氢气具有清洁、质量 / 能量密度高的优点,是一种高效的能量载体;在高碳排放工业、电力领域中替代煤炭、天然气等化石燃料,应用前景十分广阔。发展具有波动性负荷跟随能力的质子交换膜(PEM)电解水技术,是实现可再生能源耦合电解水制氢、促进可再生能源消纳的有效途径。
中国工程院院刊《中国工程科学》2023年第6期刊发北京智慧能源研究院高级工程师彭笑东研究团队的《风光波动电源下质子交换膜电解水制氢技术发展与应用》一文。文章围绕风光波动电源下电解水高效制氢技术的发展与应用,从风光波动特性及制氢方式、PEM电解水制氢特性及衰减机制、制氢应用现状、关键技术研发等方面,系统探讨风光波动电源耦合制氢存在的问题,以期为相应技术发展和产业应用研究提供基础参考。
一、前言
全球变暖趋势更为明确,开发清洁能源能够缓解使用化石燃料产生的大量温室气体排放,因而开发风能、太阳能等可再生能源对人类社会可持续发展具有重要意义。可再生能源具有很强的时空依赖性、间歇性、波动性等特点,在并网中也面临着可靠性和调峰调频的难题。因此,将可再生能源电力转化为化学能储存后再进行应用,更具灵活性,是源、网、荷协调发展的有效途径。
氢气具有清洁、质量 / 能量密度高的优点,是一种高效的能量载体,可在高碳排放工业、电力等领域中替代煤炭、天然气等化石燃料,应用前景广阔。可再生能源电解水制氢是实现可再生能源消纳、氢能绿色制取的有效途径,常见技术有碱性电解水、质子交换膜(PEM)电解水、阴离子交换膜电解水、固体氧化物电解水。其中,PEM电解水技术具有较高的电流密度、效率(80%~90%)、气体纯度,较低的能耗和体积,较好的安全可靠性。开展PEM电解水技术研发是支持实现可再生能源电力耦合制氢的重要内容。
也要注意到,可再生能源如风电、太阳能发电等具有波动性和间歇性的天然特征,发展适用于负荷频繁波动的可再生能源电力电解水技术是风电、太阳能发电耦合制氢的关键构成。PEM电解水技术在理论上具有一定的波动性负荷跟随能力(可在30%~120%额定制氢功率范围内运行),但缺乏工程示范和商业运行验证。为了模拟可再生能源电力制氢,研究过程中采用的模拟工况有恒电流、波动工况、启停工况等。在风光波动电源工况下,电解池内的电极电位、析氢速率、温度等参数发生瞬态变化;由于两相流动等传质过程的滞后效应,快速、频繁、大幅度负荷波动工况将导致局部高温、高电势以及局部应力,对电极、交换膜、双极板等部件造成潜在的不可逆损害,进而影响系统工作寿命。目前,国内外对电解槽在波动工况下的运行特性、部件衰减机制等都开展了不少研究,但未能针对风光波动电源下PEM电解水制氢开展系统的梳理和分析。
文章围绕风光波动电源下电解水高效制氢技术的发展与应用,从风光波动特性及制氢方式、PEM电解水制氢特性及衰减机制、制氢应用现状、关键技术研发等方面,系统探讨风光波动电源耦合制氢存在的问题,以期为相应技术发展和产业应用研究提供基础参考。
二、可再生电力风光波动电源制氢场景
可再生能源电力的主流形式是风电和光伏发电,具有波动性强的固有属性。分析风光电力的波动特性,才能为风光波动电源下电解水制氢技术发展辨明基础条件(见图1)。
图1 风电、光伏发电耦合制氢示意图
(一)风电耦合制氢
风电耦合制氢主要分为并网型、离网型。对于并网型风电,电网通过能源管理系统实现电压、频率控制,确保电解池在较稳定的电压下制氢;相应并网方式主要有同步风电并网、异步风电并网两种。并网型风电耦合制氢主要有3种应用场景:利用富余风电制氢,起到电网“削峰”作用;借助氢能并通过燃料电池等技术发电,起到电网“填谷”作用;利用电网供电解决风电的间歇性问题,增强制氢系统的稳定性和可靠性。
