
尽管无法建立显著的预测模型,但是所有结果均在质量标准范围内,也就是可以构建现有所研究的工艺参数的设计空间,即现在工艺参数的研究范围。但是工艺参数的显著性以及响应曲面图和稳健性评估则无法进行。
情形3:质量标准范围外+显著性模型
该情形是指一部分的实验运行结果超出了质量标准范围,不过可以获得一个具有显著性的预测模型。G0的实验结果数据属于该类型。
部分实验运行结果超出质量标准意味着需要对工艺参数进行进一步的控制,但是显著的预测模型可以获得具有显著性的工艺参数,同时响应曲面图可以获得这些工艺参数的设计空间,利用Modde软件的蒙特卡洛模拟功能还可以进行设定点分析和稳健性评估。
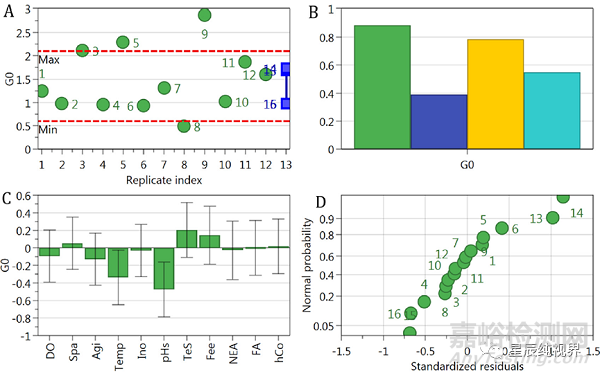
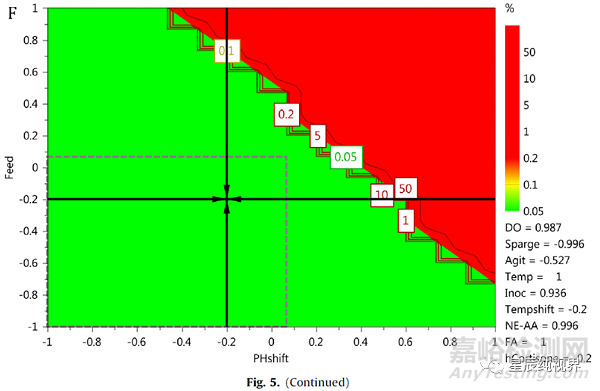
情形4:质量标准范围外+非显著性模型
该情形是指部分实验运行的结果超出了质量标准范围,但却无法建立一个具有显著型的模型。关键质量属性G2FaG2属于此类型。
该情形是最不幸运的情形,因为有超出质量标准范围的结果,但是却没有一个好的预测模型来构建设计空间,因此这意味着需要另外的实验重新建立模型,否则工艺风险会很大。
造成该情形的原因主要包括因子筛选不合适,实验过程的重复性较差或存在实验错误。需要具体问题的具体分析。
总结
本篇文献以糖型为响应,进行了DoE实验设计和分析,详细介绍了DoE结果和分析的四种不同情形,以及四种情形下设计空间的构建和分析。本篇文献为质量源于设计(QbD)的实施提供了很好的思路,非常具有借鉴和学习意义。
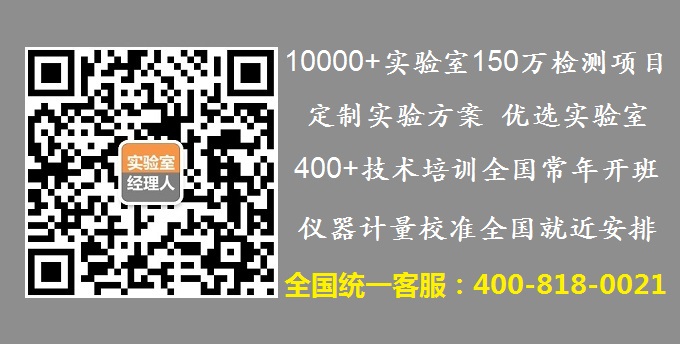