一次性袋子应用于制药生产过程已经超过二三十年的历史。目前,一次性生物工艺袋已广泛应用于细胞培养、产品混合和储存转移、培养基和缓冲液的配制和储存、半成品和成品的储存和冻存等。一次性生物工艺系统市场仍然处于高速增长区间,根据Report Linker, Emergen Research, Businesswire等多个市场调研机构的数据,2021~2022全球市场容量约在82~122亿美金,年复合增速约16~22%。不同机构的统计范围存在差异,并且该数据包含了与一次性袋子、配套耗材及相关工艺设备。另外,根据中信建投的统计和预测,国内一次性袋子2022年市场约50~60亿元,年复合增速13~20%。
▲图1. 一次性生物工艺袋市场(图片来源:Emergen Research)
驱动该市场增长的因素主要有:
全球人口老龄化,生物药的开发和生产需求增长
全球发展中国家的人均医疗支出增加
新兴疗法对小规模、多品种生产的灵活性、适应性需求增加
一次性使用系统的产品范围和渗透率增加,据American Pharmaceutical Review, 一次性工艺的渗透率在过去10年从10%上升至近30%。
在应用方面,一次性使用袋早期主要被用于培养基、缓冲液等的混合、储存以及细胞扩增。随着大规模细胞培养技术和一次性生物反应器的发展,一次性使用袋的应用拓展到大规模生物反应器并用于抗体、疫苗等的生产,目前已经开始在微生物发酵领域替代不锈钢系统。在大规模原液储存方面,一次性袋子相比于传统塑料瓶或不锈钢容器的便利性和安全性已经得到证实,被更广泛地应用。
随着新兴疗法技术的发展,比如细胞与基因治疗、mRNA药物、外泌体、基因编辑等,药物和治疗手段向小型化、个性化和灵活化发展,这也进一步促进了一次性使用系统的应用。一次性使用系统的应用降低了项目前期投资并缩短了建设周期,并提升了工艺开发和验证速度,从而极大地加速了这些新兴疗法的上市。
以细胞与基因治疗为例,一方面,其生产设施规模通常较小,灵活性要求更高。一次性使用系统已经实现了模块化设计,密闭式、自动化操作,进一步确保了小批量灵活化生产的安全性和高效性。据BioPlan统计,细胞治疗1000L以下生产规模占比59%,基因治疗该比例为53%。另一方面,NMPA于2022年发布《药品生产质量管理规范-细胞治疗产品附录(征求意见稿)》,要求直接接触细胞产品的无菌耗材应当尽可能使用一次性材料[1]。
▲图2. 细胞基因治疗流程(图片来源:Harvard Medical School)
一次性生物工艺膜的市场和技术趋势
长期以来,许多因素也在制约着一次性生物工艺系统的发展和应用,比如供应链安全、耗材成本、标准化程度等,其中两大主要挑战便是袋子泄漏和溶出析出风险。一次性生物工艺膜作为生物工艺袋的关键原材料之一,很大程度上决定了生物工艺袋的安全性。
一次性袋子厂家在早期更多地采用商业化的膜材,甚至从别的行业(如医疗、食品)借用膜材,而后随着应用经验积累和用量提升,开始针对生物工艺行业应用需求开发并拥有自己的膜材。例如,ThermoFisher最初HyperForma BPC使用Renolit 9101膜,而后增加了自己的AEGIS 5-14膜。国内的乐纯和科百特也在使用Renolit 9101膜后又推出了自有的膜材料。
早期的生物工艺膜(2006~2012)主要由低密度聚乙烯(LDPE)和乙烯-醋酸乙烯共聚物(EVA)组成接触层,而更现代的膜(2014及以后)则主要由线性低密度聚乙烯(LLDPE)和超低密度聚乙烯(ULDPE)组成接触层。对一次性生物工艺膜材的升级得益于长期的应用经验积累和问题发现,通过优化膜材结构、抗氧化剂、润滑剂等提升膜材的机械、焊接和生物兼容性能。比如,膜材中抗氧化剂TBPP(商品名Irgafos 168)的降解产物(bDtBPP)对部分细胞系的生长抑制,促使了膜材Bioclear 10升级为Bioclear 11,CX 5-14升级为Ageis 5-14。
膜材的升级和变更需要经过一系列耗时耗力的验证,对袋子生产企业和最终袋子用户都意味着高昂的费用和时间成本[2, 3]。因此,为了降低膜材验证和供应链成本,制药企业以及袋子厂家都希望能够采用统一的、标准化的膜材。比如,Cytiva推出Fortem膜是为了在上下游工艺采用统一膜材,Sartorius也推出了基于Flexsafe的上下游解决方案。
▲图3. Cytiva Fortem膜介绍(图片来源:Bioprocess Development Forum)
然而,由于生物工艺行业应用点较多,不同应用环节对膜材性能的要求不尽相同,设计一款适用于各个工艺应用要求的膜材几乎是不可能的。比如,用于细胞培养袋的膜材关注的是析出成分对细胞成长的影响、用于大体积袋体的膜材则更关注材料的机械和焊接强度、用于原液和制剂生产的袋子则要求低溶出析出及生物安全性、用于细胞或原液冻存的袋子则注重膜材的耐低温性能。再加上制药行业对工艺变更的保守,许多一次性袋子厂家在其产品线中同时保留着多款膜材制成的不同袋子产品。