离网型风电相较于并网方式,省去了并网辅助设备,可以避免并网带来的问题,降低了制氢成本。特别是对于海上风电而言,采取离网发电方式可有效解决电力输送的问题;石油和天然气传输基础设施可兼作海上风电制氢的输送通道,使相应管道的投资成本显著下降。通常,离网型风电耦合制氢主要有两种应用场景:获取的氢气通过输气管道或运氢船输出,由风电、变换器、电解槽、储氢设备、燃料电池等构建微网系统。
(二)光伏发电耦合制氢
光伏发电耦合制氢也可分为并网型、离网型。并网型光伏发电耦合制氢将光伏组件产生的电能并入电网,再从电网获取电能进行电解水制氢,常用于大规模弃光消纳和储能;离网型光伏发电耦合制氢指将光伏组件产生的电能直接供给电解槽制氢,主要用于分布式制氢。光伏发电耦合PEM电解水制氢技术主要采用光伏直流-直流变换间接耦合、光伏直接耦合两种途径。
1. 光伏直流-直流变换间接耦合制氢
光伏发电的输出功率受太阳辐射、环境温度、外界负载等多重因素的影响,难以直接为负载提供最佳功率。通常在光伏组件与电解池之间加入直流-直流变换器,更好匹配光伏电压与电解池电压,进而提高制氢效率。常用的手段是最大功率密度跟踪,如利用脉冲宽度调制技术调整占空比以跟踪最大功率点、调节变换器输出电流的鲁棒控制等。尽管直流-直流变换器能有效提高制氢效率,但变换器产生的纹波会导致输入电流的电平判别错误,进而影响电解池的工作效率;直流变换产生的损耗增加了运行成本,对制氢系统的持久性和装置寿命也会产生影响。
2. 光伏直接耦合制氢
光伏发电器件与电解池的直接耦合精简了光伏发电耦合制氢系统的复杂度。例如,光伏电解系统由2个PEM电解池与三结节太阳能光伏电池直接连接构成,可产生足够的电压来维持基于太阳能光伏电池的电解池制氢过程;调整光伏最大功率密度点与电解池进行匹配,可使得太阳能-氢的转化效率高达30%。然而,直接耦合下光伏电池的电压、电流波形直接作用于电解池,对电解池的长时间安全稳定运行构成了挑战。
(三)可再生能源的波动特性
风电负荷波动的频率范围较大,较大频率尺度平滑作用不显著。风力发电受风速影响较大,发电量与风速之间的非线性关系使得分析过程更为复杂。风速、风向和发电量在不同时间段有着显著的差异性。在时间尺度上,风力发电模式在日、月和不同季节都会发生变化。近年来,不少研究者探索建立理论模型对风力发电量进行更精细的预测,已建模型考虑了湍流的空间变化、风轮自身产生的湍流影响以及这些因素之间的相互作用。虽然已经采用聚类方法对风速的时间序列数据进行了比较和分类,但由于风力发电的波动特性与风力机惯性、偏航 / 俯仰角控制等因素密切相关,尚未形成相应波动模式的分类。风力机电力输出与风速的三次方成正比,因而详细了解风特性至关重要。风特性可由风速谱来描述,数值越大表明风速在相应时间段内发生了越显著的变化;一般也认为多台风力机并机时产生的波动幅度将显著降低。在1~2 km范围内的6个点位,利用多个风速数据进行分析,发现在快速波动区域出现了平滑效应,而在超过10 min的波动区域几乎没有观察到平滑效应。
光伏发电负荷波动主要表现为昼夜周期特性。光伏发电在稳定的太阳辐射条件下产生较高的发电量、较低的太阳辐射波动率(< 50 W/(m2·min)),而在不稳定的太阳辐射条件下产生较低的发电量、较高的太阳辐射波动率(> 150 W/(m2·min))。预测光伏发电需要了解太阳辐照模式(按天划分),目前常用时间序列数据进行分类,如聚类方法、样本熵分析、分形维数等。在3 km范围内采用9个光伏发电并机,可显著降低晴天条件下的波动幅度,甚至在多云天气下的波动幅度也可降低50%以上。因此,增加光伏电站的数量及规模可以降低光伏发电的波动幅度。
