摘 要:目前使用轻质材料是实现汽车轻量化的重要途经。通过对某全铝合金汽车前围内板冲压工艺方案的设计,论述了铝合金汽车板在冲压过程中发生的起皱、开裂、减薄、回弹等问题,并使用有限元分析软件,对前围内板工艺方案进行仿真分析,根据分析结果对工艺方案进行优化设计,并验证其可行性。最终确定的工艺方案为铝合金汽车覆盖件的开发、产品试制提供了技术支持和理论基础。
关键词:铝合金;轻量化;前围内板;冲压工艺;
前言
随着日益严峻的环境问题出现以及节能减排法律法规的实施,轻量化已经成为汽车行业不得不重视的课题。研究表明,约75%的汽车油耗与整车质量有关,每降低重量10%,汽车燃油效率可以提高6%~8%,而排放则下降4%。因此,轻量化对节能减排、环境保护具有重大意义。汽车车身零部件中约70%是冲压完成的,所以使用轻质合金是实现轻量化的重要途径之一。轻质材料中,铝合金因其耐冲击载荷好、强度高、密度小、且耐腐蚀等优点受到了各大车企的喜爱。但铝合金材料在冲压成型方面的特性与钢板又不完全相同,很多情况下不能套用钢板的变形规律,如铝板的弹性模量是钢板的1/3,而回弹量却是钢板的3倍,所以更容易出现开裂、回弹等缺陷。
本文针对铝合金前围内板的成型过程进行研究,对其冲压工艺进行分析、优化和总结,加深仿真成型对制定冲压工艺的认知,使之更好地为生产服务,从而验证仿真成型对传统冲压的优越性,并为铝合金板材的应用提供理论技术指导。
1、铝合金轻质材料性能参数
5×××系铝合金属于应变硬化铝合金,适用于汽车内板。为保证冲压成型性及强度需求,前围内板选用5182-O铝合金板,其力学性能见表1[1]。
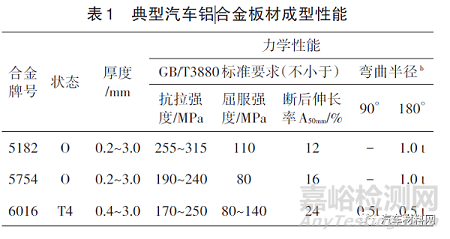
2、零件冲压工艺分析
前围内板形状如图1所示,零件外形尺寸327 mm×879 mm×215 mm,料厚1.2 mm。与之装配的零件有地板前端、前挡板横梁等零件,尺寸精度要求较高。同时前围内板形状复杂、变形量较大,零件成型后的回弹、扭曲对其精度有较大影响,因此需要充分的塑性变形来保证足够的刚性。
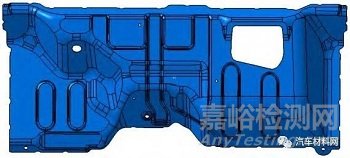
图1前围板内板
下面从三个方面对零件进行分析:
(1)零件表面质量要求:
前围内板是非外观表面,不允许有裂纹、过大起皱、破裂等缺陷。
(2)零件装配关系:
前围内板存在装配关系的零件有:前地板前端、前挡板横梁、左右前轮包等,存在有焊接关系、铆接关系、粘接关系,以及密封要求。
(3)零件精度要求:
零件精度要求如表2所示[2]。
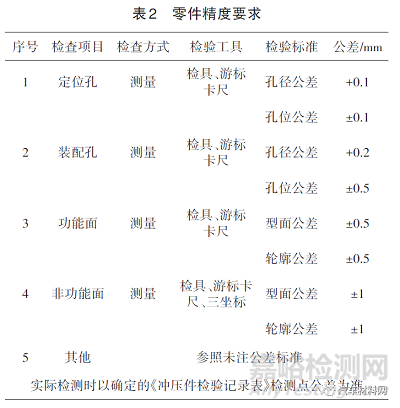
2.1零件拉伸起皱、开裂部位分析
由于板料厚度方向和平面方向上的尺寸存在较大的落差,致使拉伸时造成厚度方向不稳定,当平面方向的应力达到一定程度时,厚度方向失稳,从而产生起皱现象。仿真分析后可知该零件有2处较为明显的起皱,如图2所示。在成型过程中,急剧的断面形状变化造成材料堆积,形成较大的波纹即起皱。
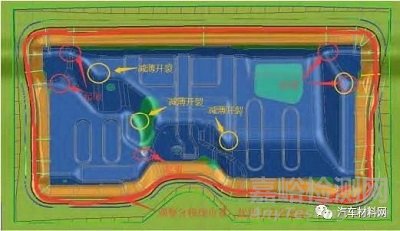
图2件起皱部位、开裂部位