▼ 表1. 进口品牌膜材组合
不论是从技术还是市场角度,未来一次性使用技术是走向标准化还是差异化,行业内的辩论从来就没有停止过,包括设计标准化、测试标准化、材料标准化等[4~8],生物工艺膜也不例外。行业用户的呼声是趋向标准化,然而新材料的迭代周期和利益相关方的博弈都很漫长,我们仍然无法预测未来的标准化程度及时间线。或许,一次性生物工艺膜也会遵循不锈钢材料的路径,未来将有统一的膜材标准和验证测试方法,符合相同标准的膜材可彼此替换以降低用户成本;同时,膜材供应链会更集中,以使产业链综合成本更低。
一次性膜材的国产化趋势和挑战
全球范围的公共卫生事件以及国际政治动荡都使得我们不得不考虑供应链安全的问题。在新冠疫情期间,我国在抗体、疫苗等生物制品生产中仍然使用着大量进口耗材,即使其中已经国产化的一次性袋子,仍主要依赖进口的一次性生物工艺膜。这些原材料的供应稳定性对国内药品生产企业的研发与生产造成了相当的影响。
尽管制药装备的国产化进程已进行多年,但国内在核心零部件和原材料上的积累和水平仍然与国外差距较大。工信部于2021年底发布了《“十四五”医药工业发展规划》,提出了产业链供应链稳定可控为主要发展目标之一,并为上游产业发展规划提供了具体指导,包括支持攻关核心装备和新型材料[9]。
近年来,一次性生物工艺系统的国产化如火如荼。据不完全统计,包含国际品牌在国内的一次性袋子生产工厂,国内已经超过30家一次性袋子生产企业。在膜材方面,据公开市场信息,目前已经有多家企业推出自有一次性膜材,与国外类似,其中既有一次性袋子厂家,如乐纯、多宁、科百特,也有专供膜材的厂家,如安肯迈、博生。
▼ 表2. 国产膜材对比
然而,由于进口膜材在原有制药企业生产工艺中已经过验证,即使部分袋子生产企业已经推出一次性生物工艺膜材,其新推出的自有膜材仍然仅限于小规模或非关键工艺环节的应用,距离大规模进口替代仍然任重道远。同时,大部分的袋子生产企业仍然完全依赖进口Renolit膜。
▲图4. AKM Primum CF1211多层共挤膜(图片来源:www.anchormanbiotech.com)
除了膜材替代成本高以外,另一个挑战是膜材的研发和制造成本。膜材的研发对材料学和制膜工艺经验的要求极高,也需要大量的资金和时间投入。Cytiva在开发Fortem膜的过程中,与Sealed Air共同筛选评估了约22种试样才确认了最终的膜材设计[10]。对大部分一次性袋子生产企业而言,对材料学和制膜过程缺乏专业能力,并且膜材的用量不足以支持其开展原材料的研发和制造。只有当这些膜材用量集中起来,由专门的膜材生产企业负责,才能够集中研发与生产资源,实现供应链的成本优化。
总结与展望
随着更多生物药的持续开发和上市,以及新兴治疗药物对小规模、灵活化生产的更高需求,一次性生物工艺系统市场将继续保持高增长速率,尤其是其中一次性使用技术渗透率相对较低的工艺系统,如超滤、层析等,以及新兴治疗药物生产工艺所需的工艺系统,如病毒收获、细胞分选等。
一次性生物工艺膜作为一次性袋子的关键原材料,已随着行业应用数据和经验的积累,完成了新一代膜材的开发升级,并已经在逐步替代较老的膜材。新一代膜材要么在某些特定工艺环节有着更优的性能表现,如细胞培养,要么增强了袋子生产厂家对膜材供应链的控制,要么有助于在上下游工艺统一膜材。然而,对于生物工艺膜材在未来将走向标准化还是个性化,行业仍然处于争论与博弈之中,似乎还没有达成一致意见。
在产业链国产化方面,国际贸易和政治局势正在加速国产化向上游供应链转移。一次性生物工艺膜材作为关键原材料,其国产化受到了国家政策的支持,并已在企业行动中已经取得了初步成果,部分国产膜材的性能测试数据已经与进口膜材不分伯仲。然而,大规模应用中的一次性膜材仍主要依赖进口,国产化膜材替代道阻且长,机遇与挑战并存。同时,笔者也期待看到国产化一次性系统和原材料在国际市场占有更多的市场份额,成为全球供应链体系的重要组成。
参考文献
[1] NMPA. 药品生产质量管理规范-细胞治疗产品附录(征求意见稿). 2022-01-06. https://www.nmpa.gov.cn/xxgk/zhqyj/zhqyjyp/20220106165600150.html
[2] Susan Burke. Considerations in Evaluating New Plastic Film for Single-Use Technologies and Film Development. Downstream Column. Feb 08, 2016. https://downstreamcolumn.com/considerations-evaluating-new-plastic-film-single-use-technologies-film-development/