风电和光伏发电均可通过多台机组并机的方式降低发电的波动,但依然无法避免因风力或者太阳辐照变化导致的电力输出波动,这就对制氢系统产生了波动性负荷输入。在较短的时间尺度下,风电表现为分钟级到小时级的随机波动,光伏发电则为基本的昼夜周期特性(见表1)。
表1 风光电力耦合制氢的方式及特点
三、风光波动电源下PEM电解水制氢的基本特性
在风光波动电源下,电解池的工作参数发生瞬态变化,可对主要部件造成不可逆损害。探究风光波动电源下PEM电解水制氢的性能特点、PEM电解槽部件的衰减机理和评估手段,对PEM电解槽部件关键技术研发具有重要价值。
(一)风光波动电源对电解池影响显著
通常,电解池的输入电压会被控制在一定范围内;当电解池输入功率波动时,电解池电压发生小幅度变化,而电流出现显著波动。在实际应用中采取稳压控制时,一旦电解池输入功率发生变化会带来电流的急剧波动,进而引起电极反应速率的急剧变化,使电解池偏离稳定工况。由于电极反应过电位的存在,电压输入明显高于理论电压;尽管电解水反应是吸热反应,但因欧姆损耗产生焦耳热,使电解池即便在稳定电源工况下温度也会随着时间的推移而逐渐升高。从模拟风电条件下的电解池工作特性可见,瞬态运行条件下温度随着发电功率波动而变化。电解池温度下降后,电极反应速率变慢、效率降低。增加功率导致温度上升,电极表面氧气、氢气产率的增加导致电极表面附着气泡,从而增大催化剂层离子传递阻力、降低有效反应面积,进而产生更高的反应过电位,导致电解池电压升高。气泡的附着和流动也导致电解液在电极表面的供给不均衡,引起电极表面反应不均匀、局部热点。
电解池内的气体互窜现象也会产生安全问题。当氧气中的氢气浓度达到4%时,构成的混合气体即可发生爆燃,故实际运行过程中一般将氧气中的氢气阈值设为2%。通常,随着电流、产气速率的变化,阴 / 阳极气体浓度与压力会发生波动;尤其在较低的电流密度下,阴 / 阳极气体产率降低,气体互窜现象加剧。电解槽运行的温度、压力同样会对气体互窜产生影响。增加膜的厚度可以有效缓解气体互窜问题,带来的负面效应则是增加欧姆内阻与离子传输阻力。加入额外电极、引入阴极水循环等方式可加速去除电极表面的氢气,从而缓解气体互窜问题。
目前研究对于气体互窜问题更多是从运行工况上进行调控,以将气体互窜抑制在安全范围内。对光伏 / 风能驱动的60 kW PEM电解池进行能耗研究发现,变压吸附除湿的能量损失最高,辅助设备和交流 / 直流转换器的能量损失次之,这些能量损失导致电解水过程的效率急剧下降;为了调控运行工况而需额外配备辅助设备,如储能模块、氢气压缩机等,提高了系统成本并增加了系统复杂度。随着新能源规模的快速发展、电解水制氢技术的不断迭代,定制化功能模块和制氢系统的集成度进一步提高,有利于稳步提升制氢系统综合能效。引入以人工智能为代表的信息技术,可精确预测新能源利用过程中的波动参数,将更加智能地优化电解水制氢系统的全特性运行指标、全生命周期的能量管理策略,更深入地考虑太阳辐照变化、风力季节性变化、电网负荷波动等因素的影响。