零件开裂部位在图2中所示的拐角处。由于拐角和根部R都比较小,拉伸成型或整形都难以达到要求,因此仿真分析后提出产品ECR变更,要求加大根部尖角处R,便于成型。图2中,三条棱线相交的断差大、R小,形成尖角,使应力集中而顶破板料。因此,增加过渡筋可以缓解起皱,避免开裂。
2.2零件回弹及扭曲
前围内板经过拉延、修边和整形后,在内应力作用下,零件回弹产生扭曲变形,尤其易出现在右侧焊接边缘部位。对策:尽量拉伸成形,减少整形成形;保证最小变形要求,提高刚度;保证流入材料的平衡性。实在不行则增加整形工序,将回弹部分整形到公差范围以内。
2.3修边冲孔和安装配合面的整形
前围内板修边主要集中在周圈修边以及内部的冲孔。为了保证修边质量,局部采用斜锲修边,其他采用正切修边;冲孔采用正冲冲孔,内部斜面冲孔斜锲无法冲裁,故采用压料芯斜锲冲裁,提高冲裁质量[3]。拉延时局部造型圆角拉延不到位的,后序整形到位;修边角度锐角不超过15°、钝角不超过20°,修边角度过大容易产生毛刺,影响精度,且修边刃口磨损较快,会降低模具寿命;废料长度小于600 mm,利于排料[2]。在修边时还要考虑废料的排出。针对铝合金板材特性,要求将废料排出到工作台面外,所以废料滑道不小于30°,滑板附加滚珠网。
通过以上分析确定前围内板的冲压工序,共需5道工序完成:①落料→②拉延→③侧修边、冲孔→④修边、冲孔、侧冲孔→⑤整形。由于回弹需求,在完成正常的冲压工艺工序以外,再增加回弹测量工序,以便查看零件的回弹情况,所以CAE工艺安排为:①落料→②拉延→③侧修边、冲孔→④修边、冲孔、侧冲孔→⑤整形→⑥回弹。
前围内板冲压工艺图如图3所示。
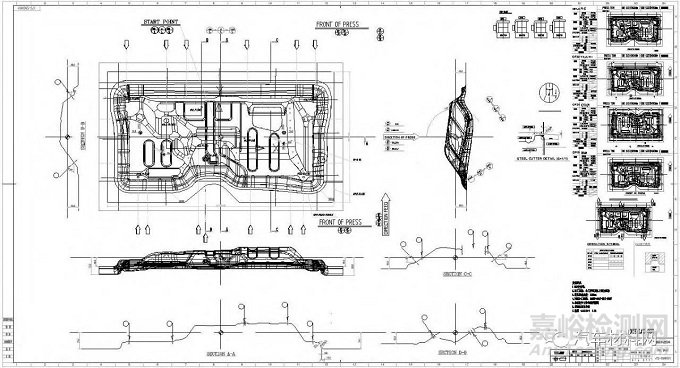
图3前围内板冲压工艺分析
3、拉延工艺设计及仿真结果
拉延是利用拉延模将平板毛坯变为开口空心零件的冲压工序。具体指毛坯在压料力的作用下,使坯料在凸凹模、压边圈之间产生流动,得到所需制件形状的过程。
拉延工艺在仿真软件中进行工艺设计和仿真计算,经反复修改和优化后确定最优工艺方案。CAD分析模型的步骤:导入模型(软件自动进行网格划分)、网格检查及空洞填充、确定模具基准、料厚及冲压方式、工具设定、坯料尺寸确定、材料选择、拉深筋布置、工艺参数设置和分析计算等。
3.1冲压方向的选择
根据前围内板的结构特点确定其冲压方向。在汽车坐标系下,零件Z方向上高度差较大,因此在考虑拉延冲压方向的时候,零件沿车身Y轴旋转145°,降低零件的高度差,以保证在拉延初期零件的腰线部分要首先接触到坯料,不能使棱线产生滑移,并保证不能出现负角。
3.2压料面的设计
压料面是工艺补充的重要组成部分,是指凹模圆角半径以外的部分,对成形起着重要作用。压料面应尽量保证坯料平展,各部位进料阻力平衡,拉延深度大致相同。
设计压料面:前围内板周圈搭接面平缓,没有剧烈起伏,没有参与法兰面位置,不采用翻边工艺。所以在这种情况下,压料面的形状是已定的,即采用外压料形式,外压料面基本保持一致。
在Autoform中构建压料面,根据以上要求,用U、V线来控制压料面的形状和深度。
3.3工艺补充设计以及拉深筋和模拟参数的设定
(1)工艺补充设计。