[3] Katharina Blaschczok, Nina Steiger, Elke Jurkiewicz, Ute Husemann, Franziska Faulstich, Regine Eibl and Gerhard Greller. Evaluating New Film for Single-Use Bags: Growth Performance Studies with Animal and Human Cells. Bioprocess International. Mar 14, 2016. https://bioprocessintl.com/upstream-processing/upstream-single-use-technologies/evaluating-new-film-for-single-use-bags-growth-performance-studies-with-animal-and-human-cells/
[4] Maribel Rios. Outlooks on Standardization. Bioprocess International, May 1, 2012. https://bioprocessintl.com/manufacturing/monoclonal-antibodies/outlooks-on-standardization-330194/
[5] Extractables and Leachables Subcommittee of the Bio-Process Systems Alliance. Extractables and Leachables Subcommittee of the Bio-Process Systems Alliance. Bioprocess International, Mar 10, 2015. https://bioprocessintl.com/manufacturing/single-use/toward-industry-standardization-extractables-testing-single-use-systems-collective-bpsa-perspective/
[6] David Wolton, Luke Heaven, Scott McFeaters and Mahesh Kodilkar. Standardization of Disposables Design: The Path Forward for a Potential Game Changer. Bioprocess International, Dec 16, 2015. https://bioprocessintl.com/manufacturing/supply-chain/standardization-of-disposables-design-the-path-forward-for-a-potential-game-changer/
[7] Javier Lozano and Austin Lock. Benefits of Single-Use Standardization: Adopting a Standard Design Approach. Bioprocess International, May 21, 2021. https://bioprocessintl.com/manufacturing/single-use/benefits-of-single-use-standardization-adopting-a-standard-design-approach/
[8] Dan Stanton. Industry calls for standardization and simplification to boost manufacturing agility. Bioprocess International. Mar 1, 2021. https://bioprocessintl.com/bioprocess-insider/industry-calls-for-standardization-and-simplification-to-boost-manufacturing-agility/
[9] 工信部. “十四五”医药工业发展规划. 2021-12-22. https://www.gov.cn/zhengce/zhengceku/2022-01/31/content_5671480.htm
[10] Cytiva. Developing a fit-for-purpose bioprocess film. https://www.cytivalifesciences.com/en/us/solutions/bioprocessing/knowledge-center/developing-a-fit-for-purpose-bioprocess-film
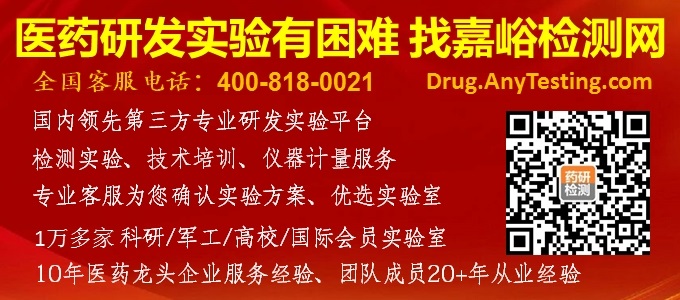