风电、光伏发电具有不同的周期和输出功率波动。研究和模拟风光电力制氢,常见的模拟工况有恒电流、波动工况、启停工况。近年来,对恒电流工况的研究比较充分,取得了一些共识性的结论。关于组件的老化和性能衰减,高电流密度要比低电流密度严重得多。通常采用恒电流测试催化剂的耐久性,一般也认为大多数催化剂的稳定性良好,但恒电流条件难以反映实际PEM电解池的运行工况。近年来,一些学者通过不同波形的脉冲电源对PEM电解池进行测试,以研究脉冲电源对PEM电解池的影响:脉冲电压能有效增加电解电流,促进气泡在电极表面的输运和电解离子的传质速率,从而提高产氢效率;不同类型的脉冲电压、电流条件可有效强化电解水效率,脉冲电源电解水可以降低功率输入、保持最低的电流水平以防止气体互窜。也要注意到,尽管脉冲负荷对电解水制氢有利,但实际风光波动电源下电解池参数的瞬态变化可能产生局部应力,将显著影响系统寿命。
近年来,风光波动电源对电解池性能衰减或老化的影响课题,尽管得到了国内外学者的较多关注,但一些结论存在分歧。通过PEM电解池的500 h持久性测试,明确了不同运行模式下的电解池性能特性,发现在快速循环运行模式(模拟光伏发电)下,随着欧姆电阻的减小,电解池性能反而得到提升。在PEM电解池1000 h耐久性测试后发现,电解池性能衰减速率为194 μV/h,78%的衰减来源于阳极-多孔层欧姆电阻的增加;在风光波动电源条件下电解池性能衰减得到明显缓解,这是因为风光波动电源使可逆的降解部分恢复,弱化了电极降解问题。不同输入特性下电解池性能的长期稳定性及其衰减机理等,仍需进一步研究。
(二)风光波动电源加速电解池部件衰减
1. 催化层
电解池催化层一般由催化剂(如Pt、RuO2、Ir、IrO2等贵金属)和黏合剂(如全氟磺酸)构成。为了增强耐久性,催化层通常负载部分导电载体材料,如TiO2、SnO2、Ta2O5、Nb2O5、Sb2O5、TaC、TiC。上述催化剂能够满足PEM电解池的高性能要求,但恶劣操作工况下的耐久性难以令人满意(见表2)。阳极在低催化剂负载条件下性能衰减更严重,相应衰减机制主要有溶解、团聚、载体钝化等模式。对PEM电解池进行长达5500 h的持久性测试后发现,催化层腐蚀、Pt催化剂降解是导致性能衰减的主要因素。通过高电流密度下PEM电解池电极的持久性能研究发现,高电压下Ir催化剂易形成可溶性配合物,而RuO2虽然具有更高的催化活性,但在PEM电解池内降解速率更快;稳定的IrO2在高于1.8 V电位时开始转变为可溶性Ir。研究阐明了铱溶解的机理,Ir(OH)3或Ir2O3存在不稳定性,Ir(Ⅲ)络合物的形成导致催化剂的溶解,进而产生电极性能衰减。采用透射电子显微镜揭示了铂迁移与过电位之间的关系,较低的电位增强了铂迁移,导致铂聚集物的形成;1000 h的耐久性测试表明,Pt纳米颗粒不断团聚,平均粒径从2.35 nm增大到2.85 nm。研究了电流密度对PEM电解池性能衰减的影响规律,发现高电流密度下产生了不可逆降解反应,在钛集电器与阳极催化层之间产生的低电导率氧化物,使欧姆阻力增加、电解池性能显著降低。值得指出的是,PEM电解池高电流密度与风光波动电源叠加,使电极表面的反应速率、气体产物生成速率发生急剧变化,导致催化层表面的冲刷和压力急变,也可能进一步加剧催化层的溶解和脱落。
2. 交换膜
在传统的PEM电解池中,交换膜用于分隔气态反应产物、质子输运,支撑阴极和阳极催化层,需要具有优良的化学稳定性、机械强度、热稳定性、质子电导率等特性。交换膜的性能衰减主要源于膜污染或化学降解。从安全性、可靠性角度看,膜的耐久性对于电解池至关重要,膜的破损可能致使产生的氢气和氧气直接混合。交换膜降解机制主要分为机械降解、热降解、化学 / 电化学降解3种(见表2)。
表2 电解池部件性能衰减机理及缓解措施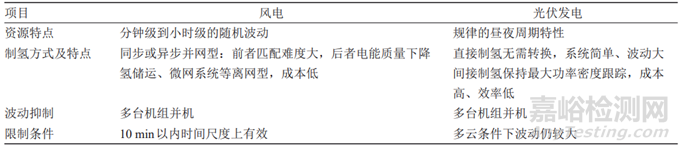