为了创造良好的拉延条件,需要将制件上的孔填平,有凸起时可以改造平滑使其成为有利成型的压料面;无凸起时需要建造一个有利进料的光滑顺畅压料面,并设置调整进料阻力的筋或坎,这些增添的部分统称为工艺补充部分。前围内板拉延工艺模型如图4所示。
(2)拉深筋和模拟参数设定。
拉深筋布置:成形过程中为了限制板料的流动,需要设置各种形状的拉深筋。Autoform中前期分析不需要建立实际的拉深筋,而采用等效拉深筋。分析时可以通过快速调整拉深筋系数来调整拉深筋阻力,以便节省分析时间。分析成功之后再根据相应的阻力系数来设计真实拉深筋几何形状[4]。等效拉深筋设置参数如图4所示。图片
图4等效拉延筋设置参数
模拟参数设定:这一步主要是对摩擦系数、压边力等工艺参数进行设置。材料选用5182-O,抗拉强度255 MPa、屈服强度110 MPa、n值0.32、AG断后延伸率为22.3%;压边圈行程100 mm,理论压边力80 t,摩擦系数选用0.15(标准下)。
前围内板拉延为单动外压料形式。
3.4仿真计算结果分析
参数设置完成后进行成形仿真计算,并对工艺补充和参数设置进行反复修改。对计算结果进行分析,主要从以下几方面入手:
(1)压料情况和成形过程分析。
板料在重力作用下下垂,同时凹模与压边圈闭合压料。图5显示了板料的压料状态以及成形期间各时间段板料的状态。图片
图5铝合金前围内板成形过程
(2)减薄率分析:铝合金板材,料厚减薄评价。
判断准则:成型区域减薄超过18%一律视为破裂,查看FLD指示,将减薄云图的刻度设置为-0.18~0.03,用不同颜色来显示[5]。减薄情况如图6所示,产品内最大减薄16%,满足产品需求。图片
图6材料减薄率分布图
(3)开裂部位分析。
从图5可以看出,零件没有开裂部位。图示两处减薄均在产品以外,属于工艺补充部分可消除,对后续工艺不产生影响。
3.5优化修改后确定拉延数模和后序成形工艺
通过设变更改和调整拉深筋布置、压边力、拉延补充的方式,对成形分析中出现的问题,反复进行仿真计算,最终得到满意的分析结果,确定工艺参数和后序成形工艺。
从铝合金前围内板的冲压工艺设计可以看出,仿真分析结果为产品设计人员和工艺设计人员提供了重要的参考,在产品设计阶段发现冲压问题及时更改产品,为后续设计节省时间和成本。同时为设计人员在以后的工艺参数调整和模具设计中,提供了技术储备,既提高了设计质量,又缩短了模具调试时间和模具设计制造周期。
4、零件后续工序分配及回弹结果
4.1修边工序工艺设计
修边偏差控制在±0.5 mm,修边角度会影响修边的质量,尤其是铝合金板材更要注意。选择冲裁方向时应注意:
(1)修边刀块与拉延型面的法向方向夹角过大时,容易发生撕裂,产生毛剃,且若凸凹模刃口成锐角,强度不足易损伤刀块,会产生铝屑。一般夹角在±20°以内,严格要求的话应在±15°[5]。
(2)修边方向分垂直修边、斜锲水平修边和斜锲倾斜修边,如图7所示。为确保模具结构简单、费用低、工作机构稳定,尽量选择垂直修边,或者采用斜锲修边[6]。图片
图7修边形式示意图
结合上述,铝合金前围内板修边工艺安排如图8所示。图片
图8修边工艺图
4.2冲孔工序工艺设计