交换膜早期失效通常由穿刺、撕裂、机械应力等因素导致机械降解而引起。在膜电极制作及运行过程中,外来材料、预紧力、局部应力等因素可使交换膜出现撕裂或者微裂纹断裂。例如,两端的金属集电器不均匀压紧将加剧膜的变形,扩散层粗糙度也会直接影响膜的耐久性。在波动工况下,运行压力、局部温度反复变化产生的局部应力等,也会导致交换膜的机械损伤。
交换膜化学 / 电化学降解主要源自自由基作用导致交换膜变薄以及金属毒化。金属离子(如Li+、Ca2+、Cu2+、Ni2+、Fe3+)是常见的膜毒物,交换膜离子电导率不可避免地受到金属离子置换的影响,即使微量的金属离子也能显著降低膜的液相电导率。相应毒降解机制可归纳为以下步骤:金属离子通过扩散和渗透溶解到膜中;金属离子占据膜的离子交换位点;膜内金属离子的迁移率远低于质子,产生更高的欧姆损失。前期研究证实,Fex+对PEM磺酸位点的亲和力高于H+,随着过电压的增大,质子浓度、电导率、有效三相界面随之减小。
电解池通常需维持一定的温度(60~80 ℃)以实现较高的电解效率,水热环境下的膜稳定性和耐久性是影响电解池耐久性的重要因素。热降解可能导致交换膜中磺酸成分的丧失,影响交换质子传导能力并增大电压损失。采用实时在线测量方式研究了不同温度下、不同厚度膜电极中膜降解导致的氟释放速率,发现较高的温度导致更高量的氟离子释放,从而加快交换膜的老化。
3. 双极板
双极板是电解池的多功能组件,以有效传导电子、提供反应物 / 产物输运的通道,保持设备的机械稳定性和完整性,作为热管理的组成部分;作为电解池的主要部件,成本约占PEM电解池的48%,其设计制造应满足高导电性、耐腐蚀性、低成本、高机械强度的要求。然而,电解池阳极具有高的过电位(1.6~2.0 V)、低的pH(2~4),对双极板的抗腐蚀和抗氧化能力提出了较高要求。石墨因其高导电性而适用于燃料电池,但石墨用作电解池双极板存在制造难度大、机械强度差、成本高、腐蚀率高的问题。在电解池阳极中,碳腐蚀减小双极板厚度,导致膜电极与集电器之间的接触电阻增大、电解槽性能下降。PEM电解池常见的衰减机制有氢脆、钝化、腐蚀等,主要采用抗腐蚀性金属(如钛、不锈钢)来增强服役适应性(见表2)。采用真空等离子体喷涂工艺,在不锈钢表面制备致密的钛涂层,由电化学腐蚀实验表明钛涂层可以保护双极板免受腐蚀。然而,波动工况下双极板表面金属镀层反复氧化和还原,也在交换膜降解产生F-条件下出现更恶劣的表面腐蚀,使双极板的耐久性下降更明显。风光波动电源下电压 / 电流变化导致电解池温度的不均匀或急剧变化,产生应力分布不均或反复的应力变化,导致接触电阻增大、机械性能劳损,最终影响电解池的耐久性。
(三)风光波动电源模拟方式
开发电解池及其组件的加速衰减测试、寿命评估和耐久性研究方案,有助于评估材料的衰减行为并更好了解材料的衰减机制。PEM电解池的耐久性主要在特定的温度、压力条件下通过恒定电流进行评估,电解池寿命测试时间较长(>4×104 h),相应耐久性评估成本偏高。目前,还没有形成标准化和普遍接受的PEM电解池组件耐久性评估方式。欧洲的学术界和产业界长期致力于表征、测试、评估电解池的性能、效率和耐久性,积累了较丰富的经验,代表性的工作有:利用加速应力测试方法,评估了PEM电解池中的膜化学稳定性;研究了不同风光波动电源输入波形对PEM电解池降解的影响,认为方形波、锯齿波电源显著加速电极降解;提出通过恒定电流、开路电压模拟电解池启动、停机运行方式,发现开路条件可加速电解池性能衰减。一般认为,加速衰减通常与电流密度、压力、温度有关,而风光波动电源下电解池加速衰减测试方法、相关标准化实施方案等依然缺乏,单一因素条件下的测试手段难以综合评估风光波动电源下电解池的衰减特性。
四、PEM电解槽核心技术研发与PEM电解槽制氢技术发展方向
(一)PEM电解槽技术研发
风光电力制氢的功率波动范围较大,对制氢装置产生的不利影响表现为大幅降低装备寿命、影响制成氢气的纯度,这些影响源自风光波动电源工况下PEM电解槽主要部件的衰减。从技术角度看,PEM电解槽面临的主要挑战是如何通过材料研发、组装工艺及优化等提升工作性能与稳定性。先进材料研发包括催化层和黏合材料、防腐蚀双极板、有机离子交换膜等方向。电解槽部件组装工艺及优化主要有膜电极制备方式优化、电解槽装配预紧力优化、膜电极 / 电解槽温度和热应力分布优化、流道优化等,近年来以膜电极作为PEM电解槽的重点研究方向。
围绕电解槽催化剂、交换膜、双极板等主要部件,开展催化剂研发的主要途径有:通过二元或多元金属复合掺杂,提高催化剂的活性和稳定性;选择耐氧化、比表面高的材料作为催化剂载体,提高催化剂的利用率和活性;设计新型结构催化剂,如核壳结构、纳米阵列等。目前主要使用的交换膜中,杜邦全氟磺酸质子膜居多,陶氏化学、3M、戈尔、日本旭硝子等品牌的短链全氟磺酸质子膜也有应用。为了提高交换膜的稳定性,通常采用聚芳烯类聚合物对膜进行强化改性,使用催化材料对隔膜进行修饰,以降低产物气体交叉。双极板成本占电解槽的50%以上,通常配置贵金属涂层以提高耐腐蚀性。未来降低制造成本的工作主要围绕新型低成本的双极板材料、表面处理工艺展开。
在组件组装工艺及优化方面,目前研究主要有阴 / 阳极非对称设计、连接卡位优化电解组件固定等。为了适应波动电源,一些研究探讨了电解槽中水流量变化、供水管路分布、膜电极结构对两侧气体渗透、温度及压力变化、电流密度等的影响。对于电解槽核心部件,目前最常用的催化剂涂覆膜工艺主要有超声喷涂法、卷对卷涂布法:相比前者,后者采用一次性涂覆催化剂层,可以更快得到更厚、更均匀的涂层,适应膜电极批量生产需求。为了避免装配产生的穿刺、开裂、机械应力、不充分的湿化与反应压力,通常在设计膜电极及其夹紧过程时充分研究所用材料特性,基于实验装置开展装载测试。
在频繁启停及风光波动电源下评估组件寿命,需要通过加速测试获得更多数据以提高电堆部件的耐用性,这是当前研发的另一类挑战。然而,PEM电解槽组件还没有标准化的加速衰减测试协议,电堆部件组分的降解率难以衡量,导致已有研究结果难以开展直接对比。建立标准化的PEM电解槽加速衰减测试协议,是当下关键技术研发亟待解决的瓶颈问题。
近年来,PEM电解槽各关键部件的技术研发都取得了显著进展。根据我国电解水制氢的技术路线,当前PEM电解槽关键技术指标为:效率约为63%,寿命约为6×104 h,成本约为1万元/kW。预计到2030年,PEM电解槽关键技术指标为:效率达到78%,寿命达到1×105 h,成本降至4000元/kW。
(二)PEM电解槽制氢技术发展方向
风光电力制氢的原理是完成风 / 光能向电力的转换,进而通过电解槽将电能转化为氢能。目前主要有4种电解水技术,以碱性电解水技术最为成熟、成本最低,已经进入商业化发展阶段;但PEM电解水技术发展迅猛,风光电力适配性良好,将是未来可再生能源电力制氢的首选方向。
目前,主要的风光耦合制氢方式有离网型和并网型。并网型制氢虽然克服了制氢电源的波动性问题,但存在电价高、电网通道受限的问题。离网方式将单台或多台风力机所发的电能(不经过电网)提供给电解水制氢设备进行制氢,适用于风资源良好但消纳受限的地区,具有稳健的商业模式和广阔的发展前景;主要应用于分布式制氢,局部应用于燃料电池发电供能。