冲孔可以整合到修边工序或整形翻边工序中,这主要取决于孔的位置。孔的安排是否合理决定了孔的位置精度。冲孔的设置原则:
(1)相同功能的安装孔,在同一工序中冲裁,保证孔与孔之间的位置公差,主副定位孔应在同一工序冲裁,且冲孔方向与孔的法向不应超过3°。
(2)孔所在零件平面如果有翻边、整形等工序时,要将此类孔放在最后一道工序来加工,保证孔的精度和位置度公差。
(3)当零件中大孔与小孔距离较近时,应先大后小,以免冲大孔时导致小孔二次变形。
(4)为了保证孔的精度和模具结构简单,应尽量垂直冲裁。冲压方向与孔的中心线夹角应满足表3要求,如不能满足,则需要斜锲冲孔[2]。
前围零件冲孔信息如图9所示:图片
图9零件冲孔信息
结合零件孔位信息和冲孔工艺要求可知:该零件冲孔采用1类孔正冲和2类孔斜锲侧冲。
4.3整形工序工艺设计
为保证零件顺利成形,拉延工序会对产品的某些形状、特征进行改动,如加大圆角等,而恢复是通过整形工艺来实现。考虑到铝合金板材的特性,将其整形工序单独作为一序来实现,避免出现划伤和压痕。
4.4回弹分析
铝合金零件的回弹是很难控制的一项缺陷,通常分为两类:
(1)拉延回弹。
当拉延过程中板料发生无法控制的复杂变形时,拉延件中会产生残余内应力,而这些内应力在修边后得以释放,从而造成回弹。
(2)翻边回弹。
翻边后由于板料的塑性变形不足,存在弹性变形,制件取出后,弹性变形恢复,从而引起回弹。
回弹对策:根据仿真分析回弹数据进行回弹补偿。
文中只对回弹进行预测,不做补偿。仿真分析结果显示自由回弹如图10所示:最大自由回弹量为红色区域,最大回弹值为4.38 mm。图片
图10 自由回弹示意图
5、生产验证
采用优化后的模拟工艺参数重新优化设计拉延工艺模面,并进行模具设计加工,经过调试,最终得到稳定的合格产品件。生产调试结果与仿真分析结果基本吻合,产品拉延成形性良好,无起皱开裂等缺陷,回弹也符合产品工艺要求。
6、结论
(1)铝合金零件在设计阶段,通过仿真分析结果对产品提出设变,可以有效提高产品质量。考虑到工艺参数波动,应以减薄率为目标,以不产生破裂、起皱等缺陷为约束函数,以压边力、拉深筋阻力等工艺参数为设计变量进行稳健性优化。
(2)仿真分析软件提供的等效拉深筋方法展现出了极大的优越性,不仅便于拉深筋参数的设置,同时避免了对几何模型反复的修改,缩短了设计时间,提高了计算效率。
(3)铝合金覆盖件冲压成形的仿真,得到了许多重要参数,为其他类似零件模具的开发提供了重要的参考,为实际生产调试节省了时间。
参考文献
[1] GB/T 3880.1.2.3—2012,一般工业用铝及铝合金板、带材[S].
[2] Q/WM 1001—2003,北京福田模具设计规范与标准[S].
[3] Q/WM 1006—2003,北京福田模具设计规范与标准[S].
[4] 林通.Auroform4.0钣金冲压成形分析从入门到精通[M].北京:机械工业出版社,2012.
[5] 涂小文.AutoForm原理技巧与战力手册[M].武汉:湖北科学技术出版社,2013:405-427.
[6] 崔令江.汽车覆盖件冲压技术[M].北京:机械工业出版社,2003:140-141.