与离网制氢类似,非并网制氢是另一种有效的制氢途径,省去了并网所需的大量辅助设备(如变流 / 变压器、滤波系统),成本相比并网制氢大幅降低。非并网制氢采用直流电,有效规避交流电上网带来的相位差、频率差问题,简化系统并节省成本。值得指出的是,相对于离 / 并网制氢,非并网风光电解水制氢将风光电力直接与PEM电解槽耦合,实现风光电力联网而不并网,从而避免波动性风光电力对电网的冲击。从这一过程来看,非并网风光电力制氢中的波动电源仅需进行简单变压及整流处理,通过变压器将电压调整到所需电压、将交流电整流为直流电。
非并网制氢技术是我国在相关领域中的原创技术,有助于打破波动性可再生能源的技术限制。风光电力不受上网约束,风电和光伏发电设备可进一步优化,能够显著降低成本,也可规避因并网产生的大规模风力机 / 光伏脱网事故,从而实现解决风光消纳问题与促进绿氢能源行业发展并举。
五、风光波动电源电解水制氢产业应用态势
(一)风电耦合制氢现状及经济性
目前,国内外研究的重点是并网型风电制氢在不同应用场景下的适用性和经济性。并网型风电制氢可有效消纳弃风(相应弃风率从35.8%降至7.5%),重点研究方向包括系统的配置优化、调控策略仿真,主要探究功率频繁变动下电压、电流、温度、压力、电极材料电化学特性等对制氢装置运行的影响,优化运行和启停控制策略,延长电解槽使用寿命。在风电耦合制氢中,海上风电制氢是未来的主流形式之一。世界范围内已公布的电解水制氢项目,储备总规模的一半来自海上风电制氢;德国、荷兰等国家均有百万千瓦级的海上风电制氢项目规划。我国海上风电发展异军突起,2021年新增装机容量超过1.69×107 kW,累计装机容量超过2.638×107 kW;预计到2030年,海上风电累计并网装机容量接近100 GW,平准化度电成本将比目前年水平下降40%以上。
近年来,国外陆续建成了20多个风电耦合制氢示范项目。在欧洲,重点研究方向有:探究氢能在电网中的储能优势,提高风能利用率、发电品质和电网稳定性;开展“电转气”项目,通过氢储能提高可再生能源占比;开发海上风电制氢项目,如荷兰将在2030年建成3~4 GW海上风电制氢工程,2040年可达10 GW装机容量、8×105 t制氢规模。我国风电制氢研究起步较晚,在关键技术、设计运行经验方面尚有诸多不足,在风电制氢系统的优化设计、制氢系统运行及优化策略、全生命周期技术经济性评价等方面表现得尤为突出。
与传统制氢方式相比,电解是决定风电制氢经济性的关键因素。电解水制氢成本70%源自电价,按照目前电价计算,风电制氢成本是传统制氢的2~3倍。当度电成本控制在0.25元时,风电制氢成本与传统制氢成本持平;若电价走低则具备经济性优势。
(二)光伏发电耦合制氢现状及经济性
光伏发电耦合制氢是可再生能源制氢的另一类主要途径。2022年,世界光伏新增装机量为142.8 GW,预计2023年全球光伏新增装机将为230 GW。目前,全球氢气需求量约为6×107 t/a,若全部制氢来自光伏发电,则每年需新增约装机900 GW。可见,光伏发电制氢发展空间巨大。
当前,国内外均积极开展光伏发电制氢项目(见表3)。多数光伏制氢项目属于并网型,部分可实现完全离网、无人值守、智能监控制氢。我国光伏发电制氢发展迅猛,内蒙古、山西、甘肃、吉林等省份是相关示范项目的主要建设地。例如,2023年8月新疆库车绿氢示范项目全面建成投产,是我国规模最大的光伏发电直接制绿氢项目,产氢量为2×104 t/a。
光伏发电制氢产业化的发展瓶颈在于成本过高,光伏度电成本的下降将大幅降低电解水制氢的成本。据测算,2025年光伏新增装机发电的度电成本将低于0.3元,届时光伏发电制氢有望趋于平价化;在光资源充沛的地区,光伏发电制氢的度电成本甚至有望降至0.15元,将进一步推动制氢成本走低。到2035年、2050年,新增光伏发电的度电成本将分别为0.2元、0.13元,全面实现良好的经济性。
根据近期研究预测和“中国2030年‘可再生氢100’发展路线图”,我国陆上风电、光伏发电的电解水制氢已接近平价化。然而,PEM电解水制氢设备要比碱性电解槽高5倍以上,平准化制氢成本高40%左右。为此,未来发展PEM电解槽制氢的关键驱动因素即在降低设备制造和运行成本。随着制氢产业的规模化、相应核心技术的不断突破,PEM电解槽成本有望降低50%以上,平准化氢气成本有望降低20%。
表3 国内外风光制氢项目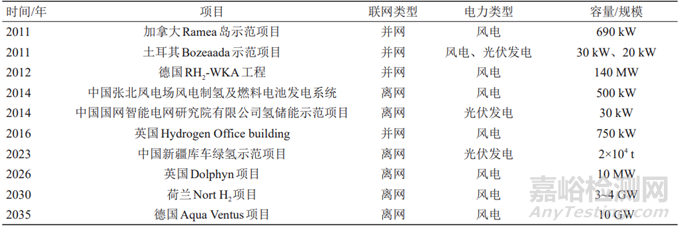
六、波动性负荷耦合制氢发展建议
当前,在国家重点研发计划等渠道的支持下,我国学术界和产业界围绕风光电解水制氢,通过关键技术突破和核心装备应用,基本构建了风光耦合制氢全链条技术体系。然而,在离网或非并网条件下风光耦合PEM电解水制氢依然面临技术、成本、制度等挑战,突出表现在电解槽效率较低、成本过高、核心技术成熟度低,技术标准缺乏,产业链发展制度保障不强。为此,面向风光等波动性负荷耦合制氢领域的未来挑战,提出技术、成本、政策布局等方面的发展建议。
(一)深化研究风光波动电源下高效电解池的基础科学问题和核心部件
风光电力负荷存在固有的波动性,模型预测和波动模式未能标准化,潜在的基础科学问题复杂而关键。商业化应用的前提之一即掌握风光波动电源下电解池耐久性、性能衰减机理及相关标准。电解池的运行和启停特性、部件衰减机理和模拟测试方法,各要素之间的作用关系等仍不清晰,有待深化研究。
目前,对电解池各部件的稳定性和衰减机制有了较清晰的认知,针对单一部件或者电解池整体性能衰减特性的研究已有展开,形成了初步的应对策略。未来需进一步加强相关电解槽设计和衰减评估标准的制定。面向风光电力波动电源,进一步提高部件的热学、力学、电化学性能,设计和开发关键催化材料,以切实增强电解槽的稳定性和服役寿命。在此基础上优化风光-荷-氢相协调的电解氢系统配置,特别是借助人工智能等手段对当前模型进行进一步优化。
(二)进一步降低制氢成本
降低电解槽制造成本,关键在于非贵金属催化剂的开发与应用。遴选Ni、Co等过渡金属催化材料,Fe等廉价金属材料应用于电解槽并明确性能,是大幅降低电解槽制造成本的重要方向。按照技术规划目标,未来可通过卷对卷直接涂布、丝网印刷、喷涂等方法构建膜电极,将催化剂载量从目前的1 mg/cm2逐步降低到0.125 mg/cm2。
虽然目前大部分地区的电力仍然难以支持实现绿氢平价化,但部分风光资源丰富地区的度电成本可低至0.3元,已接近或可局部实现绿氢平价化。随着风光发电装机总量的逐年增长,电价成本在不久的将来可支撑风光耦合制氢的商业化。推动风光制氢一体化,实现宽范围、低成本风光制氢工程的规模化发展,进一步延长制氢工作时长、降低综合运营成本。
(三)开展风光耦合制氢优化布局和制度保障研究
合理布局产业规模是风光耦合制氢发展的关键因素,形成体量化的产业集群对于降低风光耦合制氢成本、提高制氢技术成熟度、加快实现商业化至关重要。通过综合布局吸引社会资本、鼓励技术突破、完善产业链水平,加强技术、资本与产业的融合,全面提升风光耦合制氢的市场竞争力。
我国已将风光耦合制氢列为战略性新兴产业之一,但随着相关技术的成熟和商业化,推动氢气规范使用和生产等仍需积极的政策引导。在产业化发展的不同阶段,及时制定或优化调整风电耦合制氢政策,驱动可再生能源制氢产业的高质量发展。
